Beton

Beton ist ein Verbundwerkstoff, der aus feinen und groben Zuschlägen besteht, die mit einem flüssigen Zement (Zementleim) verbunden sind, der im Laufe der Zeit aushärtet (aushärtet). Beton ist nach Wasser die am zweithäufigsten verwendete Substanz der Welt und das am häufigsten verwendete Baumaterial. Sein weltweiter Verbrauch, Tonne für Tonne, ist doppelt so hoch wie der von Stahl, Holz, Kunststoff und Aluminium zusammen. Weltweit wird die Transportbetonindustrie, das größte Segment des Betonmarktes, bis 2025 voraussichtlich einen Umsatz von über 600 Milliarden Dollar erzielen. Diese weit verbreitete Verwendung hat eine Reihe von Umweltauswirkungen zur Folge. Vor allem der Herstellungsprozess von Zement verursacht große Mengen an Treibhausgasemissionen, die netto 8 % der weltweiten Emissionen ausmachen. Zu den weiteren Umweltproblemen gehören der weit verbreitete illegale Sandabbau, die Auswirkungen auf die Umgebung, wie z. B. der verstärkte Oberflächenabfluss oder der städtische Wärmeinseleffekt, sowie mögliche Auswirkungen auf die öffentliche Gesundheit durch toxische Inhaltsstoffe. Es werden erhebliche Forschungs- und Entwicklungsanstrengungen unternommen, um die Emissionen zu verringern oder Beton zu einer Quelle der Kohlenstoffbindung zu machen und den Anteil an recycelten und sekundären Rohstoffen in der Mischung zu erhöhen, um eine Kreislaufwirtschaft zu erreichen. Es wird erwartet, dass Beton ein Schlüsselmaterial für Strukturen sein wird, die gegen Klimakatastrophen resistent sind, sowie eine Lösung, um die Umweltverschmutzung anderer Industrien zu mindern, indem Abfälle wie Kohleflugasche oder Bauxitabfälle und -rückstände aufgefangen werden. ⓘ

Wenn die Zuschlagstoffe mit trockenem Portlandzement und Wasser vermischt werden, bildet die Mischung einen flüssigen Brei, der sich leicht gießen und in Form bringen lässt. Der Zement reagiert mit dem Wasser in einem Prozess, der als Betonhydratation bezeichnet wird und über mehrere Stunden hinweg aushärtet, um eine harte Matrix zu bilden, die die Materialien zu einem dauerhaften, steinähnlichen Material verbindet, das vielseitig einsetzbar ist. In dieser Zeit kann Beton nicht nur in Formen gegossen, sondern auch mit einer Vielzahl von Werkzeugen bearbeitet werden. Der Hydratationsprozess ist exotherm, was bedeutet, dass die Umgebungstemperatur eine wichtige Rolle dabei spielt, wie lange der Beton zum Abbinden braucht. Häufig werden der Mischung Zusatzstoffe (wie Puzzolane oder Fließmittel) beigefügt, um die physikalischen Eigenschaften der nassen Mischung zu verbessern, die Aushärtungszeit zu verzögern oder zu beschleunigen oder das fertige Material anderweitig zu verändern. Der meiste Beton wird mit eingebettetem Bewehrungsmaterial (z. B. Bewehrungsstäben) gegossen, um die Zugfestigkeit zu erhöhen, was zu bewehrtem Beton führt. ⓘ
In der Vergangenheit wurden häufig Zementbindemittel auf Kalkbasis, wie z. B. Kalkspachtel, verwendet, manchmal aber auch andere hydraulische (wasserbeständige) Zemente, wie z. B. Kalziumaluminatzement, oder Portlandzement, um Portlandzementbeton (benannt nach seiner optischen Ähnlichkeit mit Portlandstein) herzustellen. Es gibt viele andere, nicht zementgebundene Betonarten, bei denen die Zuschlagstoffe auf andere Weise miteinander verbunden werden, darunter Asphaltbeton mit einem Bitumenbindemittel, der häufig für Straßenbeläge verwendet wird, und Polymerbeton, der Polymere als Bindemittel verwendet. Beton unterscheidet sich von Mörtel. Während Beton selbst ein Baumaterial ist, ist Mörtel ein Bindemittel, das normalerweise Ziegel, Fliesen und andere Mauersteine zusammenhält. ⓘ



Beton ([beˈtõ], [beˈtɔŋ] österr. und z. T. bayr. [beˈtoːn]; schweiz. und alem. 1. Silbe betont [ˈbetɔ̃], vom gleichbedeutenden franz. Wort béton,) ist ein Baustoff, der als Dispersion unter Zugabe von Flüssigkeit aus einem Bindemittel und Zuschlagstoffen angemischt wird. Der ausgehärtete Beton wird in manchen Zusammenhängen auch als Kunststein bezeichnet. ⓘ
Normalbeton enthält Zement als Bindemittel und Gesteinskörnung (früher Zuschlag) als Zuschlagstoff. Das Zugabewasser (früher Anmachwasser) leitet den chemischen Abbindevorgang, d. h. die Erhärtung ein. Um die Verarbeitbarkeit und weitere Eigenschaften des Betons zu beeinflussen, werden der Mischung Betonzusatzstoffe und Betonzusatzmittel beigemengt. Das Wasser wird zum größten Teil chemisch gebunden. Die vollständige Trocknung des Gemischs darf daher erst nach der Erhärtung erfolgen. ⓘ
Frischer Beton kann als Zweistoffsystem aus flüssigem Zementleim und festem Zuschlag angesehen werden. Zementleim härtet zu Zementstein. Dieser bildet die Matrix, welche die Gesteinskörnung umgibt. ⓘ
Beton wird heute überwiegend als Verbundwerkstoff in Kombination mit einer zugfesten Bewehrung eingesetzt. Die Verbindung mit Betonstahl oder Spannstahl ergibt Stahlbeton bzw. Spannbeton. Neuere Entwicklungen sind Faserbeton mit Zugabe von Stahl-, Kunststoff- oder Glasfasern, sowie Textilbeton, der Gewirke (Textil) aus alkaliresistentem AR-Glas oder Kohlenstofffasern enthält. ⓘ
Als problematisch gilt bislang der Einfluss der Betonproduktion auf die Umwelt. Die Betonindustrie gehört zu den Hauptverursachern von Treibhausgasen, die die globale Erwärmung bewirken. Die Betonproduktion ist für etwa 6 bis 9 % aller menschengemachten CO2-Emissionen verantwortlich, was dem Drei- bis Vierfachen der Größenordnung des gesamten Luftverkehrs entspricht. ⓘ
Es werden weltweit erhebliche Mengen Wasser, Kies, Zement und Sand für die Herstellung von Beton verbraucht. Das globale Vorkommen an geeignetem Sand wird vor allem durch die Betonherstellung immer knapper. ⓘ
Etymologie
Das Wort Beton stammt vom lateinischen Wort "concretus" (kompakt oder verdichtet), dem Partizip Perfekt Passiv von "concrescere", von "con-" (zusammen) und "crescere" (wachsen). ⓘ
Geschichte
Antike Zeiten
Der Maya-Beton in den Ruinen von Uxmal wird in Incidents of Travel in the Yucatán von John L. Stephens erwähnt. "Das Dach ist flach und wurde mit Zement bedeckt". "Die Böden waren aus Zement, an manchen Stellen hart, aber durch lange Einwirkung gebrochen und jetzt unter den Füßen bröckelnd." "Aber die Wände waren durchweg massiv und bestanden aus großen, in Mörtel eingebetteten Steinen, die fast so hart wie Felsen waren." ⓘ
Die Herstellung von betonähnlichen Materialien in kleinem Maßstab wurde von den nabatäischen Händlern vorangetrieben, die ab dem 4. Jahrhundert v. Chr. eine Reihe von Oasen besetzten und kontrollierten und ein kleines Reich in den Regionen Südsyriens und Nordjordaniens aufbauten. Jahrhundert v. Chr. ein kleines Reich in Südsyrien und Nordjordanien errichteten. 700 v. Chr. entdeckten sie die Vorteile des hydraulischen Kalkes, der auch selbstzementierende Eigenschaften besitzt. Sie bauten Brennöfen, um Mörtel für den Bau von Häusern aus Bruchsteinmauerwerk, Betonböden und unterirdischen wasserdichten Zisternen zu gewinnen. Die Zisternen hielten sie geheim, da sie den Nabatäern das Überleben in der Wüste ermöglichten. Einige dieser Bauten sind bis heute erhalten geblieben. ⓘ
Klassisches Zeitalter


In der altägyptischen und später in der römischen Epoche entdeckten die Baumeister, dass die Zugabe von Vulkanasche zu der Betonmischung ein Aushärten unter Wasser ermöglichte. ⓘ
Betonböden wurden im Königspalast von Tiryns, Griechenland, gefunden, der etwa aus der Zeit 1400-1200 v. Chr. stammt. Kalkmörtel wurden 800 v. Chr. in Griechenland, Kreta und Zypern verwendet. Beim assyrischen Jerwan-Aquädukt (688 v. Chr.) wurde wasserdichter Beton verwendet. Beton wurde bei vielen antiken Bauwerken verwendet. ⓘ
Die Römer setzten Beton von 300 v. Chr. bis 476 n. Chr. in großem Umfang ein. Während des Römischen Reiches wurde römischer Beton (oder opus caementicium) aus Branntkalk, Puzzolan und einem Bimsstein hergestellt. Seine weit verbreitete Verwendung in vielen römischen Bauwerken, ein Schlüsselereignis in der Geschichte der Architektur, das als römische architektonische Revolution bezeichnet wird, befreite das römische Bauwesen von den Beschränkungen der Materialien Stein und Ziegel. Er ermöglichte revolutionäre neue Entwürfe sowohl in Bezug auf die strukturelle Komplexität als auch auf die Abmessungen. Das Kolosseum in Rom wurde größtenteils aus Beton gebaut, und das Pantheon hat die größte unbewehrte Betonkuppel der Welt. ⓘ
Beton, wie ihn die Römer kannten, war ein neues und revolutionäres Material. Er wurde in Form von Bögen, Gewölben und Kuppeln verlegt und härtete schnell zu einer starren Masse aus, die frei von vielen der inneren Belastungen war, die den Erbauern ähnlicher Strukturen aus Stein oder Ziegeln zu schaffen machten. ⓘ
Moderne Tests zeigen, dass opus caementicium die gleiche Druckfestigkeit hatte wie moderner Portland-Zementbeton (ca. 200 kg/cm2 [20 MPa; 2.800 psi]). Aufgrund der fehlenden Bewehrung war seine Zugfestigkeit jedoch weitaus geringer als die des modernen Stahlbetons, und auch die Art der Anwendung unterschied sich:
Der moderne Konstruktionsbeton unterscheidet sich vom römischen Beton in zwei wichtigen Details. Erstens ist die Konsistenz der Betonmischung flüssig und homogen, so dass sie in Formen gegossen werden kann und nicht von Hand zusammen mit dem Zuschlagstoff, der in der römischen Praxis oft aus Schotter bestand, eingebracht werden muss. Zweitens verleiht integrierter Bewehrungsstahl modernen Betonbauteilen eine hohe Zugfestigkeit, während römischer Beton nur von der Stärke der Betonbindung abhängen konnte, um Spannungen standzuhalten. ⓘ
Die langfristige Haltbarkeit römischer Betonkonstruktionen ist nachweislich auf die Verwendung von pyroklastischem (vulkanischem) Gestein und Asche zurückzuführen, wobei die Kristallisation von Strätlingit (ein spezifisches und komplexes Kalziumaluminiumsilikathydrat) und die Koaleszenz dieses und ähnlicher Kalziumaluminiumsilikathydrat-Zementbindemittel dazu beitrugen, dass der Beton selbst in seismisch aktiven Umgebungen ein höheres Maß an Bruchsicherheit aufwies. Römischer Beton ist wesentlich widerstandsfähiger gegen Erosion durch Meerwasser als moderner Beton; er verwendete pyroklastische Materialien, die mit Meerwasser reagieren und im Laufe der Zeit Al-Tobermorit-Kristalle bilden. ⓘ
Die weit verbreitete Verwendung von Beton in vielen römischen Bauwerken hat dafür gesorgt, dass viele von ihnen bis heute erhalten sind. Die Caracalla-Thermen in Rom sind nur ein Beispiel dafür. Viele römische Aquädukte und Brücken, wie der prächtige Pont du Gard in Südfrankreich, haben eine Verkleidung aus Mauerwerk auf einem Betonkern, ebenso wie die Kuppel des Pantheons. ⓘ
Nach dem Zusammenbruch des Römischen Reiches wurde Beton nur noch selten verwendet, bis die Technologie Mitte des 18. Jahrhunderts neu entwickelt wurde. Weltweit hat Beton den Stahl in Bezug auf die Menge des verwendeten Materials überholt. ⓘ
Dauerhafter Kalkmörtel als Bindemittel konnte schon an 10.000 Jahre alten Bauwerksresten in der heutigen Türkei nachgewiesen werden. Gebrannten Kalk verwendeten die Ägypter beim Bau der Pyramiden. ⓘ
In der zweiten Hälfte des 3. vorchristlichen Jahrhunderts wurde in Karthago oder Kampanien eine Betonmischung aus Zement und Ziegelsplittern entwickelt. Diese wurde gegen Ende des Zweiten Punischen Krieges erstmals beim Bau von Wohngebäuden in Rom verwendet. Die Römer entwickelten aus dieser Betonmischung in der Folgezeit das Opus caementitium (opus = Werk, Bauwerk; caementitium = Zuschlagstoff, Bruchstein), aus dessen Namen das Wort Zement abgeleitet ist. Dieser Baustoff, auch als römischer Beton oder Kalkbeton bezeichnet, bestand aus gebranntem Kalk, Wasser und Sand, dem mortar (Mörtel), gemischt mit Ziegelmehl und Vulkanasche, und zeichnete sich durch eine hohe Druckfestigkeit aus. Damit wurden unter anderem die Aquädukte und die Kuppel des Pantheons in Rom hergestellt, die einen Durchmesser von 43 Metern hat und bis heute erhalten ist. ⓘ
Eine wesentliche Verbesserung, die von den Römern entwickelt wurde, war die Verwendung inerter Zuschlagsstoffe, die hauptsächlich aus Resten von gebranntem Ziegelmaterial bestanden und die Eigenschaft besitzen, bei Temperaturänderungen keine Risse zu bilden. Dies kann noch heute an Orten in Nordafrika (z. B. Leptis Magna, Kyrene) beobachtet werden, wo es große Estrichflächen gibt, die etwa um 200–300 n. Chr. ausgeführt wurden und die trotz großer Temperaturdifferenzen zwischen Tag und Nacht noch heute völlig frei von Rissen sind. ⓘ
Das Mittelalter
Nach dem Römischen Reich wurde die Verwendung von gebranntem Kalk und Puzzolan stark reduziert. Niedrige Ofentemperaturen beim Brennen von Kalk, Mangel an Puzzolan und schlechtes Mischen trugen zu einer Verschlechterung der Qualität von Beton und Mörtel bei. Ab dem 11. Jahrhundert führte die zunehmende Verwendung von Stein im Kirchen- und Burgenbau zu einer steigenden Nachfrage nach Mörtel. Im 12. Jahrhundert begann sich die Qualität durch besseres Mahlen und Sieben zu verbessern. Mittelalterliche Kalkmörtel und -betone waren nicht hydraulisch und wurden zum Binden von Mauerwerk, zum "hearting" (Binden von Bruchsteinmauerwerkskernen) und für Fundamente verwendet. Bartholomaeus Anglicus beschreibt in seinem De proprietatibus rerum (1240) die Herstellung von Mörtel. In einer englischen Übersetzung von 1397 heißt es: "lyme ... is a stone brent; by medlynge thereof with sonde and water sement is made". Ab dem 14. Jahrhundert war die Qualität des Mörtels wieder ausgezeichnet, aber erst ab dem 17. Jahrhundert wurde üblicherweise Puzzolan zugesetzt. ⓘ
Der Canal du Midi wurde 1670 mit Beton gebaut. ⓘ
Industriezeitalter
Das Wort Beton ist übernommen aus gleichbedeutendem französisch béton, dieses aus altfranzösisch betun (Mörtel, Zement), abgeleitet von lateinisch bitumen (schlammiger Sand, Erdharz, Bergteer, Kitt). Bernard de Bélidor beschreibt die Herstellung und Verwendung von Beton in seinem Standardwerk Architecture hydraulique (Bd. 2, Paris 1753). Das Wort erscheint dann auch in der deutschen Übersetzung Architectura hydraulica (Bd. 2, Augsburg 1769). ⓘ
Die Entwicklung des Betons in der Neuzeit begann 1755 mit dem Engländer John Smeaton. Dieser führte, auf der Suche nach einem wasserbeständigen Mörtel, Versuche mit gebrannten Kalken und Tonen durch und stellte fest, dass für einen selbsterhärtenden (hydraulischen) Kalk ein bestimmter Anteil an Ton notwendig ist. ⓘ
Drei Erfindungen leiteten letztlich den modernen Betonbau ein:
- Die des Romanzements 1796 durch den Engländer J. Parker,
- die des künstlichen hydraulischen Kalks durch Louis-Joseph Vicat 1818 sowie
- die des Portlandzements durch Joseph Aspdin im Jahr 1824.
Zunächst wurde der Beton noch nicht armiert, sondern als Stampfbeton, ähnlich dem Pissébau, verwendet. Das älteste und auch erhaltene Gebäude in dieser Technik ist die Villa Lebrun in Marssac-sur-Tarn, die der Bauingenieur François Martin Lebrun für seinen Bruder errichtete. ⓘ
Mitte des 19. Jahrhunderts entstanden in Deutschland die ersten aus Beton errichteten Wohngebäude wie die Bahnwärterhäuser der Oberschwäbischen Eisenbahn, einige Mietshäuser der Berliner Victoriastadt und die Villa Merkel. ⓘ
Ein wesentlicher Entwicklungssprung war die Erfindung des Stahlbetons durch Joseph Monier (Patent: 1867), durch den die Herstellung auf Zug belasteter Bauelemente möglich wurde, wie etwa Platten und Unterzüge. Zurückgreifend auf Joseph Monier wird Bewehrungsstahl oder Betonstahl auch heute noch gelegentlich als Moniereisen bezeichnet. ⓘ
Beton wird in der zeitgenössischen Kunst auch für Denkmäler oder Skulpturen verarbeitet („Kunststein“). ⓘ

Der vielleicht größte Fortschritt bei der modernen Verwendung von Beton war der Smeaton-Turm, den der britische Ingenieur John Smeaton zwischen 1756 und 1759 in Devon, England, errichtete. Dieser dritte Eddystone-Leuchtturm leistete Pionierarbeit bei der Verwendung von hydraulischem Kalk in Beton, wobei Kieselsteine und Ziegelmehl als Zuschlagstoffe verwendet wurden. ⓘ
Ein Verfahren zur Herstellung von Portlandzement wurde in England entwickelt und 1824 von Joseph Aspdin patentiert. Aspdin wählte den Namen wegen seiner Ähnlichkeit mit dem Portlandstein, der auf der Isle of Portland in Dorset, England, abgebaut wurde. Sein Sohn William setzte die Entwicklungen bis in die 1840er Jahre fort und erwarb sich damit Anerkennung für die Entwicklung des "modernen" Portlandzements. ⓘ
Zusammensetzung
Beton ist ein künstlicher Verbundwerkstoff, der aus einer Matrix aus einem zementhaltigen Bindemittel (in der Regel Portlandzement oder Asphalt) und einer dispergierten Phase oder einem "Füllstoff" aus Zuschlagstoffen (in der Regel ein felsiges Material, lose Steine und Sand) besteht. Das Bindemittel "klebt" den Füllstoff zusammen und bildet ein synthetisches Konglomerat. Es gibt viele Arten von Beton, die durch die Zusammensetzung der Bindemittel und die Art der Zuschlagstoffe bestimmt werden, die für die Anwendung des technischen Materials verwendet werden. Diese Variablen bestimmen die Festigkeit und Dichte sowie die chemische und thermische Beständigkeit des Endprodukts. ⓘ
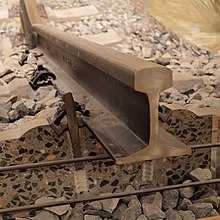
Zuschlagstoffe sind große Materialbrocken in einer Betonmischung, in der Regel grober Kies oder zerkleinertes Gestein wie Kalkstein oder Granit, zusammen mit feineren Materialien wie Sand. ⓘ
Zementleim, der meist aus Portlandzement hergestellt wird, ist die gängigste Art von Betonbindemittel. Bei zementhaltigen Bindemitteln wird Wasser mit dem trockenen Zementpulver und den Zuschlagstoffen gemischt, wodurch eine halbflüssige Aufschlämmung (Paste) entsteht, die geformt werden kann, in der Regel durch Gießen in eine Form. Der Beton verfestigt sich und härtet durch einen chemischen Prozess, der Hydratation genannt wird. Das Wasser reagiert mit dem Zement, der die anderen Bestandteile miteinander verbindet, wodurch ein robustes, steinähnliches Material entsteht. Andere zementhaltige Materialien wie Flugasche und Hüttenzement werden manchmal zugegeben - entweder als Vormischung mit dem Zement oder direkt als Betonbestandteil - und werden zu einem Teil des Bindemittels für die Zuschlagstoffe. Flugasche und Schlacke können einige Eigenschaften des Betons verbessern, z. B. die Frischbetoneigenschaften und die Dauerhaftigkeit. Alternativ können auch andere Materialien als Betonbindemittel verwendet werden: Der am weitesten verbreitete Ersatz ist Asphalt, der als Bindemittel für Asphaltbeton verwendet wird. ⓘ
Zusatzmittel werden hinzugefügt, um die Aushärtungsgeschwindigkeit oder die Eigenschaften des Materials zu verändern. Mineralische Zusatzmittel verwenden recycelte Materialien als Betonbestandteile. Zu den auffälligen Materialien gehören Flugasche, ein Nebenprodukt von Kohlekraftwerken, gemahlene Hochofenschlacke, ein Nebenprodukt der Stahlherstellung, und Silikatstaub, ein Nebenprodukt von industriellen Lichtbogenöfen. ⓘ
Bauwerke aus Portlandzementbeton enthalten in der Regel eine Stahlbewehrung, da diese Art von Beton zwar eine hohe Druckfestigkeit, aber immer eine geringere Zugfestigkeit aufweist. Daher wird er in der Regel mit zugfesten Materialien bewehrt, in der Regel mit Stahlstäben. ⓘ
Die Zusammensetzung der Betonmischung hängt von der Art des Bauwerks ab, wie der Beton gemischt und geliefert wird und wie er in das Bauwerk eingebracht wird. ⓘ
Zement
Portlandzement ist die gängigste Zementart, die allgemein verwendet wird. Er ist ein Grundbestandteil von Beton, Mörtel und vielen Putzen. Der britische Maurer Joseph Aspdin ließ den Portlandzement im Jahr 1824 patentieren. Seinen Namen erhielt er wegen der Ähnlichkeit seiner Farbe mit dem Portland-Kalkstein, der auf der englischen Insel Portland abgebaut und in der Londoner Architektur häufig verwendet wird. Er besteht aus einer Mischung von Kalziumsilikaten (Alit, Belit), Aluminaten und Ferriten - Verbindungen, die Kalzium, Silizium, Aluminium und Eisen in einer Form kombinieren, die mit Wasser reagiert. Portlandzement und ähnliche Materialien werden durch Erhitzen von Kalkstein (einer Kalziumquelle) mit Ton oder Schiefer (einer Silizium-, Aluminium- und Eisenquelle) und Mahlen dieses Produkts (Klinker genannt) mit einer Sulfatquelle (meist Gips) hergestellt. ⓘ
In modernen Zementöfen werden viele fortschrittliche Funktionen eingesetzt, um den Brennstoffverbrauch pro Tonne produzierten Klinkers zu senken. Zementöfen sind extrem große, komplexe und von Natur aus staubige Industrieanlagen und haben Emissionen, die kontrolliert werden müssen. Von den verschiedenen Bestandteilen, die zur Herstellung einer bestimmten Menge Beton verwendet werden, ist der Zement der energetisch teuerste. Selbst komplexe und effiziente Brennöfen benötigen 3,3 bis 3,6 Gigajoule Energie, um eine Tonne Klinker zu produzieren und ihn anschließend zu Zement zu mahlen. Viele Öfen können mit schwer zu entsorgenden Abfällen befeuert werden, am häufigsten mit Altreifen. Aufgrund der extrem hohen Temperaturen und der langen Verweildauer bei diesen Temperaturen können Zementöfen auch schwer zu verwertende Brennstoffe effizient und vollständig verbrennen. ⓘ
Wasser
Durch die Verbindung von Wasser mit einem zementhaltigen Material entsteht durch den Prozess der Hydratation ein Zementstein. Der Zementleim klebt die Gesteinskörnung zusammen, füllt Hohlräume aus und macht sie fließfähiger. ⓘ
Nach dem Abrams'schen Gesetz ergibt ein geringerer Wasser-Zement-Wert einen festeren, dauerhafteren Beton, während mehr Wasser einen besser fließenden Beton mit einem höheren Setzmaß ergibt. Unreines Wasser, das zur Herstellung von Beton verwendet wird, kann Probleme beim Abbinden oder ein vorzeitiges Versagen des Bauwerks verursachen. ⓘ
Portlandzement besteht aus fünf Hauptverbindungen von Kalziumsilikaten und Alumninaten mit einem Gewichtsanteil von 5 bis 50 %, die alle hydratisiert werden und zur Festigkeit des Endmaterials beitragen. Die Hydratation von Zement umfasst also viele Reaktionen, die oft gleichzeitig ablaufen. Im Laufe der Reaktionen verbinden sich die Produkte der Zementhydratation allmählich mit den einzelnen Sand- und Kiespartikeln und anderen Bestandteilen des Betons zu einer festen Masse. ⓘ
Hydratation von Tricalciumsilicat
- Zementchemiker-Schreibweise: C3S + H → C-S-H + CH + Wärme
- Standardschreibweise: Ca3SiO5 + H2O → (CaO)-(SiO2)-(H2O)(Gel) + Ca(OH)2
- Gleichgewicht: 2Ca3SiO5 + 7H2O → 3(CaO)-2(SiO2)-4(H2O)(gel) + 3Ca(OH)2 (ungefähr; die genauen Verhältnisse von CaO, SiO2 und H2O in C-S-H können variieren) ⓘ
Aufgrund der Art der chemischen Bindungen, die bei diesen Reaktionen entstehen, und der endgültigen Eigenschaften der gebildeten Partikel wird der Prozess der Zementhydratation als irreversibel angesehen, was Methoden des Zementrecyclings unmöglich macht. ⓘ
Gesteinskörnungen
Feine und grobe Zuschläge bilden den Hauptbestandteil einer Betonmischung. Zu diesem Zweck werden hauptsächlich Sand, Naturkies und Schotter verwendet. Recycelte Gesteinskörnungen (aus Bau-, Abbruch- und Aushubabfällen) werden zunehmend als teilweiser Ersatz für natürliche Gesteinskörnungen verwendet, während eine Reihe von hergestellten Gesteinskörnungen, darunter luftgekühlte Hochofenschlacke und Schlacke, ebenfalls zugelassen sind. ⓘ
Die Korngrößenverteilung der Gesteinskörnung bestimmt, wie viel Bindemittel erforderlich ist. Gesteinskörnungen mit einer sehr gleichmäßigen Größenverteilung weisen die größten Lücken auf, während die Zugabe von Gesteinskörnungen mit kleineren Partikeln diese Lücken tendenziell auffüllt. Das Bindemittel muss die Lücken zwischen den Gesteinskörnern füllen und die Oberflächen der Gesteinskörner verkleben und ist in der Regel die teuerste Komponente. Die Variation der Gesteinskörnungen senkt also die Kosten des Betons. Die Gesteinskörnung ist fast immer fester als das Bindemittel, so dass sich ihre Verwendung nicht negativ auf die Festigkeit des Betons auswirkt. ⓘ
Die Umverteilung der Gesteinskörnung nach der Verdichtung führt häufig zu einer Inhomogenität aufgrund von Schwingungseinflüssen. Dies kann zu einem Festigkeitsgefälle führen. ⓘ
Dekorative Steine wie Quarzit, kleine Flusssteine oder zerkleinertes Glas werden manchmal auf die Betonoberfläche aufgebracht, um eine dekorative "Waschbeton"-Oberfläche zu schaffen, die bei Landschaftsgestaltern beliebt ist. ⓘ
Zusatzmittel
Zusatzmittel sind Materialien in Form von Pulver oder Flüssigkeiten, die dem Beton zugesetzt werden, um ihm bestimmte Eigenschaften zu verleihen, die mit normalen Betonmischungen nicht erreicht werden können. Zusatzmittel werden als Zusätze definiert, die bei der Herstellung der Betonmischung zugefügt werden. Die gängigsten Zusatzmittel sind Verzögerer und Beschleuniger. Bei normaler Verwendung beträgt die Dosierung der Zusatzmittel weniger als 5 Massenprozent des Zements und wird dem Beton zum Zeitpunkt der Dosierung/Mischung zugegeben. (Siehe § Herstellung unten.) Die gebräuchlichen Arten von Zusatzmitteln sind wie folgt:
- Beschleuniger beschleunigen die Hydratation (Aushärtung) des Betons. Typische Zusatzstoffe sind Calciumchlorid, Calciumnitrat und Natriumnitrat. Die Verwendung von Chloriden kann jedoch zu Korrosion der Stahlbewehrung führen und ist in einigen Ländern verboten, so dass Nitrate bevorzugt werden, auch wenn sie weniger wirksam sind als das Chlorsalz. Beschleunigende Zusatzmittel sind besonders nützlich, um die Eigenschaften von Beton bei kaltem Wetter zu verändern.
- Luftporenbildner fügen dem Beton winzige Luftbläschen hinzu und binden sie ein, was die Schäden während der Frost-Tau-Zyklen verringert und die Haltbarkeit erhöht. Die Lufteinschlüsse sind jedoch mit einem Kompromiss bei der Festigkeit verbunden, da jedes 1 % Luft die Druckfestigkeit um 5 % verringern kann. Wenn durch den Mischvorgang zu viel Luft im Beton eingeschlossen wird, können Entschäumer eingesetzt werden, um die Luftblasen zu agglomerieren, an die Oberfläche des nassen Betons aufzusteigen und sich dann zu verteilen.
- Haftvermittler werden verwendet, um eine Verbindung zwischen altem und neuem Beton (in der Regel eine Art Polymer) mit hoher Temperaturtoleranz und Korrosionsbeständigkeit herzustellen.
- Korrosionsinhibitoren werden verwendet, um die Korrosion von Stahl und Stahlstäben im Beton zu minimieren.
- Kristalline Zusatzmittel werden in der Regel bei der Herstellung des Betons hinzugefügt, um die Durchlässigkeit zu verringern. Bei Kontakt mit Wasser und unhydrierten Zementpartikeln bilden sich unlösliche, nadelförmige Kristalle, die Kapillarporen und Mikrorisse im Beton ausfüllen und den Weg für Wasser und wassergebundene Verunreinigungen versperren. Beton mit kristallinem Zusatzmittel ist selbstabdichtend, da die ständige Einwirkung von Wasser die Kristallisation kontinuierlich auslöst, um einen dauerhaften Wasserschutz zu gewährleisten.
- Pigmente können verwendet werden, um die Farbe des Betons aus ästhetischen Gründen zu verändern.
- Weichmacher erhöhen die Verarbeitbarkeit von plastischem oder "frischem" Beton, so dass er leichter und mit geringerem Verdichtungsaufwand eingebracht werden kann. Ein typischer Weichmacher ist Lignosulfonat. Weichmacher können zur Verringerung des Wassergehalts eines Betons unter Beibehaltung der Verarbeitbarkeit eingesetzt werden und werden deshalb manchmal auch als Wasserreduzierer bezeichnet. Eine solche Behandlung verbessert die Festigkeits- und Dauerhaftigkeitseigenschaften des Betons.
- Superverflüssiger (auch als Hochleistungs-Wasserreduzierer bezeichnet) sind eine Klasse von Verflüssigern, die weniger schädliche Auswirkungen haben und die Verarbeitbarkeit stärker verbessern, als dies mit herkömmlichen Verflüssigern möglich ist. Fließmittel werden eingesetzt, um die Druckfestigkeit zu erhöhen. Sie erhöhen die Verarbeitbarkeit des Betons und senken den Bedarf an Wasser um 15-30%. Fließmittel führen zu verzögernden Effekten.
- Pumphilfen verbessern die Pumpfähigkeit, verdicken den Zementleim und verringern die Entmischung und das Ausbluten.
- Verzögerer verlangsamen die Hydratation des Betons und werden bei großen oder schwierigen Güssen verwendet, bei denen ein teilweises Abbinden vor Abschluss des Gusses unerwünscht ist. Typische Polyolverzögerer sind Zucker, Saccharose, Natriumgluconat, Glukose, Zitronensäure und Weinsäure. ⓘ
Mineralische Zusatzmittel und Zementmischungen
Eigenschaft | Portland zement |
Kieselsäure Flugasche |
Kalkhaltige Flugasche |
Schlacke zement |
Kieselsäure rauch | |
---|---|---|---|---|---|---|
SiO2 | 21.9 | 52 | 35 | 35 | 85–97 | |
Al2O3 | 6.9 | 23 | 18 | 12 | — | |
Fe2O3 | 3 | 11 | 6 | 1 | — | |
CaO | 63 | 5 | 21 | 40 | < 1 | |
MgO | 2.5 | — | — | — | — | |
SO3 | 1.7 | — | — | — | — | |
Spezifische Oberfläche (m2/kg) | 370 | 420 | 420 | 400 | 15,000 – 30,000 | |
Spezifisches Gewicht | 3.15 | 2.38 | 2.65 | 2.94 | 2.22 | |
Allgemeiner Zweck | Primäres Bindemittel | Zementersatz | Zementersatz | Zementersatz | Eigenschaftsverbesserer | |
Anorganische Materialien, die puzzolanische oder latent hydraulische Eigenschaften haben. Diese sehr feinkörnigen Materialien werden der Betonmischung zugesetzt, um die Eigenschaften des Betons zu verbessern (mineralische Zusatzmittel) oder als Ersatz für Portlandzement (Mischzemente). Produkte, die Kalkstein, Flugasche, Hochofenschlacke und andere nützliche Materialien mit puzzolanischen Eigenschaften in die Mischung einbeziehen, werden getestet und verwendet. Diese Entwicklungen werden immer wichtiger, um die Auswirkungen der Zementverwendung zu minimieren, die bekanntermaßen einer der größten Verursacher (mit etwa 5 bis 10 %) der weltweiten Treibhausgasemissionen ist. Die Verwendung alternativer Materialien kann auch die Kosten senken, die Betoneigenschaften verbessern und Abfälle recyceln. Letzteres ist für die Aspekte der Kreislaufwirtschaft in der Bauindustrie von Bedeutung, deren Nachfrage mit immer größeren Auswirkungen auf die Rohstoffgewinnung, das Abfallaufkommen und die Deponierung steigt.
- Flugasche: Sie ist ein Nebenprodukt von Kohlekraftwerken und wird verwendet, um Portlandzement teilweise zu ersetzen (um bis zu 60 % der Masse). Die Eigenschaften von Flugasche hängen von der Art der verbrannten Kohle ab. Im Allgemeinen ist kieselhaltige Flugasche puzzolanisch, während kalkhaltige Flugasche latent hydraulische Eigenschaften aufweist.
- Gemahlene granulierte Hochofenschlacke (GGBFS oder GGBS): Dieses Nebenprodukt der Stahlproduktion wird verwendet, um Portlandzement teilweise zu ersetzen (bis zu 80 % der Masse). Es hat latent hydraulische Eigenschaften.
- Silikastaub: Ein Nebenprodukt bei der Herstellung von Silizium- und Ferrosiliziumlegierungen. Silicastaub ist ähnlich wie Flugasche, hat aber eine 100-mal kleinere Partikelgröße. Dies führt zu einem höheren Oberflächen-Volumen-Verhältnis und einer viel schnelleren puzzolanischen Reaktion. Silikastaub wird verwendet, um die Festigkeit und Dauerhaftigkeit von Beton zu erhöhen, erfordert jedoch in der Regel die Verwendung von Fließmitteln für die Verarbeitbarkeit.
- Hochreaktives Metakaolin (HRM): Metakaolin ergibt einen Beton mit ähnlicher Festigkeit und Dauerhaftigkeit wie ein mit Silikastaub hergestellter Beton. Während Silikastaub in der Regel eine dunkelgraue oder schwarze Farbe hat, ist hochreaktives Metakaolin in der Regel strahlend weiß, was es zur bevorzugten Wahl für Architekturbeton macht, bei dem das Aussehen wichtig ist.
- Kohlenstoff-Nanofasern können dem Beton zugesetzt werden, um die Druckfestigkeit zu erhöhen und einen höheren Elastizitätsmodul zu erzielen sowie die elektrischen Eigenschaften zu verbessern, die für die Überwachung von Dehnungen, die Bewertung von Schäden und die Selbstüberwachung des Betons erforderlich sind. Kohlenstofffasern haben viele Vorteile in Bezug auf mechanische und elektrische Eigenschaften (z. B. höhere Festigkeit) und Selbstüberwachungsverhalten aufgrund der hohen Zugfestigkeit und hohen Leitfähigkeit.
- Kohlenstoffprodukte wurden eingesetzt, um Beton für Enteisungszwecke elektrisch leitfähig zu machen. ⓘ
Herstellung


Bei der Betonherstellung werden die verschiedenen Bestandteile - Wasser, Zuschlagstoffe, Zement und eventuelle Zusatzstoffe - zu Beton vermischt. Die Betonherstellung ist zeitkritisch. Sobald die Zutaten gemischt sind, müssen die Arbeiter den Beton an Ort und Stelle bringen, bevor er aushärtet. In der heutigen Zeit findet die Betonherstellung meist in einer großen Industrieanlage statt, die als Betonwerk oder oft auch als Chargenanlage bezeichnet wird. ⓘ
Im Allgemeinen gibt es zwei Haupttypen von Betonwerken: Transportbetonwerke und Zentralmischanlagen. In einem Transportbetonwerk werden alle Zutaten außer Wasser gemischt, während in einem Zentralmischwerk alle Zutaten einschließlich Wasser gemischt werden. Eine Zentralmischanlage bietet eine genauere Kontrolle der Betonqualität durch bessere Messungen der zugegebenen Wassermenge, muss aber näher an der Baustelle stehen, an der der Beton verwendet wird, da die Hydratation erst in der Anlage beginnt. ⓘ
Ein Betonwerk besteht aus großen Vorratsbehältern für verschiedene reaktive Bestandteile wie Zement, aus einem Lager für Schüttgut wie Zuschlagstoffe und Wasser, aus Mechanismen für die Zugabe verschiedener Zusatz- und Ergänzungsstoffe, aus Maschinen zum genauen Abwiegen, Bewegen und Mischen einiger oder aller dieser Bestandteile sowie aus Einrichtungen zur Ausgabe des gemischten Betons, häufig an einen Betonmischer. ⓘ
Moderner Beton wird in der Regel als viskose Flüssigkeit zubereitet, so dass er in Formen gegossen werden kann, die vor Ort aufgestellt werden, um dem Beton die gewünschte Form zu geben. Betonschalungen können auf verschiedene Weise hergestellt werden, z. B. durch Gleitschalung und Stahlplattenbau. Alternativ kann der Beton auch in trockenere, nicht flüssige Formen gemischt und im Werk zur Herstellung von Betonfertigteilen verwendet werden. ⓘ
Für die Verarbeitung von Beton wird eine Vielzahl von Geräten verwendet, von Handwerkzeugen bis hin zu schweren Industriemaschinen. Unabhängig davon, welche Geräte die Bauherren verwenden, besteht das Ziel darin, das gewünschte Baumaterial herzustellen; die Zutaten müssen ordnungsgemäß gemischt, platziert, geformt und innerhalb der vorgegebenen Zeit gehalten werden. Jede Unterbrechung beim Gießen des Betons kann dazu führen, dass das ursprünglich eingebrachte Material zu erstarren beginnt, bevor die nächste Charge hinzugefügt wird. Dadurch entsteht eine horizontale Schwachstelle, die so genannte kalte Fuge zwischen den beiden Chargen. Sobald die Mischung dort ist, wo sie sein soll, muss der Aushärtungsprozess kontrolliert werden, um sicherzustellen, dass der Beton die gewünschten Eigenschaften erreicht. Während der Betonherstellung können verschiedene technische Details die Qualität und Beschaffenheit des Produkts beeinflussen. ⓘ
Bemessungsmischung
Das Mischungsverhältnis wird von einem Ingenieur nach Analyse der Eigenschaften der verwendeten Bestandteile festgelegt. Anstatt eine "Nennmischung" aus 1 Teil Zement, 2 Teilen Sand und 4 Teilen Zuschlag zu verwenden (das zweite Beispiel von oben), entwirft ein Bauingenieur eine Betonmischung nach Maß, um die Anforderungen der Baustelle und der Bedingungen genau zu erfüllen, indem er die Materialverhältnisse festlegt und oft ein Zusatzmittelpaket zur Feinabstimmung der Eigenschaften oder zur Erhöhung der Leistungsfähigkeit der Mischung entwirft. Design-Mix-Beton kann sehr weitreichende Spezifikationen haben, die mit einfacheren Nennmischungen nicht erfüllt werden können, aber die Beteiligung des Ingenieurs erhöht oft die Kosten der Betonmischung. ⓘ
Betonmischungen werden in erster Linie in Nominalmischungen, Standardmischungen und Designmischungen unterteilt. ⓘ
Die Nennmischungsverhältnisse werden in Volumeneinheiten von . Nennmischungen sind ein einfaches und schnelles Mittel, um eine grundlegende Vorstellung von den Eigenschaften des fertigen Betons zu erhalten, ohne dass im Voraus Prüfungen durchgeführt werden müssen. ⓘ
Verschiedene Gremien (z. B. British Standards) definieren Nennmischungsverhältnisse in einer Reihe von Klassen, die in der Regel von niedriger Druckfestigkeit bis zu hoher Druckfestigkeit reichen. Die Klassen geben in der Regel die 28-Tage-Würfel-Festigkeit an. ⓘ
Mischen
Gründliches Mischen ist für die Herstellung von gleichmäßigem, hochwertigem Beton unerlässlich. ⓘ
Getrenntes Mischen von Pasten hat gezeigt, dass das Mischen von Zement und Wasser zu einem Zementleim, bevor diese Materialien mit den Zuschlagstoffen kombiniert werden, die Druckfestigkeit des resultierenden Betons erhöhen kann. Der Zementleim wird im Allgemeinen in einem HochgeschwindigkeitsmischerSchermischern mit einem w/cm (Wasser-Zement-Verhältnis) von 0,30 bis 0,45 nach Masse gemischt. Die Zementsteinvormischung kann Zusatzstoffe wie Beschleuniger oder Verzögerer, Fließmittel, Pigmente oder Silikastaub enthalten. Der vorgemischte Zementleim wird dann mit den Zuschlagstoffen und dem verbleibenden Wasser gemischt, und das endgültige Mischen erfolgt in herkömmlichen Betonmischanlagen. ⓘ
Probenanalyse - Verarbeitbarkeit


Die Verarbeitbarkeit ist die Fähigkeit einer frischen (plastischen) Betonmischung, die Form mit der gewünschten Arbeit (Gießen, Pumpen, Verteilen, Stampfen, Rütteln) ordnungsgemäß zu füllen, ohne die Qualität des Betons zu beeinträchtigen. Die Verarbeitbarkeit hängt vom Wassergehalt, der Gesteinskörnung (Form und Größenverteilung), dem Zementgehalt und dem Alter (Hydratationsgrad) ab und kann durch Zugabe von chemischen Zusatzmitteln wie Fließmittel verändert werden. Eine Erhöhung des Wassergehalts oder die Zugabe chemischer Zusatzmittel erhöht die Verarbeitbarkeit des Betons. Zu viel Wasser führt zu verstärktem Ausbluten oder Entmischung der Zuschläge (wenn Zement und Zuschläge beginnen, sich zu trennen), wodurch der Beton eine geringere Qualität aufweist. Auch Änderungen der Kornabstufung können die Verarbeitbarkeit des Betons beeinträchtigen, obwohl eine breite Palette von Kornabstufungen für verschiedene Anwendungen verwendet werden kann. Eine unerwünschte Kornabstufung kann bedeuten, dass eine große Gesteinskörnung verwendet wird, die für die Größe der Schalung zu groß ist, oder dass zu wenig kleinere Gesteinskörnungen verwendet werden, um die Lücken zwischen den größeren Kornabstufungen auszufüllen, oder dass aus demselben Grund zu wenig oder zu viel Sand verwendet wird, oder dass zu wenig Wasser oder zu viel Zement verwendet wird, oder dass sogar zerklüfteter Schotter anstelle von glatteren runden Gesteinskörnungen wie Kieselsteinen verwendet wird. Jede Kombination dieser und anderer Faktoren kann dazu führen, dass die Mischung zu hart ist, d. h., dass sie nicht gleichmäßig fließt oder sich nicht gleichmäßig verteilt, dass sie schwer in die Schalung zu bekommen ist und dass sich die Oberfläche schwer bearbeiten lässt. ⓘ
Die Verarbeitbarkeit kann mit dem Beton-Setztest gemessen werden, einem einfachen Maß für die Plastizität einer frischen Betonmischung nach den Prüfnormen ASTM C 143 oder EN 12350-2. Das Setzverhalten wird normalerweise gemessen, indem ein Abrams-Kegel" mit einer Probe aus einer frischen Betoncharge gefüllt wird. Der Kegel wird mit dem breiten Ende nach unten auf eine ebene, nicht saugende Fläche gestellt. Er wird dann in drei Schichten gleichen Volumens gefüllt, wobei jede Schicht mit einem Stahlstab festgestampft wird, um die Schicht zu verdichten. Beim vorsichtigen Abheben des Kegels sackt das eingeschlossene Material aufgrund der Schwerkraft in gewissem Umfang ab. Eine relativ trockene Probe sackt nur sehr wenig ab und hat einen Setzwert von einem oder zwei Zoll (25 oder 50 mm) auf einem Fuß (300 mm). Eine relativ feuchte Betonprobe kann bis zu acht Zoll absacken. Die Verarbeitbarkeit kann auch mit dem Fließtischtest gemessen werden. ⓘ
Das Setzverhalten kann durch Zugabe chemischer Zusatzmittel wie Fließmittel oder Superverflüssiger erhöht werden, ohne dass der Wasser-Zement-Wert verändert wird. Einige andere Zusatzmittel, insbesondere luftporenbildende Zusatzmittel, können das Setzmaß einer Mischung erhöhen. ⓘ
Fließfähiger Beton wird wie selbstverfestigender Beton mit anderen Fließmessmethoden geprüft. Eine dieser Methoden besteht darin, den Kegel auf das schmale Ende zu stellen und zu beobachten, wie das Gemisch durch den Kegel fließt, während er langsam angehoben wird. ⓘ
Nach dem Mischen ist der Beton flüssig und kann an den Ort gepumpt werden, an dem er benötigt wird. ⓘ
Aushärten
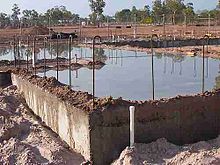
Beton muss während der Aushärtung feucht gehalten werden, um eine optimale Festigkeit und Haltbarkeit zu erreichen. Während der Aushärtung findet eine Hydratation statt, bei der sich Kalzium-Silikat-Hydrat (C-S-H) bildet. Mehr als 90 % der endgültigen Festigkeit einer Mischung werden in der Regel innerhalb von vier Wochen erreicht, die restlichen 10 % werden über Jahre oder sogar Jahrzehnte hinweg erreicht. Die Umwandlung von Kalziumhydroxid im Beton in Kalziumkarbonat durch die Aufnahme von CO2 über mehrere Jahrzehnte stärkt den Beton weiter und macht ihn widerstandsfähiger gegen Schäden. Diese Karbonatisierungsreaktion senkt jedoch den pH-Wert der Zementporenlösung und kann die Bewehrungsstäbe korrodieren. ⓘ
Die Hydratation und Aushärtung des Betons während der ersten drei Tage ist entscheidend. Ungewöhnlich schnelles Trocknen und Schwinden aufgrund von Faktoren wie Verdunstung durch Wind während des Einbaus kann zu erhöhten Zugspannungen zu einem Zeitpunkt führen, an dem der Beton noch nicht genügend Festigkeit erlangt hat, was zu größeren Schwindrissen führt. Die Frühfestigkeit des Betons kann erhöht werden, wenn er während des Nachbehandlungsprozesses feucht gehalten wird. Die Minimierung der Spannung vor dem Aushärten minimiert die Rissbildung. Beton mit hoher Frühfestigkeit ist so konzipiert, dass er schneller hydratisiert, oft durch erhöhten Zementeinsatz, der das Schwinden und die Rissbildung erhöht. Die Festigkeit des Betons ändert sich (erhöht sich) bis zu drei Jahre lang. Sie hängt von den Querschnittsabmessungen der Elemente und den Bedingungen für die Nutzung des Bauwerks ab. Die Zugabe von kurzgeschnittenen Polymerfasern kann die schwindungsbedingten Spannungen während der Aushärtung verbessern (reduzieren) und die Früh- und Enddruckfestigkeit erhöhen. ⓘ
Eine ordnungsgemäße Nachbehandlung des Betons führt zu einer höheren Festigkeit und geringeren Durchlässigkeit und vermeidet Risse, wenn die Oberfläche vorzeitig austrocknet. Es muss auch darauf geachtet werden, dass es aufgrund des exothermen Abbindens des Zements nicht zu Gefrier- oder Überhitzungserscheinungen kommt. Eine unsachgemäße Aushärtung kann zu Ablagerungen, verminderter Festigkeit, schlechter Abriebfestigkeit und Rissbildung führen. ⓘ
Der Schutz der Betonoberfläche gegen frühzeitiger Austrocknung ist zur Erzielung einer rißfreien, dichten und dauerhaften Betonoberfläche erforderlich. Die Hydratation des Zements findet nur in feuchtem Milieu statt. ⓘ
Sonneneinstrahlung und Wind bewirken ein schnelles Austrocknen der Oberfläche. Zur Vermeidung von Schwindrissen ist der Beton im Sommer über mehrere Tage feuchtzuhalten, indem er geflutet oder regelmäßig mit Wasser besprüht wird. Alternativ kann die Verdunstung auch durch das Belassen der Betonschalung, durch das Abdecken der Oberfläche oder durch den Auftrag von filmbildenden Beschichtungen (Curingmittel) eingeschränkt werden. Im Winter ist die Oberfläche zusätzlich vor Frost zu schützen. ⓘ
Die notwendige Zeitdauer der Nachbehandlung kann je nach Betoneigenschaften und Umweltbedingungen zwischen einem Tag und mehreren Wochen betragen. Grundsätzlich sollte so früh wie möglich mit der Nachbehandlung begonnen und diese möglichst lange beibehalten werden. Über die Messung des Kapillardrucks des Betons lassen sich Rückschlüsse auf die zur Aushärtung benötigte Wassermenge ziehen. Eine solche Messung findet jedoch eher in Prüflaboren Anwendung. ⓘ
Techniken
Während der Aushärtungszeit wird der Beton idealerweise bei kontrollierter Temperatur und Luftfeuchtigkeit gelagert. Um eine vollständige Hydratation während der Aushärtung zu gewährleisten, werden Betonplatten häufig mit "Nachbehandlungsmitteln" besprüht, die einen wasserhaltenden Film über dem Beton bilden. Typische Filme werden aus Wachs oder ähnlichen hydrophoben Verbindungen hergestellt. Nachdem der Beton ausreichend ausgehärtet ist, kann der Film durch normale Nutzung vom Beton abgetragen werden. ⓘ
Traditionell wird die Betonoberfläche zum Aushärten mit Wasser besprüht oder mit Wasser übergossen. Das nebenstehende Bild zeigt eine von vielen Möglichkeiten, dies zu erreichen, nämlich das Eintauchen des ausgehärteten Betons in Wasser und das Einwickeln in Plastik, um ein Austrocknen zu verhindern. Weitere gängige Nachbehandlungsmethoden sind das Abdecken des frischen Betons mit nassem Sackleinen und Plastikfolien. ⓘ
Für Anwendungen mit höherer Festigkeit kann der Beton beschleunigt ausgehärtet werden. Eine gängige Technik besteht darin, den gegossenen Beton mit Dampf zu erhitzen, um ihn feucht zu halten und die Temperatur zu erhöhen, damit der Hydratationsprozess schneller und gründlicher abläuft. ⓘ
Alternative Arten
Asphalt
Asphaltbeton (in Nordamerika als Asphalt, Blacktop oder Pavement, im Vereinigten Königreich und in der Republik Irland als Tarmac, Bitumenmakadam oder Walzasphalt bezeichnet) ist ein Verbundwerkstoff, der häufig für den Belag von Straßen, Parkplätzen und Flughäfen sowie für den Kern von Staudämmen verwendet wird. Asphaltmischungen werden seit Anfang des zwanzigsten Jahrhunderts im Straßenbau verwendet. Es besteht aus mineralischen Zuschlagstoffen, die mit Asphalt gebunden, in Schichten eingebaut und verdichtet werden. Das Verfahren wurde von dem belgischen Erfinder und US-Einwanderer Edward De Smedt verfeinert und verbessert. ⓘ
Die Begriffe Asphalt (oder Asphaltbeton), bituminöser Asphaltbeton und bituminöses Gemisch werden in der Regel nur in technischen und bautechnischen Unterlagen verwendet, in denen Beton als ein Verbundmaterial definiert wird, das aus mineralischen Zuschlagstoffen besteht, die mit einem Bindemittel verklebt sind. Die Abkürzung AC wird manchmal für Asphaltbeton verwendet, kann aber auch den Asphaltanteil oder Asphaltzement bezeichnen und bezieht sich auf den flüssigen Asphaltanteil des Verbundmaterials. ⓘ
Asphaltbeton ist eine Bezeichnung für ein Gemisch aus Bitumen und Gesteinskörnung. Der Namensteil „-beton“ verweist hier auf das „Betonprinzip“ der Mischung, d. h., wie beim Baustoff Beton sind im Asphaltbeton verschiedene Gesteinskörnungsgrößen gleichmäßig verteilt und vollständig von Bindemittel ummantelt. ⓘ
Concretene
Concretene ist dem Beton sehr ähnlich, mit der Ausnahme, dass während des Zementmischprozesses eine kleine Menge Graphen (< 0,5 Gew.-%) hinzugefügt wird. ⓘ
Mit Graphen verstärkte(r) Beton
Bei Graphenbeton handelt es sich um eine Standardausführung von Betonmischungen mit dem Unterschied, dass beim Mischen des Zements oder bei der Herstellung eine geringe Menge Graphen (in der Regel < 0,5 Gewichtsprozent) zugesetzt wird. Diese verbesserten Graphenbetone sind auf die jeweilige Betonanwendung abgestimmt. ⓘ
Mikrobielle
Bakterien wie Bacillus pasteurii, Bacillus pseudofirmus, Bacillus cohnii, Sporosarcina pasteuri und Arthrobacter crystallopoietes erhöhen durch ihre Biomasse die Druckfestigkeit von Beton. Einige Formen von Bakterien können jedoch auch betonzerstörend wirken. Bacillus sp. CT-5. kann die Korrosion der Bewehrung in Stahlbeton um das bis zu Vierfache reduzieren. Sporosarcina pasteurii verringert die Wasser- und Chloriddurchlässigkeit. B. pasteurii erhöht die Beständigkeit gegen Säure. Bacillus pasteurii und B. sphaericus können die Ausfällung von Kalziumkarbonat in der Oberfläche von Rissen bewirken und so die Druckfestigkeit erhöhen. ⓘ
Nanobeton

Nanobeton (auch "Nanobeton" oder "Nanobeton") ist eine Materialklasse, die Portlandzementpartikel mit einer Größe von höchstens 100 μm und Siliziumdioxidpartikel mit einer Größe von höchstens 500 μm enthält, die Hohlräume ausfüllen, die sonst in normalem Beton auftreten würden, und so die Festigkeit des Materials erheblich erhöhen. Er wird häufig bei Fußgänger- und Autobahnbrücken verwendet, wo eine hohe Biege- und Druckfestigkeit erforderlich ist. ⓘ
Durchlässig
Durchlässiger Beton ist eine Mischung aus speziell abgestuften groben Zuschlagstoffen, Zement, Wasser und wenig bis gar keinen feinen Zuschlagstoffen. Dieser Beton wird auch als "no-fines" oder Porenbeton bezeichnet. Durch das Mischen der Zutaten in einem sorgfältig kontrollierten Prozess entsteht eine Paste, die die Gesteinskörner umhüllt und verbindet. Der ausgehärtete Beton enthält zusammenhängende Luftporen von insgesamt etwa 15 bis 25 Prozent. Das Wasser fließt durch die Hohlräume im Belag in den darunter liegenden Boden. Luftporenbildner werden häufig in Frost-Tau-Klimazonen eingesetzt, um die Gefahr von Frostschäden zu minimieren. Durchlässiger Beton ermöglicht es auch, dass Regenwasser durch Straßen und Parkplätze sickert und die Grundwasserleiter auffüllt, anstatt zu Abflüssen und Überschwemmungen beizutragen. ⓘ
Polymer
Polymerbeton ist ein Gemisch aus Zuschlagstoffen und verschiedenen Polymeren und kann verstärkt werden. Der Zement ist teurer als Zemente auf Kalkbasis, aber Polymerbetone haben dennoch Vorteile: Sie haben auch ohne Bewehrung eine hohe Zugfestigkeit und sind weitgehend wasserundurchlässig. Polymerbetone werden häufig für die Reparatur und den Bau von anderen Anwendungen, wie z. B. Abwasserkanälen, verwendet. ⓘ
Vulkanisch
Vulkanischer Beton ersetzt den Kalkstein, der zu Klinker gebrannt wird, durch vulkanisches Gestein. Er verbraucht eine ähnliche Menge an Energie, setzt aber nicht direkt Kohlenstoff als Nebenprodukt frei. Vulkangestein/Asche wird als zusätzliches Zementmaterial in Beton verwendet, um die Widerstandsfähigkeit gegen Sulfat-, Chlorid- und Alkali-Kieselsäure-Reaktionen durch Porenverfeinerung zu verbessern. Außerdem sind sie im Allgemeinen im Vergleich zu anderen Zuschlagstoffen kostengünstig, eignen sich gut für Halb- und Leichtbeton und sind gut für die Wärme- und Schalldämmung. ⓘ
Pyroklastische Materialien wie Bimsstein, Schlacke und Asche entstehen aus abkühlendem Magma bei explosiven Vulkanausbrüchen. Sie werden als ergänzende zementhaltige Materialien (SCM) oder als Zuschlagstoffe für Zement und Beton verwendet. Sie werden seit der Antike in großem Umfang zur Herstellung von Baumaterialien verwendet. Beispielsweise wurden Bimsstein und andere vulkanische Gläser beim Bau der Villa San Marco in der römischen Epoche (89 v. Chr. - 79 n. Chr.) als natürliches Puzzolanmaterial für Mörtel und Putze verwendet, die zu den am besten erhaltenen otium villae des Golfs von Neapel in Italien gehören. ⓘ
Lichtabfall
Waste light ist eine Form von polymermodifiziertem Beton. Die spezielle Polymerbeimischung ermöglicht es, alle herkömmlichen Zuschlagstoffe (Kies, Sand, Stein) durch eine beliebige Mischung fester Abfallstoffe mit einer Korngröße von 3-10 mm zu ersetzen, um ein Produkt mit niedriger Druckfestigkeit (3-20 N/mm2) für den Straßen- und Hochbau zu erhalten. Ein Kubikmeter Abfall-Leichtbeton enthält 1,1-1,3 m3 geschredderten Abfall und keine anderen Zuschlagstoffe. ⓘ
Schwefelbeton
Schwefelbeton ist eine Mischung aus Quarzsand, Kalkstein oder Schottersteinen, der als Bindemittel 15–20 % Schwefel beigemischt wird. Der Schwefel wird vorher mit dimeren Cyclopentadien modifiziert und als plastischer Schwefel stabilisiert. Der Schwefelbeton verfügt gegenüber Beton über eine höhere Druck- und Zugfestigkeit sowie Frühfestigkeit, ist wesentlich korrosionsbeständiger gegenüber Säuren und Salzlösungen und hat eine um 40 % bessere CO₂-Bilanz. Nachteilig sind das Erweichen bei Temperaturen über 120 °C und die Brennbarkeit. Die Einsatzmöglichkeit von Schwefelbeton ist dort von Bedeutung, wo er im Freien herkömmlichen Beton ersetzen kann, z. B. Eisenbahnschwellen, oder Lagerung bzw. Umfüllung von aggressiven Chemikalien oder grundwasserschädlichen Stoffen. Die Verwendung ist in Deutschland bisher eingeschränkt. ⓘ
Eigenschaften
Beton hat eine relativ hohe Druckfestigkeit, aber eine viel geringere Zugfestigkeit. Daher wird er in der Regel mit zugfesten Materialien (häufig Stahl) verstärkt. Die Elastizität von Beton ist bei niedrigen Spannungen relativ konstant, nimmt aber bei höheren Spannungen ab, wenn sich Risse in der Matrix bilden. Beton hat einen sehr niedrigen thermischen Ausdehnungskoeffizienten und schrumpft, wenn er reift. Alle Betonkonstruktionen bekommen in gewissem Maße Risse, die auf Schwinden und Spannungen zurückzuführen sind. Beton, der lang anhaltenden Kräften ausgesetzt ist, ist anfällig für Kriechbewegungen. ⓘ
Es können Prüfungen durchgeführt werden, um sicherzustellen, dass die Betoneigenschaften den Spezifikationen für die Anwendung entsprechen. ⓘ

Die Inhaltsstoffe beeinflussen die Festigkeit des Materials. Die Festigkeitswerte von Beton werden in der Regel als untere Grenze der Druckfestigkeit eines zylindrischen oder kubischen Probekörpers angegeben, die durch Standardprüfverfahren ermittelt wird. ⓘ
Die Festigkeit des Betons richtet sich nach seiner Funktion. Beton mit einer sehr geringen Festigkeit von 14 MPa (2.000 psi) oder weniger kann verwendet werden, wenn der Beton leicht sein muss. Leichtbeton wird häufig durch die Zugabe von Luft, Schaumstoffen oder Leichtzuschlägen erreicht, mit dem Nebeneffekt, dass die Festigkeit reduziert wird. Für die meisten Routineanwendungen wird häufig Beton mit 20 bis 32 MPa (2.900 bis 4.600 psi) verwendet. Beton mit 40 MPa (5.800 psi) ist im Handel als haltbarere, wenn auch teurere Option erhältlich. Höherfester Beton wird häufig für größere Bauvorhaben verwendet. Festigkeiten über 40 MPa (5.800 psi) werden häufig für bestimmte Bauelemente verwendet. Für die unteren Geschossstützen von Hochhäusern kann beispielsweise Beton mit einer Festigkeit von 80 MPa (11.600 psi) oder mehr verwendet werden, um die Größe der Stützen gering zu halten. Bei Brücken können lange Balken aus hochfestem Beton verwendet werden, um die Anzahl der erforderlichen Spannweiten zu verringern. Gelegentlich können andere strukturelle Anforderungen hochfesten Beton erfordern. Wenn ein Bauwerk sehr steif sein muss, kann Beton mit einer sehr hohen Festigkeit spezifiziert werden, der sogar viel stärker ist, als es für die Betriebslasten erforderlich ist. Aus diesen Gründen wurden im Handel Festigkeiten von bis zu 130 MPa (18.900 psi) verwendet. ⓘ
Typische Einsatzgebiete von Stahlbeton:
- Gründungen, (Keller)Wände, Decken, Stützen und Ringanker im allgemeinen Hochbau,
- Skelettbau-Tragkonstruktionen von Hochhäusern und Gewerbebauten,
- Verkehrsbauten wie Tunnel, Brücken und Stützwände. ⓘ
Unbewehrter Beton wird für Schwergewichtswände, gebogene Gewichtsstaumauern und andere kompakte, massive Bauteile verwendet, die überwiegend auf Druck belastet werden. Größere Zugspannungen müssen entweder konstruktiv vermieden werden oder es darf von einem Bruch des Materials keine Gefährdung ausgehen. Dies ist beispielsweise bei kleineren vorgefertigte Elementen wie Blocksteinen für den Mauerwerksbau oder (Waschbeton-)Platten im Gartenbau der Fall. Auf Grund geringer Kosten, beliebiger Formbarkeit und vergleichsweise hoher Dichte von etwa 2400 kg/m³ wird Beton auch für Gegengewichte an Kränen und für Wellenbrecher verwendet. ⓘ
Zu beachten ist das Schwinden des Bauteil-Volumens bei Austrocknung sowie durch chemische Vorgänge. Das Schwindmaß ist dabei abhängig von der Zusammensetzung des Ausgangsmaterials. Ein gewisses Kriechen tritt bei allen belasteten Bauteilen auf und bezeichnet die mit der Zeit zunehmende Verformung unter Belastung. ⓘ
Energieeinsparung
Der Energiebedarf für den Transport von Beton ist gering, da er vor Ort aus lokalen Ressourcen hergestellt wird, in der Regel in einem Umkreis von 100 km um die Baustelle. Ebenso wird bei der Herstellung und Kombination der Rohstoffe relativ wenig Energie verbraucht (obwohl bei den chemischen Reaktionen bei der Zementherstellung große Mengen an CO2 entstehen). Die Gesamtenergie von Beton ist daher mit etwa 1 bis 1,5 Megajoule pro Kilogramm niedriger als bei den meisten anderen Konstruktions- und Baumaterialien. ⓘ
Einmal eingebaut, bietet Beton während der gesamten Lebensdauer eines Gebäudes eine hohe Energieeffizienz. Betonwände lassen viel weniger Luft entweichen als solche aus Holz. Luftleckagen machen einen großen Teil des Energieverlustes eines Hauses aus. Die thermischen Masseeigenschaften von Beton erhöhen die Effizienz von Wohn- und Geschäftsgebäuden. Die thermische Masse des Betons speichert die zum Heizen oder Kühlen benötigte Energie und gibt sie wieder ab, was das ganze Jahr über Vorteile bringt, da die Temperaturschwankungen im Inneren reduziert und die Heiz- und Kühlkosten minimiert werden. Während die Isolierung den Energieverlust durch die Gebäudehülle verringert, nutzt die thermische Masse die Wände, um Energie zu speichern und abzugeben. Moderne Betonwandsysteme nutzen sowohl die Außendämmung als auch die thermische Masse, um ein energieeffizientes Gebäude zu schaffen. Isolierende Betonschalungen (ICF) sind Hohlblöcke oder Platten aus Isolierschaum oder Raster, die gestapelt werden, um die Form der Wände eines Gebäudes zu bilden, und dann mit Stahlbeton gefüllt werden, um die Struktur zu schaffen. ⓘ
Brandsicherheit
Gebäude aus Beton sind widerstandsfähiger gegen Feuer als Gebäude mit Stahlrahmen, da Beton eine geringere Wärmeleitfähigkeit als Stahl hat und daher unter den gleichen Brandbedingungen länger hält. Beton wird manchmal als Feuerschutz für Stahlrahmen verwendet, mit dem gleichen Effekt wie oben beschrieben. Beton als Feuerschutz, z. B. Fondu fyre, kann auch in extremen Umgebungen wie einer Raketenabschussrampe verwendet werden. ⓘ
Zu den Optionen für nicht brennbare Konstruktionen gehören Böden, Decken und Dächer aus Ortbeton und Hohlkernbetonfertigteilen. Für Wände sind Betonmauerwerk und Isolierbetonformen (ICF) eine weitere Option. ICFs sind Hohlblöcke oder Platten aus feuerfestem Isolierschaum, die zu den Wänden eines Gebäudes gestapelt und dann mit Stahlbeton gefüllt werden, um die Struktur zu bilden. ⓘ
Beton bietet aufgrund seiner seitlichen Steifigkeit, die zu minimalen horizontalen Bewegungen führt, auch guten Widerstand gegen von außen einwirkende Kräfte wie starke Winde, Wirbelstürme und Tornados. Diese Steifigkeit kann sich jedoch bei bestimmten Arten von Betonkonstruktionen negativ auswirken, insbesondere dann, wenn eine relativ hohe Durchbiegung erforderlich ist, um extremeren Kräften zu widerstehen. ⓘ
Erdbebensicherheit
Wie bereits erwähnt, ist Beton in Druckrichtung sehr stark, in Zugrichtung jedoch schwach. Größere Erdbeben können sehr große Scherkräfte auf Bauwerke ausüben. Durch diese Scherkräfte wird das Bauwerk sowohl auf Zug als auch auf Druck beansprucht. Betonbauten ohne Bewehrung können ebenso wie andere unbewehrte Mauerwerksbauten bei schweren Erdbeben versagen. Unbewehrte Mauerwerksbauten stellen weltweit eines der größten Erdbebenrisiken dar. Diese Risiken können durch die seismische Nachrüstung gefährdeter Gebäude (z. B. Schulgebäude in Istanbul, Türkei) verringert werden. ⓘ
Bauen mit Beton
Beton ist einer der dauerhaftesten Baustoffe. Im Vergleich zu Holzkonstruktionen bietet er eine bessere Feuerbeständigkeit und gewinnt mit der Zeit an Festigkeit. Bauwerke aus Beton können eine lange Lebensdauer haben. Beton wird mehr als jeder andere künstliche Baustoff auf der Welt verwendet. Im Jahr 2006 wurden etwa 7,5 Milliarden Kubikmeter Beton pro Jahr hergestellt, also mehr als ein Kubikmeter für jeden Menschen auf der Erde. ⓘ
Bewehrter Beton
Die Verwendung von Bewehrung in Form von Eisen wurde in den 1850er Jahren von dem französischen Industriellen François Coignet eingeführt, und erst in den 1880er Jahren verwendete der deutsche Bauingenieur G. A. Wayss Stahl als Bewehrung. Beton ist ein relativ sprödes Material, das unter Druck, aber weniger unter Zug belastbar ist. Einfacher, unbewehrter Beton ist für viele Bauwerke ungeeignet, da er Beanspruchungen durch Schwingungen, Windlasten usw. relativ schlecht standhält. Um die Gesamtfestigkeit zu erhöhen, können daher Stahlstangen, -drähte, -gitter oder -kabel in den Beton eingebettet werden, bevor er ausgehärtet ist. Diese Bewehrung, oft auch als Bewehrungsstab bezeichnet, widersteht Zugkräften. ⓘ
Stahlbeton (RC) ist ein vielseitiger Verbundwerkstoff und eines der am häufigsten verwendeten Materialien im modernen Bauwesen. Er setzt sich aus verschiedenen Bestandteilen mit sehr unterschiedlichen Eigenschaften zusammen, die sich gegenseitig ergänzen. Im Falle von Stahlbeton sind die Bestandteile fast immer Beton und Stahl. Diese beiden Materialien gehen eine starke Verbindung ein und sind in der Lage, einer Vielzahl von einwirkenden Kräften zu widerstehen, so dass sie effektiv wie ein einziges Strukturelement wirken. ⓘ
Stahlbeton kann als Fertigteil oder als Ortbeton hergestellt werden und wird in einer Vielzahl von Anwendungen eingesetzt, z. B. im Platten-, Wand-, Balken-, Stützen-, Fundament- und Rahmenbau. Die Bewehrung wird in der Regel in den Bereichen des Betons angebracht, die wahrscheinlich auf Zug beansprucht werden, wie z. B. im unteren Teil von Trägern. In der Regel beträgt die Überdeckung sowohl über als auch unter der Stahlbewehrung mindestens 50 mm, um Abplatzungen und Korrosion zu verhindern, die zu struktureller Instabilität führen können. Andere Arten der Bewehrung, die nicht aus Stahl bestehen, wie z. B. faserverstärkte Betone, werden für spezielle Anwendungen verwendet, vor allem als Mittel zur Kontrolle der Rissbildung. ⓘ
Vorgefertigter Beton
Betonfertigteile sind Betone, die an einem Ort gegossen werden, um an anderer Stelle verwendet zu werden, und sind ein mobiles Material. Der größte Teil der Fertigteilproduktion erfolgt in den Werken spezialisierter Zulieferer, obwohl in einigen Fällen aufgrund wirtschaftlicher und geografischer Faktoren, des Umfangs des Produkts oder der schwierigen Zugänglichkeit die Elemente auf oder neben der Baustelle gegossen werden. Das Fertigteilverfahren bietet erhebliche Vorteile, da es in einer kontrollierten Umgebung und geschützt vor Witterungseinflüssen durchgeführt wird, doch die Kehrseite der Medaille ist der Beitrag zu den Treibhausgasemissionen durch den Transport zur Baustelle. ⓘ
Vorteile, die durch den Einsatz von Betonfertigteilen erzielt werden können:
- Es gibt bevorzugte Abmessungsschemata mit Elementen aus bewährten Designs, die in einem Katalog erhältlich sind.
- Erhebliche Zeiteinsparungen ergeben sich aus der Herstellung von Bauteilen außerhalb der Reihe von Ereignissen, die die Gesamtdauer des Bauwerks bestimmen und von Planungsingenieuren als "kritischer Pfad" bezeichnet werden.
- Verfügbarkeit von Laboreinrichtungen, die in der Lage sind, die geforderten Kontrollprüfungen durchzuführen, wobei viele von ihnen für spezifische Prüfungen gemäß den nationalen Normen zertifiziert sind.
- Ausrüstungen, die für bestimmte Produktionsarten geeignet sind, wie z. B. Spannbetten mit entsprechender Kapazität, Formen und Maschinen für bestimmte Produkte.
- Hochwertige Oberflächen, die direkt aus der Form kommen, machen eine Innenausstattung überflüssig und sorgen für niedrige Wartungskosten. ⓘ
Massive Strukturen
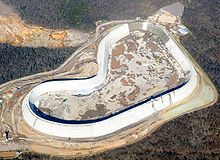
Aufgrund der exothermen chemischen Reaktion von Zement während des Abbindens erzeugen große Betonkonstruktionen wie Dämme, Schleusen, große Mattenfundamente und große Wellenbrecher während der Hydratation und der damit verbundenen Ausdehnung übermäßige Wärme. Um diese Auswirkungen abzumildern, wird während der Bauarbeiten üblicherweise eine Nachkühlung vorgenommen. Ein frühes Beispiel ist der Hoover-Damm, bei dem ein Netz von Rohren zwischen den vertikalen Betonschichten verlegt wurde, um Kühlwasser während des Aushärtungsprozesses zirkulieren zu lassen und so eine schädliche Überhitzung zu vermeiden. Ähnliche Systeme werden auch heute noch verwendet; je nach Volumen des Betons, der verwendeten Betonmischung und der Umgebungstemperatur kann der Kühlprozess viele Monate nach dem Einbringen des Betons andauern. Auch für die Vorkühlung der Betonmischung in Massenbetonbauten werden verschiedene Methoden eingesetzt. ⓘ
Ein weiterer Ansatz für Massenbetonkonstruktionen, bei dem die thermischen Nebenprodukte des Zements minimiert werden, ist die Verwendung von Walzbeton, bei dem eine Trockenmischung verwendet wird, die einen viel geringeren Kühlbedarf hat als der herkömmliche Nasseinbau. Er wird in dicken Schichten als halbtrockenes Material eingebracht und dann mit einer Walze zu einer dichten, festen Masse verdichtet. ⓘ
Oberflächenbeschaffenheit

Rohe Betonoberflächen sind in der Regel porös und haben ein relativ uninteressantes Aussehen. Um das Erscheinungsbild zu verbessern und die Oberfläche vor Fleckenbildung, eindringendem Wasser und Frost zu schützen, können zahlreiche Oberflächenbehandlungen vorgenommen werden. ⓘ
Beispiele für ein verbessertes Aussehen sind Stempelbeton, bei dem dem nassen Beton ein Muster aufgeprägt wird, um einen gepflasterten, kopfsteinpflasterartigen oder ziegelsteinartigen Effekt zu erzielen, und der mit einer Farbgebung versehen werden kann. Ein weiterer beliebter Effekt für Bodenbeläge und Tischplatten ist polierter Beton, bei dem der Beton mit Diamantschleifmitteln optisch glatt poliert und mit Polymeren oder anderen Versiegelungsmitteln versiegelt wird. ⓘ
Andere Oberflächen können durch Meißeln oder konventionellere Techniken wie Streichen oder Abdecken mit anderen Materialien erzielt werden. ⓘ
Die richtige Behandlung der Betonoberfläche und damit ihrer Eigenschaften ist ein wichtiger Schritt beim Bau und bei der Renovierung von Bauwerken. ⓘ
Vorgespannte Strukturen

Spannbeton ist eine Form von Stahlbeton, bei der während des Baus Druckspannungen aufgebaut werden, die den Zugspannungen im Betrieb entgegenwirken. Dadurch kann das Gewicht von Balken oder Platten erheblich reduziert werden, da die Spannungen in der Struktur besser verteilt werden, um die Bewehrung optimal zu nutzen. Zum Beispiel neigt ein horizontaler Träger zum Durchhängen. Eine vorgespannte Bewehrung an der Unterseite des Trägers wirkt dem entgegen. Bei vorgespanntem Beton wird die Vorspannung durch die Verwendung von Spanngliedern oder Stäben aus Stahl oder Polymeren erreicht, die vor dem Gießen einer Zugkraft ausgesetzt werden, oder bei nachgespanntem Beton nach dem Gießen. ⓘ
Es werden zwei verschiedene Systeme verwendet:
- Vorgespannter Beton wird fast immer vorgefertigt und enthält Stahldrähte (Spannglieder), die unter Spannung gehalten werden, während der Beton um sie herum eingebracht wird und aushärtet.
- Vorgespannter Beton ist mit Hüllrohren durchzogen. Nachdem der Beton seine Festigkeit erreicht hat, werden die Spannglieder durch die Hüllrohre gezogen und gespannt. Die Hüllrohre werden dann mit Mörtel gefüllt. Bei Brücken, die auf diese Weise gebaut wurden, kam es zu erheblichen Korrosionsschäden an den Spanngliedern, so dass jetzt eine externe Vorspannung verwendet werden kann, bei der die Spannglieder an der Außenfläche des Betons entlanglaufen. Bei vorgespanntem Beton wird die Vorspannung durch die Verwendung von Stahl- oder Polymerspanngliedern oder -stäben erreicht, die vor dem Gießen bzw. bei nachgespanntem Beton nach dem Gießen einer Zugkraft ausgesetzt werden. ⓘ
Mehr als 55.000 Meilen (89.000 km) der Autobahnen in den Vereinigten Staaten sind mit diesem Material gepflastert. Stahlbeton, Spannbeton und Betonfertigteile sind die am häufigsten verwendeten Arten von Funktionserweiterungen aus Beton in der heutigen Zeit. Für weitere Informationen siehe Brutalistische Architektur. ⓘ
Platzierung bei kaltem Wetter

Extreme Wetterbedingungen (extreme Hitze oder Kälte, Wind und Feuchtigkeitsschwankungen) können die Qualität des Betons erheblich beeinträchtigen. Beim Einbau bei kaltem Wetter sind viele Vorsichtsmaßnahmen zu beachten. Niedrige Temperaturen verlangsamen die chemischen Reaktionen bei der Hydratation des Zements erheblich, was sich auf die Festigkeitsentwicklung auswirkt. Die wichtigste Vorsichtsmaßnahme ist die Verhinderung des Einfrierens, da die Bildung von Eiskristallen die kristalline Struktur des hydratisierten Zementsteins beschädigen kann. Wenn die Oberfläche des Betongusses gegen die Außentemperaturen isoliert ist, verhindert die Hydratationswärme das Einfrieren. ⓘ
Die Definition des American Concrete Institute (ACI) für den Einbau bei kaltem Wetter, ACI 306, lautet wie folgt
- Ein Zeitraum, in dem die durchschnittliche tägliche Lufttemperatur an mehr als drei aufeinanderfolgenden Tagen unter 40 °F (~ 4,5 °C) fällt, und
- wenn die Temperatur während mehr als der Hälfte eines beliebigen 24-Stunden-Zeitraums unter 10 °C (50 °F) bleibt. ⓘ
In Kanada, wo die Temperaturen während der kalten Jahreszeit viel niedriger sind, werden die folgenden Kriterien von CSA A23.1 verwendet:
- Wenn die Lufttemperatur ≤ 5 °C ist, und
- wenn die Wahrscheinlichkeit besteht, dass die Temperatur innerhalb von 24 Stunden nach dem Einbringen des Betons unter 5 °C fallen kann. ⓘ
Die Mindestfestigkeit, bevor der Beton der extremen Kälte ausgesetzt wird, beträgt 3,4 MPa (500 psi). CSA A 23.1 schreibt eine Druckfestigkeit von 7,0 MPa vor, die als sicher für die Einwirkung von Frost angesehen wird. ⓘ
Einbringen unter Wasser
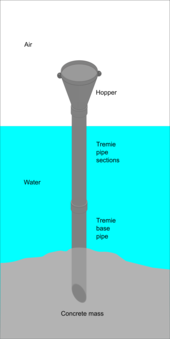
Der Beton kann unter Wasser eingebracht und ausgehärtet werden. Bei der Einbaumethode muss darauf geachtet werden, dass der Zement nicht ausgewaschen wird. Zu den Einbaumethoden unter Wasser gehören das Tremie, das Pumpen, das Einbringen mit dem Skip, das manuelle Einbringen mit Hilfe von Toggle Bags und Bagwork. ⓘ
Verpresste Gesteinskörnung ist eine alternative Methode zur Herstellung einer Betonmasse unter Wasser, bei der die Formen mit groben Gesteinskörnungen gefüllt werden und die Hohlräume dann vollständig mit gepumptem Mörtel ausgefüllt werden. ⓘ
Straßen
Straßen aus Beton sind kraftstoffsparender, reflektierender und halten wesentlich länger als andere Beläge, haben aber einen viel geringeren Marktanteil als andere Beläge. Moderne Pflastermethoden und Entwurfspraktiken haben die Wirtschaftlichkeit von Betonpflastern verändert, so dass ein gut entworfener und eingebauter Betonpflasterbelag bei den Anschaffungskosten günstiger ist und über die gesamte Lebensdauer hinweg deutlich weniger kostet. Ein weiterer großer Vorteil ist, dass wasserdurchlässiger Beton verwendet werden kann, wodurch die Notwendigkeit entfällt, Regenabflüsse in der Nähe der Straße zu verlegen, und die Notwendigkeit einer leicht geneigten Fahrbahn verringert wird, damit das Regenwasser besser abfließen kann. Da das Regenwasser nicht mehr über Abflüsse entsorgt werden muss, wird auch weniger Strom benötigt (da sonst im Wasserverteilungssystem mehr gepumpt werden muss), und das Regenwasser wird nicht verschmutzt, da es sich nicht mehr mit verschmutztem Wasser vermischt. Stattdessen wird es sofort vom Boden aufgenommen. ⓘ
Umwelt, Gesundheit und Sicherheit
Die Herstellung und Verwendung von Beton hat eine Vielzahl von ökologischen, wirtschaftlichen und sozialen Auswirkungen. ⓘ
Beton, Zement und die Umwelt
Die Betonproduktion ist für etwa 6 bis 9 % aller menschengemachten CO2-Emissionen verantwortlich. Dies hat zwei Hauptgründe: das Brennen des für die Betonherstellung benötigten Zements ist sehr energieaufwendig, der größere Teil des freigesetzten Kohlendioxids löst sich jedoch während des Brennvorganges als geogenes CO2 aus dem Kalkstein. Weltweit werden jährlich 4,1 Milliarden Tonnen Zement hergestellt, der im Mittel etwa 60 % CaO enthält. Damit ergibt sich durch das Freisetzen des im Kalk gebundenen Kohlendioxids selbst bei optimaler Prozessführung ein Ausstoß von mindestens zwei Milliarden Tonnen CO2 oder 6 % des weltweiten jährlichen CO2-Ausstoßes. In der Schweiz sind es sogar 9 % aller menschengemachten Emissionen. ⓘ
Weltweit werden eine Reihe von Ansätzen verfolgt, um die Emissionen der Zementherstellung zu begrenzen:
- Chemische Verfahren, bei denen mehr Tonminerale und weniger Kalkstein und Hitze verwendet werden
- Speicherung von Kohlendioxid aus industriellen Prozessen im Beton durch Mineralisierung, siehe CO2-Abscheidung und -Speicherung
- Ersatz des Zements durch andere hydraulische Bindemittel (Puzzuolane), wie Hüttensand (Stahlschlacke) ⓘ
Forscher entwickelten 2020 einen Beton-ähnlichen Werkstoff (living building material, LBM), der bei seiner Produktion kein Kohlenstoffdioxid (CO2) freisetzt. Stattdessen wird das Treibhausgas sogar gebunden. Der Werkstoff geht von einer Mischung aus Sand und Gelatine aus, in der Bakterien (Gattung: Synechococcus) das Treibhausgas mittels Photosynthese in Form von Calciumcarbonat (CaCO3) mineralisieren. Der Werkstoff ist ähnlich stabil wie gewöhnlicher Mörtel (Festigkeit: ∼3.5 MPa, dies entspricht der Mindestfestigkeit von Portlandzementbasis). Die Forscher sehen das Material nicht als vollständigen Ersatz für Zement, sondern mögliche Einsatzzwecke beispielsweise in Strukturen mit geringer Belastung wie Pflaster, Fassaden und temporäre zivile sowie militärische Strukturen. Interessanterweise konnte mittels Einstellen von Temperatur und die Feuchtigkeit die Stoffwechselaktivität der Mikroorganismen kontrolliert werden. In der Studie lebten in dem festen Material nach 30 Tagen bei 50 % relativer Luftfeuchtigkeit noch 9 bis 14 % der Mikroorganismen. ⓘ
Ein Hauptbestandteil von Beton ist Zement, eine feine, weiche, pulverförmige Substanz, die hauptsächlich verwendet wird, um feinen Sand und grobe Zuschlagstoffe in Beton zu binden. Obwohl es eine Vielzahl von Zementarten gibt, ist der gebräuchlichste "Portlandzement", der durch Mischen von Klinker mit kleineren Mengen anderer Zusatzstoffe wie Gips und gemahlenem Kalkstein hergestellt wird. Die Herstellung von Klinker, dem Hauptbestandteil von Zement, ist für den Großteil der Treibhausgasemissionen des Sektors verantwortlich, und zwar sowohl für die Energieintensität als auch für die Prozessemissionen. ⓘ
Beton wird verwendet, um harte Oberflächen zu schaffen, die zum Oberflächenabfluss beitragen, was zu starker Bodenerosion, Wasserverschmutzung und Überschwemmungen führen kann, aber umgekehrt auch dazu, Überschwemmungen umzuleiten, zu dämmen und zu kontrollieren. Betonstaub, der beim Abriss von Gebäuden und bei Naturkatastrophen freigesetzt wird, kann eine wichtige Quelle für gefährliche Luftverschmutzung sein. Beton trägt zum städtischen Wärmeinseleffekt bei, wenn auch in geringerem Maße als Asphalt. ⓘ
Beton und Klimawandel
Eine Verringerung des Zementklinkeranteils könnte sich positiv auf die Ökobilanz von Beton auswirken. Es wurden bereits einige Forschungsarbeiten zur Reduzierung des Zementklinkeranteils in Beton durchgeführt. Allerdings gibt es unterschiedliche Forschungsstrategien. Häufig wurde der Ersatz eines Teils des Klinkers durch große Mengen an Schlacke oder Flugasche auf der Grundlage der herkömmlichen Betontechnologie untersucht. Dies könnte zu einer Verschwendung von knappen Rohstoffen wie Schlacke und Flugasche führen. Das Ziel anderer Forschungsaktivitäten ist die effiziente Verwendung von Zement und reaktiven Materialien wie Schlacke und Flugasche in Beton auf der Grundlage eines modifizierten Mischungsentwurfs. ⓘ
Eine Umweltuntersuchung ergab, dass der Kohlenstoffgehalt einer vorgefertigten Betonfassade um 50 % gesenkt werden kann, wenn der vorgestellte faserverstärkte Hochleistungsbeton anstelle einer herkömmlichen Stahlbetonverkleidung verwendet wird. ⓘ
Die Studien wurden in der Erwartung durchgeführt, dass sie als Daten für die Kommerzialisierung von kohlenstoffarmen Betonen genutzt werden können. Die Ökobilanz (LCA) von kohlenstoffarmem Beton wurde in Abhängigkeit vom Verhältnis des Ersatzes von Hüttensand (GGBS) und Flugasche (FA) untersucht. Das globale Erwärmungspotenzial (GWP) von GGBS sank um 1,1 kg CO2-Äq/m3, während FA um 17,3 kg CO2-Äq/m3 sank, wenn der Anteil der Mineralzusatzstoffe um 10 % erhöht wurde. In dieser Studie wurden auch die Druckfestigkeitseigenschaften von binär gemischtem kohlenstoffarmen Beton in Abhängigkeit von den Austauschverhältnissen verglichen und der anwendbare Bereich von Mischungsverhältnissen abgeleitet. ⓘ
Forscher der University of Auckland arbeiten an der Verwendung von Biokohle in Betonanwendungen, um die Kohlenstoffemissionen bei der Betonherstellung zu verringern und die Festigkeit zu verbessern. ⓘ
Beton und Anpassung an den Klimawandel
Leistungsstarke Baumaterialien sind besonders wichtig, um die Widerstandsfähigkeit zu erhöhen, auch für den Hochwasserschutz und den Schutz kritischer Infrastrukturen. Die Risiken für die Infrastruktur und die Städte, die durch extreme Wetterereignisse entstehen, sind besonders groß an Orten, die Überschwemmungen und Hurrikanen ausgesetzt sind, aber auch dort, wo die Bewohner vor extremen Sommertemperaturen geschützt werden müssen. Herkömmlicher Beton kann durch Feuchtigkeit und höhere CO2-Konzentrationen in der Atmosphäre unter Druck geraten. Auch wenn Beton in Bereichen mit schwierigen Umweltbedingungen weiterhin eine wichtige Rolle spielen wird, sind auch neuartige, intelligentere und anpassungsfähigere Materialien erforderlich. ⓘ
Beton - Gesundheit und Sicherheit

Beim Schleifen von Beton kann gefährlicher Staub entstehen. Die Exposition gegenüber Zementstaub kann zu Problemen wie Silikose, Nierenerkrankungen, Hautreizungen und ähnlichen Auswirkungen führen. Das U.S. National Institute for Occupational Safety and Health (Nationales Institut für Arbeitssicherheit und Gesundheitsschutz) in den Vereinigten Staaten empfiehlt, elektrische Betonschleifmaschinen mit lokalen Absaugvorrichtungen auszustatten, um die Ausbreitung dieses Staubs zu kontrollieren. Darüber hinaus hat die Occupational Safety and Health Administration (OSHA) strengere Vorschriften für Unternehmen erlassen, deren Mitarbeiter regelmäßig mit Quarzstaub in Kontakt kommen. Eine aktualisierte Siliziumdioxidvorschrift, die die OSHA am 23. September 2017 für Bauunternehmen in Kraft gesetzt hat, beschränkt die Menge an atembarem kristallinem Siliziumdioxid, mit der Arbeitnehmer legal in Kontakt kommen können, auf 50 Mikrogramm pro Kubikmeter Luft pro achtstündigem Arbeitstag. Dieselbe Vorschrift trat am 23. Juni 2018 für die allgemeine Industrie, Hydraulic Fracturing und die Schifffahrt in Kraft. Die Frist wurde für technische Kontrollen in der Hydraulic-Fracturing-Industrie bis zum 23. Juni 2021 verlängert. Unternehmen, die die verschärften Sicherheitsvorschriften nicht einhalten, können mit finanziellen Belastungen und umfangreichen Strafen rechnen. Das Vorhandensein einiger Stoffe im Beton, einschließlich nützlicher und unerwünschter Zusatzstoffe, kann aufgrund von Toxizität und Radioaktivität zu gesundheitlichen Problemen führen. Frischer Beton (vor dem Aushärten) ist stark alkalisch und muss mit entsprechender Schutzausrüstung gehandhabt werden. ⓘ
Kreislaufwirtschaft
Beton ist ein hervorragendes Material für die Herstellung langlebiger und energieeffizienter Gebäude. Doch selbst bei guter Planung ändern sich die Bedürfnisse der Menschen, und es entsteht potenzieller Abfall. ⓘ
End-of-Life: Betonabbau und Abfall

Beton kann durch viele Prozesse geschädigt werden, z. B. durch die Ausdehnung von Korrosionsprodukten der Stahlbewehrungsstäbe, das Einfrieren von eingeschlossenem Wasser, Feuer oder Strahlungswärme, die Ausdehnung von Zuschlagstoffen, Meerwassereinwirkung, bakterielle Korrosion, Auslaugung, Erosion durch schnell fließendes Wasser, physikalische Schäden und chemische Schäden (durch Karbonatisierung, Chloride, Sulfate und Destillatwasser). Die Mikropilze Aspergillus alternaria und Cladosporium konnten auf Betonproben wachsen, die als Barriere für radioaktive Abfälle im Reaktor von Tschernobyl verwendet wurden; sie laugen Aluminium, Eisen, Kalzium und Silizium aus. ⓘ
Beton kann gemäß dem Beschluss der Europäischen Kommission von 2014/955/EU für das Abfallverzeichnis unter den folgenden Codes als Abfall betrachtet werden: 17 (Bau- und Abbruchabfälle, einschließlich Bodenaushub von kontaminierten Standorten) 01 (Beton, Ziegel, Fliesen und Keramik), 01 (Beton) und 17. 01.06* (Gemische aus, getrennte Fraktionen von Beton, Ziegeln, Fliesen und Keramik, die gefährliche Stoffe enthalten), und 17.01.07 (Gemische aus, getrennte Fraktionen von Beton, Ziegeln, Fliesen und Keramik, die nicht unter 17.01.06 fallen). Schätzungen zufolge fielen in der Europäischen Union im Jahr 2018 371.910 Tausend Tonnen mineralische Bau- und Abbruchabfälle an, von denen fast 4 % als gefährlich eingestuft werden. Deutschland, Frankreich und das Vereinigte Königreich waren die drei größten Verursacher mit 86.412 Tausend Tonnen, 68.976 und 68.732 Tausend Tonnen Bauabfall. ⓘ
Derzeit gibt es in der EU keine End-of-Waste-Kriterien für Betonmaterialien. Verschiedene Sektoren haben jedoch Alternativen für Betonabfälle vorgeschlagen und sie als Sekundärrohstoffe für verschiedene Anwendungen, einschließlich der Betonherstellung selbst, wiederverwendet. ⓘ
Wiederverwendung von Beton
Die Wiederverwendung von Blöcken in ihrer ursprünglichen Form oder durch Zerschneiden in kleinere Blöcke hat noch geringere Umweltauswirkungen; allerdings gibt es derzeit nur einen begrenzten Markt. Verbesserte Gebäudekonzepte, die die Wiederverwendung von Platten und die Umgestaltung von Gebäuden ohne Abriss ermöglichen, könnten diese Verwendung steigern. Hohlkörperplatten aus Beton sind leicht zu demontieren, und die Spannweite ist normalerweise konstant, so dass sie sich gut für die Wiederverwendung eignen. ⓘ
Andere Fälle von Wiederverwendung sind mit Betonfertigteilen möglich: Durch selektiven Abriss können solche Teile demontiert und zur weiteren Verwendung auf anderen Baustellen gesammelt werden. Studien zeigen, dass die Rück- und Wiederaufbauplanung von Bauteilen (d.h. die Wiederverwendung von Betonfertigteilen) eine Alternative für eine ressourcenschonende und energiesparende Bauweise darstellt. Besonders langlebige, dauerhafte, energieintensive Baustoffe wie Beton können durch Recycling länger im Lebenszyklus gehalten werden. Vorgefertigte Konstruktionen sind die Voraussetzung für notwendigerweise zerlegbare Konstruktionen. Bei optimaler Anwendung im Rohbau werden die Kosteneinsparungen auf 26% geschätzt, eine lukrative Ergänzung zu neuen Bauweisen. Allerdings hängt dies von mehreren zu setzenden Weichen ab. Die Durchführbarkeit dieser Alternative muss untersucht werden, da die mit dem Transport schwerer Betonteile verbundene Logistik den Betrieb finanziell beeinträchtigen und auch die CO2-Bilanz des Projekts erhöhen kann. Außerdem können die sich ständig ändernden Vorschriften für neue Gebäude weltweit höhere Qualitätsstandards für Bauelemente erfordern und die Verwendung alter Elemente, die als veraltet eingestuft werden könnten, verhindern. ⓘ
Recycling von Beton
Betonrecycling ist eine zunehmend verbreitete Methode für die Entsorgung von Betonkonstruktionen. Früher wurde Betonschutt routinemäßig auf Mülldeponien entsorgt, aber das Recycling nimmt aufgrund des gestiegenen Umweltbewusstseins, staatlicher Gesetze und wirtschaftlicher Vorteile zu. ⓘ
Entgegen der allgemeinen Annahme ist die Rückgewinnung von Beton möglich - Beton kann zerkleinert und als Zuschlagstoff für neue Projekte wiederverwendet werden. ⓘ
Das Recycling oder die Rückgewinnung von Beton verringert die Ausbeutung natürlicher Ressourcen und die damit verbundenen Transportkosten und reduziert die Abfalldeponien. Es hat jedoch kaum Auswirkungen auf die Verringerung der Treibhausgasemissionen, da die meisten Emissionen bei der Herstellung von Zement entstehen und Zement allein nicht recycelt werden kann. Gegenwärtig wird der meiste wiedergewonnene Beton für den Unterbau von Straßen und für Tiefbauprojekte verwendet. Unter dem Gesichtspunkt der Nachhaltigkeit bieten diese relativ minderwertigen Verwendungen derzeit das optimale Ergebnis. ⓘ
Der Recyclingprozess kann an Ort und Stelle, mit mobilen Anlagen oder in speziellen Recyclinganlagen durchgeführt werden. Das Ausgangsmaterial kann frischer (nasser) Rücklaufbeton aus Transportbetonmischern, Produktionsabfälle aus Fertigteilwerken oder Abfälle aus Bau- und Abbrucharbeiten sein. Die wichtigste Quelle sind Abbruchabfälle, vorzugsweise vorsortiert aus selektiven Abbruchprozessen. ⓘ
Die bei weitem häufigste Methode für das Recycling von trockenem und gehärtetem Beton ist das Zerkleinern. Mobile Sortieranlagen und Brecher werden häufig auf Baustellen installiert, um die Verarbeitung vor Ort zu ermöglichen. In anderen Fällen werden spezielle Aufbereitungsanlagen eingerichtet, die in der Regel in der Lage sind, höherwertige Zuschlagstoffe zu produzieren. Siebe werden eingesetzt, um die gewünschte Korngröße zu erreichen und Schmutz, Fremdpartikel und Feinmaterial aus den groben Zuschlagstoffen zu entfernen. ⓘ
Chloride und Sulfate sind unerwünschte Verunreinigungen, die aus dem Boden und der Witterung stammen und Korrosionsprobleme an Aluminium- und Stahlkonstruktionen hervorrufen können. Das Endprodukt, Recycled Concrete Aggregate (RCA), weist interessante Eigenschaften auf: kantige Form, raue Oberfläche, niedrigeres spezifisches Gewicht (20 %), höhere Wasseraufnahme und einen pH-Wert von über 11 - dieser erhöhte pH-Wert erhöht das Risiko von Alkalireaktionen. ⓘ
Die geringere Dichte von RCA erhöht in der Regel die Projekteffizienz und senkt die Auftragskosten - rezyklierte Betonzuschläge liefern mehr Volumen nach Gewicht (bis zu 15 %). Die physikalischen Eigenschaften von groben Gesteinskörnungen aus gebrochenem Abbruchbeton machen sie zum bevorzugten Material für Anwendungen wie Straßenunterbau und Unterbau. Dies liegt daran, dass rezyklierte Gesteinskörnungen oft bessere Verdichtungseigenschaften aufweisen und weniger Zement für den Unterbau benötigen. Außerdem sind sie im Allgemeinen billiger zu beschaffen als neues Material. ⓘ
Anwendungen von rezyklierten Betonzuschlagstoffen
Die wichtigsten kommerziellen Anwendungen der endgültigen rezyklierten Betonzuschlagstoffe sind:
- Die Tragschicht oder die unbehandelten Gesteinskörnungen, die als Grundlage für Straßenbeläge verwendet werden, sind die darunter liegende Schicht (unter dem Straßenbelag), die die strukturelle Grundlage für den Straßenbau bildet. Bis heute ist dies aus technisch-wirtschaftlichen Gründen die beliebteste Anwendung für RCA.
- Zuschlagstoffe für Transportbeton, indem einfach 10 bis 45 % der natürlichen Zuschlagstoffe in der Betonmischung durch eine Mischung aus Zement, Sand und Wasser ersetzt werden. Einige Konzeptgebäude zeigen die Fortschritte in diesem Bereich. Da das RCA Zement enthält, müssen die Mischungsverhältnisse angepasst werden, um die gewünschten strukturellen Anforderungen wie Verarbeitbarkeit, Festigkeit und Wasseraufnahme zu erreichen.
- Bodenstabilisierung: Einarbeitung von rezyklierten Gesteinskörnungen, Kalk oder Flugasche in minderwertiges Unterbaumaterial, um die Tragfähigkeit des Untergrunds zu verbessern.
- Rohrbettung: Dient als stabiles Bett oder festes Fundament für die Verlegung unterirdischer Versorgungsleitungen. Die Vorschriften einiger Länder verbieten die Verwendung von RCA und anderen Bau- und Abbruchabfällen in Filter- und Drainagebetten aufgrund einer möglichen Verunreinigung mit Chrom und Auswirkungen auf den pH-Wert.
- Landschaftsbaumaterialien: zur Förderung einer grünen Architektur. Bislang wurden rezyklierte Betonzuschläge für Felswände, Unterführungsbauwerke, Erosionsstrukturen, Wasserspiele, Stützmauern und vieles mehr verwendet. ⓘ
Cradle-to-Cradle-Herausforderungen
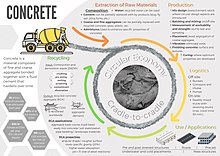
Die bisher für RCA entwickelten Anwendungen sind nicht erschöpfend, und es werden noch viele weitere Anwendungen entwickelt, da Vorschriften, Institutionen und Normen Wege finden, Bau- und Abbruchabfälle als Sekundärrohstoffe auf sichere und wirtschaftliche Weise zu nutzen. In Anbetracht des Ziels der Kreislaufführung von Ressourcen im Lebenszyklus von Beton ist die einzige Anwendung von RCA, die als Recycling von Beton betrachtet werden könnte, der Ersatz von natürlichen Zuschlagstoffen in Betonmischungen. Alle anderen Anwendungen würden unter die Kategorie des Downcycling fallen. Es wird geschätzt, dass selbst bei einer nahezu vollständigen Verwertung von Beton aus Bau- und Abbruchabfällen nur etwa 20 % des Gesamtbedarfs an Zuschlagstoffen in den Industrieländern gedeckt werden können. ⓘ
Der Weg zur Kreislaufwirtschaft geht über die eigentliche Betontechnologie hinaus und hängt von multilateralen Fortschritten in der Zementindustrie, der Forschung und Entwicklung alternativer Materialien, der Bauplanung und -verwaltung, dem Abriss sowie der bewussten Nutzung von Flächen in städtischen Gebieten zur Verringerung des Verbrauchs ab. ⓘ
Weltrekorde
Der Weltrekord für den größten Betonguss in einem einzigen Projekt ist der Drei-Schluchten-Damm in der Provinz Hubei, China, der von der Three Gorges Corporation errichtet wurde. Die für den Bau des Staudamms verwendete Betonmenge wird auf 16 Millionen Kubikmeter in 17 Jahren geschätzt. Der bisherige Rekord lag bei 12,3 Millionen Kubikmetern, gehalten vom Itaipu-Wasserkraftwerk in Brasilien. ⓘ
Der Weltrekord im Pumpen von Beton wurde am 7. August 2009 beim Bau des Parbati-Wasserkraftprojekts in der Nähe des Dorfes Suind im indischen Bundesstaat Himachal Pradesh aufgestellt, als die Betonmischung durch eine vertikale Höhe von 715 m gepumpt wurde. ⓘ
Das Polavaram-Staudammwerk in Andhra Pradesh wurde am 6. Januar 2019 in das Guinness-Buch der Rekorde aufgenommen, weil in 24 Stunden 32.100 Kubikmeter Beton gegossen wurden. Der Weltrekord für das größte kontinuierlich gegossene Betonfloß wurde im August 2007 in Abu Dhabi vom Bauunternehmen Al Habtoor-CCC Joint Venture und dem Betonlieferanten Unibeton Ready Mix aufgestellt. Bei dem Guss (ein Teil des Fundaments für den Landmark Tower in Abu Dhabi) wurden innerhalb von zwei Tagen 16 000 Kubikmeter Beton gegossen. Der bisherige Rekord von 13 200 Kubikmetern, die in 54 Stunden gegossen wurden, obwohl die Baustelle wegen eines schweren Tropensturms mit Planen abgedeckt werden musste, um die Arbeiten fortzusetzen, wurde 1992 von den japanisch-südkoreanischen Konsortien Hazama Corporation und Samsung C&T Corporation für den Bau der Petronas Towers in Kuala Lumpur, Malaysia, aufgestellt. ⓘ
Der Weltrekord für den größten kontinuierlich gegossenen Betonboden wurde am 8. November 1997 in Louisville, Kentucky, von der Projektentwicklungsfirma EXXCEL Project Management aufgestellt. Der monolithische Einbau bestand aus 225.000 Quadratfuß (20.900 m2) Beton, der in 30 Stunden mit einer Ebenheitstoleranz von FF 54,60 und einer Ebenheitstoleranz von FL 43,83 eingebaut wurde. Damit wurde der bisherige Rekord um 50 % im Gesamtvolumen und 7,5 % in der Gesamtfläche übertroffen. ⓘ
Der Rekord für den größten kontinuierlich eingebrachten Unterwasserbeton wurde am 18. Oktober 2010 in New Orleans, Louisiana, vom Bauunternehmen C. J. Mahan Construction Company, LLC aus Grove City, Ohio, aufgestellt. Dabei wurden 10.251 Kubikmeter Beton in 58,5 Stunden mit zwei Betonpumpen und zwei speziellen Betonmischanlagen eingebracht. Nach dem Aushärten des Betons kann der 4.662 m2 große Kofferdamm etwa 7,9 m unter dem Meeresspiegel entwässert werden, so dass der Bau des Inner Harbor Navigation Canal Sill & Monolith Project im Trockenen abgeschlossen werden kann. ⓘ
Unterscheidungsmerkmale
Beton lässt sich anhand verschiedener Merkmale unterscheiden. Gebräuchlich sind Unterscheidungen nach
- der Trockenrohdichte in Leichtbeton, Normalbeton und Schwerbeton,
- der Festigkeit, wobei die Druckfestigkeit die wichtigste Rolle einnimmt,
- dem Ort der Herstellung in Baustellen- oder Transportbeton,
- dem Verwendungszweck in beispielsweise wasserundurchlässigen Beton, Unterwasserbeton,
- der Konsistenz in Klassen von steif bis (sehr) fließfähig,
- der Art der Verdichtung in Rüttelbeton, Stampfbeton, Walzbeton, Fließbeton, Schüttbeton, Spritzbeton, …
- der Art der Gesteinskörnung in Sandbeton, Kiesbeton, Splittbeton, …
- dem Erhärtungszustand in den noch verarbeitbaren Frischbeton, den bereits eingebauten und verdichteten grünen Beton, den jungen Beton, dessen Aushärtung bereits begonnen hat und schließlich den ausgehärteten Festbeton,
- den Anforderungen zur Qualitätssicherung in Rezeptbeton (Herstellungsklasse R nach ÖNORM 4200 bzw. Klasse B I nach DIN 1045) und Beton nach Eignungsprüfung (Herstellungsklasse E bzw. Klasse B II nach DIN). ⓘ
Ebenso wie Beton ist Mörtel ein Gemisch aus einem Bindemittel, Gesteinskörnung und Zusatzstoffen bzw. -mitteln. Der Unterschied besteht in der Größe des Zuschlags, der bei Mörtel höchstens 4 mm im Durchmesser aufweisen darf. Eine Überschneidung besteht bei Spritzputzen und Mauermörteln, die in besonderen Fällen ein Größtkorn von bis zu 16 mm enthalten können, sowie bei Estrich, der im Regelfall mit 8 mm Körnung angemischt wird. ⓘ
Klima- und Umweltauswirkungen
Umweltprobleme
Sand- und Kies-Abbau
Für Sand besteht eine weltweit hohe Nachfrage, da er neben Wasser, Kies und Zement einer der Hauptbestandteile von Beton ist. Der weltweite Abbau von Sand für die Bauwirtschaft und insbesondere die Betonproduktion führt zu einer Verknappung des Rohstoffes. 95 Prozent des weltweit vorhandenen Sands, insbesondere Wüstensand, sind allerdings schlecht für die Betonherstellung geeignet, da die Körner zu fein sind. Anders als früher vermutet, spielt die abgeschliffene Form der Körner keine nennenswerte Rolle. Dem Wüstensand fehlen hingegen die Mittel- und Grobsandteile, welche im Beton als Stützkorn essentiell sind. ⓘ
Ein gewisser Prozentsatz des Sand- und Kiesanteils lässt sich durch den beim Recycling von Beton gewonnenen Betonbruch ersetzen. Siehe Recyclingbeton ⓘ
2018 wurde ein Verfahren patentiert, welches die Verwendung von Wüstensand und Feinsand erlaubt. Der Sand wird in einem Mahlwerk zu Steinmehl verarbeitet, das anschließend mit mineralischen Bindemitteln zu einem Granulat vermengt wird. Hieraus lässt sich besonders belastbarer Beton herstellen, der zudem 40 % weniger Zement benötigt. Die Verwendung von Wüstensand lohnt sich in Europa nicht, da die Transportkosten oft ab ca. 50 km den Materialwert übersteigen. Allein in Deutschland fallen jedoch pro Jahr hunderttausende Tonnen bislang ungenutzten Feinsands an. Im Frühjahr 2020 sollten zwei erste Anlagen in Saudi-Arabien und in Ägypten in Betrieb genommen werden. 2019 prüfte das Institut für Angewandte Bauforschung (IAB) in Weimar den Baustoff. Im Erfolgsfall könnte auf Basis eines zertifizierten Prüfberichts des Instituts für Angewandte Bauforschung das Deutsche Institut für Bautechnik derartigen Beton zur Verwendung in Deutschland freigeben. ⓘ
Frischbeton
Bestandteile und Zusammensetzung
Die Zusammensetzung eines Betons wird vor der industriellen Herstellung in einer Betonrezeptur nach Norm festgelegt, die durch Erfahrungswerte und Versuche angepasst wird. Die Zusammensetzung richtet sich insbesondere nach der gewünschten Festigkeitsklasse, den Umweltbedingungen denen das spätere Bauteil ausgesetzt sein wird und der gewünschten Verarbeitbarkeit, bei Sichtbeton auch nach dem optischen Erscheinungsbild. Dementsprechend werden Zement, Wasser, Gesteinskörnung, Betonzusatzstoffe und Betonzusatzmittel in einem bestimmten Verhältnis vermischt. ⓘ
Zur Herstellung eines Kubikmeters Beton der Festigkeitsklasse C25/30 werden ungefähr 300 kg Zement, 180 l Wasser sowie 1890 kg Zuschläge benötigt. Um die genauen Festbetoneigenschaften abzuschätzen, reichen diese Angaben nicht aus. Sowohl der Zement als auch die Zuschläge können je nach gewähltem Produkt die Festigkeit erheblich beeinflussen. Zur Herstellung von kritischen Bauteilen müssen die Eigenschaften der Ausgangsstoffe bekannt und das Mischungsverhältnis durch Messung von Gewicht oder Volumen genau bestimmt werden können. ⓘ
Bei der nicht-industriellen Herstellung wie auf Kleinbaustellen wird in der Regel auf das Abwiegen der Bestandteile verzichtet. ⓘ
Mischvorgang
Der Wasser-Zement-Wert ist für die Festigkeit und Dichtigkeit von überragender Bedeutung. Von der Dichtigkeit hängt wiederum die Dauerhaftigkeit von Beton ab, der korrosiven Einflüssen ausgesetzt ist. Dies betrifft Stahlbeton, welcher der Witterung ausgesetzt ist. Auch Grundwasser kann korrosive Stoffe beinhalten. ⓘ
Typischerweise wird zunächst das Anmachwasser mit dem zugehörigen Zementanteil zum Zementleim vorgemischt. Meist wird bereits eine gewisse Menge Kies hinzugefügt, um das Vermischen des Zementpulvers mit dem Wasser zu beschleunigen. Wenn es auf den verwendeten Sand oder poröse Zuschläge zuvor geregnet hat, erhöht sich deren Feuchtigkeitsgehalt so deutlich, dass dies beim Mischungsverhältnis zu berücksichtigen ist. Bei Verwendung von feuchten Zuschlägen empfiehlt es sich, einen Anteil des abgemessenen Anmachwassers zurückzuhalten, um die so eingebrachte Feuchte auszugleichen. ⓘ
Beim manuellen Anmischen wird in einem zweiten Schritt dann nach und nach die Menge an Zuschlag hinzugefügt, die nötig ist, um die gewünschte Konsistenz zu erreichen. ⓘ
Konsistenz
Die Konsistenz des Frischbetons beschreibt wie fließfähig bzw. steif der Frischbeton ist. Sie ist vorab entsprechend zu wählen, sodass der Beton ohne wesentliche Trennung der gröberen und feineren Bestandteile gefördert, eingebaut und praktisch vollständig verdichtet werden kann. Die dafür maßgebende Frischbetoneigenschaft ist die Verarbeitbarkeit. Die Frischbetonkonsistenz ist vor Baubeginn festzulegen und während der Bauausführung einzuhalten. ⓘ
Die genormten Konsistenzbereiche erstrecken sich von „(sehr) steif“, über „plastisch“, „weich“ und „sehr weich“ bis hin zu „(sehr) fließfähig“. An die Konsistenzbereiche sind Messwerte geknüpft, die mit genormten, baustellengerechten Verfahren, wie dem Ausbreitversuch, dem Setzversuch und dem Verdichtungsversuch geprüft und kontrolliert werden können. Das nachträgliche Zumischen von Wasser zum fertigen Frischbeton, z. B. bei Ankunft auf der Baustelle, verbessert zwar die Fließeigenschaften, ist nach den deutschen Vorschriften allerdings unzulässig, da dadurch der Wasserzementwert (w/z-Wert) und in der Folge die Festbetoneigenschaften negativ beeinflusst werden. Einem Transportbeton darf vor Ort aber Fließmittel beigemischt werden, um die Verarbeitbarkeit zu verbessern. Die zulässige Höchstmenge liegt bei 2 l/m³, was aus einem plastischen Beton einen leicht fließfähigen Beton macht. ⓘ
Die Einbaubedingungen legen die nötige Konsistenz fest. Für Bauteile mit komplizierten Geometrien oder hohen Bewehrungsgraden ist tendenziell ein eher fließfähigerer Beton vonnöten. Auch die Förderung des Frischbetons bestimmt die benötigte Konsistenz. Soll ein Beton beispielsweise mit einer Betonpumpe gefördert werden, sollte die Betonkonsistenz mindestens im plastischen Bereich, d. h. Ausbreitmaßklasse F2, besser F3, liegen. ⓘ
Einbau und Verdichtung

Beton ist schnellstmöglich nach dem Mischen bzw. der Anlieferung einzubauen und mit geeigneten Geräten zu verdichten. Durch das Verdichten werden die Lufteinschlüsse ausgetrieben, damit ein dichtes Betongefüge mit wenigen Luftporen entsteht. Rütteln, Schleudern, Stampfen, Stochern, Spritzen und Walzen sind je nach Betonkonsistenz und Einbaumethode geeignete Verdichtungsverfahren. Als Verdichtungsgerät kommt auf Baustellen des Hochbaus heutzutage in der Regel der Innenrüttler (auch „Flaschen-“ oder „Tauchrüttler“ genannt) zum Einsatz. Bei der Herstellung hoher Bauteile oder bei sehr enger Bewehrung können auch Außenrüttler („Schalungsrüttler“) verwendet werden. Beim Einbau von Beton für Straßen oder Hallenböden ist eine Verdichtung mit Hilfe von Rüttelbohlen üblich. Rütteltische werden im Fertigteilwerk benutzt. ⓘ
Bereits beim Einbau ist darauf zu achten, dass sich der Beton nicht entmischt, d. h., dass sich größere Körner unten absetzen und sich an der Oberfläche eine Wasser- oder Wasserzementschicht bildet. Frischbeton darf deshalb nicht aus größerer Höhe in die Schalung fallen gelassen werden. Durch Rutschen, Fallrohre oder Schläuche ist der Beton bis in die Schalung zu leiten, sodass die maximale freie Fallhöhe nicht mehr als 1,5 m beträgt. Um anschließend gut verdichten zu können, muss der Beton außerdem in Lagen von höchstens 50 cm Höhe eingebaut werden. Erst nach der Verdichtung einer Lage folgt die nächste. ⓘ
Ein Entmischen, sodass sich an der Oberfläche eine wässrige Zementschlämme bildet, kann sich auch bei einer zu großen Rütteldauer einstellen. Das Absondern von Wasser an der Betonoberfläche nach dem Einbau wird auch als „Bluten“ bezeichnet. Die Entmischung wirkt sich insbesondere nachteilig auf die Festigkeit und Dauerhaftigkeit des Betons aus. Bei richtiger Verdichtung und passender Konsistenz bildet sich an der Oberfläche nur eine dünne Feinmörtelschicht. Im restlichen Betonkörper sind die Gesteinskörner annähernd gleichmäßig verteilt. ⓘ
Beim Einbau des Frischbetons sollte die Betontemperatur zwischen +5 °C und +30 °C liegen, anderenfalls sind besondere Maßnahmen erforderlich. Im Winter kann dies z. B. das Heizen der Schalung mit Gebläsen sein. Im Sommer ist gegebenenfalls eine Kühlung des Betons notwendig. ⓘ
Erhärtung
Der Zement dient als Bindemittel, um die anderen Bestandteile zusammenzuhalten. Die Festigkeit des Betons entsteht durch die exotherme Reaktion der Auskristallisierung der Klinkerbestandteile des Zements unter Wasseraufnahme. Es wachsen Kristallnadeln, die sich fest ineinander verzahnen. Das Kristallwachstum hält über Monate an, sodass die endgültige Festigkeit erst lange nach dem Betonguss erreicht wird. Es wird aber wie in der DIN 1164 (Festigkeitsklassen von Zement) angenommen, dass bei normalen Temperatur- und Feuchtigkeitsbedingungen nach 28 Tagen die Normfestigkeit erreicht ist. Neben dieser hydraulischen Reaktion entwickelt sich bei silikatischen Zuschlagstoffen zusätzlich die sogenannte puzzolanische Reaktion. ⓘ
Eigenschaften des Festbetons
Als Festbeton wird der erhärtete Frischbeton bezeichnet. ⓘ
Festigkeitsklassen
Die Druckfestigkeit ist eine der wichtigsten Eigenschaften des Betons. Die DIN 1045-2 (Tragwerke aus Beton, Stahlbeton und Spannbeton) schreibt eine Beurteilung durch die Prüfung nach 28 Tagen Wasserlagerung anhand von Würfeln mit 15 cm Kantenlänge (Probewürfeln) oder 30 cm langen Zylindern mit 15 cm Durchmesser vor. Die Vorschriften für die Geometrie und Lagerung der Prüfkörper sind weltweit nicht einheitlich geregelt und haben sich auch in den einzelnen Normgenerationen geändert. Anhand der ermittelten Druckfestigkeit, die im Bauteil abweichen kann, lässt sich der Beton den Festigkeitsklassen zuordnen. Ein C12/15 hat danach die charakteristische Zylinderdruckfestigkeit von 12 N/mm² sowie eine charakteristische Würfeldruckfestigkeit von 15 N/mm². Das C in der Nomenklatur steht für englisch concrete (deutsch: „Beton“). Im Zuge der Harmonisierung des europäischen Normenwerks sind diese Betonfestigkeitsklassen in der aktuellen Normengeneration europaweit vereinheitlicht. In der folgenden Tabelle sind die Bezeichnungen nach der alten DIN 1045 noch zur Information in der letzten Spalte angegeben. ⓘ
Die Beton-Festigkeitsklasse ist nicht zu verwechseln mit der Zement-Festigkeitsklasse (Normfestigkeit von 32,5, 42,5 und 52,5 N/mm²) nach EN 197. ⓘ
Über- wachungs- klasse |
Festig- keits- klasse |
Zylinderdruckfestigkeit (N/mm²) | Mittlere Zugfestigkeit (N/mm²) |
Mittlerer E-Modul (N/mm²) |
Bezeichnung nach alter DIN 1045 | |
---|---|---|---|---|---|---|
charakteristisch |
Mittelwert | |||||
1 | C8/10* | 8 / 10 | − | − | − | B10 |
C12/15 | 12 / 15 | 20 | 1,6 | 27000 | B15 | |
C16/20 | 16 / 20 | 24 | 1,9 | 29000 | − | |
C20/25 | 20 / 25 | 28 | 2,2 | 30000 | B25 | |
C25/30 | 25 / 30 | 33 | 2,6 | 31000 | − | |
2 | C30/37 | 30 / 37 | 38 | 2,9 | 33000 | B35 |
C35/45 | 35 / 45 | 43 | 3,2 | 34000 | B45 | |
C40/50 | 40 / 50 | 48 | 3,5 | 35000 | − | |
C45/55 | 45 / 55 | 53 | 3,8 | 36000 | B55 | |
C50/60 | 50 / 60 | 58 | 4,1 | 37000 | − | |
3 | C55/67 | 55 / 67 | 63 | 4,2 | 38000 | B65 |
C60/75 | 60 / 75 | 68 | 4,4 | 39000 | B75 | |
C70/85 | 70 / 85 | 78 | 4,6 | 41000 | B85 | |
C80/95 | 80 / 95 | 88 | 4,8 | 42000 | B95 | |
C90/105 | 90 / 105 | 98 | 5,0 | 44000 | − | |
C100/115 | 100 / 115 | 108 | 5,2 | 45000 | − | |
Elastizitätsmodul, Schubmodul und Querdehnungszahl
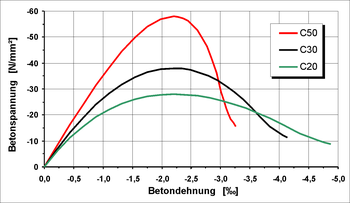
Der Elastizitätsmodul des Betons hängt in hohem Maße von den verwendeten Betonzuschlägen ab. Vereinfachend kann er im linear-elastischen Spannungszustand (d. h. maximal 40 % der Festigkeit) in Abhängigkeit von der Betonfestigkeit nach dem Eurocode mit der empirischen Gleichung ermittelt werden. Somit beträgt der Elastizitätsmodul bei den Betonfestigkeitsklassen von C12/15 bis C50/60 nach Eurocode zwischen 27.000 N/mm² und 37.000 N/mm². ⓘ
Die Querdehnungszahl schwankt im Bereich der Gebrauchsspannungen je nach Betonzusammensetzung, Betonalter und Betonfeuchte zwischen 0,15 und 0,25. Gemäß den Normen kann der Einfluss mit 0,2 bei ungerissenem Beton berücksichtigt werden. Für gerissenen Beton ist die Querdehnungszahl zu Null zu setzen. ⓘ
Der Schubmodul kann näherungsweise, wie bei isotropen Baustoffen, aus Elastizitätsmodul und Querdehnungszahl errechnet werden. ⓘ
Rohdichte
Die Rohdichte des Betons hängt vom Zuschlag ab. Bei Normalbeton beträgt die Trockenrohdichte zwischen 2000 und 2600 kg/m³. Meist können 2400 kg/m³ angesetzt werden. Betone oberhalb von 2600 kg/m³ werden als Schwerbeton bezeichnet, unterhalb von 2000 kg/m³ als Leichtbeton. ⓘ
Leichtbeton hat porige Leichtzuschläge wie Blähton oder Bims. Er ist normativ in die Rohdichteklassen 1,0 – 1,2 – 1,4 – 1,6 – 1,8 – 2,0 eingeteilt, welche den Rohdichten zwischen 1000 und 2000 kg/m³ entsprechen. Stahlbeton hat näherungsweise eine um 100 kg/m³ erhöhte Rohdichte. ⓘ
Verbundzone

Eine Schwachstelle im Gefüge des hydratisierten Betons stellt die Verbundzone zwischen Zementstein und Gesteinskörnung dar. Durch die Ansammlung von Ettringit und Portlandit (CH, Calciumhydroxid) an den Rändern der Gesteinskörner können sich keine verfestigenden CSH-Phasen bilden. Das hat eine verringerte Festigkeit in diesem Bereich zur Folge. Durch Zugabe von Puzzolanen wird das Portlandit über die puzzolanische Reaktion in CSH-Phasen umgewandelt. Puzzolane sind hochsilikatische Zuschlagsstoffe wie Mikrosilika oder Flugasche. Das hochalkalische Milieu löst sie partiell und leitet eine Reaktion mit dem Calciumhydroxyd (CH) zu CSH ohne zusätzliche Wasseraufnahme ein:
- 2SiO2 + 3Ca(OH)2 → 3CaO + 2SiO2 + 3H2O
oder kurz:
- S + CH → CSH. ⓘ
Vor allem bei der Entwicklung und Herstellung von hochfestem- und ultrahochfestem Beton hat dies eine große Bedeutung. ⓘ
Poren im Beton
Neben der Festigkeit ist die Porosität des Betons ein wichtiges Qualitätskriterium. Die verschiedenen Arten von Poren unterscheiden sich voneinander teilweise stark in Entstehung und Auswirkung. Grundsätzlich sinkt mit steigender Kapillar-, Luft- und Verdichtungsporosität die Festigkeit proportional. Auch eine Verringerung des Elastizitätsmodul ist nachweisbar. ⓘ
Man unterscheidet folgende Arten von Poren:
- Gelporen (Ø ca. 0,1–10 nm)
- Das physikalisch gebundene Anmachwasser, welches als Gelwasser bezeichnet wird, ist in Gelporen gespeichert. Da immer der gleiche Anteil Wasser in Gelwasser umgewandelt wird, lässt sich ihre Entstehung nicht vermeiden.
- Schrumpfporen (Ø ca. 10 nm)
- Da die Reaktionsprodukte der Hydratation ein kleineres Volumen als die Ausgangsstoffe haben, kommt es zu Schrumpfvorgängen. Es bilden sich Schrumpfporen. Ihre Entstehung kann ebenfalls nicht vermieden werden.
- Kapillarporen (Ø 10 nm – 100 µm)
- Bei w/z-Werten > 0,42 bleibt für die Hydratation nicht benötigtes Wasser im Beton zurück, welches mit der Zeit austrocknet und Kapillarporen hinterlässt. Diese sind verantwortlich für Transportprozesse und beeinflussen stark die Festigkeit und den E-Modul des Werkstoffs. Ihr Gesamtvolumen ist durch die Wahl eines günstigen w/z-Werts steuerbar.
- Luftporen (Ø 1 µm – 1 mm)
- Durch den Mischvorgang gelangt Luft in das Zementgel, welche Luftporen bildet. Sie stellen einen Ausweichraum für gefrierendes Wasser dar und erhöhen somit die Frostbeständigkeit des Betons. Eine gezielte Beeinflussung des Anteils an Luftporen ist durch Luftporenbildner möglich.
- Verdichtungsporen (Ø > 1 mm)
- Verdichtungsporen haben ihre Ursache in unzureichender Verdichtung des Betons nach dem Einbau. Aufgrund ihrer Größe können sie die Festigkeit des Werkstoffs deutlich beeinflussen. An Sichtbetonoberflächen sind Verdichtungsporen überdies unerwünscht – optisch, haptisch und weil sich Schmutz in den offenstehenden Poren einlagert. ⓘ
Bauphysikalische Eigenschaften
Für Beton kann eine Wasserdampfdiffusionswiderstandszahl zwischen 70 (feucht) und 150 (trocken) angesetzt werden. Die Wärmeleitfähigkeit beträgt etwa 2,1 W/(m·K) für Normalbeton, die spezifische Wärmekapazität 1000 J/(kg·K). Beide Werte sind jedoch stark vom Zuschlagstoff abhängig. Der Wärmeausdehnungskoeffizient beträgt nach den Stahlbetonnormen 10−5/K (z. B. DIN 1045-1:2001-07). Allerdings kann dieser je nach Art des Betonzuschlags, Zementgehalt sowie Feuchtezustand des Betons zwischen 6 und 14 · 10−6/K variieren. Der Feuchtegehalt beträgt bei 23 °C und 50 % relativer Luftfeuchtigkeit 25 Liter Wasser je Kubikmeter Beton und bei 80 % relativer Luftfeuchtigkeit 40 l/m³. Alle diese Betoneigenschaften sind außerdem erheblich temperaturabhängig und gelten näherungsweise nur deutlich unterhalb 100 °C. ⓘ
Arbeitsvermögen
Die mögliche Energieaufnahme eines Betonbauteils bis zum Versagen wird als Arbeitsvermögen bezeichnet. Der Graph des Spannungs-Dehnungs-Diagramms wird bei Beton auch Arbeitslinie genannt. Das Arbeitsvermögen ist als die Fläche unter der Arbeitslinie definiert und umfasst damit alle elastischen und irreversiblen Verformungsanteile. ⓘ
Überwachungsklassen
Für die Überprüfung der maßgebenden Frisch- und Festbetoneigenschaften wird der Beton in drei Überwachungsklassen eingeteilt. Daraus ergibt sich der Umfang und die Häufigkeit der Prüfungen, was in DIN 1045-3 geregelt ist. Beton der Überwachungsklassen 1, 2 und 3 ist u. a. durch Eigenüberwachung der ausführenden Firma und eine anerkannte Überwachungsstelle zu überprüfen. Wobei die Prüfungen in der Überwachungsklasse 1 nur der Selbstkontrolle der ausführenden Firma dient. Die Überwachungsklasse 2 wird bei Betonen mit erhöhten Anforderungen wie z. B. WU-, Spann-, Unterwasser- und Strahlenschutzbeton usw. angewandt. Geprüft wird mit mindestens drei Probekörpern jeden 3. Betoniertag oder alle 300 m³. In der Überwachungsklasse 3 erfolgt die Prüfung mindestens jeden Betoniertag oder alle 50 m³. ⓘ
Betonsorten
Unter einer Betonsorte versteht man eine genau definierte Mischung, die immer wieder, entsprechend einer Betonrezeptur, hergestellt wird. Lieferwerke haben meist eigene Sorten, die von Kunden bestellt werden. Bei großen Bauvorhaben stellen oft auch die Bauunternehmen in Absprache mit dem Bauherrn und den Lieferwerken eigene Betonsorten in einem Sortenverzeichnis zusammen. Diese Betone sind dann für eine Baustelle und deren Besonderheiten „maßgeschneidert“. ⓘ
Betonarten
Alle Betone lassen sich entsprechend ihrer Herstellung, ihrer Einbauart oder ihrer besonderen Eigenschaften unterscheiden. Dabei gehört ein Beton nicht zwangsläufig nur einer Art an. Ein und dasselbe Produkt wird meist mehreren Kategorien zugeordnet. Beispielsweise ist jeder Beton entweder ein Transport- oder ein Baustellenbeton. Abhängig von den Eigenschaften sind diese Betone dann z. B. Luftporenbetone, hochfeste Betone usw. Die verwendeten Bezeichnungen der gebräuchlichen Betone sind in der Liste gebräuchlicher Betone aufgeführt. ⓘ
Dauerhaftigkeit, Schädigungen und Instandsetzung

Für dauerhafte Betonbauwerke müssen die verlangten Gebrauchseigenschaften und die Standsicherheit unter den planmäßigen Beanspruchungen über die erwartete Nutzungsdauer bei normalem Unterhaltsaufwand konstant sein. Wichtig sind für eine ausreichende Dauerhaftigkeit des Betons die Betonzusammensetzung (Wasserzementwert und Zementgehalt), die Festigkeitsklasse, die Verdichtung und die Nachbehandlung des Betons. ⓘ
Beton ist ein chemisch instabiler Baustoff. Verschiedene innere und äußere Einflüsse können die Beständigkeit von Beton nachhaltig beeinflussen. Durch die typische Anwendung von Beton im Verbund mit Bewehrung aus Stahl ergeben sich weitere die Dauerhaftigkeit von Beton beeinflussende Faktoren, wie zu geringe Überdeckung des Bewehrungstahles durch Beton. Daher erfolgt mit den Expositionsklassen eine Klassifizierung der chemischen und physikalischen Umgebungsbedingungen, denen der Beton ausgesetzt ist, woraus die Anforderungen an die Zusammensetzung des zu verwendenden Betons sowie bei Stahlbeton die Mindestbetondeckung folgen. ⓘ
Folgende Schädigungsmechanismen können auftreten:
- Bewehrungskorrosion aufgrund von Carbonatisierung des Betons
- Lochfraßkorrosion der Bewehrung durch eingetragene Chloride
- Betonkorrosion infolge von:
- Sulfattreiben
- Alkali-Kieselsäure-Reaktion
- Kalktreiben
- Frost-Tau-Wechsel ⓘ
Oberflächenschutzsysteme, wie Anstriche oder die Imprägnierung der Betonoberflächen mit einem Hydrophobierungsmittel, dienen der Verbesserung der Dauerhaftigkeit und können sowohl direkt nach der Herstellung aufgebracht werden oder im Zuge einer Betoninstandsetzung eine Maßnahme zur Lebensdauerverlängerung darstellen. ⓘ
Zur Betoninstandsetzung zählen zudem alle Maßnahmen, bei denen Schäden (Risse, Abplatzungen usw.) behoben und die ursprünglichen Schutzeigenschaften des Betons möglichst wiederhergestellt oder verbessert werden. Die Instandsetzungsmaßnahmen werden von spezialisierten Betoninstandsetzern durchgeführt. ⓘ
Im Brückenbau, besonders bei Autobahnbrücken, wird der kathodische Korrosionsschutz (KKS) mittels Fremdstromanode durchgeführt. Dazu wird ein Anodengitter aus beschichtetem Titan auf die zu schützende Oberfläche aufgebracht und mit Spritzbeton circa 2 cm bis 3 cm eingespritzt. Der Spritzbeton dient dabei als Elektrolyt. Der Strom wird über Gleichrichter in die Bewehrung eingeleitet und so der kathodische Schutz erreicht. Die Maßnahme wird mit einem automatischen Überwachungssystem laufend überprüft. ⓘ
KKS-Felder der Lieserschluchtbrücke ⓘ
Eine gute Erklärung über den KKS geben diese beiden Präsentationen:
- Kathodischer Korrosionsschutz allgemein a-bau.co.at (PDF; 55 KB)
- Kathodischer Korrosionsschutz im Brückenbau a-bau.co.at (PDF; 2,4 MB) ⓘ
Einbauteile
Zur Reduzierung des Eigengewichtes von Betonteilen werden unter anderem sogenannte Verdrängungskörper eingebaut. Dies bewirkt, dass Hohlräume entstehen und weniger Beton notwendig ist. Häufig wird das bei Plattenkonstruktionen angewendet. ⓘ
Früher wurden hierfür Teile aus Polystyrolschaum und anderen Schaumstoffen genutzt, die heute wegen nachteiliger Auswirkungen bei Bränden nicht mehr gestattet sind. Derzeit werden Kugeln oder würfelförmige Elemente aus Polyethylen oder Polypropylen eingesetzt, wodurch bis zu einem Drittel des Betons und folglich des Eigengewichtes eingespart werden kann. So sind große Bauteile, z. B. Dachkonstruktionen, mit Stützweiten von bis zu 19 Metern möglich. ⓘ
Aufgrund von größeren Bauschäden aus der Vergangenheit ist in Deutschland der Einbau von Verdrängungskörpern bei Brückenbauten nicht mehr zulässig. ⓘ
Vorgefertigte Betonprodukte
- Betonwerkstein
- Betonpflasterstein
- Betonplatte ⓘ
Andere als „Beton“ bezeichnete Werkstoffe
Die Bezeichnung „Beton“ wird auch in Zusammenhang mit anderen Baustoffen verwendet und soll deren hohe Festigkeit oder deren Zusammensetzungsprinzip beschreiben. ⓘ
Porenbeton
Porenbeton (früher Gasbeton) ist ein mineralischer Werkstoff, welcher durch chemisches Aufschäumen einer Mörtelmischung erzeugt wird. Die alkalische Mörtelsuspension reagiert unter Bildung von Gas mit Pulvern unedler Metalle wie z. B. Aluminium. Porenbeton enthält so gut wie keine Zuschläge. Porenbeton besitzt im Vergleich zu konventionellem Beton wegen seiner geringen Rohdichte eine geringe Festigkeit und eine geringe Wärmeleitfähigkeit. ⓘ
Faserbeton
Faserbeton ist eine Erweiterung des künstlichen Baustoffes Beton. Es werden dem Beton bei der Herstellung Fasern zugegeben um die Materialeigenschaften wie Zug-, Druck- und Scherfestigkeit sowie das Bruch- und Rissverhalten zu verbessern. Damit kann der Faserbeton im Gegensatz zu Beton besser Zugkräfte übernehmen. Dies führt unter anderem zu der Möglichkeit jegliche Körperform statisch tragend herzustellen. ⓘ
Betonglas
Betonglas ist ein Glasbaustein, der waagerecht angeordnet wird und hohe Druckfestigkeit aufweist. ⓘ
Mineralbeton
Mineralbeton ist eine Bezeichnung für ein hochverdichtetes Mineralstoffgemisch, meist unter Verwendung eines hohen Anteils gebrochenen Korns. Die Sieblinie ist gemäß der Fuller-Parabel aufzubauen, es ist der für die Verdichtung optimale Wassergehalt einzustellen. Beim Einbau sind Entmischungen zu vermeiden. Mineralbeton wird ohne Bindemittel zu einem hochstandfesten Baustoff, der etwa in Straßendecken verwendet wird. Gängiges Produkt ist die korngestufte Schottertragschicht mit 0 bis 32 mm als Frostschutzmaterial gemäß ZTV T-StB 95. ⓘ
Kunstharzbeton
Kunstharzbeton nutzt – genauso wie Kunstharzmörtel – ungesättigtes Polyesterharz, Methacrylatharz oder Epoxidharz als Bindemittel. Zement wird für die Festigkeit nicht benötigt. Hier kommen Härter und Beschleuniger in geringen Mengen zum Einsatz. Das Prinzip, Anwendungsbereiche und Verarbeitung sind allerdings typisch für Beton. Aufgrund der schnellen Aushärtung eignet sich der Beton gut für Ausbesserungen. Im Vergleich zu zementgebundenem Beton ergibt sich eine deutlich höhere Zugfestigkeit und ein kleiner Elastizitätsmodul. ⓘ
Erscheinungsbild
Beton dessen Oberfläche nach Fertigstellung des Bauwerks noch sichtbar ist, wird allgemein als Sichtbeton bezeichnet. Im engeren Sinne bezeichnet Sichtbeton Betonoberflächen mit besonderer gestalterischer Qualität. ⓘ
Im Architekturstil des Brutalismus wurde demgegenüber gerade der rohe, unverfeinerte Beton als gestalterisches Mittel eingesetzt. Die Bauwerke des Brutalismus beeindrucken eher durch ihre Grobstruktur, d. h. durch ihre Kubatur, als durch die Oberflächenqualität. ⓘ
Architekturbeton
Der Begriff Architekturbeton wird gelegentlich von spezialisierten Anbietern des Baugewerbes verwendet, um Sichtbeton zu bezeichnen, an den besonders hohe gestalterische Anforderungen hinsichtlich Oberflächenstruktur und -qualität gestellt werden. ⓘ
Durchgefärbter Beton
Durchgefärbter Beton enthält Pigmente, die seine Farbe verändern. ⓘ
Verwandte Themen
- Biorock-Technologie, künstliche Korallenriffe aus betonähnlichem Werkstoff im Meer
- Brutalismus, ein Architekturstil mit Sichtbeton
- Ökologische Bedenken zum Bindemittel Zement, siehe Umweltschutzaspekte ⓘ