Wärmekraftwerk



Ein Wärmekraftwerk ist eine Art von Kraftwerk, in dem Wärmeenergie in elektrische Energie umgewandelt wird. In einem Dampferzeugungskreislauf wird die Wärme genutzt, um Wasser in einem großen Druckbehälter zu kochen und Hochdruckdampf zu erzeugen, der eine Dampfturbine antreibt, die mit einem elektrischen Generator verbunden ist. Die Niederdruckabgase der Turbine gelangen in einen Dampfkondensator, wo sie abgekühlt werden, um heißes Kondensat zu erzeugen, das in den Heizprozess zurückgeführt wird, um weiteren Hochdruckdampf zu erzeugen. Dies wird als Rankine-Kreislauf bezeichnet. ⓘ
Die Bauweise von Wärmekraftwerken hängt von der vorgesehenen Energiequelle ab: Fossile Brennstoffe, Kernkraft und Erdwärme, Solarenergie, Biobrennstoffe und Müllverbrennung werden alle genutzt. Bestimmte Wärmekraftwerke sind neben der Stromerzeugung auch für die Erzeugung von Wärme für industrielle Zwecke, für Fernwärme oder für die Entsalzung von Wasser ausgelegt. ⓘ
Erdgas oder Erdöl können auch direkt in einer Gasturbine verbrannt werden, die mit einem Stromgenerator verbunden ist. Zur Verbesserung des Wirkungsgrads werden die heißen Abgase dann verwendet, um Wasser zu kochen und mehr Dampf für den Einsatz in einem Dampferzeugungskreislauf zu erzeugen. Dies wird als Gas- und Dampfturbinenkraftwerk bezeichnet. ⓘ
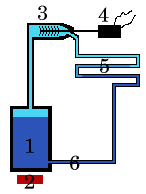
1:Dampfkessel
2: Hitzequelle
3: Dampfturbine
4: Generator
5: Kondensator / Kühlung
6: Verbindende Rohrleitung ⓘ
Viele Wärmekraftwerke sind Dampfkraftwerke. Es gibt allerdings auch Kraftwerke, die keine Dampfturbinen oder nicht einmal einen Wasserkreislauf aufweisen, wie beispielsweise historische Kraftwerke mit Dampfmaschinen oder moderne Diesel-/Gasmotor- oder Gasturbinenkraftwerke. Ein gemeinsames Kennzeichen von heutigen Wärmekraftwerken sind die thermodynamischen Kreisläufe des Arbeitsmittels, die beim Dampfkraftwerk geschlossen und beim Gaskraftwerk offen sind. ⓘ
Arten von Wärmeenergie
Fast alle Kohlekraftwerke, Erdöl-, Kernkraft-, Geothermie-, Solarthermie- und Müllverbrennungsanlagen sowie alle Erdgaskraftwerke sind Wärmekraftwerke. Erdgas wird häufig sowohl in Gasturbinen als auch in Heizkesseln verbrannt. Die Abwärme einer Gasturbine in Form von heißem Abgas kann zur Dampferzeugung genutzt werden, indem dieses Gas durch einen Abhitzedampferzeuger (HRSG) geleitet wird. Der Dampf wird dann zum Antrieb einer Dampfturbine in einem Kombikraftwerk verwendet, was den Gesamtwirkungsgrad verbessert. Kraftwerke, die mit Kohle, Heizöl oder Erdgas befeuert werden, werden oft als Kraftwerke für fossile Brennstoffe bezeichnet. Auch einige mit Biomasse befeuerte Wärmekraftwerke gibt es inzwischen. Nichtnukleare Wärmekraftwerke, insbesondere mit fossilen Brennstoffen betriebene Anlagen, die keine Kraft-Wärme-Kopplung nutzen, werden manchmal als konventionelle Kraftwerke bezeichnet. ⓘ
Kommerzielle Stromversorgungskraftwerke werden in der Regel in großem Maßstab gebaut und sind für den Dauerbetrieb ausgelegt. Praktisch alle Elektrizitätswerke verwenden Drehstromgeneratoren zur Erzeugung von Wechselstrom mit einer Frequenz von 50 Hz oder 60 Hz. Große Unternehmen oder Institutionen können über eigene Kraftwerke verfügen, um ihre Einrichtungen mit Wärme oder Strom zu versorgen, insbesondere wenn ohnehin Dampf für andere Zwecke erzeugt wird. Die meisten Schiffe wurden im 20. Jahrhundert mit Dampfkraftwerken angetrieben. Schiffskraftwerke koppeln die Turbine in der Regel über Getriebe direkt mit den Schiffsschrauben. Kraftwerke in solchen Schiffen liefern auch Dampf für kleinere Turbinen, die elektrische Generatoren zur Stromversorgung antreiben. Nukleare Schiffsantriebe werden, von wenigen Ausnahmen abgesehen, nur in Marineschiffen eingesetzt. Es gibt viele turbo-elektrische Schiffe, bei denen eine dampfgetriebene Turbine einen elektrischen Generator antreibt, der wiederum einen Elektromotor für den Antrieb versorgt. ⓘ
Kraft-Wärme-Kopplungs-Anlagen (KWK-Anlagen) erzeugen sowohl elektrischen Strom als auch Wärme für Prozesswärme oder Raumheizung, z. B. Dampf und Heißwasser. ⓘ
Geschichte

Die Kolben-Dampfmaschine wird seit dem 18. Jahrhundert zur Erzeugung mechanischer Energie eingesetzt, wobei James Watt wesentliche Verbesserungen vornahm. Als 1882 in der Pearl Street Station in New York und im Holborn-Viaduct-Kraftwerk in London die ersten kommerziell entwickelten zentralen Elektrizitätswerke errichtet wurden, kamen Dampfmaschinen mit Kolbenantrieb zum Einsatz. Die Entwicklung der Dampfturbine im Jahr 1884 ermöglichte größere und effizientere Maschinenkonstruktionen für zentrale Kraftwerke. Bis 1892 wurde die Turbine als bessere Alternative zu Kolbenmaschinen angesehen; Turbinen boten höhere Drehzahlen, kompaktere Maschinen und eine stabile Drehzahlregelung, die den parallelen Synchronbetrieb von Generatoren an einer gemeinsamen Sammelschiene ermöglichte. Ab etwa 1905 ersetzten die Turbinen die Kolbenmotoren in fast allen großen zentralen Kraftwerken vollständig. ⓘ
Die größten jemals gebauten Kolbenmotor-Generator-Gruppen wurden 1901 für die Manhattan Elevated Railway fertiggestellt. Jedes der siebzehn Aggregate wog etwa 500 Tonnen und hatte eine Leistung von 6000 Kilowatt; ein zeitgenössisches Turbinenaggregat mit ähnlicher Leistung hätte etwa 20 % so viel gewogen. ⓘ
Wirkungsgrad der thermischen Stromerzeugung

Der Energiewirkungsgrad eines konventionellen Wärmekraftwerks ist definiert als die erzeugte verkaufbare Energie in Prozent des Heizwerts des verbrauchten Brennstoffs. Eine Gasturbine mit einfachem Zyklus erreicht einen Wirkungsgrad von 20 bis 35 % bei der Energieumwandlung. Typische kohlebasierte Kraftwerke, die mit einem Dampfdruck von 170 bar und 570 °C arbeiten, haben einen Wirkungsgrad von 35 bis 38 %, während moderne fossile Kraftwerke einen Wirkungsgrad von 46 % erreichen. Kombikraftwerke können höhere Werte erreichen. Wie bei allen Wärmekraftmaschinen ist ihr Wirkungsgrad begrenzt und wird durch die Gesetze der Thermodynamik bestimmt. ⓘ
Der Carnot-Wirkungsgrad besagt, dass höhere Wirkungsgrade durch eine Erhöhung der Dampftemperatur erreicht werden können. Kraftwerke für fossile Brennstoffe mit unterkritischem Druck können einen Wirkungsgrad von 36-40 % erreichen. Überkritische Kraftwerke haben Wirkungsgrade im unteren bis mittleren 40 %-Bereich, wobei neue "ultrakritische" Kraftwerke mit einem Druck von über 30,3 MPa (4400 psi) und mehrstufiger Zwischenüberhitzung einen Wirkungsgrad von 45-48 % erreichen. Oberhalb des kritischen Punkts für Wasser von 374 °C (705 °F) und 22,06 MPa (3212 psi) gibt es keinen Phasenübergang von Wasser zu Dampf, sondern nur eine allmähliche Abnahme der Dichte. ⓘ
Gegenwärtig müssen die meisten Kernkraftwerke unterhalb der Temperaturen und Drücke betrieben werden, die in Kohlekraftwerken herrschen, um konservativere Sicherheitsspannen in den Systemen zu gewährleisten, die dem Kernbrennstoff Wärme entziehen. Dies wiederum begrenzt ihren thermodynamischen Wirkungsgrad auf 30-32 %. Einige der untersuchten fortschrittlichen Reaktorkonzepte, wie der Hochtemperaturreaktor, der fortschrittliche gasgekühlte Reaktor und der überkritische Wasserreaktor, würden bei ähnlichen Temperaturen und Drücken wie die derzeitigen Kohlekraftwerke arbeiten und einen vergleichbaren thermodynamischen Wirkungsgrad aufweisen. ⓘ
Die Energie eines Wärmekraftwerks, die nicht zur Stromerzeugung genutzt wird, muss die Anlage in Form von Wärme an die Umwelt abgeben. Diese Abwärme kann durch einen Kondensator geleitet und mit Kühlwasser oder in Kühltürmen entsorgt werden. Wird die Abwärme stattdessen für Fernwärme genutzt, spricht man von Kraft-Wärme-Kopplung. Eine wichtige Klasse von Wärmekraftwerken sind Entsalzungsanlagen, die typischerweise in Wüstenländern mit großen Erdgasvorkommen zu finden sind und in denen die Erzeugung von Süßwasser und Strom gleichermaßen wichtige Nebenprodukte sind. ⓘ
Für andere Kraftwerkstypen gelten andere Effizienzgrenzen. Die meisten Wasserkraftwerke in den Vereinigten Staaten haben einen Wirkungsgrad von etwa 90 % bei der Umwandlung der Energie des fallenden Wassers in Elektrizität, während der Wirkungsgrad einer Windturbine durch das Betz'sche Gesetz auf etwa 59,3 % begrenzt ist und die tatsächlichen Windturbinen einen geringeren Wirkungsgrad aufweisen. ⓘ
Kosten der Elektrizität
Die direkten Kosten der von einem Wärmekraftwerk erzeugten elektrischen Energie ergeben sich aus den Brennstoffkosten, den Kapitalkosten für die Anlage, den Arbeitskosten des Betreibers, der Wartung und Faktoren wie Aschebehandlung und -entsorgung. Indirekte soziale oder ökologische Kosten, wie z. B. der wirtschaftliche Wert der Umweltauswirkungen oder die Umwelt- und Gesundheitsauswirkungen des gesamten Brennstoffkreislaufs und der Anlagenstilllegung, werden in der Praxis der Versorgungsunternehmen in der Regel nicht den Erzeugungskosten für Wärmekraftwerke zugerechnet, können aber Teil einer Umweltverträglichkeitsprüfung sein. Diese indirekten Kosten gehören zu dem weiter gefassten Konzept der externen Effekte. ⓘ
Kessel und Dampfkreislauf

Im Bereich der Kernkraftwerke bezieht sich der Begriff Dampferzeuger auf einen bestimmten Typ großer Wärmetauscher, der in einem Druckwasserreaktor (DWR) verwendet wird, um das Primärsystem (Reaktoranlage) und das Sekundärsystem (Dampfanlage) thermisch zu verbinden, wodurch Dampf erzeugt wird. In einem Siedewasserreaktor (SWR) wird kein separater Dampferzeuger verwendet und das Wasser kocht im Reaktorkern. ⓘ
In einigen Industrieanlagen können auch dampfproduzierende Wärmetauscher, so genannte Abhitzedampferzeuger (HRSG), eingesetzt werden, die die Wärme aus einem industriellen Prozess nutzen, in den meisten Fällen aus den heißen Abgasen einer Gasturbine. Der dampferzeugende Kessel muss Dampf mit der hohen Reinheit, dem hohen Druck und der hohen Temperatur erzeugen, die für die Dampfturbine erforderlich sind, die den Stromgenerator antreibt. ⓘ
Geothermische Anlagen benötigen keine Kessel, da sie natürlich vorkommende Dampfquellen nutzen. Wärmetauscher können eingesetzt werden, wenn der geothermische Dampf sehr korrosiv ist oder zu viele Schwebstoffe enthält. ⓘ
Ein Dampferzeuger für fossile Brennstoffe besteht aus einem Economizer, einer Dampftrommel und der Feuerung mit ihren Dampferzeugungsrohren und Überhitzerschlangen. Zum Schutz vor übermäßigem Kesseldruck sind an geeigneten Stellen die erforderlichen Sicherheitsventile angebracht. Zur Luft- und Rauchgasführung gehören: Gebläse (FD), Luftvorwärmer (AP), Kesselfeuerung, Saugzuggebläse (ID), Flugascheabscheider (Elektrofilter oder Baghouse) und der Rauchgaskamin. ⓘ
Speisewassererwärmung
Das im Dampfkessel verwendete Kesselspeisewasser ist ein Mittel zur Übertragung der Wärmeenergie aus dem verbrennenden Brennstoff auf die mechanische Energie der sich drehenden Dampfturbine. Das gesamte Speisewasser besteht aus rezirkuliertem Kondensatwasser und gereinigtem Zusatzwasser. Da die metallischen Werkstoffe, mit denen es in Berührung kommt, bei hohen Temperaturen und Drücken der Korrosion ausgesetzt sind, wird das Zusatzwasser vor der Verwendung stark gereinigt. Ein System von Wasserenthärtern und Ionenaustauschern sorgt für so reines Wasser, dass es gleichzeitig ein elektrischer Isolator mit einer Leitfähigkeit im Bereich von 0,3-1,0 Mikrosiemens pro Zentimeter ist. Das Speisewasser in einem 500-MWe-Kraftwerk beträgt vielleicht 120 US-Gallonen pro Minute (7,6 l/s), um das Wasser zu ersetzen, das aus den Kesseltrommeln für das Reinheitsmanagement entnommen wird, und auch um die geringen Verluste durch Dampflecks im System auszugleichen. ⓘ
Der Speisewasserkreislauf beginnt damit, dass Kondensatwasser aus dem Kondensator gepumpt wird, nachdem es die Dampfturbinen durchlaufen hat. Der Kondensatdurchsatz bei Volllast in einem 500-MW-Kraftwerk beträgt etwa 6.000 US-Gallonen pro Minute (400 L/s). ⓘ

Das Wasser wird in zwei Stufen unter Druck gesetzt und fließt durch eine Reihe von sechs oder sieben Speisewasser-Zwischenerhitzern, die an jedem Punkt mit Dampf aufgeheizt werden, der aus einer entsprechenden Leitung an den Turbinen entnommen wird und in jeder Stufe an Temperatur gewinnt. In der Mitte dieser Reihe von Speisewassererhitzern und vor der zweiten Stufe der Druckbeaufschlagung fließt das Kondensat zusammen mit dem Zusatzwasser in der Regel durch einen Entgaser, der das Wasser von gelöster Luft befreit und damit weiter reinigt und seine Korrosivität verringert. Nach diesem Schritt kann das Wasser mit Hydrazin dosiert werden, einer Chemikalie, die den Restsauerstoff im Wasser auf unter 5 ppb (parts per billion) reduziert. Außerdem wird es mit pH-Kontrollmitteln wie Ammoniak oder Morpholin versetzt, um den Restsäuregehalt niedrig und damit nicht korrosiv zu halten. ⓘ
Betrieb des Kessels
Der Kessel ist eine rechteckige Feuerung mit einer Seitenlänge von etwa 15 m (50 Fuß) und einer Höhe von 40 m (130 Fuß). Seine Wände bestehen aus einem Geflecht von Hochdruckstahlrohren mit einem Durchmesser von etwa 58 mm (2,3 Zoll). ⓘ
Der Brennstoff, z. B. Kohlenstaub, wird durch Brenner an den vier Ecken, an einer Wand oder an zwei gegenüberliegenden Wänden in den Ofen geblasen und entzündet sich schnell, so dass sich in der Mitte ein großer Feuerball bildet. Die Wärmestrahlung des Feuerballs erwärmt das Wasser, das durch die Kesselrohre in der Nähe des Kesselrands zirkuliert. Die Wasserzirkulationsrate im Kessel beträgt das Drei- bis Vierfache des Durchsatzes. Während das Wasser im Kessel zirkuliert, nimmt es Wärme auf und verwandelt sich in Dampf. Dieser wird in einer Trommel am oberen Ende des Ofens vom Wasser getrennt. Der gesättigte Dampf wird in Überhitzungspendelrohre geleitet, die im heißesten Teil der Verbrennungsgase hängen, wenn diese den Ofen verlassen. Hier wird der Dampf auf 1.000 °F (540 °C) überhitzt, um ihn für die Turbine vorzubereiten. ⓘ
In Anlagen, die Gasturbinen einsetzen, um das Wasser für die Umwandlung in Dampf zu erhitzen, kommen Kessel zum Einsatz, die als Abhitzedampferzeuger (HRSG) bezeichnet werden. Die Abwärme der Gasturbinen wird zur Erzeugung von überhitztem Dampf genutzt, der dann in einem konventionellen Wasser-Dampf-Erzeugungskreislauf verwendet wird, wie im Abschnitt über Gasturbinen-Kombikraftwerke beschrieben. ⓘ
Kesselfeuerung und Dampftrommel
Das Wasser tritt in den Kessel durch einen Abschnitt im Konvektionszug ein, der Economizer genannt wird. Vom Economizer gelangt es in die Dampftrommel und von dort über Fallrohre zu Einlasssammlern am Boden der Wasserwände. Von diesen Sammlern steigt das Wasser durch die Wasserwände des Ofens, wo ein Teil des Wassers in Dampf umgewandelt wird, und das Wasser-Dampf-Gemisch tritt dann wieder in die Dampftrommel ein. Dieser Prozess kann durch natürliche Zirkulation (da das Wasser in den Fallrohren dichter ist als das Wasser-Dampf-Gemisch in den Wasserwänden) oder mit Hilfe von Pumpen erfolgen. In der Dampftrommel wird das Wasser in die Fallrohre zurückgeführt, und der Dampf wird durch eine Reihe von Dampfabscheidern und Trocknern geleitet, die Wassertröpfchen aus dem Dampf entfernen. Der trockene Dampf strömt dann in die Überhitzerschlangen. ⓘ
Zu den Hilfseinrichtungen des Kesselofens gehören Kohlezufuhrdüsen und Zündpistolen, Rußbläser, Wasserlanzen und Beobachtungsöffnungen (in den Feuerraumwänden) zur Beobachtung des Feuerraumes. Ofenexplosionen aufgrund von Ansammlungen brennbarer Gase nach einer Auslösung werden vermieden, indem solche Gase vor dem Anzünden der Kohle aus der Verbrennungszone gespült werden. ⓘ
Die Dampftrommel (sowie die Überhitzerschlangen und -sammler) sind mit Entlüftungs- und Entleerungsöffnungen versehen, die für die Erstinbetriebnahme erforderlich sind. ⓘ
Überhitzer
Kraftwerke, die mit fossilen Brennstoffen betrieben werden, verfügen häufig über einen Überhitzer in der Dampferzeugungsfeuerung. Der Dampf gelangt über die Trocknungsanlage in der Dampftrommel in den Überhitzer, eine Reihe von Rohren im Feuerraum. Hier nimmt der Dampf mehr Energie aus den heißen Rauchgasen außerhalb der Rohre auf, und seine Temperatur ist nun über die Sättigungstemperatur hinaus überhitzt. Der überhitzte Dampf wird dann durch die Hauptdampfleitungen zu den Ventilen vor der Hochdruckturbine geleitet. ⓘ
Kernkraftwerke verfügen nicht über solche Abschnitte, sondern erzeugen Dampf im Wesentlichen in gesättigtem Zustand. Experimentelle Kernkraftwerke wurden mit fossil befeuerten Überhitzern ausgestattet, um die Gesamtbetriebskosten der Anlage zu verbessern. ⓘ
Dampfkondensation
Der Kondensator kondensiert den Dampf aus dem Abgas der Turbine zu einer Flüssigkeit, damit er gepumpt werden kann. Wenn der Kondensator gekühlt werden kann, wird der Druck des Abdampfes verringert und der Wirkungsgrad des Kreislaufs erhöht. ⓘ

Der Oberflächenkondensator ist ein Rohrbündelwärmetauscher, in dem Kühlwasser durch die Rohre zirkuliert. Der Abdampf aus der Niederdruckturbine tritt in den Mantel ein, wo er abgekühlt und in Kondensat (Wasser) umgewandelt wird, indem er über die Rohre fließt, wie in der nebenstehenden Abbildung dargestellt. In solchen Kondensatoren werden Dampfstrahler oder rotierende, motorgetriebene Auspuffanlagen eingesetzt, um Luft und Gase kontinuierlich von der Dampfseite zu entfernen und das Vakuum aufrechtzuerhalten. ⓘ
Um einen optimalen Wirkungsgrad zu erzielen, muss die Temperatur im Kondensator so niedrig wie möglich gehalten werden, um einen möglichst niedrigen Druck im kondensierenden Dampf zu erreichen. Da die Kondensatortemperatur fast immer deutlich unter 100 °C gehalten werden kann, wo der Dampfdruck des Wassers viel geringer ist als der atmosphärische Druck, arbeitet der Kondensator im Allgemeinen unter Vakuum. Daher müssen Leckagen von nicht kondensierbarer Luft in den geschlossenen Kreislauf verhindert werden. ⓘ
Normalerweise kondensiert der Dampf durch das Kühlwasser bei einer Temperatur von etwa 25 °C (77 °F), wodurch im Kondensator ein absoluter Druck von etwa 2-7 kPa (0,59-2,07 inHg) entsteht, d. h. ein Vakuum von etwa -95 kPa (-28 inHg) relativ zum Atmosphärendruck. Die starke Volumenverringerung, die bei der Kondensation von Wasserdampf zu Flüssigkeit auftritt, erzeugt das niedrige Vakuum, das dazu beiträgt, den Dampf durchzuziehen und den Wirkungsgrad der Turbinen zu erhöhen. ⓘ
Der begrenzende Faktor ist die Temperatur des Kühlwassers, die wiederum durch die vorherrschenden durchschnittlichen klimatischen Bedingungen am Standort des Kraftwerks begrenzt wird (es kann möglich sein, dass die Temperatur im Winter über die Grenzen der Turbine hinaus abgesenkt wird, was zu übermäßiger Kondensation in der Turbine führt). Kraftwerke, die in heißen Klimazonen betrieben werden, müssen unter Umständen ihre Leistung reduzieren, wenn sich die Kühlwasserquelle des Kondensators erwärmt; leider fällt dies in der Regel mit Zeiten hohen Strombedarfs für Klimaanlagen zusammen. ⓘ
Der Kondensator verwendet im Allgemeinen entweder zirkulierendes Kühlwasser aus einem Kühlturm, um die Abwärme an die Atmosphäre abzugeben, oder Durchlaufkühlwasser aus einem Fluss, See oder Meer. In den Vereinigten Staaten verwenden etwa zwei Drittel der Kraftwerke OTC-Systeme, die oft erhebliche negative Umweltauswirkungen haben. Zu den Auswirkungen gehören die thermische Verschmutzung und die Tötung einer großen Anzahl von Fischen und anderen Wasserlebewesen an den Kühlwassereinlässen. ⓘ

Die vom zirkulierenden Kühlwasser in den Kondensatorrohren aufgenommene Wärme muss ebenfalls abgeführt werden, um die Fähigkeit des Wassers zur Kühlung aufrechtzuerhalten, während es zirkuliert. Dazu wird das warme Wasser aus dem Kondensator entweder durch Naturzug-, Zwangszug- oder Saugzugkühltürme (wie im nebenstehenden Bild zu sehen) gepumpt, die die Temperatur des Wassers durch Verdunstung um etwa 11 bis 17 °C (20 bis 30 °F) senken und die Abwärme an die Atmosphäre abgeben. Die Durchflussmenge des Kühlwassers in einem 500-MW-Block beträgt bei Volllast etwa 14,2 m3/s (500 ft3/s oder 225.000 US gal/min). ⓘ
Die Kondensatorrohre sind aus Messing oder Edelstahl gefertigt, um der Korrosion von beiden Seiten zu widerstehen. Dennoch können sie während des Betriebs durch Bakterien oder Algen im Kühlwasser oder durch Mineralablagerungen von innen verschmutzt werden, was die Wärmeübertragung behindert und den thermodynamischen Wirkungsgrad verringert. Viele Anlagen sind mit einem automatischen Reinigungssystem ausgestattet, das Schwammgummikugeln durch die Rohre zirkulieren lässt, um sie zu reinigen, ohne dass das System abgeschaltet werden muss. ⓘ
Das Kühlwasser, das zur Kondensation des Dampfes im Kondensator verwendet wird, kehrt zu seiner Quelle zurück, ohne dass es verändert, sondern nur erwärmt wurde. Wenn das Wasser in ein lokales Gewässer zurückfließt (und nicht in einen Umlaufkühlturm), wird es häufig mit kühlem "Rohwasser" temperiert, um einen Temperaturschock zu vermeiden, wenn es in das Gewässer eingeleitet wird. ⓘ
Eine weitere Form des Kondensationssystems ist der luftgekühlte Kondensator. Der Prozess ähnelt dem eines Kühlers und eines Ventilators. Die Abwärme aus dem Niederdruckteil einer Dampfturbine fließt durch die Kondensationsrohre, die in der Regel mit Rippen versehen sind, und die Umgebungsluft wird mit Hilfe eines großen Ventilators durch die Rippen gedrückt. Der Dampf kondensiert zu Wasser und wird im Wasser-Dampf-Kreislauf wiederverwendet. Luftgekühlte Kondensatoren arbeiten in der Regel mit einer höheren Temperatur als wassergekühlte Versionen. Dadurch wird zwar Wasser gespart, aber der Wirkungsgrad des Kreislaufs sinkt (was zu mehr Kohlendioxid pro Megawattstunde Strom führt). ⓘ
Am Boden des Kondensators führen leistungsstarke Kondensatpumpen den kondensierten Dampf (Wasser) wieder in den Wasser-Dampf-Kreislauf zurück. ⓘ
Direkte Kühlung ⓘ
Im einfachsten Fall wird das aus einem Fluss entnommene Wasser direkt zur Kühlung hinter der Turbine verwendet; dabei sind besonders die Kondensatoren der Dampfturbinen von Verschmutzung betroffen, die daher mit dem Kugelumlaufverfahren gereinigt werden müssen. ⓘ
Zwei- und mehrstufiger Kühlkreislauf ⓘ
Damit Verschmutzungen nicht den nachgeschalteten Turbinenkondensator verstopfen und damit unwirksam machen, wird das Turbinenkondensator-Kühlwasser mitunter in einem (weitgehend) geschlossenen Kühlwasserkreislauf gekühlt, dem Primär-Kühlkreislauf. Dieses Kühlwasser wird seinerseits über einen Wärmeübertrager vom Flusswasser (Sekundär-Kühlwasser) gekühlt, das Sekundärkühlwasser befindet sich dann meist in einem offenen Kreislauf. ⓘ
Bei Atomkraftwerken ist mitunter eine weitere Trennstufe vorhanden – also drei Kühlwasserkreisläufe, um radioaktive und nicht-radioaktive Bereiche zu trennen. ⓘ
Kühlsystem | Effizienzfaktor ⓘ |
---|---|
Durchlaufkühlung (Seewasser) | 1,024 |
Durchlaufkühlung (Flusswasser) | 1,015 |
Nasskühlturm | 1,000 |
Trockenkühlturm | 0,952 |
Zwischenüberhitzer
Kraftwerksöfen können einen Zwischenüberhitzer haben, dessen Rohre durch heiße Rauchgase außerhalb der Rohre beheizt werden. Der Abdampf der Hochdruckturbine wird durch diese beheizten Rohre geleitet, um mehr Energie zu gewinnen, bevor er die Zwischen- und dann die Niederdruckturbine antreibt. ⓘ
Luftweg
Um ausreichend Luft für die Verbrennung zu erhalten, sind externe Gebläse vorgesehen. Das Primärluftgebläse saugt Luft aus der Atmosphäre an und wärmt die Luft zunächst im Luftvorwärmer auf, um eine bessere Wirtschaftlichkeit zu erzielen. Die Primärluft strömt dann durch die Kohlemühlen und transportiert den Kohlenstaub zu den Brennern, wo er in den Feuerraum eingeblasen wird. Das Sekundärluftgebläse saugt Luft aus der Atmosphäre an und erwärmt die Luft zunächst im Luftvorwärmer, um eine bessere Wirtschaftlichkeit zu erreichen. Die Sekundärluft wird in den Brennern mit dem Kohle-/Primärluftstrom vermischt. ⓘ
Das Saugzuggebläse unterstützt das FD-Gebläse, indem es brennbare Gase aus dem Feuerraum absaugt und den Druck im Feuerraum leicht unter dem Atmosphärendruck hält, um das Austreten von Verbrennungsprodukten aus dem Kesselgehäuse zu vermeiden. ⓘ
Dampfturbinengenerator
Ein Dampfturbinengenerator besteht aus einer Reihe von Dampfturbinen, die miteinander verbunden sind, und einem Generator auf einer gemeinsamen Welle. ⓘ
Dampfturbine

An einem Ende befindet sich in der Regel eine Hochdruckturbine, gefolgt von einer Mitteldruckturbine und schließlich einer, zwei oder drei Niederdruckturbinen sowie der Welle, die mit dem Generator verbunden ist. Während sich der Dampf durch das System bewegt und dabei Druck und Wärmeenergie verliert, vergrößert sich sein Volumen, so dass die Schaufeln in jeder weiteren Stufe einen größeren Durchmesser und eine größere Länge haben müssen, um die verbleibende Energie zu gewinnen. Die gesamte rotierende Masse kann über 200 Tonnen wiegen und 30 m lang sein. Sie ist so schwer, dass sie auch im Stillstand langsam gedreht werden muss (mit 3 Umdrehungen pro Minute), damit sich die Welle nicht einmal leicht durchbiegt und aus dem Gleichgewicht gerät. Dies ist so wichtig, dass es eine von nur sechs Funktionen der Notstrombatterien vor Ort ist. (Die anderen fünf sind Notbeleuchtung, Kommunikation, Stationsalarm, Wasserstoffdichtungssystem des Generators und Schmieröl des Turbogenerators). ⓘ
In einem typischen Kraftwerk des späten 20. Jahrhunderts wird überhitzter Dampf aus dem Kessel durch Rohrleitungen mit einem Durchmesser von 360-410 mm (14-16 Zoll) mit einem Druck von 17 MPa (160 atm) und 540 °C (1.000 °F) zur Hochdruckturbine geleitet, wo der Druck auf 4,1 MPa (41 atm) (600 psi) und die Temperatur auf 320 °C (600 °F) durch die Stufe fällt. Er verlässt die Turbine über kalte Zwischenüberhitzungsleitungen mit einem Durchmesser von 610-660 mm (24-26 Zoll) und wird zurück in den Kessel geleitet, wo der Dampf in speziellen Zwischenüberhitzungsrohren wieder auf 540 °C (1.000 °F) erhitzt wird. Der heiße Zwischenüberhitzungsdampf wird zur Mitteldruckturbine geleitet, wo er sowohl an Temperatur als auch an Druck verliert und direkt zu den langblättrigen Niederdruckturbinen und schließlich zum Kondensator geleitet wird. ⓘ
Turbogenerator
Der Generator, der in der Regel etwa 9 m (30 Fuß) lang ist und einen Durchmesser von 3,7 m (12 Fuß) hat, besteht aus einem feststehenden Stator und einem sich drehenden Rotor, die jeweils kilometerlange, schwere Kupferleiter enthalten. Im Allgemeinen gibt es keinen Dauermagneten, so dass Schwarzstarts vermieden werden. Im Betrieb erzeugt er bis zu 21.000 Ampere bei 24.000 Volt Wechselstrom (504 MWe), während er sich entweder mit 3.000 oder 3.600 Umdrehungen pro Minute dreht und mit dem Stromnetz synchronisiert ist. Der Rotor dreht sich in einer abgedichteten Kammer, die mit Wasserstoffgas gekühlt wird, das ausgewählt wurde, weil es den höchsten bekannten Wärmeübertragungskoeffizienten aller Gase hat und wegen seiner geringen Viskosität, die die Windverluste reduziert. Dieses System erfordert eine besondere Handhabung beim Anfahren, wobei die Luft in der Kammer zunächst durch Kohlendioxid verdrängt wird, bevor sie mit Wasserstoff gefüllt wird. Dadurch wird sichergestellt, dass keine hochexplosive Wasserstoff-Sauerstoff-Umgebung entsteht. ⓘ
Die Frequenz des Stromnetzes beträgt in Nordamerika 60 Hz und in Europa, Ozeanien, Asien (Korea und Teile Japans sind bemerkenswerte Ausnahmen) und Teilen Afrikas 50 Hz. Die gewünschte Frequenz wirkt sich auf die Konstruktion von Großturbinen aus, da diese für eine bestimmte Drehzahl optimiert sind. ⓘ
Der Strom fließt in ein Verteilungsnetz, wo Transformatoren die Spannung für die Übertragung an den Bestimmungsort erhöhen. ⓘ
Die von Dampfturbinen angetriebenen Generatoren verfügen über Hilfssysteme, die einen zufriedenstellenden und sicheren Betrieb ermöglichen. Der Dampfturbinengenerator ist ein rotierendes Gerät und hat im Allgemeinen eine schwere Welle mit großem Durchmesser. Die Welle muss daher nicht nur abgestützt, sondern auch während des Betriebs in Position gehalten werden. Um den Reibungswiderstand bei der Drehung zu minimieren, verfügt die Welle über eine Reihe von Lagern. Die Lagerschalen, in denen sich die Welle dreht, sind mit einem reibungsarmen Material wie Babbitt-Metall ausgekleidet. Um die Reibung zwischen Welle und Lageroberfläche weiter zu verringern und die Wärmeentwicklung zu begrenzen, ist eine Ölschmierung vorgesehen. ⓘ
Abgasweg und Reinigung
Beim Austritt aus dem Kessel wird das Rauchgas durch einen rotierenden flachen Korb aus Metallgewebe geleitet, der die Wärme aufnimmt und sie an die einströmende Frischluft zurückgibt, während sich der Korb dreht. Dies wird als Luftvorwärmer bezeichnet. Das aus dem Kessel austretende Gas ist mit Flugasche beladen, bei der es sich um winzige kugelförmige Aschepartikel handelt. Das Rauchgas enthält Stickstoff sowie die Verbrennungsprodukte Kohlendioxid, Schwefeldioxid und Stickoxide. Die Flugasche wird durch Schlauchfilter in Schlauchkammern oder Elektrofilter entfernt. Nach der Entfernung kann das Nebenprodukt Flugasche manchmal bei der Herstellung von Beton verwendet werden. Diese Reinigung der Rauchgase erfolgt jedoch nur in Anlagen, die mit der entsprechenden Technologie ausgestattet sind. Die meisten Kohlekraftwerke der Welt verfügen jedoch nicht über solche Anlagen. In Europa wurden wirksame Rechtsvorschriften erlassen, um die Verschmutzung durch Rauchgase zu verringern. In Japan wird die Technologie zur Rauchgasreinigung bereits seit über 30 Jahren eingesetzt, in den USA seit über 25 Jahren. China beginnt nun, sich mit der von Kohlekraftwerken verursachten Verschmutzung auseinander zu setzen. ⓘ
Wo dies gesetzlich vorgeschrieben ist, werden Schwefel- und Stickoxidschadstoffe durch Abgaswäscher entfernt, die einen pulverisierten Kalkstein oder eine andere alkalische Nassaufschlämmung verwenden, um diese Schadstoffe aus dem Abgas zu entfernen. Andere Geräte verwenden Katalysatoren, um Stickoxidverbindungen aus dem Rauchgasstrom zu entfernen. Das Gas, das den Schornstein hinaufströmt, kann zu diesem Zeitpunkt bereits auf etwa 50 °C (120 °F) abgekühlt sein. Ein typischer Rauchgaskamin kann 150-180 Meter hoch sein, um die verbleibenden Rauchgasbestandteile in der Atmosphäre zu verteilen. Der höchste Rauchgaskamin der Welt ist 419,7 Meter hoch und befindet sich im Kraftwerk Ekibastuz GRES-2 in Kasachstan. ⓘ
In den Vereinigten Staaten und einer Reihe anderer Länder sind Studien zur Modellierung der atmosphärischen Ausbreitung erforderlich, um die Höhe des Schornsteins zu bestimmen, die zur Einhaltung der örtlichen Luftverschmutzungsvorschriften erforderlich ist. In den Vereinigten Staaten muss die Höhe eines Abgaskamins auch der so genannten "good engineering practice" (GEP) entsprechen. Bei bestehenden Schornsteinen, die die GEP-Schornsteinhöhe überschreiten, müssen alle Studien zur Ausbreitung der Luftverschmutzung für solche Schornsteine die GEP-Schornsteinhöhe und nicht die tatsächliche Schornsteinhöhe verwenden. ⓘ
Hilfssysteme
Kesselspeisewasser-Aufbereitungsanlage und -Lagerung
Da kontinuierlich Dampf entnommen und Kondensat in den Kessel zurückgeführt wird, müssen die Verluste durch Abschlämmung und Leckagen ausgeglichen werden, um den gewünschten Wasserstand in der Dampftrommel des Kessels aufrechtzuerhalten. Zu diesem Zweck wird dem Kesselwassersystem kontinuierlich Ergänzungswasser zugeführt. Verunreinigungen im Rohwasser, das der Anlage zugeführt wird, bestehen im Allgemeinen aus Kalzium- und Magnesiumsalzen, die dem Wasser Härte verleihen. Die Härte im Zusatzwasser für den Kessel führt zu Ablagerungen auf den Wasseroberflächen der Rohre, was zu Überhitzung und Ausfall der Rohre führt. Daher müssen die Salze aus dem Wasser entfernt werden, was durch eine Wasserentsalzungsanlage (DM) geschieht. Eine DM-Anlage besteht im Allgemeinen aus Kationen-, Anionen- und Mischbettaustauschern. Alle Ionen im Endprodukt dieses Prozesses bestehen im Wesentlichen aus Wasserstoff- und Hydroxidionen, die sich zu reinem Wasser rekombinieren. Sehr reines DM-Wasser wird aufgrund seiner sehr hohen Affinität zu Sauerstoff stark korrosiv, sobald es Sauerstoff aus der Atmosphäre aufnimmt. ⓘ
Die Kapazität der DM-Anlage wird durch die Art und Menge der Salze im Rohwasser bestimmt. Ein gewisser Vorrat ist jedoch unerlässlich, da die DM-Anlage zu Wartungszwecken außer Betrieb sein kann. Zu diesem Zweck wird ein Vorratstank installiert, aus dem kontinuierlich DM-Wasser für die Kesselnachspeisung entnommen wird. Der Speicherbehälter für DM-Wasser besteht aus Materialien, die von korrosivem Wasser nicht angegriffen werden, z. B. PVC. Die Rohrleitungen und Ventile sind im Allgemeinen aus rostfreiem Stahl. Manchmal wird eine Dampfabdeckung oder ein Edelstahlschwimmer über dem Wasser im Tank angebracht, um den Kontakt mit der Luft zu vermeiden. Die DM-Wassernachspeisung wird im Allgemeinen im Dampfraum des Oberflächenkondensators (d. h. auf der Vakuumseite) hinzugefügt. Bei dieser Anordnung wird nicht nur das Wasser versprüht, sondern das DM-Wasser wird auch entlüftet, wobei die gelösten Gase durch einen Entlüfter über einen am Kondensator angebrachten Ejektor entfernt werden. ⓘ
System zur Brennstoffaufbereitung

In Kohlekraftwerken wird die Rohkohle aus dem Kohlelager zunächst zerkleinert und dann zu den Kohlebehältern an den Kesseln befördert. Anschließend wird die Kohle zu einem sehr feinen Pulver zermahlen. Bei den Mühlen kann es sich um Kugelmühlen, rotierende Trommelmühlen oder andere Arten von Mühlen handeln. ⓘ
Einige Kraftwerke verbrennen Heizöl anstelle von Kohle. Das Öl muss in den Heizöllagertanks warm (über dem Pourpoint) gehalten werden, um zu verhindern, dass das Öl gerinnt und nicht mehr gepumpt werden kann. Das Öl wird in der Regel auf etwa 100 °C erwärmt, bevor es durch die Heizölspritzdüsen des Ofens gepumpt wird. ⓘ
Die Kessel in einigen Kraftwerken verwenden aufbereitetes Erdgas als Hauptbrennstoff. Andere Kraftwerke können aufbereitetes Erdgas als Hilfsbrennstoff verwenden, wenn die Hauptbrennstoffversorgung (Kohle oder Öl) unterbrochen ist. In solchen Fällen sind an den Kesselöfen separate Gasbrenner vorgesehen. ⓘ
Sperrdrehvorrichtung
Das Sperrwerk (oder "Drehwerk") ist ein Mechanismus, der dafür sorgt, dass sich die Turbinengeneratorwelle nach einem Blockstillstand mit einer sehr niedrigen Drehzahl dreht. Nach dem "Auslösen" des Blocks (d. h. Schließen des Dampfeinlassventils) läuft die Turbine bis zum Stillstand aus. Bei vollständigem Stillstand neigt die Turbinenwelle dazu, sich zu verbiegen, wenn sie zu lange in einer Position verharrt. Dies liegt daran, dass sich die Wärme im Inneren des Turbinengehäuses in der oberen Hälfte des Gehäuses konzentriert, so dass die obere Hälfte der Welle heißer ist als die untere Hälfte. Die Welle kann sich daher um Millionstel Zoll verziehen oder verbiegen. ⓘ
Diese geringe Wellendurchbiegung, die nur von Exzentrizitätsmessgeräten festgestellt werden kann, würde ausreichen, um beim Wiederanfahren der gesamten Dampfturbinen-Generatoreinheit schädliche Schwingungen zu verursachen. Die Welle wird daher automatisch mit niedriger Drehzahl (etwa ein Prozent der Nenndrehzahl) durch das Sperrrad gedreht, bis sie ausreichend abgekühlt ist, um einen vollständigen Stillstand zu ermöglichen. ⓘ
Ölsystem
Für die Ölversorgung beim Anfahren des Dampfturbinengenerators wird eine Hilfsölsystempumpe eingesetzt. Sie versorgt das Hydraulikölsystem, das für das Dampfeinlass-Hauptabsperrventil der Dampfturbine, die Regelventile, die Lager- und Dichtungsölsysteme, die entsprechenden Hydraulikrelais und andere Mechanismen erforderlich ist. ⓘ
Bei einer voreingestellten Drehzahl der Turbine während des Anfahrens übernimmt eine von der Hauptwelle der Turbine angetriebene Pumpe die Funktionen des Hilfssystems. ⓘ
Kühlung des Generators
Während kleine Generatoren durch Luft gekühlt werden können, die durch Filter am Einlass angesaugt wird, erfordern größere Einheiten in der Regel spezielle Kühlvorrichtungen. Die Kühlung mit Wasserstoffgas in einem ölgedichteten Gehäuse wird verwendet, weil es den höchsten bekannten Wärmeübergangskoeffizienten aller Gase hat und wegen seiner geringen Viskosität, die die Windverluste reduziert. Dieses System erfordert eine besondere Handhabung beim Anfahren, wobei die Luft im Generatorgehäuse zunächst durch Kohlendioxid verdrängt wird, bevor es mit Wasserstoff gefüllt wird. Dadurch wird sichergestellt, dass sich der hochentzündliche Wasserstoff nicht mit dem Luftsauerstoff vermischt. ⓘ
Der Wasserstoffdruck im Inneren des Gehäuses wird etwas höher als der Atmosphärendruck gehalten, um das Eindringen von Außenluft zu vermeiden, und bis zu einem Druck von etwa zwei Atmosphären, um die Effizienz der Wärmeübertragung zu verbessern. Der Wasserstoff muss an der Stelle, an der die Welle aus dem Gehäuse austritt, gegen ein Austreten nach außen abgedichtet werden. Um die Welle herum werden Gleitringdichtungen mit einem sehr kleinen Ringspalt eingebaut, um ein Reiben zwischen der Welle und den Dichtungen zu vermeiden. Um zu verhindern, dass das Wasserstoffgas in die Atmosphäre entweicht, wird Dichtungsöl verwendet. ⓘ
Der Generator wird auch mit Wasser gekühlt. Da die Generatorspulen auf einem Potenzial von etwa 22 kV liegen, wird eine isolierende Barriere wie Teflon verwendet, um die Wasserleitung und die Hochspannungswicklungen des Generators miteinander zu verbinden. Es wird demineralisiertes Wasser mit geringer Leitfähigkeit verwendet. ⓘ
Generator-Hochspannungsanlage
Die Generatorspannung für moderne, an das Stromnetz angeschlossene Generatoren reicht von 11 kV bei kleineren Anlagen bis zu 30 kV bei größeren Anlagen. Die Hochspannungsleitungen des Generators bestehen normalerweise aus großen Aluminiumkanälen, da sie im Vergleich zu den Kabeln kleinerer Maschinen eine hohe Stromstärke aufweisen. Sie sind in gut geerdeten Aluminiumkanälen untergebracht und werden von geeigneten Isolatoren getragen. Die Hochspannungsleitungen des Generators sind mit Aufwärtstransformatoren verbunden, die den Anschluss an ein Hochspannungs-Umspannwerk (in der Regel im Bereich von 115 kV bis 765 kV) zur Weiterleitung durch das örtliche Stromnetz herstellen. ⓘ
Für die Hochspannungsleitungen sind die erforderlichen Schutz- und Messeinrichtungen vorgesehen. Somit bilden der Dampfturbinengenerator und der Transformator eine Einheit. Kleinere Einheiten können sich einen gemeinsamen Generator-Aufwärtstransformator mit einzelnen Leistungsschaltern teilen, um die Generatoren an eine gemeinsame Sammelschiene anzuschließen. ⓘ
Überwachungs- und Alarmsystem
Die meisten Betriebssteuerungen des Kraftwerks sind automatisch. Gelegentlich kann jedoch ein manuelles Eingreifen erforderlich sein. Daher ist das Kraftwerk mit Überwachungs- und Alarmsystemen ausgestattet, die die Kraftwerksbetreiber alarmieren, wenn bestimmte Betriebsparameter erheblich von ihrem normalen Bereich abweichen. ⓘ
Batteriegespeiste Notbeleuchtung und Kommunikation
Ein zentrales Batteriesystem, bestehend aus Blei-Säure-Zellen-Einheiten, liefert im Bedarfsfall Notstrom für wichtige Einrichtungen wie die Kontrollsysteme des Kraftwerks, die Kommunikationssysteme, das Wasserstoffdichtungssystem des Generators, die Schmierölpumpen der Turbine und die Notbeleuchtung. Dies ist für eine sichere, schadensfreie Abschaltung der Blöcke in einer Notfallsituation unerlässlich. ⓘ
Wasserumlaufsystem
Zur Abführung der thermischen Belastung durch den Abdampf der Hauptturbine, das Kondensat aus dem Stopfbuchsendampfkondensator und das Kondensat aus dem Niederdruckerhitzer durch kontinuierliche Zufuhr von Kühlwasser zum Hauptkondensator, was zur Kondensation führt. ⓘ
Schätzungen zufolge wird der Kühlwasserverbrauch von Kraftwerken im Binnenland die Verfügbarkeit der meisten Wärmekraftwerke bis 2040-2069 verringern. ⓘ
Bedeutung des Wärmekraftwerkes
Wärmekraftwerke liefern in den meisten industrialisierten Staaten (Ausnahmen: Norwegen, Schweiz und Österreich) einen Großteil (je nach Region 60–100 %) der elektrischen Energie. Der Grund für diese Stellung sind die sehr großen, leicht erschließbaren Energievorkommen in Form von fossilen Brennstoffen wie Erdöl und Kohle, sowie Energievorkommen aus Uran; diese Quellen wurden jahrzehntelang genutzt und die Technologien optimiert. Alternative Energiequellen und Verfahren gewinnen aber stetig an Bedeutung, da die fossilen Vorkommen begrenzt sind und ihre Abgas- und Abfallprodukte umweltschädlich sind. ⓘ
Faktoren für die praktische Nutzbarkeit
Neben dem Wirkungsgrad sind folgende Faktoren zu beachten:
- Generelle verfügbare Energiemenge der primären Energiequelle
- Erschliessbare Vorkommen
- Kosten pro erzeugter Energieeinheit
- Technische Realisierbarkeit der Verbrennung
- Umweltbelastung beispielsweise durch Emissionen, Abwärme oder ionisierende Strahlung
- Betriebsrisiken ⓘ
Kühlung
Wärmekraftwerke gewinnen ihre Energie aus einer Temperaturdifferenz; je höher diese ist, desto mehr Energie kann gewonnen werden. Neben einer möglichst heißen Wärmequelle ist daher auch eine möglichst kalte Wärmesenke hilfreich, weshalb viele Wärmekraftwerke an geeigneter Stelle eine Kühlung ihres Arbeitsmittels haben. ⓘ
Viele Wärmekraftwerke nutzen zur Kühlung das Wasser vorbeifließender Flüsse. Das erspart oder unterstützt den Kühlturm mit seinen vielen Nachteilen und die Temperatur am Auslass der Dampfturbine kann wirkungsvoller abgesenkt werden. Allerdings kann dadurch das Flusswasser zu warm werden. Es sind deshalb Grenzwerte festgelegt, um wie viel Grad Celsius bzw. auf welche Temperatur der Fluss maximal erwärmt werden darf, um ein Umkippen zu verhindern. Dies kann im Sommer bei hoher Wassertemperatur dazu führen, dass ein Kraftwerk abgeschaltet werden muss. Seit den 1970er Jahren wurden sogenannte Wärmelastpläne eingerichtet, denen man die maximale Temperatur des Gewässers entnehmen kann. Eine weitere, auch kombinierbare Möglichkeit ist die Verwendung von Kühltürmen, über die die Abwärme abgegeben wird, sofern man sie nicht über die Kraft-Wärme-Kopplung zur Heizung benachbarter Wohnsiedlungen oder von Gewächshäusern nutzen kann. ⓘ
Wärmekraftwerke gehören zu den größten Wasserverbrauchern in der Wirtschaft. In den Industriestaaten entfällt etwa 40 % der gesamten Wasserentnahme aus Frischwasserquellen auf Wärmekraftwerke, wobei die höchsten Verbräuche Kernkraftwerke und (zukünftige) Kohlekraftwerke mit CO2-Abscheidung und -Speicherung aufweisen. ⓘ
Durchlaufkühlung ohne Kühlturm
Wenn das erwärmte Kühlwasser unbehandelt in das Gewässer zurückgeführt wird, handelt es sich um eine Durchlaufkühlung. Die Durchlaufkühlung stellt die effizienteste und wirtschaftlichste Form der Kühlung dar. Sie kann jedoch nur dort angewandt werden, wo der Wärmeeintrag keine unzumutbare Belastung für das Gewässer darstellt. Kritisch sind die Sommermonate, weil dann ein Umkippen des Gewässers erfolgen kann. In Deutschland wird Durchlaufkühlung vorwiegend an Küstenstandorten oder am Rhein betrieben. Speziell am Rhein hat die "Arbeitsgemeinschaft der Bundesländer zur Reinhaltung des Rheins (ARGE Rhein)" bereits 1971 einen Wärmelastplan für den deutschen Rheinabschnitt vorgelegt, der noch heute Gültigkeit besitzt. ⓘ
Ablaufkühlung mit Kühlturm
Bei diesem Verfahren wird einem Fließgewässer das notwendige Kühlwasser entnommen, im Kondensator erwärmt und dann im Kühlturm versprüht. Das nicht verdampfte und auf seine Ursprungstemperatur abgekühlte Wasser wird wieder dem Fließgewässer zugeführt, um Salze und Verunreinigungen auszuschwemmen. Letztere würden in ihrer Konzentration ständig zunehmen, wenn das nicht an die Atmosphäre abgegebene Wasser wiederholt im Turm eingesetzt werden würde. ⓘ
Umlaufkühlung mit Kühlturm
Die Umlaufkühlung verwendet dagegen stets das gleiche Wasser; es werden ausschließlich die Verluste aus Verdampfung und Abflut ergänzt. Dieses Verfahren hat sich bei einem geringen Angebot an Kühlwasser sehr bewährt. Jedoch hat die ständige Verdunstung eine Aufsalzung (die Eindickung) des Kühlwassers zur Folge, sodass es zu Ablagerungen insbesondere von Calcium- und Magnesium-Karbonaten (Härtebildner) kommt. Um dem Effekt entgegenzuwirken, wird das Kühlwasser mit Chemikalien (z. B. Phosphonsäure) stabilisiert. Ab einer gewissen Obergrenze des Gesamtsalzgehaltes und der Gesamthärte muss über Abflut und Frischwasserzulauf eine Verdünnung des Kühlwassers herbeigeführt werden. Beim Einleiten der Abflut in städtische Schmutzwasseranlagen (Indirekteinleitung) oder Gewässer (Direkteinleitung) gelten staatliche Umweltauflagen. Ein weiteres Problem der Umlaufkühlung ist das Wachstum von Mikroorganismen. Neben dem Fouling müssen hygienische Probleme mit lungengängigen Bakterien im Kühlturm (Legionella spec., Pseudomonas aeruginosa) berücksichtigt werden. Daher wird das Kühlwasser auch mit Biozid und Bio-Dispergator behandelt. ⓘ
Technische Realisierungen des Prinzips Wärmekraftwerk
- Wärmeentnahme aus der Natur (alle regenerativ):
- Erdwärmekraftwerk
- Meereswärmekraftwerk
- Sonnenwärmekraftwerk
- Wärmefreisetzung im Kraftwerk selber:
- Kernphysikalisches Kraftwerk
- Kernkraftwerk (eigentlich Kernspaltungskraftwerk)
- Kernfusionskraftwerk (bislang nur Forschungsanlagen)
- Kohlekraftwerk
- Braunkohlekraftwerk
- Steinkohlekraftwerk
- Torfkraftwerk
- Heizölkraftwerk
- Erdgaskraftwerk
- Gasturbinenkraftwerk
- GuD-Kraftwerk
- Biomassekraftwerk (regenerative Energiequelle)
- Kernphysikalisches Kraftwerk
- Wärmeentnahme aus anderen technischen Prozessen:
- Abwärmekraftwerk
- Müllheizkraftwerk ⓘ
- Abwärmekraftwerk