Zement


Zement ist ein Bindemittel, eine Substanz, die im Bauwesen verwendet wird, um andere Materialien zu binden, zu härten und an ihnen zu haften. Zement wird selten allein verwendet, sondern eher, um Sand und Kies (Zuschlagstoffe) miteinander zu verbinden. Zement gemischt mit feinen Zuschlägen ergibt Mörtel für Mauerwerk, oder mit Sand und Kies ergibt er Beton. Beton ist das am häufigsten verwendete Material überhaupt und nach Wasser die am meisten verbrauchte Ressource der Erde. ⓘ
Die im Bauwesen verwendeten Zemente sind in der Regel anorganisch, oft auf Kalk- oder Kalziumsilikatbasis, die je nach der Fähigkeit des Zements, in Gegenwart von Wasser zu erhärten, als nichthydraulisch oder hydraulisch bezeichnet werden können (siehe hydraulischer und nichthydraulischer Kalkputz). ⓘ
Nicht-hydraulischer Zement härtet nicht in nassem Zustand oder unter Wasser aus. Vielmehr härtet er beim Trocknen aus und reagiert mit dem Kohlendioxid der Luft. Nach dem Abbinden ist er resistent gegen den Angriff von Chemikalien. ⓘ
Hydraulische Zemente (z. B. Portlandzement) härten aus und werden durch eine chemische Reaktion zwischen den trockenen Bestandteilen und Wasser klebrig. Durch die chemische Reaktion entstehen mineralische Hydrate, die nur wenig wasserlöslich sind und daher in Wasser recht beständig und sicher vor chemischen Angriffen sind. Dies ermöglicht das Abbinden in nassen Bedingungen oder unter Wasser und schützt das ausgehärtete Material zusätzlich vor chemischen Angriffen. Das chemische Verfahren zur Herstellung von hydraulischem Zement wurde von den alten Römern entwickelt, die vulkanische Asche (Puzzolan) mit Kalk (Kalziumoxid) verwendeten. ⓘ
Das Wort "Zement" lässt sich auf den altrömischen Begriff opus caementicium zurückführen, mit dem Mauerwerk beschrieben wurde, das dem modernen Beton ähnelt und aus zerkleinertem Gestein mit gebranntem Kalk als Bindemittel hergestellt wurde. Die vulkanische Asche und die pulverisierten Ziegelzusätze, die dem gebrannten Kalk hinzugefügt wurden, um ein hydraulisches Bindemittel zu erhalten, wurden später als cementum, cimentum, cäment und Zement bezeichnet. In der heutigen Zeit werden manchmal organische Polymere als Zemente in Beton verwendet. ⓘ
Die Weltproduktion beträgt etwa vier Milliarden Tonnen pro Jahr, wovon etwa die Hälfte in China hergestellt wird. Wäre die Zementindustrie ein Land, so wäre sie mit bis zu 2,8 Milliarden Tonnen der drittgrößte Kohlendioxid-Emittent der Welt, übertroffen nur von China und den Vereinigten Staaten. Die erste Kalzinierungsreaktion bei der Herstellung von Zement ist für etwa 4 % der weltweiten CO2-Emissionen verantwortlich. Der Gesamtprozess ist für etwa 8 % der weltweiten CO2-Emissionen verantwortlich, da der Zementofen, in dem die Reaktion abläuft, in der Regel mit Kohle oder Petrolkoks befeuert wird, da eine helle Flamme erforderlich ist, um den Ofen durch Strahlungswärme zu erhitzen. Daher trägt die Zementherstellung in hohem Maße zum Klimawandel bei. ⓘ

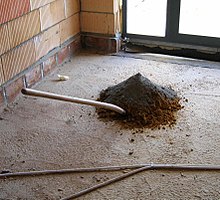
Zement (lateinisch caementum „Bruchstein“, „Baustein“) ist ein anorganischer und nichtmetallischer Baustoff. Er ist feingemahlen und zählt daher zu den Schüttgütern. Aufgrund seiner Eigenschaften wird er in Zementwerken als Baustoff hergestellt und zum Anfertigen von Bauteilen und Bauwerken verwendet. Innerhalb der Baustoffe zählt Zement zu den Bindemitteln. Er erhärtet durch die chemische Reaktion mit Wasser (Hydratation) und bleibt danach fest. Zur Herstellung von Baustoffen wie Mörtel und Beton werden dem Zementpulver sogenanntes Zugabewasser (früher „Anmachwasser“) und andere Stoffe als Zuschlagstoffe beigemengt. Aufgrund der weltweiten Verfügbarkeit der Rohstoffe sowie der Festigkeit und Dauerhaftigkeit von Beton, ist Zement weltweit eines der wichtigsten Bindemittel. Mit einer Weltproduktion von 4,1 Milliarden Tonnen im Jahr 2017 ist Zement der meistverwendete Werkstoff. ⓘ
Zement wird in Zementwerken produziert. Zu seiner Herstellung werden die natürlichen Rohstoffe Kalkstein und Ton verwendet, die häufig als natürliches Gemisch vorliegen und dann als Mergel bezeichnet werden. Falls nötig, werden als Korrekturmaterialien auch Quarzsand und eisenoxidhaltige Stoffe für eine bessere Sinterung beigemischt. Die Rohstoffe werden zu Rohmehl gemahlen und anschließend auf etwa 1.450 °C erhitzt, bis sie an den Korngrenzen teilweise miteinander verschmelzen (Sintern) und der sogenannte Zementklinker entsteht. Das Material, mit nun kugelförmiger Struktur, wird abgekühlt und zum Endprodukt Zement gemahlen. Um Zementsorten mit bestimmten Eigenschaften zu erhalten, können vor dem Mahlen Hüttensand, Flugasche, Kalkstein und Gips in unterschiedlicher Dosierung und Mahlfeinheit zugegeben werden. ⓘ
Chemie
Zementmaterialien können in zwei verschiedene Kategorien eingeteilt werden: nichthydraulische Zemente und hydraulische Zemente, je nach ihrem jeweiligen Abbinde- und Erhärtungsmechanismus. Das Abbinden und Erhärten von hydraulischem Zement beruht auf Hydratationsreaktionen und erfordert daher Wasser, während nichthydraulische Zemente nur mit einem Gas reagieren und direkt an der Luft abbinden können. ⓘ
Hydraulischer Zement

Die bei weitem häufigste Zementart ist der hydraulische Zement, der durch Hydratation der Klinkermineralien unter Zugabe von Wasser aushärtet. Hydraulische Zemente (wie z. B. Portlandzement) bestehen aus einem Gemisch von Silikaten und Oxiden, wobei die vier Hauptmineralphasen des Klinkers in der Zementchemiker-Notation wie folgt abgekürzt werden
- C3S: Alit (3CaO-SiO2);
- C2S: Belit (2CaO-SiO2);
- C3A: Tricalciumaluminat (3CaO-Al2O3) (historisch und gelegentlich immer noch als Celit bezeichnet);
- C4AF: Braunmillerit (4CaO-Al2O3-Fe2O3). ⓘ
Die Silikate sind für die mechanischen Eigenschaften des Zements verantwortlich - das Tricalciumaluminat und der Brownmillerit sind für die Bildung der flüssigen Phase während des Sinterprozesses (Brennen) des Klinkers bei hohen Temperaturen im Ofen unerlässlich. Die Chemie dieser Reaktionen ist nicht vollständig geklärt und noch immer Gegenstand der Forschung. ⓘ
Zunächst wird der Kalkstein (Kalziumkarbonat) gebrannt, um seinen Kohlenstoff zu entfernen, wobei Kalk (Kalziumoxid) in einer so genannten Kalzinierungsreaktion entsteht. Diese einzige chemische Reaktion ist einer der Hauptverursacher der weltweiten Kohlendioxidemissionen.
- Fehler beim Parsen (Syntaxfehler): {\displaystyle \ce{CaCO3 -> CaO + CO2 <span title="Aus: Englische Wikipedia, Abschnitt "Hydraulic cement"" class="plainlinks">[https://en.wikipedia.org/wiki/Cement#Hydraulic_cement <span style="color:#dddddd">ⓘ</span>]</span>}}
Der Kalk reagiert mit Siliziumdioxid und bildet Dicalciumsilikat und Tricalciumsilikat.
- Fehler beim Parsen (Syntaxfehler): {\displaystyle \ce{3CaO + SiO2 -> 3CaO.SiO2 <span title="Aus: Englische Wikipedia, Abschnitt "Hydraulic cement"" class="plainlinks">[https://en.wikipedia.org/wiki/Cement#Hydraulic_cement <span style="color:#dddddd">ⓘ</span>]</span>}}
Der Kalk reagiert auch mit Aluminiumoxid und bildet Tricalciumaluminat.
- Fehler beim Parsen (Syntaxfehler): {\displaystyle \ce{3CaO + Al2O3 -> 3CaO.Al2O3 <span title="Aus: Englische Wikipedia, Abschnitt "Hydraulic cement"" class="plainlinks">[https://en.wikipedia.org/wiki/Cement#Hydraulic_cement <span style="color:#dddddd">ⓘ</span>]</span>}}
Im letzten Schritt reagieren Kalziumoxid, Aluminiumoxid und Eisenoxid zusammen und bilden Zement.
- Fehler beim Parsen (Syntaxfehler): {\displaystyle \ce{4CaO + Al2O3 + Fe2O3 -> 4CaO.Al2O3.Fe2O3 <span title="Aus: Englische Wikipedia, Abschnitt "Hydraulic cement"" class="plainlinks">[https://en.wikipedia.org/wiki/Cement#Hydraulic_cement <span style="color:#dddddd">ⓘ</span>]</span>}}
Beim Aushärten von Zement mit Wasser (Hydratation) wachsen einerseits Calciumsilicathydrat-Fasern, kurz CSH oder C3S2H3 (3 CaO · 2 SiO2 · 3 H2O), und andererseits bildet sich Portlandit, kurz CH (Ca(OH)2), der dem Endprodukt eine hohe Alkalität mit einem pH-Wert von 12–14 verleiht. ⓘ
Nichthydraulischer Zement
Eine weniger verbreitete Form von Zement ist nichthydraulischer Zement, wie z. B. Löschkalk (mit Wasser vermischtes Kalziumoxid), der durch Karbonatisierung in Kontakt mit Kohlendioxid, das in der Luft vorhanden ist, aushärtet (~ 412 Vol. ppm ≃ 0,04 Vol. %). Zunächst wird Calciumoxid (Kalk) aus Calciumcarbonat (Kalkstein oder Kreide) durch Brennen bei Temperaturen über 825 °C (1.517 °F) für etwa 10 Stunden bei atmosphärischem Druck hergestellt:
Das Kalziumoxid wird dann verbraucht (gelöscht), indem es mit Wasser gemischt wird, um gelöschten Kalk (Kalziumhydroxid) herzustellen:
Sobald das überschüssige Wasser vollständig verdampft ist (dieser Vorgang wird technisch als Abbinden bezeichnet), beginnt die Karbonisierung:
Diese Reaktion verläuft langsam, da der Partialdruck von Kohlendioxid in der Luft niedrig ist (~ 0,4 Millibar). Die Karbonatisierungsreaktion setzt voraus, dass der trockene Zement der Luft ausgesetzt wird, so dass der gelöschte Kalk ein nichthydraulischer Zement ist und nicht unter Wasser verwendet werden kann. Dieser Prozess wird als Kalkkreislauf bezeichnet. ⓘ
Geschichte
Das vielleicht älteste bekannte Vorkommen von Zement stammt aus der Zeit vor zwölf Millionen Jahren. Ein Zementvorkommen bildete sich, nachdem ein Ölschiefervorkommen, das an ein Kalksteinbett angrenzte, durch natürliche Ursachen verbrannt war. Diese alten Ablagerungen wurden in den 1960er und 1970er Jahren untersucht. ⓘ
In der Antike verwendete Alternativen zu Zement
Zement ist chemisch gesehen ein Produkt, das Kalk als Hauptbestandteil des Bindemittels enthält, aber bei weitem nicht das erste Material, das zur Zementierung verwendet wurde. Die Babylonier und Assyrer verwendeten Bitumen, um gebrannte Ziegel oder Alabasterplatten miteinander zu verbinden. Im alten Ägypten wurden Steinblöcke mit einem Mörtel aus Sand und grob gebranntem Gips (CaSO4 - 2H2O), der oft Kalziumkarbonat (CaCO3) enthielt, zusammengeklebt. ⓘ
Die Griechen und die Römer
Kalk (Kalziumoxid) wurde auf Kreta und von den alten Griechen verwendet. Es gibt Hinweise darauf, dass die Minoer auf Kreta zerkleinerte Tonscherben als künstliches Puzzolan für hydraulischen Zement verwendeten. Niemand weiß, wer zuerst entdeckt hat, dass eine Kombination aus hydratisiertem, nichthydraulischem Kalk und einem Puzzolan eine hydraulische Mischung ergibt (siehe auch: Puzzolanische Reaktion), aber ein solcher Beton wurde von den antiken Makedoniern und drei Jahrhunderte später von römischen Ingenieuren in großem Umfang verwendet. ⓘ
Es gibt ... eine Art von Pulver, das aus natürlichen Gründen erstaunliche Ergebnisse erzielt. Man findet es in der Nähe von Baiae und im Land der Städte rund um den Vesuv. Wenn diese Substanz mit Kalk und Schutt vermischt wird, verleiht sie nicht nur Gebäuden anderer Art Festigkeit, sondern selbst wenn Pfeiler daraus im Meer gebaut werden, werden sie unter Wasser hart.
- Marcus Vitruvius Pollio, Liber II, De Architectura, Kapitel VI "Pozzolana" Sec. 1 ⓘ
Die Griechen verwendeten vulkanischen Tuffstein von der Insel Thera als Puzzolan und die Römer zerkleinerte vulkanische Asche (aktivierte Aluminiumsilikate) mit Kalk. Dieses Gemisch konnte unter Wasser aushärten, was seine Korrosionsbeständigkeit wie Rost erhöhte. Das Material wurde Puzzolan genannt, nach der Stadt Pozzuoli westlich von Neapel, wo die Vulkanasche abgebaut wurde. In Ermangelung von Puzzolanasche verwendeten die Römer pulverisierte Ziegel oder Keramik als Ersatz, und bevor sie in der Nähe von Rom natürliche Quellen entdeckten, benutzten sie möglicherweise auch zerkleinerte Fliesen für diesen Zweck. Die riesige Kuppel des Pantheons in Rom und die gewaltigen Caracalla-Thermen sind Beispiele für antike Bauwerke aus diesem Beton, von denen viele noch erhalten sind. Auch das riesige System der römischen Aquädukte machte ausgiebig Gebrauch von hydraulischem Zement. Römischer Beton wurde nur selten an der Außenseite von Gebäuden verwendet. Die übliche Technik bestand darin, Ziegelverkleidungen als Schalung für eine Füllung aus Mörtel zu verwenden, der mit einer Mischung aus zerbrochenen Steinen, Ziegeln, Scherben, wiederverwerteten Betonbrocken oder anderem Bauschutt vermischt wurde. ⓘ
Mittelalter
Es ist nicht bekannt, ob dieses Wissen in der mittelalterlichen Literatur erhalten geblieben ist, aber mittelalterliche Steinmetze und einige Militäringenieure verwendeten hydraulischen Zement aktiv bei Bauwerken wie Kanälen, Festungen, Häfen und Schiffsbauanlagen. Eine Mischung aus Kalkmörtel und Zuschlagstoffen mit Ziegel- oder Steinverkleidungen wurde sowohl im Oströmischen Reich als auch im Westen bis in die Gotik hinein verwendet. Im deutschen Rheinland wurde während des gesamten Mittelalters hydraulischer Mörtel verwendet, da es dort Puzzolanablagerungen gab, die Trass genannt wurden. ⓘ
16. Jahrhundert
Tabby ist ein Baumaterial, das aus Austernschalenkalk, Sand und ganzen Austernschalen hergestellt wird und einen Beton ergibt. Die Spanier führten es im sechzehnten Jahrhundert in Amerika ein. ⓘ
18. Jahrhundert
Die technischen Kenntnisse zur Herstellung von hydraulischem Zement wurden im 18. Jahrhundert von französischen und britischen Ingenieuren formalisiert. ⓘ
John Smeaton leistete einen wichtigen Beitrag zur Entwicklung von Zementen, als er den Bau des dritten Eddystone-Leuchtturms (1755-59) im Ärmelkanal plante, der heute als Smeaton's Tower bekannt ist. Er benötigte einen hydraulischen Mörtel, der in der Zwölf-Stunden-Periode zwischen aufeinanderfolgenden Fluten abbinden und eine gewisse Festigkeit entwickeln würde. Er experimentierte mit Kombinationen aus verschiedenen Kalksteinen und Zusätzen wie Trass und Puzzolanen und führte eine umfassende Marktforschung über die verfügbaren hydraulischen Kalke durch, wobei er die Produktionsstätten besuchte und feststellte, dass die Hydraulizität" des Kalks direkt mit dem Tongehalt des zu seiner Herstellung verwendeten Kalksteins zusammenhing. Smeaton war von Beruf Bauingenieur und verfolgte diese Idee nicht weiter. ⓘ
An der Südatlantikküste der Vereinigten Staaten wurde von den 1730er bis zu den 1860er Jahren beim Hausbau Kalkstein verwendet, der sich auf die Austernschalenmulden früherer indianischer Völker stützte. ⓘ
Vor allem in Großbritannien wurde hochwertiger Baustein in einer Zeit des raschen Wachstums immer teurer, und es wurde üblich, Prestigebauten aus den neuen Industrieziegeln zu errichten und sie mit einem Stuck zu versehen, der Stein imitieren sollte. Hierfür wurden hydraulische Kalke bevorzugt, aber der Bedarf an einer schnellen Abbindezeit förderte die Entwicklung neuer Zemente. Am bekanntesten war der "Römische Zement" von Parker. Dieser wurde von James Parker in den 1780er Jahren entwickelt und schließlich 1796 patentiert. Es handelte sich dabei nicht um das von den Römern verwendete Material, sondern um einen "natürlichen Zement", der durch Brennen von Septarien hergestellt wurde - Knollen, die in bestimmten Tonvorkommen zu finden sind und sowohl Tonmineralien als auch Kalziumkarbonat enthalten. Die verbrannten Knollen wurden zu einem feinen Pulver gemahlen. Dieses Produkt, das mit Sand zu einem Mörtel verarbeitet wurde, härtete in 5-15 Minuten aus. Der Erfolg des "Römischen Zements" veranlasste andere Hersteller, Konkurrenzprodukte zu entwickeln, indem sie künstliche hydraulische Kalkzemente aus Ton und Kreide brannten. Römischer Zement wurde schnell populär, wurde aber in den 1850er Jahren weitgehend durch Portlandzement ersetzt. ⓘ
19. Jahrhundert
Offenbar in Unkenntnis von Smeatons Arbeit entdeckte der Franzose Louis Vicat im ersten Jahrzehnt des 19. Jahrhunderts dasselbe Prinzip. Vicat entwickelte eine Methode, um Kreide und Ton zu einem innigen Gemisch zu verbinden, und stellte 1817 durch Brennen einen "künstlichen Zement" her, der als "Hauptvorläufer" des Portlandzements gilt, und "...Edgar Dobbs aus Southwark patentierte 1811 einen Zement dieser Art". ⓘ
In Russland entwickelte Egor Cheliev ein neues Bindemittel, indem er Kalk und Ton mischte. Seine Ergebnisse wurden 1822 in seinem Buch A Treatise on the Art to Prepare a Good Mortar veröffentlicht, das in St. Petersburg erschien. Einige Jahre später, 1825, veröffentlichte er ein weiteres Buch, in dem er verschiedene Methoden zur Herstellung von Zement und Beton sowie die Vorteile von Zement beim Bau von Gebäuden und Dämmen beschrieb. ⓘ

Portlandzement, die weltweit gebräuchlichste Zementart, die als Grundbestandteil von Beton, Mörtel, Stuck und nicht spezialisiertem Mörtel verwendet wird, wurde Mitte des 19. Jahrhunderts in England entwickelt und wird in der Regel aus Kalkstein hergestellt. James Frost stellte etwa zur gleichen Zeit auf ähnliche Weise den so genannten "britischen Zement" her, erhielt jedoch erst 1822 ein Patent. 1824 ließ Joseph Aspdin ein ähnliches Material patentieren, das er Portlandzement nannte, weil der daraus hergestellte Putz in der Farbe dem berühmten Portlandstein ähnelte, der auf der Isle of Portland in Dorset, England, abgebaut wird. Aspdins' Zement entsprach jedoch nicht dem modernen Portlandzement, sondern war ein erster Schritt in seiner Entwicklung, der als Proto-Portlandzement bezeichnet wurde. Der Sohn von Joseph Aspdins, William Aspdin, hatte das Unternehmen seines Vaters verlassen und stellte in den 1840er Jahren bei der Zementherstellung offenbar versehentlich Kalziumsilikate her, die einen Zwischenschritt in der Entwicklung des Portlandzements darstellten. William Aspdins Innovation war für die Hersteller "künstlicher Zemente" kontraintuitiv, denn sie erforderten mehr Kalk in der Mischung (ein Problem für seinen Vater), eine viel höhere Ofentemperatur (und damit mehr Brennstoff), und der entstehende Klinker war sehr hart und zermürbte schnell die Mühlsteine, die damals die einzige verfügbare Mahltechnik waren. Die Herstellungskosten waren daher erheblich höher, aber das Produkt härtete relativ langsam aus und entwickelte schnell eine hohe Festigkeit, wodurch sich ein Markt für die Verwendung in Beton eröffnete. Die Verwendung von Beton im Bauwesen nahm ab 1850 rasch zu und war bald die vorherrschende Verwendung für Zemente. Damit begann der Portlandzement seine vorherrschende Rolle zu spielen. Isaac Charles Johnson verfeinerte die Herstellung von Meso-Portlandzement (mittlere Entwicklungsstufe) und behauptete, er sei der eigentliche Vater des Portlandzements. ⓘ
Abbindezeit und "Frühfestigkeit" sind wichtige Eigenschaften von Zementen. Hydraulische Kalke, "natürliche" Zemente und "künstliche" Zemente sind alle auf ihren Belitgehalt (2 CaO - SiO2, abgekürzt C2S) angewiesen, um ihre Festigkeit zu entwickeln. Belit entwickelt seine Festigkeit langsam. Da sie bei Temperaturen unter 1.250 °C gebrannt wurden, enthielten sie kein Alit (3 CaO - SiO2, abgekürzt C3S), das in modernen Zementen für die frühe Festigkeit verantwortlich ist. Der erste Zement, der durchweg Alit enthielt, wurde von William Aspdin in den frühen 1840er Jahren hergestellt: Dies war das, was wir heute als "modernen" Portlandzement bezeichnen. Aufgrund der geheimnisvollen Atmosphäre, mit der William Aspdin sein Produkt umgab, haben andere (z. B. Vicat und Johnson) den Vorrang dieser Erfindung für sich beansprucht, aber neuere Analysen sowohl seines Betons als auch seines Rohzements haben gezeigt, dass das von William Aspdin in Northfleet, Kent, hergestellte Produkt ein echter Zement auf Alitbasis war. Aspdins Methoden waren jedoch "Faustregeln": Vicat ist für die Festlegung der chemischen Grundlagen dieser Zemente verantwortlich, und Johnson legte die Bedeutung der Sinterung der Mischung im Ofen fest. ⓘ
In den USA wurde der Rosendale-Zement, ein natürlicher Zement, der aus einem riesigen Dolomitvorkommen gewonnen wurde, das Anfang des 19. Jahrhunderts in der Nähe von Rosendale, New York, entdeckt wurde, erstmals in großem Umfang verwendet. Rosendale-Zement war sehr beliebt für die Gründung von Gebäuden (z. B. Freiheitsstatue, Capitol Building, Brooklyn Bridge) und die Auskleidung von Wasserleitungen. ⓘ
Sorel-Zement, ein Zement auf Magnesia-Basis, wurde 1867 von dem Franzosen Stanislas Sorel patentiert. Er war fester als Portlandzement, aber seine schlechte Wasserbeständigkeit (Auslaugung) und seine korrosiven Eigenschaften (Lochfraß aufgrund des Vorhandenseins von auslaugbaren Chloridanionen und des niedrigen pH-Werts (8,5-9,5) des Porenwassers) schränkten seine Verwendung als Stahlbeton für den Hochbau ein. ⓘ
Die nächste Entwicklung bei der Herstellung von Portlandzement war die Einführung des Drehofens. Er erzeugte eine Klinkermischung, die aufgrund der verstärkten Bildung von Alit (C3S) bei der erreichten höheren Temperatur (1450 °C) fester und homogener war. Da dem Drehrohrofen ständig Rohmaterial zugeführt wird, ermöglichte er einen kontinuierlichen Herstellungsprozess, der die Chargenproduktion mit geringerer Kapazität ablöste. ⓘ
20. Jahrhundert
Calciumaluminatzemente wurden 1908 in Frankreich von Jules Bied wegen ihrer besseren Sulfatbeständigkeit patentiert. Ebenfalls 1908 experimentierte Thomas Edison in Union, N.J., mit Betonfertigteilen für Häuser. ⓘ
In den USA wurde Rosendale-Zement nach dem Ersten Weltkrieg aufgrund seiner langen Aushärtungszeit von mindestens einem Monat für den Bau von Autobahnen und Brücken unpopulär, und viele Bundesstaaten und Bauunternehmen wandten sich dem Portlandzement zu. Aufgrund der Umstellung auf Portlandzement hatte Ende der 1920er Jahre nur noch eines der 15 Rosendale-Zementunternehmen überlebt. Doch Anfang der 1930er Jahre entdeckten die Bauherren, dass Portlandzement zwar schneller aushärtete, aber nicht so haltbar war, vor allem nicht für Autobahnen, so dass einige Staaten den Bau von Autobahnen und Straßen mit Zement einstellten. Bertrain H. Wait, ein Ingenieur, dessen Unternehmen am Bau des Catskill-Aquädukts in New York City beteiligt war, war von der Haltbarkeit des Rosendale-Zements beeindruckt und entwickelte eine Mischung aus Rosendale- und Portlandzement, die die guten Eigenschaften beider Zemente in sich vereinte. Er war sehr haltbar und härtete viel schneller aus. Wait überzeugte den New Yorker Commissioner of Highways, einen experimentellen Autobahnabschnitt in der Nähe von New Paltz, New York, mit einem Sack Rosendale-Zement zu sechs Säcken Portlandzement zu bauen. Das Experiment war ein Erfolg, und jahrzehntelang wurde die Rosendale-Portlandzement-Mischung beim Bau von Autobahnen und Brücken verwendet. ⓘ
Zementartige Materialien werden seit mehr als einem halben Jahrhundert als Immobilisierungsmatrix für Atommüll verwendet. In vielen Ländern wurden Technologien zur Zementierung von Abfällen entwickelt und im industriellen Maßstab eingesetzt. Zementgebundene Abfallformen erfordern eine sorgfältige Auswahl und ein auf die jeweilige Abfallart abgestimmtes Designverfahren, um die strengen Abfallannahmekriterien für die langfristige Lagerung und Entsorgung zu erfüllen. ⓘ
Moderne Zemente
Die Entwicklung moderner hydraulischer Zemente begann mit dem Beginn der industriellen Revolution (um 1800) und wurde durch drei Hauptbedürfnisse angetrieben:
- Hydraulischer Zementputz (Stuck) für die Fertigstellung von Ziegelgebäuden in feuchten Klimazonen
- Hydraulische Mörtel für das Mauerwerk von Hafenanlagen usw., die mit Meerwasser in Berührung kommen
- Entwicklung von festen Betonen ⓘ
Eigenschaft | Portland zement |
Kieselerde Flugasche |
Kalkhaltige Flugasche |
Schlacke zement |
Kieselsäure rauch | |
---|---|---|---|---|---|---|
SiO2 | 21.9 | 52 | 35 | 35 | 85–97 | |
Al2O3 | 6.9 | 23 | 18 | 12 | — | |
Fe2O3 | 3 | 11 | 6 | 1 | — | |
CaO | 63 | 5 | 21 | 40 | < 1 | |
MgO | 2.5 | — | — | — | — | |
SO3 | 1.7 | — | — | — | — | |
Spezifische Oberfläche (m2/kg) | 370 | 420 | 420 | 400 | 15,000 – 30,000 | |
Spezifisches Gewicht | 3.15 | 2.38 | 2.65 | 2.94 | 2.22 | |
Allgemeiner Zweck | Primäres Bindemittel | Zementersatz | Zementersatz | Zementersatz | Verbesserung der Eigenschaften | |
Moderne Zemente sind häufig Portlandzement oder Portlandzementmischungen, aber die Industrie verwendet auch andere Zemente. ⓘ
Portlandzement
Portlandzement, eine Form von hydraulischem Zement, ist die bei weitem häufigste Zementart, die weltweit verwendet wird. Dieser Zement wird durch Erhitzen von Kalkstein (Kalziumkarbonat) mit anderen Materialien (wie Ton) in einem Brennofen auf 1.450 °C hergestellt. Bei diesem als Kalzinierung bezeichneten Prozess wird ein Molekül Kohlendioxid aus dem Kalziumkarbonat freigesetzt und bildet Kalziumoxid oder Branntkalk, der sich dann mit den anderen Materialien in der Mischung chemisch verbindet und Kalziumsilikate und andere zementartige Verbindungen bildet. Die so entstandene harte Substanz, Klinker" genannt, wird dann mit einer kleinen Menge Gips zu einem Pulver gemahlen, um gewöhnlichen Portlandzement, die am häufigsten verwendete Zementart (oft als OPC bezeichnet), herzustellen. Portlandzement ist ein Grundbestandteil von Beton, Mörtel und den meisten nicht spezialisierten Mörteln. Die häufigste Verwendung von Portlandzement ist die Herstellung von Beton. Beton ist ein Verbundmaterial, das aus Zuschlagstoffen (Kies und Sand), Zement und Wasser besteht. Als Baumaterial kann Beton in fast jede beliebige Form gegossen werden und ist nach dem Aushärten ein tragendes Element. Portlandzement kann grau oder weiß sein. ⓘ
Portlandzementmischung
Portlandzementmischungen sind häufig als Zwischenmischungen von Zementherstellern erhältlich, aber ähnliche Rezepturen werden oft auch im Betonmischwerk aus den Bodenbestandteilen gemischt. ⓘ
Portlandhüttenzement oder Hochofenzement (Nomenklatur ASTM C595 bzw. EN 197-1) enthält bis zu 95 % gemahlenen Hüttensand, der Rest ist Portlandklinker und etwas Gips. Alle Zusammensetzungen weisen eine hohe Endfestigkeit auf, aber mit steigendem Schlackengehalt nimmt die Frühfestigkeit ab, während die Sulfatbeständigkeit zunimmt und die Wärmeentwicklung abnimmt. Er wird als wirtschaftliche Alternative zu sulfatbeständigen Portlandzementen und Zementen mit geringer Wärmeentwicklung verwendet. ⓘ
Portland-Flugasche-Zement enthält bis zu 40 % Flugasche nach ASTM-Normen (ASTM C595) bzw. 35 % nach EN-Normen (EN 197-1). Die Flugasche ist puzzolanisch, so dass die Endfestigkeit erhalten bleibt. Da die Zugabe von Flugasche einen niedrigeren Wassergehalt des Betons ermöglicht, kann auch die Frühfestigkeit beibehalten werden. Wo qualitativ gute und billige Flugasche verfügbar ist, kann sie eine wirtschaftliche Alternative zu gewöhnlichem Portlandzement sein. ⓘ
Portlandzement mit Puzzolanen umfasst Flugaschezement, da Flugasche ein Puzzolan ist, aber auch Zemente, die aus anderen natürlichen oder künstlichen Puzzolanen hergestellt werden. In Ländern, in denen vulkanische Asche verfügbar ist (z. B. Italien, Chile, Mexiko, Philippinen), sind diese Zemente häufig die am häufigsten verwendete Form. Die maximalen Austauschverhältnisse sind im Allgemeinen wie für Portland-Flugasche-Zement definiert. ⓘ
Portland-Silikastaubzement. Durch die Zugabe von Silikastaub können außergewöhnlich hohe Festigkeiten erzielt werden, und es werden gelegentlich Zemente mit einem Silikastaubanteil von 5-20 % hergestellt, wobei 10 % der nach EN 197-1 maximal zulässige Anteil ist. In der Regel wird dem Portlandzement jedoch erst im Betonmischer Silikastaub zugesetzt. ⓘ
Mauerzemente werden für die Herstellung von Mauermörtel und Stuck verwendet und dürfen nicht in Beton eingesetzt werden. Es handelt sich in der Regel um komplexe, geschützte Formulierungen, die Portlandklinker und eine Reihe anderer Bestandteile enthalten, darunter Kalkstein, Kalkhydrat, Luftporenbildner, Verzögerer, Wasserfestmacher und Farbstoffe. Sie sind so formuliert, dass sie verarbeitbare Mörtel ergeben, die eine schnelle und gleichmäßige Mauerwerksarbeit ermöglichen. Zu den subtilen Varianten von Mauerwerkszementen in Nordamerika gehören plastische Zemente und Stuckzemente. Sie sind so konzipiert, dass sie eine kontrollierte Verbindung mit Mauersteinen herstellen. ⓘ
Expansivzemente enthalten neben Portlandklinker auch Expansivklinker (in der Regel Sulfoaluminatklinker) und sollen die Auswirkungen des Trocknungsschwindens ausgleichen, die normalerweise bei hydraulischen Zementen auftreten. Mit diesem Zement kann Beton für Bodenplatten (bis zu 60 m im Quadrat) ohne Schwundfugen hergestellt werden. ⓘ
Weißzemente können aus weißem Klinker (der wenig oder kein Eisen enthält) und weißen Zusatzstoffen wie hochreinem Metakaolin hergestellt werden. Farbige Zemente dienen dekorativen Zwecken. Einige Normen erlauben die Zugabe von Pigmenten zur Herstellung von farbigem Portlandzement. Andere Normen (z. B. ASTM) lassen keine Pigmente in Portlandzement zu, und farbige Zemente werden als gemischte hydraulische Zemente verkauft. ⓘ
Sehr fein gemahlene Zemente sind Zement, der mit Sand, Schlacke oder anderen puzzolanartigen Mineralien gemischt und extrem fein gemahlen ist. Solche Zemente können die gleichen physikalischen Eigenschaften wie normaler Zement haben, jedoch mit 50 % weniger Zement, insbesondere aufgrund ihrer größeren Oberfläche für die chemische Reaktion. Selbst bei intensiver Vermahlung verbrauchen sie bei der Herstellung bis zu 50 % weniger Energie (und damit weniger Kohlenstoffemissionen) als herkömmliche Portlandzemente. ⓘ
Andere Zemente
Puzzolan-Kalk-Zemente sind Mischungen aus gemahlenem Puzzolan und Kalk. Diese Zemente wurden bereits von den Römern verwendet und sind in erhaltenen römischen Bauwerken wie dem Pantheon in Rom zu finden. Sie entwickeln ihre Festigkeit nur langsam, ihre Endfestigkeit kann jedoch sehr hoch sein. Die Hydratationsprodukte, die die Festigkeit erzeugen, sind im Wesentlichen die gleichen wie in Portlandzement. ⓘ
Hüttensandzemente - gemahlener Hüttensand ist nicht von sich aus hydraulisch, sondern wird durch Zugabe von Alkalien "aktiviert", am wirtschaftlichsten mit Kalk. Sie ähneln in ihren Eigenschaften den Puzzolankalkzementen. Nur granulierte Schlacke (d.h. wassergelöschte, glasartige Schlacke) ist als Zementbestandteil wirksam. ⓘ
Supersulfatzemente enthalten etwa 80 % gemahlenen Hüttensand, 15 % Gips oder Anhydrit und ein wenig Portlandklinker oder Kalk als Aktivator. Sie erzeugen Festigkeit durch Bildung von Ettringit, wobei die Festigkeit ähnlich wie bei einem langsamen Portlandzement zunimmt. Sie weisen eine gute Beständigkeit gegen aggressive Stoffe, einschließlich Sulfat, auf. Calciumaluminatzemente sind hydraulische Zemente, die hauptsächlich aus Kalkstein und Bauxit hergestellt werden. Die aktiven Bestandteile sind Monokalziumaluminat CaAl2O4 (CaO - Al2O3 oder CA in der Zementchemiker-Notation, CCN) und Mayenit Ca12Al14O33 (12 CaO - 7 Al2O3 oder C12A7 in CCN). Die Festigkeit entsteht durch Hydratation zu Calciumaluminathydraten. Sie eignen sich gut für die Verwendung in feuerfesten (hochtemperaturbeständigen) Betonen, z. B. für Ofenauskleidungen. ⓘ
Calciumsulfoaluminatzemente werden aus Klinkern hergestellt, die Ye'elimit (Ca4(AlO2)6SO4 oder C4A3S in der Schreibweise der Zementchemiker) als Primärphase enthalten. Sie werden in Expansionszementen, in Zementen mit ultrahoher Frühfestigkeit und in "niederenergetischen" Zementen verwendet. Bei der Hydratation entsteht Ettringit, und spezielle physikalische Eigenschaften (wie Ausdehnung oder schnelle Reaktion) werden durch Anpassung der Verfügbarkeit von Calcium- und Sulfationen erreicht. Ihre Verwendung als energiesparende Alternative zu Portlandzement wurde in China erprobt, wo mehrere Millionen Tonnen pro Jahr hergestellt werden. Der Energiebedarf ist aufgrund der niedrigeren Ofentemperaturen, die für die Reaktion erforderlich sind, und der geringeren Menge an Kalkstein (der endotherm entkohlt werden muss) in der Mischung geringer. Darüber hinaus führen der geringere Kalksteingehalt und der niedrigere Brennstoffverbrauch zu einem CO2-Ausstoß, der etwa halb so hoch ist wie der von Portlandklinker. Allerdings sind die SO2-Emissionen in der Regel deutlich höher. ⓘ
"Natürliche" Zemente, die bestimmten Zementen aus der Zeit vor Portland entsprechen, werden durch das Brennen von tonhaltigen Kalksteinen bei moderaten Temperaturen hergestellt. Der Anteil der Tonkomponenten im Kalkstein (etwa 30-35 %) ist so hoch, dass große Mengen Belit (das Mineral mit niedriger Frühfestigkeit und hoher Spätfestigkeit im Portlandzement) gebildet werden, ohne dass übermäßige Mengen an freiem Kalk entstehen. Wie jedes natürliche Material haben auch diese Zemente sehr unterschiedliche Eigenschaften. ⓘ
Geopolymerzemente werden aus Mischungen von wasserlöslichen Alkalimetallsilikaten und aluminosilikatischen Mineralpulvern wie Flugasche und Metakaolin hergestellt. ⓘ
Polymere Zemente werden aus organischen Chemikalien hergestellt, die polymerisieren. Die Hersteller verwenden häufig duroplastische Materialien. Sie sind zwar oft wesentlich teurer, können aber ein wasserfestes Material mit einer brauchbaren Zugfestigkeit ergeben. ⓘ
Sorel-Zement ist ein harter, dauerhafter Zement, der durch die Kombination von Magnesiumoxid und einer Magnesiumchloridlösung hergestellt wird. ⓘ
Faserzement oder faserverstärkter Beton ist ein Zement, der aus faserigen Materialien wie synthetischen Fasern, Glasfasern, Naturfasern und Stahlfasern besteht. Diese Art von Gewebe wird gleichmäßig über den nassen Beton verteilt. Der Zweck des Fasergeflechts besteht darin, den Wasserverlust des Betons zu verringern und seine strukturelle Integrität zu verbessern. Bei der Verwendung in Putzen erhöhen Fasergewebe die Kohäsionskraft, die Zugfestigkeit, die Schlagfestigkeit und die Verringerung des Schwindens; letztlich besteht der Hauptzweck dieser kombinierten Eigenschaften in der Verringerung der Rissbildung. ⓘ
Abbinden, Erhärten und Aushärten
Zement beginnt zu erstarren, wenn er mit Wasser vermischt wird, was eine Reihe von chemischen Hydratationsreaktionen auslöst. Die Bestandteile hydratisieren langsam und die Mineralhydrate verfestigen sich und härten aus. Die Verklammerung der Hydrate verleiht dem Zement seine Festigkeit. Entgegen der landläufigen Meinung härtet hydraulischer Zement nicht durch Austrocknen aus - eine ordnungsgemäße Aushärtung erfordert die Aufrechterhaltung eines angemessenen Feuchtigkeitsgehalts, der für die Hydratationsreaktionen während des Abbinde- und Erhärtungsprozesses erforderlich ist. Wenn hydraulische Zemente während der Aushärtungsphase austrocknen, kann das resultierende Produkt unzureichend hydratisiert und erheblich geschwächt sein. Empfohlen wird eine Mindesttemperatur von 5 °C und nicht mehr als 30 °C. Der Beton im jungen Alter muss vor Wasserverdunstung durch direkte Sonneneinstrahlung, hohe Temperatur, niedrige relative Luftfeuchtigkeit und Wind geschützt werden. ⓘ
Die Grenzflächenübergangszone (ITZ) ist ein Bereich des Zementleims um die Gesteinskörner im Beton. In dieser Zone kommt es zu einem allmählichen Übergang der mikrostrukturellen Merkmale. Diese Zone kann bis zu 35 Mikrometer breit sein. Andere Studien haben gezeigt, dass die Breite bis zu 50 Mikrometer betragen kann. Der durchschnittliche Gehalt an nicht umgesetzter Klinkerphase nimmt ab, und die Porosität nimmt in Richtung der Aggregatoberfläche ab. In ähnlicher Weise nimmt der Gehalt an Ettringit in ITZ zu. ⓘ
Sicherheitsaspekte
Auf Zementsäcken sind üblicherweise Gesundheits- und Sicherheitswarnungen aufgedruckt, da Zement nicht nur stark alkalisch ist, sondern der Abbindeprozess auch exotherm ist. Daher ist nasser Zement stark ätzend (pH = 13,5) und kann leicht schwere Hautverbrennungen verursachen, wenn er nicht sofort mit Wasser abgewaschen wird. Ebenso kann trockenes Zementpulver bei Kontakt mit Schleimhäuten schwere Augen- oder Atemwegsreizungen hervorrufen. Einige Spurenelemente, wie z. B. Chrom, aus Verunreinigungen, die in den zur Zementherstellung verwendeten Rohstoffen natürlich vorkommen, können allergische Dermatitis verursachen. Häufig werden dem Zement Reduktionsmittel wie Eisensulfat (FeSO4) zugesetzt, um das krebserregende sechswertige Chromat (CrO42-) in dreiwertiges Chrom (Cr3+) umzuwandeln, eine weniger giftige chemische Verbindung. Zementbenutzer müssen außerdem geeignete Handschuhe und Schutzkleidung tragen. ⓘ
Zementindustrie in der Welt


Im Jahr 2010 wurden weltweit 3.300 Megatonnen (3.600×106 kurze Tonnen) hydraulischer Zement hergestellt. Die drei größten Produzenten waren China mit 1.800, Indien mit 220 und die USA mit 63,5 Millionen Tonnen, d. h. die drei bevölkerungsreichsten Staaten der Welt produzierten insgesamt mehr als die Hälfte der Weltmenge. ⓘ
Bei der weltweiten Produktionskapazität für Zement im Jahr 2010 war die Situation ähnlich, wobei auf die drei führenden Staaten (China, Indien und USA) knapp die Hälfte der weltweiten Gesamtkapazität entfiel. ⓘ
In den Jahren 2011 und 2012 stieg der weltweite Verbrauch weiter an, auf 3585 Mio. Tonnen im Jahr 2011 und 3736 Mio. Tonnen im Jahr 2012, wobei sich die jährlichen Wachstumsraten auf 8,3 % bzw. 4,2 % abschwächten. ⓘ
China, auf das ein immer größerer Anteil des weltweiten Zementverbrauchs entfällt, bleibt der Hauptmotor des globalen Wachstums. Im Jahr 2012 lag die chinesische Nachfrage bei 2160 Mio. t, was 58 % des Weltverbrauchs entspricht. Die jährlichen Wachstumsraten, die 2010 16 % erreichten, haben sich offenbar abgeschwächt und sind 2011 und 2012 auf 5-6 % gesunken, da Chinas Wirtschaft eine nachhaltigere Wachstumsrate anstrebt. ⓘ
Außerhalb Chinas stieg der weltweite Verbrauch 2010 um 4,4 % auf 1462 Mio. t, 2011 um 5 % auf 1535 Mio. t und 2012 schließlich um 2,7 % auf 1576 Mio. t. ⓘ
Der Iran ist inzwischen der drittgrößte Zementproduzent der Welt und hat seine Produktion von 2008 bis 2011 um über 10 % gesteigert. Aufgrund der steigenden Energiekosten in Pakistan und anderen großen zementproduzierenden Ländern ist der Iran als Handelspartner in einer einzigartigen Position, da er sein eigenes überschüssiges Erdöl für den Betrieb von Klinkeranlagen nutzt. Als führender Produzent im Nahen Osten baut der Iran seine dominante Position auf den lokalen Märkten und im Ausland weiter aus. ⓘ
Die Entwicklung in Nordamerika und Europa stand im Zeitraum 2010-12 in auffälligem Kontrast zu derjenigen in China, da sich die globale Finanzkrise für viele Volkswirtschaften in dieser Region zu einer Staatsschuldenkrise und einer Rezession entwickelte. Der Zementverbrauch in dieser Region sank 2010 um 1,9 % auf 445 Mio. t, erholte sich 2011 um 4,9 % und ging 2012 erneut um 1,1 % zurück. ⓘ
Die Entwicklung in der übrigen Welt, zu der viele aufstrebende Volkswirtschaften in Asien, Afrika und Lateinamerika gehören und die im Jahr 2010 eine Zementnachfrage von etwa 1020 Mio. t repräsentierte, war positiv und konnte die Rückgänge in Nordamerika und Europa mehr als ausgleichen. Das jährliche Verbrauchswachstum lag 2010 bei 7,4 % und verlangsamte sich in den Jahren 2011 und 2012 auf 5,1 % bzw. 4,3 %. ⓘ
Zum Jahresende 2012 bestand die weltweite Zementindustrie aus 5673 Zementproduktionsanlagen, einschließlich integrierter und gemahlener Anlagen, von denen 3900 in China und 1773 in der übrigen Welt angesiedelt waren. ⓘ
Die weltweite Zementkapazität belief sich 2012 auf 5245 Mio. Tonnen, davon 2950 Mio. Tonnen in China und 2295 Mio. Tonnen im Rest der Welt. ⓘ
Rang | Land | Produktion (in Mio. t) |
Rang | Land | Produktion (in Mio. t) |
---|---|---|---|---|---|
1 | ![]() |
2.400,0 | 10 | ![]() |
58,0 |
2 | ![]() |
280,0 | 11 | ![]() |
56,0 |
3 | ![]() |
86,3 | 12 | ![]() |
54,0 |
4 | ![]() |
78,0 | 13 | ![]() |
53,0 |
5 | ![]() |
77,0 | 14 | ![]() |
35,0 |
6 | ![]() |
66,0 | 15 | ![]() |
35,0 |
7 | ![]() |
63,0 | 16 | ![]() |
32,0 |
8 | ![]() |
59,0 | 17 | ![]() |
32,0 |
9 | ![]() |
58,0 | 18 | ![]() |
23,0 |
China
"In den letzten 18 Jahren hat China durchgehend mehr Zement produziert als jedes andere Land der Welt. [...] (Jedoch) erreichte Chinas Zementexport 1994 mit 11 Millionen Tonnen seinen Höhepunkt und ist seither stetig zurückgegangen. Im Jahr 2002 wurden nur noch 5,18 Millionen Tonnen aus China exportiert. Mit einem Preis von 34 Dollar pro Tonne verdrängt der chinesische Zement den Markt, da in Thailand für dieselbe Qualität nur 20 Dollar verlangt werden. ⓘ
Im Jahr 2006 wurden in China schätzungsweise 1,235 Milliarden Tonnen Zement hergestellt, was 44 % der weltweiten Zementproduktion entspricht. "Es wird erwartet, dass die Nachfrage nach Zement in China jährlich um 5,4 % steigt und 2008 die Marke von 1 Milliarde Tonnen überschreitet, was auf ein langsames, aber gesundes Wachstum der Bauausgaben zurückzuführen ist. Der Zementverbrauch in China wird 44 % der weltweiten Nachfrage ausmachen, und China wird mit großem Abstand der größte nationale Zementverbraucher der Welt bleiben." ⓘ
Im Jahr 2010 wurden weltweit 3,3 Milliarden Tonnen Zement verbraucht. Davon entfielen 1,8 Milliarden Tonnen auf China. ⓘ
Die Zementindustrie in Deutschland gliedert sich in 22 Unternehmen, die zusammen 55 Zementwerke betreiben. Mit ca. 7.900 Mitarbeitern haben die deutschen Zementwerke im Jahr 2014 rund 32 Millionen Tonnen Zement hergestellt und dabei einen Umsatz von rund 2,5 Milliarden Euro erzielt. 1,2 Millionen Tonnen Zement wurden 2014, vorwiegend aus den europäischen Nachbarländern, importiert. Gleichzeitig exportierten die deutschen Hersteller rund 6,1 Millionen Tonnen Zement. Die Investitionsquote der Hersteller lag bei rund 6,5 Prozent. ⓘ
Umweltauswirkungen
Die Zementherstellung verursacht in allen Phasen des Prozesses Umweltauswirkungen. Dazu gehören Emissionen von Luftverschmutzung in Form von Staub, Gasen, Lärm und Erschütterungen beim Betrieb von Maschinen und bei Sprengungen in Steinbrüchen sowie Schäden an der Landschaft durch den Abbau. Anlagen zur Verringerung der Staubemissionen bei der Gewinnung und Herstellung von Zement sind weit verbreitet, und Anlagen zum Auffangen und Abscheiden von Abgasen werden zunehmend eingesetzt. Zum Umweltschutz gehört auch die Wiedereingliederung von Steinbrüchen in die Landschaft nach deren Stilllegung, indem sie der Natur zurückgegeben oder rekultiviert werden. ⓘ
CO2-Emissionen
Die Kohlenstoffkonzentration in Zement reicht von ≈5 % in Zementstrukturen bis zu ≈8 % bei Straßen aus Zement. Bei der Zementherstellung wird CO2 in die Atmosphäre freigesetzt, und zwar sowohl direkt, wenn Kalziumkarbonat erhitzt wird und dabei Kalk und Kohlendioxid entsteht, als auch indirekt durch den Einsatz von Energie, wenn bei der Herstellung CO2 freigesetzt wird. Die Zementindustrie ist für etwa 10 % der weltweiten, vom Menschen verursachten CO2-Emissionen verantwortlich, von denen 60 % auf den chemischen Prozess und 40 % auf die Verbrennung von Brennstoffen zurückzuführen sind. Eine Chatham House-Studie aus dem Jahr 2018 schätzt, dass die 4 Milliarden Tonnen Zement, die jährlich produziert werden, 8 % der weltweiten CO2-Emissionen ausmachen. ⓘ
Pro 1000 kg produziertem Portlandzement werden fast 900 kg CO2 emittiert. In der Europäischen Union konnte der spezifische Energieverbrauch für die Herstellung von Zementklinker seit den 1970er Jahren um rund 30 % gesenkt werden. Diese Verringerung des Primärenergiebedarfs entspricht etwa 11 Millionen Tonnen Kohle pro Jahr mit entsprechenden Vorteilen bei der Reduzierung der CO2-Emissionen. Dies macht etwa 5 % des anthropogenen CO2 aus. ⓘ
Der Großteil der Kohlendioxidemissionen bei der Herstellung von Portlandzement (ca. 60 %) entsteht bei der chemischen Zersetzung von Kalkstein zu Kalk, einem Bestandteil des Portlandzementklinkers. Diese Emissionen können durch eine Senkung des Klinkeranteils im Zement verringert werden. Sie können auch durch alternative Herstellungsverfahren wie das Vermahlen von Zement mit Sand oder mit Schlacke oder anderen puzzolanartigen Mineralien zu einem sehr feinen Pulver reduziert werden. ⓘ
Um den Transport schwerer Rohstoffe zu verringern und die damit verbundenen Kosten zu minimieren, ist es wirtschaftlicher, Zementwerke näher an den Kalksteinbrüchen als an den Verbraucherzentren zu bauen. ⓘ
Bei bestimmten Anwendungen nimmt Kalkmörtel einen Teil des bei seiner Herstellung freigesetzten CO2 wieder auf und hat einen geringeren Energiebedarf bei der Herstellung als herkömmlicher Zement. Neu entwickelte Zementsorten von Novacem und Eco-cement können während der Aushärtung Kohlendioxid aus der Umgebungsluft absorbieren. ⓘ
Ab 2019 soll die Kohlendioxidabscheidung und -speicherung erprobt werden, aber die finanzielle Tragfähigkeit ist ungewiss. ⓘ
Schwermetallemissionen in die Luft
Unter bestimmten Umständen, die vor allem von der Herkunft und der Zusammensetzung der verwendeten Rohstoffe abhängen, können bei der Hochtemperaturkalzinierung von Kalkstein und Tonmineralien Gase und Stäube in die Atmosphäre gelangen, die reich an flüchtigen Schwermetallen sind, von denen Thallium, Cadmium und Quecksilber die giftigsten sind. Schwermetalle (Tl, Cd, Hg, ...) und auch Selen finden sich oft als Spurenelemente in gewöhnlichen Metallsulfiden (Pyrit (FeS2), Zinkblende (ZnS), Bleiglanz (PbS), ...), die als Sekundärmineralien in den meisten Rohstoffen vorkommen. In vielen Ländern gibt es Umweltvorschriften zur Begrenzung dieser Emissionen. In den Vereinigten Staaten dürfen Zementöfen seit 2011 "gesetzlich mehr Giftstoffe in die Luft pumpen als Sondermüllverbrennungsanlagen". ⓘ
Besonderes Augenmerk wird auf die Emission von flüchtigen Spurenelementen und Schwermetallen, wie Quecksilber, Cadmium oder Thallium gelegt, während alle schwer- und nicht flüchtigen Spurenelemente durch den frisch entsäuerten Kalkstein adsorptiv gebunden werden (Prinzip der Trockensorption). In Zementen enthaltene lösliche Chromate können eine Allergie, die so genannte Maurerkrätze auslösen, wobei der hohe basische pH-Wert der wässrigen Lösung die Reizung der Haut verstärkt. ⓘ
Im Klinker enthaltene Schwermetalle
Das Vorhandensein von Schwermetallen im Klinker ergibt sich sowohl aus den natürlichen Rohstoffen als auch aus der Verwendung von recycelten Nebenprodukten oder alternativen Brennstoffen. Der im Zementporenwasser vorherrschende hohe pH-Wert (12,5 < pH < 13,5) schränkt die Mobilität vieler Schwermetalle ein, indem er ihre Löslichkeit verringert und ihre Sorption an den Mineralphasen des Zements erhöht. Nickel, Zink und Blei kommen im Zement häufig in nicht zu vernachlässigenden Konzentrationen vor. Chrom kann auch direkt als natürliche Verunreinigung aus den Rohstoffen oder als sekundäre Verunreinigung durch den Abrieb der in den Kugelmühlen verwendeten Hartchromstahllegierungen beim Mahlen des Klinkers entstehen. Da Chromat (CrO42-) giftig ist und in Spurenkonzentrationen schwere Hautallergien hervorrufen kann, wird es manchmal durch Zugabe von Eisensulfat (FeSO4) zu dreiwertigem Cr(III) reduziert. ⓘ
Verwendung von alternativen Brennstoffen und Nebenerzeugnissen
Ein Zementwerk verbraucht 3 bis 6 GJ Brennstoff pro Tonne produzierten Klinkers, je nach Rohstoffen und Verfahren. Die meisten Zementöfen verwenden heute Kohle und Petrolkoks als primäre Brennstoffe, in geringerem Maße auch Erdgas und Heizöl. Ausgewählte Abfälle und Nebenprodukte mit verwertbarem Heizwert können als Brennstoffe in einem Zementofen verwendet werden (als Co-Processing bezeichnet) und einen Teil der herkömmlichen fossilen Brennstoffe wie Kohle ersetzen, wenn sie strenge Spezifikationen erfüllen. Ausgewählte Abfälle und Nebenprodukte, die nützliche Mineralien wie Kalzium, Siliziumdioxid, Tonerde und Eisen enthalten, können als Rohmaterial im Ofen verwendet werden und Rohmaterialien wie Ton, Schiefer und Kalkstein ersetzen. Da einige Materialien sowohl einen Gehalt an nützlichen Mineralien als auch einen verwertbaren Heizwert aufweisen, ist die Unterscheidung zwischen alternativen Brennstoffen und Rohstoffen nicht immer eindeutig. Klärschlamm zum Beispiel hat einen geringen, aber signifikanten Heizwert und brennt zu Asche, die nützliche Mineralien für die Klinkermatrix enthält. Auto- und Lkw-Reifenschrott ist für die Zementherstellung nützlich, da er einen hohen Heizwert hat und das in den Reifen eingebettete Eisen als Ausgangsmaterial verwendet werden kann. ⓘ
Bei der Herstellung von Klinker werden die Rohstoffe im Hauptbrenner eines Ofens auf eine Temperatur von 1.450 °C erhitzt. Die Flamme erreicht Temperaturen von 1.800 °C. Das Material verbleibt 12-15 Sekunden lang bei 1.200 °C und 5-8 Sekunden lang bei 1.800 °C (und/oder?) (auch als Verweilzeit bezeichnet). Diese Eigenschaften eines Klinkerofens bieten zahlreiche Vorteile und gewährleisten eine vollständige Zerstörung der organischen Verbindungen, eine vollständige Neutralisierung der sauren Gase, Schwefeloxide und Chlorwasserstoff. Außerdem werden Schwermetallspuren in die Klinkerstruktur eingebettet und es entstehen keine Nebenprodukte wie Asche oder Rückstände. ⓘ
Die Zementindustrie der EU verwendet bereits mehr als 40 % Brennstoffe, die aus Abfällen und Biomasse gewonnen werden, um die thermische Energie für den Herstellungsprozess von Grauklinker bereitzustellen. Obwohl die Entscheidung für diese so genannten alternativen Brennstoffe (AF) in der Regel von den Kosten abhängt, gewinnen andere Faktoren zunehmend an Bedeutung. Der Einsatz alternativer Brennstoffe bietet sowohl für die Gesellschaft als auch für das Unternehmen Vorteile: Die CO2-Emissionen sind geringer als bei fossilen Brennstoffen, Abfälle können auf effiziente und nachhaltige Weise mitverarbeitet werden und der Bedarf an bestimmten neuen Materialien kann reduziert werden. Dennoch gibt es große Unterschiede zwischen den Mitgliedstaaten der Europäischen Union (EU), was den Anteil alternativer Brennstoffe angeht. Der gesellschaftliche Nutzen könnte verbessert werden, wenn mehr Mitgliedstaaten ihren Anteil an alternativen Kraftstoffen erhöhen würden. In der Ecofys-Studie wurden die Hindernisse und Möglichkeiten für eine weitere Verbreitung alternativer Kraftstoffe in 14 EU-Mitgliedstaaten untersucht. Die Ecofys-Studie ergab, dass lokale Faktoren das Marktpotenzial in weitaus größerem Maße einschränken als die technische und wirtschaftliche Machbarkeit der Zementindustrie selbst. ⓘ
Ökologischer Zement
Ökologischer Zement ist ein zementartiges Material, das die funktionalen Leistungsmerkmale von gewöhnlichem Portlandzement erfüllt oder übertrifft, indem es recycelte Materialien enthält und optimiert, wodurch der Verbrauch von natürlichen Rohstoffen, Wasser und Energie reduziert wird, was zu einem nachhaltigeren Baumaterial führt. Einer davon ist Geopolymerzement. ⓘ
Neue Herstellungsverfahren für ökologischen Zement werden mit dem Ziel erforscht, die Produktion und Freisetzung von schädlichen Schadstoffen und Treibhausgasen, insbesondere CO2, zu verringern oder sogar ganz zu vermeiden. ⓘ
Die wachsende Sorge um die Umwelt und die steigenden Kosten für Brennstoffe fossilen Ursprungs haben in vielen Ländern zu einer starken Verringerung der für die Zementherstellung benötigten Ressourcen und der Abwässer (Staub und Abgase) geführt. ⓘ
Ein Team der Universität Edinburgh hat das "DUPE"-Verfahren entwickelt, das auf der mikrobiellen Aktivität von Sporosarcina pasteurii basiert, einem Bakterium, das Kalziumkarbonat ausfällt, das, wenn es mit Sand und Urin gemischt wird, Mörtelblöcke mit einer Druckfestigkeit herstellen kann, die 70 % derjenigen herkömmlicher Baumaterialien entspricht. ⓘ
Einen Überblick über klimafreundliche Methoden zur Zementherstellung finden Sie hier. ⓘ
Herstellungsprozess
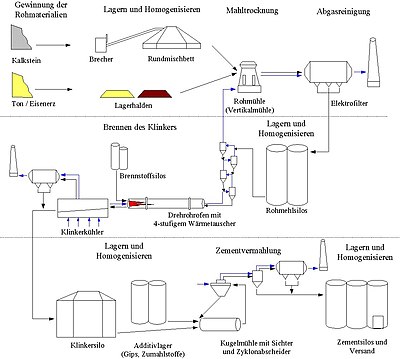
Der Ausgangsstoff für Zement wird aus überwiegend natürlichen Rohstoffen im Trockenverfahren gemahlen und gemischt, anschließend in einem kontinuierlichen Prozess in Drehrohröfen gebrannt, gekühlt und erneut gemahlen. Typische Durchsätze der Drehrohröfen sind 3.000 bis 10.000 Tonnen Klinker pro Tag. ⓘ
Vorgänger des Trockenverfahrens beim Mahlen der Rohstoffe waren Nass- und Halbnassverfahren, bei denen die Rohstoffe im nassen Zustand vermahlen und gemischt wurden. Wegen des hohen Energieaufwands beim anschließenden Trocknen sind diese Verfahren heute jedoch in der Regel nicht mehr konkurrenzfähig. ⓘ
Die Rohstoffe sind Kalkstein (Calciumcarbonat als Quelle für Calciumoxid), Ton (für Siliciumdioxid und Aluminiumoxid), Sand (für Siliciumdioxid) und Eisenerz (Eisen(III)-oxid). Durch die Zumahlung von Zusatzstoffen wie z. B. Hüttensand, Puzzolan oder Flugasche können Zemente mit verschiedenen chemischen und physikalischen Eigenschaften hergestellt werden. Gips oder Anhydrit wird dem Endprodukt zugesetzt. ⓘ
Die Rohstoffe werden in Steinbrüchen oder Tagebauen abgebaut, in Brechern vorzerkleinert und in das Zementwerk befördert. In einer Vertikalmühle oder Rohmühle werden alle Rohstoffe zusammen vermahlen und gleichzeitig getrocknet. Das dabei entstehende Rohmehl wird dann in einem Drehrohrofen bei Temperaturen von ca. 1.400–1.450 °C zu sogenanntem Zementklinker gebrannt. Beim Brennen wird das im Kalk gebundene Kohlendioxid freigesetzt. Nach Kühlen auf eine Temperatur von unter 200 °C werden die graubraunen Granalien anschließend in einer Kugelmühle zusammen mit Gips zum fertigen Produkt, dem Zement, vermahlen. ⓘ
Einteilung und Eigenschaften
Durch die Zumahlung von Stoffen wie Hüttensand, Puzzolan, Flugasche oder Kalkstein erhält man Zemente mit besonderen chemischen und physikalischen Eigenschaften. So beispielsweise:
- Zement mit niedriger Hydratationsgeschwindigkeit und niedriger Hydratationswärme: LH
- Zement mit hohem Sulfatwiderstand: SR,
- Zement mit niedrigem wirksamen Alkaligehalt: NA ⓘ
Außer der chemischen und mineralogischen Zusammensetzung ist auch die Feinheit eines Zements ausschlaggebend für seine Eigenschaften. Grundsätzlich kann gesagt werden, dass ein Zement, der feiner ist, auch eine höhere Festigkeit entwickelt. Die spezifische Oberfläche (auch als Blaine bezeichnet) dient als Maß für die Feinheit und liegt normalerweise zwischen 2.500 und 5.000 cm²/g. ⓘ
Die lose Schüttdichte von pulverförmigem Zement liegt bei 0,9 bis 1,2 kg/dm³. Diese erhöht sich durch Einrütteln auf 1,6 bis 1,9 kg/dm³. Abgebundener Zement ist mit einer Dichte von rund 3 kg/dm³ deutlich kompakter. ⓘ
Arten, Festigkeit und Verwendung nach EN 197 und DIN 1164
Bezeichnung | Druckfestigkeit [N/mm²] | Kennfarbe ⓘ | |||
---|---|---|---|---|---|
nach 2 Tagen | nach 7 Tagen | nach 28 Tagen | Sackfarbe | Aufschriftfarbe | |
32,5 L | – | ≥ 12,0 | 32,5 – 52,5 | hellbraun | |
32,5 N | – | ≥ 16,0 | schwarz | ||
32,5 R | ≥ 10,0 | – | rot | ||
42,5 L | – | ≥ 16,0 | 42,5 – 62,5 | grün | |
42,5 N | ≥ 10,0 | – | schwarz | ||
42,5 R | ≥ 20,0 | – | rot | ||
52,5 L | ≥ 10,0 | – | ≥ 52,5 | rot | |
52,5 N | ≥ 20,0 | – | schwarz | ||
52,5 R | ≥ 30,0 | – | weiß |
Die Festigkeit von Zementen wird in Europa durch die Europäische Norm EN 197 geregelt. Es wird zwischen drei verschiedenen Festigkeitsklassen unterschieden, mit Normfestigkeiten von 32,5, 42,5 und 52,5 N/mm² nach 28 Tagen Erhärtung. In Abhängigkeit von der Anfangsfestigkeit eines Zements wird dieser zudem innerhalb einer Festigkeitsklasse als langsam- (L), normal- (N) oder schnellerhärtend (R, von engl. rapid) bezeichnet. Um Verwechslungen insbesondere auf der Baustelle vorzubeugen, sind den Zementen in Deutschland Kennfarben beim Papier der Zementsäcke und dem Aufdruck zugeordnet. Die Zuordnung erfolgt in der DIN 1164. Die europäische Norm verzichtet auf solche Kennzeichnungen. ⓘ
Die EN 197-1 klassifiziert neben der Festigkeit Zemente auch nach ihrer Zusammensetzung. Fünf verschiedene Arten werden in der Norm definiert:
- CEM I – Portlandzement
- CEM II – Portlandkompositzement
- CEM III – Hochofenzement
- CEM IV – Puzzolanzement
- CEM V – Kompositzement ⓘ
Zusätzlich werden im Allgemeinen 27 Normalzementarten über die prozentualen Gewichtsanteile der Ausgangsstoffe definiert. Sonstige Zemente werden Sonderzemente genannt. Eine Beschreibungsvorschrift regelt die Bezeichnung dieser Zemente, für die in der Norm keine genaue Zusammensetzung definiert wird. ⓘ
Neben der EN 197-1 benennt in Deutschland die DIN 1164 die vorgesehenen Anwendungsbereiche der einzelnen Zementarten. Abhängig von den erwarteten Umwelteinflüssen und Einbausituationen definiert die DIN 1164 „Expositionsklassen“ und benennt die jeweils geeigneten Zementarten (z. B. eignen sich hüttensandhaltige Zemente zur Herstellung von Unterwasserbeton). ⓘ
Portlandzement




Portlandzement wird hergestellt durch die Vermahlung von Zementklinker und Kalk bzw. Anhydrit. Er besteht chemisch gesehen aus ca. 58 bis 66 % Calciumoxid (CaO), 18 bis 26 % Siliciumdioxid (SiO2), 4 bis 10 % Aluminiumoxid (Al2O3) und 2 bis 5 % Eisenoxid (Fe2O3). ⓘ
Ab einem Anteil von 36 % Hüttensand wird der Zement als Hochofenzement bezeichnet. ⓘ
In der Zahnmedizin wird eine modifizierte Form des Portlandzements unter dem Namen Mineral Trioxid Aggregat (MTA) zum retrograden Verschluss von Wurzelkanälen oder zur Perforationsdeckung verwendet. ⓘ
Spezialzemente
- Thurament
- ist ein spezieller Zement aus Hochofenschlacke bzw. Hüttensand mit einem Anteil Gips, der in Thüringen hergestellt wird. ⓘ
- Celitement
- ist ein Spezialzement, der im Gegensatz zu herkömmlichem Zement eine wesentlich günstigere Stoff- und Energiebilanz aufweist. Ähnlich robust und fest wie herkömmlicher Zement wird Celitement bei unter 300 Grad Celsius hergestellt; in einer Pilotanlage wird es bei etwa 200 Grad Celsius in einem Autoklaven „geköchelt“ und benötigt weniger Kalk als herkömmlicher Zement. Dies bringt erhebliche ökologische und ökonomische Vorteile: Energieverbrauch und Kohlenstoffdioxidausstoß reduzieren sich gegenüber der Herstellung von Portlandzement um die Hälfte. Er basiert auf vorher unbekannten hydraulisch aktiven Calciumhydrosilikaten. ⓘ
Energie- und Rohstoffverbrauch
Die Herstellung von Zementklinker erfordert einen großen Energieeinsatz. Ein gewisser Anteil des Zementklinkers lässt sich durch Zumahlstoffe mit puzzolanischen Eigenschaften ersetzen. Das Ergebnis sind sogenannte Kompositzemente. Bislang wurden häufig Hüttensand und Flugasche eingesetzt, bei denen es sich um Rest- und Abfallstoffe aus anderen Industriezweigen handelt, deren Verfügbarkeit aber rückläufig ist. ⓘ
Kalzinierter Ton wird in Zukunft voraussichtlich zum wichtigsten Kompositmaterial (auch SCM, supplementary cementitious material) zur Herstellung von Kompositzement. Tonminerale sind weltweit fast uneingeschränkt verfügbar. Die Verwendbarkeit hängt von den genauen Inhaltsstoffen und der Reinheit des Tons ab, der überwiegend aus Kaolinit, Illit und Montmorillonit besteht. ⓘ
Die Wärmeenergiebilanz des Herstellungsprozesses von Zementklinker hat sich durch die Nutzung von Abwärme aus dem Drehrohrofen, beispielsweise zur Mahltrocknung und zum Vorwärmen des Rohmehls, verbessert. ⓘ
Die Gewinnung der Rohstoffe für die Zementherstellung führte in manchen Regionen zur Vertreibung der indigenen Bevölkerung, zum Verlust ihrer Lebensgrundlage und zur Zerstörung der natürlichen Landschaften. ⓘ
Vorsichtsmaßnahmen bei der Verarbeitung
Sicherheitshinweise ⓘ | ||||||||
---|---|---|---|---|---|---|---|---|
Name |
Zement | |||||||
CAS-Nummer | ||||||||
EG-Nummer |
266-043-4 | |||||||
|
Unter Einfluss von Wasser entsteht im Zement eine Lauge mit hohem pH-Wert von bis zu 13, die zu schweren Verätzungen und Nekrosen an Haut oder Augen führen kann (Zementbrand). Da die Symptome oft erst nach Stunden auftreten, wird die Gefahr oft zu spät erkannt. Daher sollten bei der Verarbeitung von Zement Brille und Handschuhe getragen werden. Sollten bei der Verarbeitung von Zement Kleidung oder Handschuhe durch die Zementlauge durchnässt werden, sollten diese gewechselt werden. ⓘ
Wirtschaftliche Aspekte
Verbraucher
Den größten Bedarf an Zement hat die Volksrepublik China. Dort werden ungefähr 45 % der weltweiten Produktion verbaut. In den Jahren 2012–2014 wurde dieselbe Menge Zement verbaut wie im gesamten 20. Jahrhundert in den USA. Nicht nur der Bauboom Chinas, sondern auch die Bauqualität spielen hier eine Rolle, da oft binnen einiger weniger Jahrzehnte Gebäude als baufällig gelten. ⓘ
Der Jahresverbrauch an Zement ist so eine wichtige Kenngröße zur Intensität wie auch der Art der Bautätigkeit in einer Region. In Ländern wie Indonesien werden nur ca. 15 bis 20 kg pro Einwohner jährlich benötigt; in Ländern wie Singapur oder den arabischen Ländern kann der Verbrauch mehr als 2.000 kg pro Einwohner im Jahr betragen. Der Verbrauch in Deutschland beträgt etwa 350 kg pro Einwohner im Jahr, der der Schweiz ist etwa doppelt so hoch. ⓘ
Siehe auch
- Puzzolanische Reaktion
- Zementation (Geologie) ⓘ
Literatur
- Lothar Müller: Portlandzement. In: Chemie in unserer Zeit. Band 7, Nr. 1, 1973, S. 19–24, doi:10.1002/ciuz.19730070104.
- Friedrich W. Locher: Zement: Grundlagen der Herstellung und Verwendung. Verlag Bau + Technik, Düsseldorf 2000, ISBN 3-7640-0400-2.
- Verein Deutscher Zementwerke: Zement-Taschenbuch 2002, 50. Ausgabe. Verlag Bau + Technik, Düsseldorf 2002, ISBN 3-7640-0427-4.
- Wilhelm Scholz, Wolfram Hiese: Baustoffkenntnis. Werner Verlag, Köln 2007, ISBN 978-3-8041-5227-4.
- Georges Spicher, Hugo Marfurt, Nicolas Stoll: Ohne Zement geht nichts. Geschichte der schweizerischen Zementindustrie. NZZ Libro, Zürich 2013, ISBN 978-3-03823-835-5. ⓘ
Weblinks

- Zementmerkblatt B1: Zemente und ihre Herstellung (PDF-Datei; 309 kB)
- Zement-Taschenbuch, 50. Auflage 2002 (PDF-Datei; 7,3 MB)
- Initiative für Nachhaltigkeit in der deutschen Zementindustrie
- Virtuelle Zementfabrik
- Deutsches Zementmuseum in Hemmoor an der Oste
- Die Entwicklung des deutschen Cementes, Der Architekt, 1895 ⓘ
Verbände
- Verein Deutscher Zementwerke e.V.
- Vereinigung der Österreichischen Zementindustrie
- Verband der Schweizerischen Cementindustrie
- VDZ – Darstellung der Geschichte ⓘ