Elektromotor

Ein Elektromotor ist eine elektrische Maschine, die elektrische Energie in mechanische Energie umwandelt. Die meisten Elektromotoren funktionieren durch die Wechselwirkung zwischen dem Magnetfeld des Motors und dem elektrischen Strom in einer Drahtwicklung, um eine Kraft in Form eines Drehmoments zu erzeugen, das auf die Motorwelle wirkt. Ein elektrischer Generator ist mechanisch identisch mit einem Elektromotor, arbeitet jedoch mit einem umgekehrten Energiefluss und wandelt mechanische Energie in elektrische Energie um. ⓘ
Elektromotoren können durch Gleichstromquellen (DC), z. B. Batterien oder Gleichrichter, oder durch Wechselstromquellen (AC), z. B. ein Stromnetz, Wechselrichter oder elektrische Generatoren, betrieben werden. ⓘ
Elektromotoren können unter anderem nach der Art der Stromquelle, der Konstruktion, der Anwendung und der Art der Bewegungsausgabe klassifiziert werden. Sie können mit Wechsel- oder Gleichstrom betrieben werden, bürstenbehaftet oder bürstenlos, einphasig, zweiphasig oder dreiphasig, mit axialem oder radialem Fluss sein und können luft- oder flüssigkeitsgekühlt sein. ⓘ
Genormte Motoren bieten eine praktische mechanische Leistung für den industriellen Einsatz. Die größten werden für Schiffsantriebe, Pipelinekompression und Pumpspeicheranwendungen mit einer Leistung von über 100 Megawatt eingesetzt. ⓘ
Zu den Anwendungen gehören industrielle Ventilatoren, Gebläse und Pumpen, Werkzeugmaschinen, Haushaltsgeräte, Elektrowerkzeuge, Fahrzeuge und Festplattenlaufwerke. Kleine Motoren sind auch in elektrischen Uhren zu finden. In bestimmten Anwendungen, wie z. B. beim regenerativen Bremsen mit Fahrmotoren, können Elektromotoren umgekehrt als Generatoren eingesetzt werden, um Energie zurückzugewinnen, die sonst als Wärme und Reibung verloren ginge. ⓘ
Elektromotoren erzeugen eine lineare oder rotierende Kraft (Drehmoment), die dazu dient, einen externen Mechanismus anzutreiben, z. B. einen Ventilator oder einen Aufzug. Ein Elektromotor ist im Allgemeinen für eine kontinuierliche Drehung oder für eine lineare Bewegung über eine im Vergleich zu seiner Größe beträchtliche Strecke ausgelegt. Magnetspulen sind ebenfalls Wandler, die elektrische Energie in mechanische Bewegung umwandeln, können aber nur eine begrenzte Strecke zurücklegen. ⓘ
Geschichte
Frühe Motoren

Vor den modernen elektromagnetischen Motoren wurden experimentelle Motoren untersucht, die mit elektrostatischer Kraft arbeiteten. Die ersten Elektromotoren waren einfache elektrostatische Geräte, die der schottische Mönch Andrew Gordon und der amerikanische Experimentator Benjamin Franklin in den 1740er Jahren in Experimenten beschrieben. Das ihnen zugrunde liegende theoretische Prinzip, das Coulombsche Gesetz, wurde 1771 von Henry Cavendish entdeckt, aber nicht veröffentlicht. Dieses Gesetz wurde 1785 unabhängig davon von Charles-Augustin de Coulomb entdeckt, der es veröffentlichte, so dass es heute unter seinem Namen bekannt ist. Aufgrund der Schwierigkeit, die erforderlichen hohen Spannungen zu erzeugen, wurden elektrostatische Motoren nie für praktische Zwecke eingesetzt. ⓘ
Die Erfindung der elektrochemischen Batterie durch Alessandro Volta im Jahr 1799 ermöglichte die Erzeugung anhaltender elektrischer Ströme. Hans Christian Ørsted entdeckte 1820, dass ein elektrischer Strom ein magnetisches Feld erzeugt, das eine Kraft auf einen Magneten ausüben kann. Es dauerte nur wenige Wochen, bis André-Marie Ampère die erste Formulierung der elektromagnetischen Wechselwirkung entwickelte und das Ampère'sche Kraftgesetz vorstellte, das die Erzeugung mechanischer Kraft durch die Wechselwirkung eines elektrischen Stroms und eines Magnetfelds beschrieb. ⓘ
Die erste Demonstration des Effekts mit einer Drehbewegung wurde von Michael Faraday am 3. September 1821 im Keller der Royal Institution durchgeführt. Ein frei hängender Draht wurde in ein Quecksilberbad getaucht, auf dem ein Permanentmagnet (PM) angebracht war. Wenn ein Strom durch den Draht geleitet wurde, drehte sich der Draht um den Magneten, was zeigte, dass der Strom ein enges kreisförmiges Magnetfeld um den Draht erzeugte. Faraday veröffentlichte die Ergebnisse seiner Entdeckung im Quarterly Journal of Science und schickte Kopien seiner Arbeit zusammen mit Modellen seines Geräts im Taschenformat an Kollegen in aller Welt, damit auch sie das Phänomen der elektromagnetischen Rotation beobachten konnten. Dieser Motor wird häufig in physikalischen Experimenten demonstriert, wobei das (giftige) Quecksilber durch Salzsole ersetzt wird. Barlows Rad war eine frühe Weiterentwicklung dieser Faraday-Demonstration, obwohl diese und ähnliche homopolare Motoren bis zum Ende des Jahrhunderts für die praktische Anwendung ungeeignet blieben. ⓘ


Im Jahr 1827 begann der ungarische Physiker Ányos Jedlik mit elektromagnetischen Spulen zu experimentieren. Nachdem Jedlik die technischen Probleme der kontinuierlichen Rotation mit der Erfindung des Kommutators gelöst hatte, nannte er seine frühen Geräte "elektromagnetische Selbstläufer". Obwohl sie nur zu Lehrzwecken verwendet wurden, demonstrierte Jedlik 1828 das erste Gerät, das die drei Hauptbestandteile praktischer Gleichstrommotoren enthielt: den Stator, den Rotor und den Kommutator. Das Gerät kam ohne Dauermagnete aus, da die Magnetfelder sowohl der feststehenden als auch der sich drehenden Teile allein durch die Ströme erzeugt wurden, die durch ihre Wicklungen flossen. ⓘ
Gleichstrommotoren
Der erste Gleichstrommotor mit Kommutator, der Maschinen antreiben konnte, wurde 1832 vom britischen Wissenschaftler William Sturgeon erfunden. Nach Sturgeons Arbeit wurde von dem amerikanischen Erfinder Thomas Davenport und Emily Davenport ein Gleichstrommotor mit Kommutator gebaut, den er 1837 patentieren ließ. Die Motoren liefen mit bis zu 600 Umdrehungen pro Minute und trieben Werkzeugmaschinen und eine Druckmaschine an. Aufgrund der hohen Kosten für Primärbatterien waren die Motoren kommerziell nicht erfolgreich und führten zum Bankrott von Davenport. Mehrere Erfinder folgten Sturgeon bei der Entwicklung von Gleichstrommotoren, aber alle stießen auf die gleichen Probleme mit den Batteriekosten. Da es zu dieser Zeit noch kein Stromverteilungssystem gab, entstand kein praktischer Markt für diese Motoren. ⓘ
Nach vielen anderen mehr oder weniger erfolgreichen Versuchen mit relativ schwachen rotierenden und hin- und hergehenden Apparaten entwickelte der Preuße Moritz von Jacobi im Mai 1834 den ersten echten rotierenden Elektromotor. Er entwickelte eine bemerkenswerte mechanische Ausgangsleistung. Sein Motor stellte einen Weltrekord auf, den Jacobi vier Jahre später im September 1838 verbesserte. Sein zweiter Motor war stark genug, um ein Boot mit 14 Personen über einen breiten Fluss zu treiben. In den Jahren 1839/40 gelang es auch anderen Entwicklern, Motoren mit ähnlicher und dann höherer Leistung zu bauen. ⓘ
1855 baute Jedlik ein Gerät, das auf ähnlichen Prinzipien beruhte wie seine elektromagnetischen Selbstläufer und nützliche Arbeit leisten konnte. Im selben Jahr baute er ein Modell eines Elektrofahrzeugs. ⓘ
Ein wichtiger Wendepunkt kam 1864, als Antonio Pacinotti erstmals den Ringanker beschrieb (obwohl er ursprünglich für einen Gleichstromgenerator, d. h. einen Dynamo, konzipiert war). Dieser bestand aus symmetrisch angeordneten, in sich geschlossenen Spulen, die mit den Stäben eines Kommutators verbunden waren, dessen Bürsten praktisch keinen schwankenden Strom lieferten. Die ersten kommerziell erfolgreichen Gleichstrommotoren folgten den Entwicklungen von Zénobe Gramme, der 1871 Pacinottis Entwurf neu erfand und einige Lösungen von Werner Siemens übernahm. ⓘ
Die Entdeckung der Reversibilität der elektrischen Maschine, die von Siemens 1867 angekündigt und von Pacinotti 1869 beobachtet wurde, kam den Gleichstrommaschinen zugute. Gramme demonstrierte sie zufällig anlässlich der Wiener Weltausstellung 1873, als er zwei solche Gleichstromgeräte bis zu 2 km voneinander entfernt miteinander verband und eines davon als Generator und das andere als Motor verwendete. ⓘ
Der Trommelrotor wurde 1872 von Friedrich von Hefner-Alteneck von Siemens & Halske eingeführt, um den Ringanker von Pacinotti zu ersetzen und so den Wirkungsgrad der Maschine zu verbessern. Im folgenden Jahr führte Siemens & Halske den Lamellenrotor ein, mit dem geringere Eisenverluste und höhere induzierte Spannungen erzielt wurden. Im Jahr 1880 versah Jonas Wenström den Rotor mit Schlitzen zur Aufnahme der Wicklung, was den Wirkungsgrad weiter erhöhte. ⓘ
1886 erfand Frank Julian Sprague den ersten praktischen Gleichstrommotor, ein funkenloses Gerät, das eine relativ konstante Drehzahl bei variabler Last beibehielt. Weitere elektrische Erfindungen von Sprague aus dieser Zeit verbesserten die Stromverteilung im Netz (die Arbeiten wurden bereits während seiner Anstellung bei Thomas Edison durchgeführt), ermöglichten die Rückspeisung von Strom aus Elektromotoren in das Stromnetz, sorgten für die Stromverteilung an Straßenbahnen über Oberleitungen und den Strommast und boten Kontrollsysteme für den elektrischen Betrieb. So konnte Sprague mit Hilfe von Elektromotoren 1887-88 in Richmond, Virginia, das erste elektrische Oberleitungssystem, 1892 den elektrischen Aufzug und das Steuerungssystem sowie die elektrische U-Bahn mit unabhängig angetriebenen, zentral gesteuerten Wagen erfinden. Letztere wurde erstmals 1892 in Chicago von der South Side Elevated Railroad installiert, wo sie im Volksmund als "L" bekannt wurde. Spragues Motor und verwandte Erfindungen führten zu einem explosionsartigen Anstieg des Interesses an Elektromotoren und deren Einsatz in der Industrie. Die Entwicklung von Elektromotoren mit akzeptablem Wirkungsgrad wurde mehrere Jahrzehnte lang verzögert, weil man die extreme Bedeutung eines Luftspalts zwischen Rotor und Stator nicht erkannte. Effiziente Konstruktionen haben einen vergleichsweise kleinen Luftspalt. Der St.-Louis-Motor, der lange Zeit in Klassenzimmern zur Veranschaulichung von Motorprinzipien verwendet wurde, ist aus demselben Grund ineffizient und sieht auch nicht wie ein moderner Motor aus. ⓘ
Elektromotoren revolutionierten die Industrie. Industrielle Prozesse waren nicht mehr durch die Kraftübertragung mittels Wellen, Riemen, Druckluft oder Hydraulikdruck begrenzt. Stattdessen konnte jede Maschine mit einer eigenen Stromquelle ausgestattet werden, was eine einfache Steuerung am Einsatzort ermöglichte und die Effizienz der Kraftübertragung verbesserte. Elektromotoren in der Landwirtschaft machten die Muskelkraft von Mensch und Tier bei Aufgaben wie der Getreideverarbeitung oder dem Pumpen von Wasser überflüssig. Der Einsatz von Elektromotoren im Haushalt (z. B. in Waschmaschinen, Geschirrspülern, Ventilatoren, Klimaanlagen und Kühlschränken (als Ersatz für Eiskästen)) reduzierte die schwere Arbeit im Haushalt und ermöglichte einen höheren Standard an Bequemlichkeit, Komfort und Sicherheit. Heute verbrauchen Elektromotoren mehr als die Hälfte der in den USA erzeugten elektrischen Energie. ⓘ
Wechselstrommotoren
1824 formulierte der französische Physiker François Arago die Existenz rotierender Magnetfelder, die so genannten Arago'schen Rotationen, die Walter Baily 1879 durch manuelles Ein- und Ausschalten von Schaltern als den ersten primitiven Induktionsmotor nachwies. In den 1880er Jahren versuchten viele Erfinder, funktionsfähige Wechselstrommotoren zu entwickeln, da die Vorteile des Wechselstroms bei der Hochspannungsübertragung über große Entfernungen durch die Unfähigkeit, Motoren mit Wechselstrom zu betreiben, aufgehoben wurden. ⓘ
Der erste kommutatorlose Wechselstrom-Induktionsmotor wurde 1885 von Galileo Ferraris erfunden. Ferraris konnte seine erste Konstruktion verbessern, indem er 1886 fortschrittlichere Konstruktionen herstellte. 1888 veröffentlichte die Königliche Akademie der Wissenschaften von Turin Ferraris' Forschungsergebnisse, in denen er die Grundlagen des Motorbetriebs darlegte, kam aber zu dem Schluss, dass "der auf diesem Prinzip basierende Apparat als Motor keine kommerzielle Bedeutung haben könnte". ⓘ
Eine mögliche industrielle Entwicklung wurde von Nikola Tesla ins Auge gefasst, der 1887 unabhängig seinen Induktionsmotor erfand und im Mai 1888 ein Patent erhielt. Im selben Jahr legte Tesla der AIEE sein Papier A New System of Alternate Current Motors and Transformers vor, in dem er drei patentierte zweiphasige Vier-Stator-Pol-Motortypen beschrieb: einen mit einem vierpoligen Rotor, der einen nicht selbstanlaufenden Reluktanzmotor bildet, einen anderen mit einem gewickelten Rotor, der einen selbstanlaufenden Induktionsmotor bildet, und den dritten einen echten Synchronmotor mit separat erregter Gleichstromversorgung der Rotorwicklung. Eines der Patente, die Tesla 1887 anmeldete, beschrieb jedoch auch einen Induktionsmotor mit kurzgeschlossenem Rotor. George Westinghouse, der bereits die Rechte von Ferraris erworben hatte (1.000 USD), kaufte Teslas Patente umgehend auf (60.000 USD plus 2,50 USD pro verkauftem PS, gezahlt bis 1897), stellte Tesla für die Entwicklung seiner Motoren ein und beauftragte C.F. Scott, Tesla zu helfen; Tesla verließ jedoch 1889 das Unternehmen, um sich anderen Aufgaben zu widmen. Der Wechselstrom-Induktionsmotor mit konstanter Drehzahl erwies sich als ungeeignet für Straßenfahrzeuge, aber Westinghouse-Ingenieure passten ihn 1891 erfolgreich für den Antrieb eines Bergwerks in Telluride, Colorado, an. Westinghouse stellte 1892 seinen ersten praktischen Induktionsmotor her und entwickelte 1893 eine Reihe von mehrphasigen 60-Hertz-Induktionsmotoren, aber diese frühen Westinghouse-Motoren waren Zweiphasenmotoren mit gewickelten Rotoren. Später entwickelte B.G. Lamme einen rotierenden Stabwicklungsrotor. ⓘ
Michail Doliwo-Dobrowolski, der die Entwicklung der Drehstromtechnik konsequent vorantrieb, erfand 1889 den Drehstrom-Induktionsmotor, sowohl mit Käfigläufer als auch mit gewickeltem Läufer und mit Anlaufrheostat, und 1890 den dreigliedrigen Transformator. Nach einer Vereinbarung zwischen der AEG und der Maschinenfabrik Oerlikon entwickelten Doliwo-Dobrowolski und Charles Eugene Lancelot Brown größere Modelle, nämlich einen Käfigläufer mit 20 PS und einen gewickelten Läufer mit 100 PS und einem Anlaufrheostat. Dies waren die ersten für den praktischen Betrieb geeigneten Drehstrom-Asynchronmotoren. Seit 1889 wurden ähnliche Entwicklungen von Drehstrommaschinen von Wenström begonnen. Auf der Internationalen Elektrotechnischen Ausstellung 1891 in Frankfurt wurde das erste Langstrecken-Drehstromsystem erfolgreich vorgestellt. Es war für 15 kV ausgelegt und erstreckte sich über 175 km vom Lauffener Wasserfall am Neckar. Das Lauffener Kraftwerk umfasste einen 240-kW-Generator mit 86 V und 40 Hz und einen Aufwärtstransformator, während auf der Ausstellung ein Abwärtstransformator einen 100-PS-Drehstrominduktionsmotor speiste, der einen künstlichen Wasserfall antrieb, was die Übertragung der ursprünglichen Stromquelle darstellte. Die Dreiphasen-Induktion wird heute für die meisten kommerziellen Anwendungen verwendet. Mikhail Dolivo-Dobrovolsky behauptete, dass Teslas Motor wegen der zweiphasigen Pulsationen nicht praktikabel sei, was ihn dazu veranlasste, seine dreiphasige Arbeit fortzusetzen. ⓘ
Die General Electric Company begann 1891 mit der Entwicklung von Dreiphasen-Induktionsmotoren. Im Jahr 1896 unterzeichneten General Electric und Westinghouse eine gegenseitige Lizenzvereinbarung über die Konstruktion des Stabwickelrotors, der später als Käfigläufer bezeichnet wurde. Die aus diesen Erfindungen und Innovationen resultierenden Verbesserungen der Induktionsmotoren führten dazu, dass ein 100-PS-Induktionsmotor heute die gleichen Einbaumaße hat wie ein 7,5-PS-Motor von 1897. ⓘ
Einundzwanzigstes Jahrhundert
Im Jahr 2022 wird der Absatz von Elektromotoren auf 800 Millionen Stück geschätzt, mit einem jährlichen Wachstum von 10 %. Elektromotoren verbrauchen ~50 % des weltweiten Stroms. ⓘ
Bestandteile
Die beiden mechanischen Teile eines Elektromotors sind der Rotor, der sich bewegt, und der Stator, der sich nicht bewegt. Er enthält außerdem zwei elektrische Teile, einen Satz Magnete und einen Anker, von denen einer am Rotor und der andere am Stator befestigt ist, die zusammen einen Magnetkreis bilden:
- Feldmagnete - Die Magnete erzeugen ein Magnetfeld, das durch den Anker verläuft. Dabei kann es sich um Elektromagnete oder Dauermagnete handeln. In der Regel befindet sich der Feldmagnet am Stator und der Anker am Rotor, bei einigen Motortypen ist dies jedoch umgekehrt. ⓘ
Lager
Der Rotor wird von Lagern getragen, die die Drehung des Rotors um seine Achse ermöglichen. Die Lager werden ihrerseits vom Motorgehäuse getragen. ⓘ
Rotor
Der Rotor ist das bewegliche Teil, das die mechanische Kraft überträgt. Der Rotor enthält in der Regel stromführende Leiter, auf die das Magnetfeld des Stators eine Kraft ausübt, um die Welle zu drehen. Alternativ dazu tragen einige Rotoren Permanentmagnete, und der Stator hält die Leiter. Dauermagnete bieten einen hohen Wirkungsgrad über einen größeren Betriebsgeschwindigkeits- und Leistungsbereich. ⓘ
Ein Luftspalt zwischen Stator und Rotor ermöglicht dessen Drehung. Die Breite des Spalts hat einen erheblichen Einfluss auf die elektrischen Eigenschaften des Motors. In der Regel wird er so klein wie möglich gehalten, da ein größerer Spalt die Reluktanz des magnetischen Pfads und den Leistungsverlust durch turbulente Luftströmungen erhöht. Der Magnetisierungsstrom steigt und der Leistungsfaktor sinkt mit zunehmendem Luftspalt, so dass schmale Spalte besser sind. Umgekehrt können zu kleine Spalte neben Geräuschen und Verlusten auch zu mechanischen Problemen führen. ⓘ
Die Motorwelle erstreckt sich durch die Lager bis zur Außenseite des Motors, wo die Last angreift. Da die Kräfte der Last über das äußerste Lager hinaus wirken, wird die Last als fliegend bezeichnet. ⓘ
Stator
Der Stator umgibt den Rotor und enthält in der Regel Feldmagnete, bei denen es sich entweder um Elektromagnete, die aus Drahtwicklungen um einen ferromagnetischen Eisenkern bestehen, oder um Permanentmagnete handelt. Diese erzeugen ein Magnetfeld, das durch den Anker des Rotors verläuft und eine Kraft auf die Wicklungen ausübt. Der Statorkern besteht aus vielen dünnen Metallblechen, die gegeneinander isoliert sind, den so genannten Blechen. Die Lamellen werden verwendet, um die Energieverluste zu verringern, die bei der Verwendung eines massiven Kerns entstehen würden. Harzgekapselte Motoren, die in Waschmaschinen und Klimaanlagen eingesetzt werden, nutzen die dämpfenden Eigenschaften von Harz (Kunststoff), um Geräusche und Vibrationen zu reduzieren. Bei diesen Motoren ist der Stator in Kunststoff eingekapselt. ⓘ
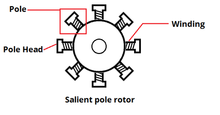
Anker
Der Anker besteht aus Drahtwicklungen um einen ferromagnetischen Kern. Elektrischer Strom, der durch den Draht fließt, bewirkt, dass das Magnetfeld des Feldmagneten eine Kraft (Lorentzkraft) auf ihn ausübt und den Rotor dreht, der die mechanische Leistung erbringt. Wicklungen sind Drähte, die in Spulen verlegt sind und in der Regel um einen geschichteten ferromagnetischen Kern aus Weicheisen gewickelt sind, so dass sie bei Stromzufuhr Magnetpole bilden. ⓘ
Elektrische Maschinen gibt es in Ausführungen mit und ohne Schenkelpole. Bei einem Motor mit Schenkelpolen haben die ferromagnetischen Kerne auf dem Rotor und dem Stator einander zugewandte Vorsprünge, die als Pole bezeichnet werden, wobei um jeden Pol unterhalb der Polfläche ein Draht gewickelt ist, der zu Nord- oder Südpolen des Magnetfelds wird, wenn Strom durch den Draht fließt. Bei einem nicht polaren Motor (oder einem Motor mit verteiltem Feld oder einem Rundläufer) ist der ferromagnetische Kern ein glatter Zylinder, bei dem die Wicklungen gleichmäßig in Schlitzen auf dem Umfang verteilt sind. Durch die Zuführung von Wechselstrom in die Wicklungen entstehen Pole im Kern, die sich kontinuierlich drehen. Ein Spaltpolmotor hat eine Wicklung um einen Teil des Pols, die die Phase des Magnetfelds für diesen Pol verzögert. ⓘ
Kommutator

Ein Kommutator ist ein elektrischer Drehschalter, der den Rotor mit Strom versorgt. Er kehrt den Stromfluss in den Rotorwicklungen periodisch um, wenn sich die Welle dreht. Er besteht aus einem Zylinder, der aus mehreren Metallkontaktsegmenten auf dem Anker besteht. Zwei oder mehr elektrische Kontakte, so genannte "Bürsten", die aus einem weichen, leitfähigen Material wie Kohlenstoff bestehen, drücken gegen den Kommutator. Die Bürsten berühren die aufeinanderfolgenden Kommutatorsegmente gleitend, während er sich dreht, und versorgen den Rotor mit Strom. Die Wicklungen des Rotors sind mit den Kommutatorsegmenten verbunden. Der Kommutator kehrt die Stromrichtung in den Rotorwicklungen bei jeder halben Umdrehung (180°) periodisch um, so dass das auf den Rotor wirkende Drehmoment immer in dieselbe Richtung geht. Ohne diese Stromumkehr würde sich die Richtung des Drehmoments an jeder Rotorwicklung mit jeder halben Umdrehung umkehren, so dass der Rotor stehen bleiben würde. Kommutatoren sind ineffizient und kommutierte Motoren wurden größtenteils durch bürstenlose Gleichstrommotoren, Permanentmagnetmotoren und Induktionsmotoren ersetzt. ⓘ
Motorversorgung und -steuerung
Motorversorgung
Ein Gleichstrommotor wird in der Regel über einen Spaltringkommutator versorgt, wie oben beschrieben. ⓘ
Die Kommutierung von Wechselstrommotoren kann entweder über einen Schleifringkommutator oder eine externe Kommutierung erfolgen. Sie können mit fester oder variabler Drehzahl, synchron oder asynchron betrieben werden. Universalmotoren können sowohl mit Wechselstrom als auch mit Gleichstrom betrieben werden. ⓘ
Motorsteuerung
Gleichstrommotoren können durch Anpassung der an die Klemmen angelegten Spannung oder durch Pulsweitenmodulation (PWM) mit unterschiedlichen Drehzahlen betrieben werden. ⓘ
Wechselstrommotoren, die mit einer festen Drehzahl betrieben werden, werden im Allgemeinen direkt vom Netz oder über Motor-Softstarter versorgt. ⓘ
Wechselstrommotoren, die mit variablen Drehzahlen betrieben werden, werden mit verschiedenen Wechselrichter-, Frequenzumrichter- oder elektronischen Kommutatortechnologien betrieben. ⓘ
Der Begriff elektronischer Kommutator wird gewöhnlich mit selbstkommutierenden bürstenlosen Gleichstrommotoren und geschalteten Reluktanzmotoren in Verbindung gebracht. ⓘ
Typen
Elektromotoren arbeiten nach einem von drei physikalischen Prinzipien: Magnetismus, Elektrostatik und Piezoelektrizität. ⓘ
Bei Magnetmotoren bilden sich sowohl im Rotor als auch im Stator Magnetfelder. Das Produkt aus diesen beiden Feldern erzeugt eine Kraft und damit ein Drehmoment an der Motorwelle. Eines oder beide dieser Felder müssen sich mit der Drehung des Rotors ändern. Dies geschieht durch rechtzeitiges Ein- und Ausschalten der Pole oder durch Veränderung der Polstärke. ⓘ
Die Haupttypen sind Gleichstrommotoren und Wechselstrommotoren, wobei letztere die ersteren ersetzen. ⓘ
Wechselstrom-Elektromotoren sind entweder asynchron oder synchron. ⓘ
Nach dem Start muss ein Synchronmotor für alle normalen Drehmomentbedingungen mit der Geschwindigkeit des sich bewegenden Magnetfelds synchronisiert werden. ⓘ
Bei Synchronmaschinen muss das Magnetfeld auf andere Weise als durch Induktion erzeugt werden, z. B. durch separat erregte Wicklungen oder Permanentmagnete. ⓘ
Ein Kleinstmotor hat entweder eine Leistung von weniger als 1 PS (0,746 kW) oder wird mit einer kleineren Standardbaugröße als ein Standardmotor mit 1 PS hergestellt. Viele Haushalts- und Industriemotoren fallen in die Klasse der Kleinstmotoren. ⓘ
Selbstkommutiert | Extern kommutiert ⓘ | |||
---|---|---|---|---|
Mechanischer Kommutator | Elektronischer Kommutator | Asynchron | Synchron2 | |
AC | DC | AC5, 6 | AC6 | |
|
Elektrisch
erregt:
PM |
PM-Rotor:
Ferromagnetischer Rotor:
|
Dreiphasig:
Zweiphasig: (Verflüssiger) Einphasig:
|
WRSM, PMSM oder BLAC:
SyRM Hysterese Hybride:
Schrittschaltwerk |
Einfache Elektronik | Gleichrichter,
Lineartransistor(en) oder DC-Chopper |
Aufwändigere
Elektronik |
Aufwendigste
Elektronik (VFD), sofern vorhanden |
Anmerkungen:
- Die Drehung ist unabhängig von der Frequenz der Wechselspannung.
- Die Drehung ist gleich der Synchrondrehzahl (Motor-Stator-Feld-Drehzahl).
- Bei SCIM-Betrieb mit fester Drehzahl ist die Drehzahl gleich der Synchrondrehzahl abzüglich der Schlupfdrehzahl.
- In Systemen mit schlupffreier Energierückgewinnung wird WRIM in der Regel für den Motorstart verwendet, kann aber auch zur Änderung der Lastdrehzahl eingesetzt werden.
- Betrieb mit variabler Drehzahl.
- Während die Antriebe von Induktions- und Synchronmotoren in der Regel eine sechsstufige oder sinusförmige Ausgangsfrequenz aufweisen, haben BLDC-Motoren in der Regel eine trapezförmige Stromform; das Verhalten von sinusförmigen und trapezförmigen PM-Maschinen ist jedoch in seinen grundlegenden Aspekten identisch.
- Im drehzahlvariablen Betrieb wird WRIM in Anwendungen mit Schlupf-Energierückgewinnung und doppelt gespeisten Asynchronmaschinen eingesetzt.
- Eine Käfigwicklung ist ein kurzgeschlossener Käfigläufer, eine gewickelte Wicklung ist extern über Schleifringe angeschlossen.
- Meistens einphasig, teilweise auch dreiphasig. ⓘ
Abkürzungen:
- BLAC - Bürstenloser Wechselstrom
- BLDC - Bürstenloser Gleichstrom
- BLDM - Bürstenloser Gleichstrommotor
- EC - Elektronischer Kommutator
- PM - Permanentmagnet
- IPMSM - Innenraum-Dauermagnet-Synchronmotor
- PMSM - Permanentmagnet-Synchronmotor
- SPMSM - Oberflächen-Permanentmagnet-Synchronmotor
- SCIM - Kurzschlussläufermotor (Squirrel Cage Induction)
- SRM - Geschalteter Reluktanzmotor
- SyRM - Synchroner Reluktanzmotor
- VFD - Antrieb mit variabler Frequenz
- WRIM - Induktionsmotor mit gewickeltem Rotor
- WRSM - Wickelrotor-Synchronmotor
- LRA - Strom bei blockiertem Läufer: Der Strom, den Sie unter Startbedingungen erwarten können, wenn Sie die volle Spannung anlegen. Er tritt sofort während des Anlaufs auf.
- RLA - Nennlast-Ampere: Der maximale Strom, den ein Motor unter allen Betriebsbedingungen aufnehmen sollte. Wird oft fälschlicherweise als Lauflaststrom bezeichnet, was zu der irrigen Annahme führt, dass der Motor immer diesen Strom aufnehmen sollte.
- FLA - Volllast-Ampere: Wurde 1976 in "RLA - Nennlast-Ampere" geändert. ⓘ
Selbstgeführter Motor
Gebürsteter Gleichstrommotor
Die meisten Gleichstrommotoren sind kleine Permanentmagnetmotoren (PM). Sie verfügen über eine interne mechanische Kommutierung mit Bürste, um den Strom der Motorwicklungen synchron mit der Rotation umzukehren. ⓘ
Elektrisch erregter Gleichstrommotor

Ein kommutierter Gleichstrommotor besteht aus einem Satz rotierender Wicklungen, die auf einen Anker gewickelt sind, der auf einer rotierenden Welle montiert ist. Die Welle trägt auch den Kommutator. Jeder bürstenbehaftete Gleichstrommotor hat also einen Wechselstrom, der durch seine Wicklungen fließt. Der Strom fließt durch ein oder mehrere Bürstenpaare, die den Kommutator berühren; die Bürsten verbinden eine externe Stromquelle mit dem rotierenden Anker. ⓘ
Der rotierende Anker besteht aus einer oder mehreren Drahtspulen, die um einen geschichteten, magnetisch "weichen" ferromagnetischen Kern gewickelt sind. Der Strom von den Bürsten fließt durch den Kommutator und eine Wicklung des Ankers, wodurch dieser zu einem temporären Magneten (Elektromagnet) wird. Das erzeugte Magnetfeld interagiert mit einem stationären Magnetfeld, das entweder von den PMs oder einer anderen Wicklung (einer Feldspule) als Teil des Motorgehäuses erzeugt wird. Durch die Kraft zwischen den beiden Magnetfeldern wird die Welle gedreht. Der Kommutator schaltet die Stromzufuhr zu den Spulen, wenn sich der Rotor dreht, und sorgt dafür, dass sich die Pole nie vollständig mit den Magnetpolen des Statorfelds ausrichten, so dass sich der Rotor weiterdreht, solange Strom anliegt. ⓘ
Viele der Einschränkungen des klassischen Kommutator-Gleichstrommotors sind darauf zurückzuführen, dass die Bürsten den Kontakt mit dem Kommutator aufrechterhalten müssen, wodurch Reibung entsteht. Die Bürsten erzeugen Funken, wenn sie die Isolierspalte zwischen den Kommutatorabschnitten überqueren. Je nach Kommutatorkonstruktion können die Bürsten Kurzschlüsse zwischen benachbarten Abschnitten und damit Spulenenden verursachen. Außerdem führt die Induktivität der Rotorspulen dazu, dass die Spannung an den einzelnen Spulen ansteigt, wenn der Stromkreis geöffnet wird, was die Funkenbildung verstärkt. Diese Funkenbildung begrenzt die Höchstgeschwindigkeit der Maschine, da eine zu schnelle Funkenbildung zur Überhitzung, Erosion oder sogar zum Schmelzen des Kommutators führt. Die Stromdichte pro Flächeneinheit der Bürsten in Kombination mit ihrem spezifischen Widerstand begrenzt die Leistung des Motors. Das Überqueren der Lücken erzeugt außerdem elektrisches Rauschen; Funkenbildung erzeugt RFI. Die Bürsten verschleißen mit der Zeit und müssen ersetzt werden, und auch der Kommutator selbst unterliegt dem Verschleiß und muss gewartet oder ersetzt werden. Die Kommutatorbaugruppe eines großen Motors ist ein kostspieliges Element, das die präzise Montage vieler Teile erfordert. Bei kleinen Motoren ist der Kommutator in der Regel fest in den Rotor integriert, so dass ein Austausch des Kommutators in der Regel den Austausch des Rotors erfordert. ⓘ
Während die meisten Kommutatoren zylindrisch sind, gibt es auch flache, segmentierte Scheiben, die auf einem Isolator montiert sind. ⓘ
Große Bürsten erzeugen eine große Kontaktfläche, was die Motorleistung maximiert, während kleine Bürsten eine geringe Masse haben, um die Geschwindigkeit zu maximieren, mit der der Motor ohne übermäßige Funkenbildung laufen kann. (Kleine Bürsten sind wegen ihrer geringeren Kosten wünschenswert.) Durch steifere Bürstenfedern können Bürsten mit einer bestimmten Masse trotz größerer Reibungsverluste (geringerer Wirkungsgrad) und beschleunigtem Bürsten- und Kommutatorverschleiß mit einer höheren Drehzahl arbeiten. Bei der Konstruktion von Bürsten für Gleichstrommotoren muss daher ein Kompromiss zwischen Ausgangsleistung, Geschwindigkeit und Effizienz/Verschleiß gefunden werden. ⓘ
Gleichstrommaschinen sind wie folgt definiert:
- Ankerkreis - Eine Wicklung, die die Last trägt, entweder stationär oder rotierend.
- Feldkreis - Ein Satz von Wicklungen, der ein Magnetfeld erzeugt.
- Kommutierung: Eine mechanische Technik, mit der eine Gleichrichtung erreicht werden kann oder von der Gleichstrom abgeleitet werden kann. ⓘ

Die fünf Arten von bürstenbehafteten Gleichstrommotoren sind:
- Nebenschluss mit Wicklung
- Reihenschluss
- Compound (zwei Konfigurationen):
- Kumulativ zusammengesetzt
- Differentialgekoppelt
- Permanentmagnet (nicht abgebildet)
- Fremderregt (nicht abgebildet). ⓘ
Dauermagnet
Ein Motor mit Permanentmagneten (PM) hat keine Feldwicklung auf dem Statorrahmen, sondern nutzt stattdessen PMs zur Erzeugung des Magnetfelds. Bei großen Motoren können Kompensationswicklungen in Reihe mit dem Anker verwendet werden, um die Kommutierung unter Last zu verbessern. Dieses Feld ist fest und kann nicht zur Drehzahlregelung eingestellt werden. PM-Felder (Statoren) sind in Miniaturmotoren praktisch, um den Stromverbrauch der Feldwicklung zu eliminieren. Die meisten größeren Gleichstrommotoren sind vom Typ "Dynamo", die über Statorwicklungen verfügen. In der Vergangenheit konnten PMs nicht dazu gebracht werden, einen hohen Fluss beizubehalten, wenn sie zerlegt wurden; Feldwicklungen waren praktischer, um den benötigten Fluss zu erhalten. Große PMs sind jedoch kostspielig, gefährlich und schwierig zu montieren; dies begünstigt gewickelte Felder für große Maschinen. ⓘ
Um das Gesamtgewicht und die Größe zu minimieren, können Miniatur-PM-Motoren Hochenergiemagnete aus Neodym verwenden; die meisten bestehen aus einer Neodym-Eisen-Bor-Legierung. Mit ihrer höheren Flussdichte sind elektrische Maschinen mit Hochenergie-PMs mindestens konkurrenzfähig mit allen optimal ausgelegten einseitig gespeisten Synchron- und Induktionsmaschinen. Miniaturmotoren ähneln dem Aufbau in der Abbildung, mit dem Unterschied, dass sie mindestens drei Rotorpole haben (um das Anlaufen unabhängig von der Rotorposition zu gewährleisten) und ihr Außengehäuse ein Stahlrohr ist, das die Außenseiten der gekrümmten Feldmagnete magnetisch verbindet. ⓘ
Elektronischer Kommutator (EC)
Bürstenloser Gleichstrom
Einige der Probleme des bürstenbehafteten Gleichstrommotors werden bei der BLDC-Konstruktion eliminiert. Bei diesem Motor wird der mechanische "Drehschalter" oder Kommutator durch einen externen elektronischen Schalter ersetzt, der mit der Position des Rotors synchronisiert ist. BLDC-Motoren haben in der Regel einen Wirkungsgrad von mehr als 85 % und erreichen bis zu 96,5 %, während bürstenbehaftete Gleichstrommotoren in der Regel einen Wirkungsgrad von 75-80 % aufweisen. ⓘ
Die charakteristische trapezförmige Wellenform der gegenelektromotorischen Kraft (CEMF) des BLDC-Motors ergibt sich zum einen aus der gleichmäßigen Verteilung der Statorwicklungen und zum anderen aus der Anordnung der Permanentmagnete des Rotors. Die Statorwicklungen von trapezförmigen BLDC-Motoren, die auch als elektronisch kommutierte Gleichstrom- oder Inside-Out-Gleichstrommotoren bekannt sind, können einphasig, zweiphasig oder dreiphasig sein und verwenden Hall-Effekt-Sensoren, die auf ihren Wicklungen zur Erfassung der Rotorposition und zur kostengünstigen Kommutatorsteuerung angebracht sind. ⓘ
BLDC-Motoren werden häufig dort eingesetzt, wo eine präzise Drehzahlregelung erforderlich ist, wie z. B. in Computerlaufwerken oder Videokassettenrekordern. Die Spindeln in CD- und CD-ROM-Laufwerken (usw.) und Mechanismen in Bürogeräten wie Lüftern, Laserdruckern und Fotokopierern. Sie haben mehrere Vorteile gegenüber herkömmlichen Motoren:
- Sie sind effizienter als Wechselstromlüfter mit Spaltpolmotoren und laufen viel kühler als die entsprechenden Wechselstrommotoren. Dieser kühle Betrieb führt zu einer wesentlich längeren Lebensdauer der Lager des Lüfters.
- Ohne Kommutator kann die Lebensdauer eines BLDC-Motors im Vergleich zu einem bürstenbehafteten Gleichstrommotor mit Kommutator erheblich länger sein. Ohne Kommutator oder Bürsten kann ein BLDC-Motor in elektrisch empfindlichen Geräten wie Audiogeräten oder Computern eingesetzt werden.
- Dieselben Hall-Effekt-Sensoren, die für die Kommutierung sorgen, können ein praktisches Tachometersignal für Anwendungen mit geschlossenem Regelkreis (servogesteuert) liefern. Bei Lüftern kann das Tachometersignal verwendet werden, um ein "Lüfter-OK"-Signal abzuleiten und eine Rückmeldung über die Betriebsgeschwindigkeit zu geben.
- Der Motor kann mit einem internen oder externen Taktgeber synchronisiert werden, was eine präzise Drehzahlregelung ermöglicht.
- BLDC-Motoren sprühen keine Funken, wodurch sie sich besser für Umgebungen mit flüchtigen Chemikalien und Kraftstoffen eignen. Funkenbildung erzeugt auch Ozon, das sich in schlecht belüfteten Gebäuden ansammeln kann.
- BLDC-Motoren werden in der Regel in kleinen Geräten wie Computern und in Lüftern zur Wärmeabfuhr eingesetzt.
- Sie sind geräuscharm, was bei Geräten, die von Vibrationen betroffen sind, ein Vorteil ist. ⓘ
Die Leistung moderner BLDC-Motoren reicht von einem Bruchteil eines Watts bis zu mehreren Kilowatt. Größere BLDC-Motoren mit einer Leistung von bis zu 100 kW werden in Elektrofahrzeugen eingesetzt. Sie werden auch in elektrischen Modellflugzeugen eingesetzt. ⓘ
Geschalteter Reluktanzmotor

Der geschaltete Reluktanzmotor (SRM) hat keine Bürsten oder Dauermagnete, und der Rotor hat keine elektrischen Ströme. Das Drehmoment entsteht durch einen leichten Versatz der Pole des Rotors gegenüber den Polen des Stators. Der Rotor richtet sich auf das Magnetfeld des Stators aus, während die Feldwicklungen des Stators nacheinander erregt werden, um das Statorfeld zu drehen. ⓘ
Der von den Feldwicklungen erzeugte magnetische Fluss folgt dem Weg des geringsten Magnetfeldes und fließt durch die Rotorpole, die den erregten Polen des Stators am nächsten liegen, wodurch diese Pole des Rotors magnetisiert werden und ein Drehmoment entsteht. Wenn sich der Rotor dreht, werden verschiedene Wicklungen erregt, wodurch sich der Rotor weiter dreht. ⓘ
SRMs werden in einigen Geräten und Fahrzeugen eingesetzt. ⓘ
Universeller AC/DC-Motor
Ein kommutierter, elektrisch erregter, in Reihe oder parallel gewickelter Motor wird als Universalmotor bezeichnet, da er sowohl für den Betrieb mit Wechselstrom als auch mit Gleichstrom ausgelegt werden kann. Ein Universalmotor kann gut mit Wechselstrom betrieben werden, da der Strom sowohl in den Feld- als auch in den Ankerspulen (und damit die resultierenden Magnetfelder) die Polarität synchron umkehren, so dass die resultierende mechanische Kraft in einer konstanten Drehrichtung auftritt. ⓘ
Da sie mit normalen Netzfrequenzen arbeiten, werden Universalmotoren häufig für Anwendungen im Sub-Kilowatt-Bereich eingesetzt. Universalmotoren bildeten die Grundlage für den traditionellen Traktionsmotor der elektrischen Eisenbahnen. Bei dieser Anwendung würde die Verwendung von Wechselstrom für einen Motor, der für den Betrieb mit Gleichstrom ausgelegt ist, zu Effizienzverlusten führen, die auf die Wirbelstromerwärmung der magnetischen Komponenten zurückzuführen sind, insbesondere der Polschuhe des Motorfelds, die bei Gleichstrom aus massivem (nicht laminiertem) Eisen bestehen. Sie werden heute nur noch selten verwendet. ⓘ
Ein Vorteil ist, dass Wechselstrom für Motoren verwendet werden kann, die ein hohes Anlaufmoment und eine kompakte Bauweise aufweisen, wenn hohe Drehzahlen verwendet werden. Im Gegensatz dazu ist der Wartungsaufwand höher und die Lebensdauer ist kürzer. Solche Motoren werden in wenig genutzten Geräten eingesetzt, die ein hohes Anlaufmoment benötigen. Mehrere Anzapfungen an der Feldspule ermöglichen eine (ungenaue) stufenweise Drehzahlregelung. Haushaltsmixer, die mit mehreren Geschwindigkeiten werben, kombinieren typischerweise eine Erregerspule mit mehreren Anzapfungen und eine Diode, die in Reihe mit dem Motor geschaltet werden kann (wodurch der Motor mit halbwellengleichgerichteter Wechselspannung läuft). Universalmotoren eignen sich auch für eine elektronische Drehzahlregelung und sind daher eine gute Wahl für Geräte wie Haushaltswaschmaschinen. Der Motor kann die Trommel bewegen (sowohl vorwärts als auch rückwärts), indem er die Feldwicklung in Bezug auf den Anker umschaltet. ⓘ
Während SCIMs eine Welle nicht schneller drehen können, als es die Netzfrequenz zulässt, können Universalmotoren mit viel höheren Geschwindigkeiten laufen. Dies macht sie für Geräte wie Mixer, Staubsauger und Haartrockner nützlich, bei denen eine hohe Geschwindigkeit und ein geringes Gewicht erwünscht sind. Sie werden auch häufig in tragbaren Elektrowerkzeugen wie Bohrmaschinen, Schleifmaschinen, Kreissägen und Stichsägen eingesetzt, wo die Eigenschaften des Motors gut funktionieren. Viele Staubsauger- und Unkrauttrimmermotoren erreichen mehr als 10.000 Umdrehungen pro Minute, während Miniaturschleifmaschinen bis zu 30.000 Umdrehungen pro Minute erreichen können. ⓘ
Extern kommutierte AC-Maschine
Induktions- und Synchronwechselstrommotoren sind für den Betrieb an ein- oder mehrphasigen sinusförmigen oder quasisinusförmigen Stromwellen optimiert, wie sie für Anwendungen mit fester Drehzahl vom Wechselstromnetz oder für Anwendungen mit variabler Drehzahl von frequenzgeregelten Antriebsreglern (VFD) geliefert werden. ⓘ
Induktionsmotor
Ein Induktionsmotor ist ein asynchroner Wechselstrommotor, bei dem die Leistung durch elektromagnetische Induktion auf den Rotor übertragen wird, ähnlich wie bei einem Transformator. Ein Induktionsmotor ähnelt einem rotierenden Transformator, da der Stator (stationärer Teil) im Wesentlichen die Primärseite des Transformators und der Rotor (rotierender Teil) die Sekundärseite darstellt. Mehrphasige Induktionsmotoren sind in der Industrie weit verbreitet.

Käfig und gewickelter Rotor
Induktionsmotoren lassen sich in Käfigläufer-Induktionsmotoren (SCIM) und Wickelrotor-Induktionsmotoren (WRIM) unterteilen. SCIMs haben eine schwere Wicklung aus massiven Stäben, in der Regel Aluminium oder Kupfer, die durch Ringe an den Enden des Rotors elektrisch verbunden sind. Die Stäbe und Ringe als Ganzes ähneln dem rotierenden Käfig eines Tieres. ⓘ
Die in diese Wicklung induzierten Ströme bilden das Magnetfeld des Rotors. Die Form der Rotorstäbe bestimmt die Drehzahl-Drehmoment-Eigenschaften. Bei niedrigen Drehzahlen ist der in den Käfig induzierte Strom fast netzfrequent und verbleibt tendenziell in den äußeren Teilen des Käfigs. Wenn der Motor beschleunigt, wird die Schlupffrequenz niedriger und mehr Strom erreicht das Innere. Indem man die Stäbe so formt, dass sich der Widerstand der Wicklungsabschnitte in den inneren und äußeren Teilen des Käfigs ändert, wird ein variabler Widerstand in den Rotorkreis eingefügt. Die meisten dieser Motoren verwenden jedoch gleichförmige Stäbe. ⓘ
Bei einem WRIM besteht die Rotorwicklung aus vielen Windungen isolierten Drahtes und ist mit Schleifringen auf der Motorwelle verbunden. Ein externer Widerstand oder ein anderes Steuergerät kann in den Rotorkreis geschaltet werden. Widerstände ermöglichen die Steuerung der Motordrehzahl, verbrauchen jedoch viel Strom. Ein Umrichter kann aus dem Rotorkreis gespeist werden und die Schlupffrequenzleistung, die andernfalls verschwendet würde, über einen Wechselrichter oder einen separaten Motor-Generator in das Stromnetz zurückführen. ⓘ
WRIMs werden in erster Linie zum Starten einer Last mit hohem Trägheitsmoment oder einer Last verwendet, die ein hohes Startdrehmoment über den gesamten Drehzahlbereich erfordert. Durch die richtige Auswahl der im Sekundärwiderstand oder Schleifringstarter verwendeten Widerstände kann der Motor bei einem relativ niedrigen Versorgungsstrom von Null bis zur vollen Drehzahl ein maximales Drehmoment erzeugen. ⓘ
Die Motordrehzahl kann geändert werden, da die Drehmomentkurve des Motors durch den an den Rotorkreis angeschlossenen Widerstand effektiv verändert wird. Eine Erhöhung des Widerstands senkt die Drehzahl des maximalen Drehmoments. Wenn der Widerstand über den Punkt hinaus erhöht wird, an dem das maximale Drehmoment bei Drehzahl Null auftritt, verringert sich das Drehmoment weiter. ⓘ
Bei einer Last mit einer Drehmomentkurve, die mit der Drehzahl ansteigt, arbeitet der Motor bei der Drehzahl, bei der das vom Motor entwickelte Drehmoment gleich dem Lastdrehmoment ist. Eine Verringerung der Last führt zu einer Beschleunigung des Motors, während eine Erhöhung der Last zu einer Verlangsamung des Motors führt, bis Last- und Motordrehmoment wieder gleich sind. Bei dieser Betriebsweise werden die Schlupfverluste in den Sekundärwiderständen abgeleitet und können beträchtlich sein. Die Drehzahlregelung und der Nettowirkungsgrad sind schlecht. ⓘ
Torquemotor
Ein Torquemotor kann im blockierten Zustand, d. h. bei blockiertem Rotor, unbegrenzt arbeiten, ohne Schaden zu nehmen. In dieser Betriebsart übt der Motor ein gleichmäßiges Drehmoment auf die Last aus. ⓘ
Eine häufige Anwendung sind die Motoren der Zu- und Abwickelspulen in einem Bandlaufwerk. In dieser Anwendung, die von einer niedrigen Spannung angetrieben wird, üben die Eigenschaften dieser Motoren eine gleichmäßige leichte Spannung auf das Band aus, unabhängig davon, ob die Bandspule das Band an den Bandköpfen vorbeiführt oder nicht. Torquemotoren, die mit einer höheren Spannung betrieben werden (und ein höheres Drehmoment liefern), ermöglichen einen schnellen Vor- und Rücklauf, ohne dass zusätzliche Mechanismen wie Getriebe oder Kupplungen erforderlich sind. In der Welt der Computerspiele werden Torquemotoren in Force-Feedback-Lenkrädern eingesetzt. ⓘ
Eine weitere gängige Anwendung ist die Steuerung der Drosselklappe eines Verbrennungsmotors mit einem elektronischen Regler. Der Motor arbeitet gegen eine Rückstellfeder, um die Drosselklappe in Übereinstimmung mit dem Reglerausgang zu bewegen. Dieser überwacht die Motordrehzahl, indem er elektrische Impulse von der Zündanlage oder von einem magnetischen Aufnehmer zählt und je nach Drehzahl kleine Anpassungen an der Stromstärke vornimmt. Wird der Motor langsamer als die gewünschte Drehzahl, erhöht sich die Stromstärke, wodurch ein größeres Drehmoment erzeugt wird, das gegen die Rückholfeder zieht und die Drosselklappe öffnet. Läuft der Motor zu schnell, reduziert der Regler die Stromstärke, so dass die Rückstellfeder zurückzieht und die Drosselklappe verringert. ⓘ
Synchroner Motor
Ein Synchron-Elektromotor ist ein Wechselstrommotor. Er enthält einen Rotor, der sich mit Spulen dreht, die Magnete mit der gleichen Frequenz wie der Wechselstrom durchlaufen und ein Magnetfeld erzeugen, das ihn antreibt. Unter typischen Betriebsbedingungen hat er keinen Schlupf. Im Gegensatz dazu müssen Induktionsmotoren schlupfen, um ein Drehmoment zu erzeugen. Eine Art von Synchronmotor ist wie ein Induktionsmotor, mit dem Unterschied, dass der Rotor durch ein Gleichfeld erregt wird. Schleifringe und Bürsten leiten den Strom zum Rotor. Die Rotorpole sind miteinander verbunden und bewegen sich mit der gleichen Geschwindigkeit. Bei einem anderen Typ, der für ein geringes Lastdrehmoment ausgelegt ist, sind auf einem herkömmlichen Käfigläufer Flächen geschliffen, um einzelne Pole zu bilden. Ein weiterer Typ, wie er von Hammond für seine Uhren vor dem Zweiten Weltkrieg und in älteren Hammond-Orgeln hergestellt wurde, hat keine Rotorwicklungen und einzelne Pole. Sie ist nicht selbststartend. Die Uhr muss mit einem kleinen Knopf auf der Rückseite manuell gestartet werden, während die älteren Hammond-Orgeln einen Hilfsstartmotor hatten, der über einen federbelasteten, manuell betätigten Schalter angeschlossen war. ⓘ
Hysterese-Synchronmotoren sind typischerweise (im Wesentlichen) Zweiphasenmotoren mit einem Phasenschieberkondensator für eine Phase. Sie starten wie Induktionsmotoren, aber wenn die Schlupfrate ausreichend abnimmt, wird der Rotor (ein glatter Zylinder) vorübergehend magnetisiert. Durch seine verteilten Pole verhält er sich dann wie ein Synchronmotor mit Permanentmagneten. Das Material des Rotors, wie das eines gewöhnlichen Nagels, bleibt magnetisiert, kann aber ohne große Schwierigkeiten entmagnetisiert werden. Einmal in Betrieb, bleiben die Pole des Rotors an ihrem Platz; sie driften nicht. ⓘ
Synchronuhrenmotoren mit geringer Leistung (z. B. für herkömmliche elektrische Uhren) können mehrpolige Permanentmagnet-Außenbecherrotoren haben und verwenden Abschattungsspulen, um ein Startdrehmoment zu erzeugen. Telechron-Uhrenmotoren haben schraffierte Pole für das Anlaufdrehmoment und einen zweispeichigen Ringrotor, der sich wie ein einzelner zweipoliger Rotor verhält. ⓘ
Zweifach gespeiste elektrische Maschine
Doppelt gespeiste Elektromotoren haben zwei unabhängige mehrphasige Wicklungssätze, die Wirkleistung (d. h. Arbeitsleistung) zum Energieumwandlungsprozess beitragen, wobei mindestens einer der Wicklungssätze für den Betrieb mit variabler Drehzahl elektronisch gesteuert wird. Zwei unabhängige mehrphasige Wicklungssätze (d. h. Doppelanker) sind das Maximum, das in einem einzigen Gehäuse ohne Topologiedopplung möglich ist. Zweifach gespeiste Elektromotoren haben einen effektiven Drehzahlbereich mit konstantem Drehmoment, der bei einer gegebenen Erregerfrequenz das Doppelte der Synchrondrehzahl beträgt. Dieser Bereich ist doppelt so groß wie der Bereich der konstanten Drehmomentdrehzahl im Vergleich zu einfach gespeisten Elektromaschinen, die nur einen aktiven Wicklungssatz haben. ⓘ
Ein doppelt gespeister Motor ermöglicht einen kleineren elektronischen Umrichter, aber die Kosten für die Rotorwicklung und die Schleifringe können die Einsparungen bei den Komponenten der Leistungselektronik ausgleichen. Bei Anwendungen mit synchroner Drehzahlbegrenzung gibt es Schwierigkeiten bei der Drehzahlregelung. ⓘ
Spezielle Magnetmotoren
Drehend
Eisenloser oder kernloser Rotormotor

Der kernlose oder eisenlose Gleichstrommotor ist ein spezieller Permanentmagnet-Gleichstrommotor. Der für schnelle Beschleunigung optimierte Rotor ist ohne Eisenkern aufgebaut. Der Rotor kann die Form eines mit Wicklungen gefüllten Zylinders oder einer selbsttragenden Struktur haben, die nur aus Draht und Bindematerial besteht. Der Rotor kann in die Statormagnete eingepasst werden; ein weichmagnetischer stationärer Zylinder im Inneren des Rotors sorgt für die Rückführung des magnetischen Flusses des Stators. Bei einer zweiten Anordnung umgibt der Rotorwicklungskorb die Statormagnete. Bei dieser Konstruktion sitzt der Rotor in einem weichmagnetischen Zylinder, der als Motorgehäuse dienen kann, und bietet einen Rückflussweg für den Magnetfluss. ⓘ
Da der Rotor eine viel geringere Masse hat als ein herkömmlicher Rotor, kann er viel schneller beschleunigen und erreicht oft eine mechanische Zeitkonstante von unter einer Millisekunde. Dies gilt insbesondere, wenn die Wicklungen aus Aluminium und nicht aus (schwererem) Kupfer bestehen. Der Rotor hat keine Metallmasse, die als Wärmesenke dienen könnte; selbst kleine Motoren müssen gekühlt werden. Überhitzung kann bei diesen Konstruktionen ein Problem sein. ⓘ
Der Vibrationsalarm von Mobiltelefonen kann von zylindrischen Permanentmagnetmotoren oder scheibenförmigen Motoren mit einem dünnen mehrpoligen Scheibenmagneten und einer absichtlich unausgewogenen Rotorstruktur aus geformtem Kunststoff mit zwei miteinander verbundenen kernlosen Spulen erzeugt werden. Metallbürsten und ein flacher Kommutator schalten den Strom zu den Rotorspulen. ⓘ
Ähnliche Aktuatoren mit begrenztem Hub haben keinen Kern und eine geklebte Spule, die zwischen den Polen von dünnen Hochfluss-Permanentmagneten angeordnet ist. Dies sind die schnellen Kopfpositionierer für Starrplattenlaufwerke ("Festplatten"). Obwohl sich das heutige Design erheblich von dem von Lautsprechern unterscheidet, wird es immer noch grob (und fälschlicherweise) als "Schwingspulen"-Struktur bezeichnet, da sich einige frühere Festplattenlaufwerke in geraden Linien bewegten und eine Antriebsstruktur hatten, die der eines Lautsprechers sehr ähnlich war. ⓘ
Pancake- oder Axialrotormotor
Der gedruckte Anker oder Pancake-Motor hat scheibenförmige Wicklungen, die zwischen Anordnungen von Hochflussmagneten laufen. Die Magnete sind in einem Kreis angeordnet, der dem Rotor zugewandt ist und einen axialen Luftspalt bildet. Diese Bauart ist wegen ihres flachen Profils allgemein als Pfannkuchenmotor bekannt. ⓘ
Der Anker (ursprünglich auf einer Leiterplatte) besteht aus gestanzten Kupferblechen, die mit modernen Verbundwerkstoffen zu einer dünnen, starren Scheibe zusammenlaminiert werden. Der Anker verfügt nicht über einen separaten Ringkommutator. Die Bürsten bewegen sich direkt auf der Oberfläche des Ankers, wodurch die gesamte Konstruktion kompakt ist. ⓘ
Eine alternative Konstruktion ist die Verwendung von gewickeltem Kupferdraht, der flach mit einem zentralen konventionellen Kommutator in Form einer Blume oder eines Blütenblattes verlegt wird. Die Wicklungen werden in der Regel mit elektrischen Epoxid-Vergusssystemen stabilisiert. Dabei handelt es sich um gefüllte Epoxidharze mit mittlerer Mischviskosität und langer Gelierzeit. Sie zeichnen sich durch eine geringe Schrumpfung und eine niedrige Exothermie aus und sind in der Regel nach UL 1446 als isolierte Vergussmasse mit einer Temperatur von 180 °C (356 °F), Klasse H, zugelassen. ⓘ
Der einzigartige Vorteil von eisenlosen Gleichstrommotoren ist das Fehlen von Cogging (Drehmomentschwankungen, die durch die wechselnde Anziehung zwischen Eisen und Magneten verursacht werden). Im Rotor können sich keine parasitären Wirbelströme bilden, da er völlig eisenlos ist, obwohl Eisenrotoren laminiert sind. Dies kann den Wirkungsgrad erheblich verbessern, doch müssen drehzahlvariable Regler wegen der geringeren elektromagnetischen Induktion eine höhere Schaltfrequenz (>40 kHz) oder Gleichstrom verwenden. ⓘ
Diese Motoren wurden für den Antrieb der Capstan(s) von Magnetbandlaufwerken erfunden, bei denen eine minimale Zeit bis zum Erreichen der Betriebsgeschwindigkeit und ein minimaler Bremsweg entscheidend waren. Pancake-Motoren werden häufig in hochleistungsfähigen servogesteuerten Systemen, Robotersystemen, industrieller Automatisierung und medizinischen Geräten eingesetzt. Aufgrund der Vielfalt der heute verfügbaren Konstruktionen wird die Technologie in Anwendungen eingesetzt, die von militärischen Hochtemperaturanwendungen bis hin zu kostengünstigen Pumpen und einfachen Servomotoren reichen. ⓘ
Ein anderer Ansatz (Magnax) besteht in der Verwendung eines einzelnen Stators, der zwischen zwei Rotoren eingebettet ist. Eine solche Konstruktion hat eine Spitzenleistung von 15 kW/kg und eine Dauerleistung von etwa 7,5 kW/kg erreicht. Dieser yoklose Axialflussmotor bietet einen kürzeren Flussweg, da die Magnete weiter von der Achse entfernt sind. Die Konstruktion ermöglicht einen Wicklungsüberhang von Null; 100 Prozent der Wicklungen sind aktiv. Dies wird durch die Verwendung von Kupferdraht mit rechteckigem Querschnitt noch verbessert. Die Motoren können gestapelt werden, um parallel zu arbeiten. Instabilitäten werden minimiert, indem sichergestellt wird, dass die beiden Rotorscheiben gleiche und entgegengesetzte Kräfte auf die Statorscheibe ausüben. Die Rotoren sind über einen Wellenring direkt miteinander verbunden, wodurch sich die magnetischen Kräfte aufheben. ⓘ
Die Magnax-Motoren haben einen Durchmesser von 0,15 bis 5,4 Metern (5,9 in - 17 ft 8,6 in). ⓘ
Servomotor
Ein Servomotor ist ein Motor, der in einem System zur Positions- oder Geschwindigkeitsregelung eingesetzt wird. Servomotoren werden in Anwendungen wie Werkzeugmaschinen, Stiftplottern und anderen Prozesssystemen eingesetzt. Motoren, die für den Einsatz in einem Servomechanismus vorgesehen sind, müssen vorhersehbare Eigenschaften für Drehzahl, Drehmoment und Leistung aufweisen. Die Drehzahl-Drehmoment-Kurve ist wichtig und hat bei einem Servomotor ein hohes Verhältnis. Dynamische Eigenschaften wie Wicklungsinduktivität und Rotorträgheit sind wichtig; diese Faktoren begrenzen die Leistung. Große, leistungsstarke, aber langsam reagierende Servoschleifen können konventionelle AC- oder DC-Motoren und Antriebssysteme mit Positions- oder Geschwindigkeitsrückführung verwenden. Wenn die Anforderungen an die Dynamik steigen, werden speziellere Motorkonstruktionen wie kernlose Motoren verwendet. Die überlegene Leistungsdichte und die Beschleunigungseigenschaften von AC-Motoren sprechen für Permanentmagnet-Synchron-, BLDC-, Induktions- und SRM-Antriebskonzepte. ⓘ
Ein Servosystem unterscheidet sich von einigen Schrittmotoranwendungen dadurch, dass die Positionsrückmeldung kontinuierlich erfolgt, während der Motor läuft. Ein Schrittmotorsystem arbeitet von Natur aus mit offenem Regelkreis, d. h. es verlässt sich darauf, dass der Motor keine Schritte verpasst, um eine kurzfristige Genauigkeit zu erreichen, wobei jegliche Rückmeldung, wie z. B. ein "Home"-Schalter oder ein Positionsgeber, außerhalb des Motorsystems erfolgt. ⓘ
Schrittmotor

Schrittmotoren werden in der Regel verwendet, um präzise Drehungen zu ermöglichen. Ein Innenrotor mit Permanentmagneten oder ein weichmagnetischer Rotor mit ausgeprägten Polen wird von einem Satz elektronisch geschalteter Außenmagnete gesteuert. Ein Schrittmotor kann auch als eine Kreuzung zwischen einem Gleichstrommotor und einem Drehmagneten betrachtet werden. Wenn jede Spule nacheinander erregt wird, richtet sich der Rotor auf das von der erregten Feldwicklung erzeugte Magnetfeld aus. Im Gegensatz zu einem Synchronmotor dreht sich der Schrittmotor nicht kontinuierlich, sondern bewegt sich schrittweise von einer Position zur nächsten, indem die Feldwicklungen nacheinander erregt und entregt werden. Je nach Sequenz kann sich der Rotor vorwärts oder rückwärts drehen, er kann jederzeit die Richtung ändern, anhalten, beschleunigen oder verlangsamen. ⓘ
Einfache Schrittmotortreiber schalten die Feldwicklungen vollständig ein oder aus, was dazu führt, dass der Rotor eine begrenzte Anzahl von Positionen ansteuert. Mikroschritttreiber können die Leistung der Feldwicklungen proportional steuern, so dass die Rotoren zwischen den Zahnradpunkten positioniert werden können und sich gleichmäßig drehen. Computergesteuerte Schrittmotoren sind eines der vielseitigsten Positioniersysteme, insbesondere als Teil eines digitalen servogesteuerten Systems. ⓘ
Schrittmotoren können problemlos in diskreten Schritten auf einen bestimmten Winkel gedreht werden. Daher wurden Schrittmotoren für die Positionierung von Lese-/Schreibköpfen in frühen Festplattenlaufwerken verwendet, wo sie aufgrund ihrer Präzision und Geschwindigkeit den Lese-/Schreibkopf korrekt positionieren konnten. Mit zunehmender Laufwerksdichte wurden sie aufgrund von Präzisions- und Geschwindigkeitseinschränkungen für Festplattenlaufwerke überflüssig - die Präzisionseinschränkung machte sie unbrauchbar und die Geschwindigkeitseinschränkung machte sie nicht mehr wettbewerbsfähig -, weshalb neuere Festplattenlaufwerke auf Schwingspulen basierende Kopfstellsysteme verwenden. (Der Begriff "Schwingspule" ist in diesem Zusammenhang historisch bedingt; er bezieht sich auf die Struktur eines Kegellautsprechers.) ⓘ
Schrittmotoren werden häufig in Computerdruckern, optischen Scannern und digitalen Fotokopierern verwendet, um das aktive Element, den Druckkopfschlitten (Tintenstrahldrucker) und die Druckwalze oder die Vorschubwalzen zu bewegen. ⓘ
Sogenannte analoge Quarzarmbanduhren enthalten die kleinsten handelsüblichen Schrittmotoren; sie haben eine Spule, verbrauchen wenig Strom und haben einen Permanentmagnetrotor. Die gleiche Art von Motor treibt batteriebetriebene Quarzuhren an. Einige dieser Uhren, z. B. Chronographen, enthalten mehr als einen Schrittmotor. ⓘ
Schrittmotoren und SRM sind konstruktiv eng mit den Drehstrom-Synchronmotoren verwandt und werden als Motoren mit variabler Reluktanz eingestuft. ⓘ
Linearmotor
Bei einem Linearmotor handelt es sich im Wesentlichen um einen Elektromotor, der so "abgerollt" wurde, dass er statt eines Drehmoments (Rotation) eine geradlinige Kraft entlang seiner Länge erzeugt. ⓘ
Bei Linearmotoren handelt es sich in der Regel um Induktionsmotoren oder Schrittmotoren. Linearmotoren werden häufig in Achterbahnen eingesetzt, wo die schnelle Bewegung des motorlosen Triebwagens durch die Schiene gesteuert wird. Sie werden auch in Magnetschwebebahnen eingesetzt, bei denen der Zug über den Boden "fliegt". In kleinerem Maßstab verwendete der HP 7225A Stiftplotter aus dem Jahr 1978 zwei lineare Schrittmotoren, um den Stift entlang der X- und Y-Achse zu bewegen. ⓘ
Vergleich nach Hauptkategorien
Typ | Vorteile | Nachteile | Typische Anwendung | Typischer Antrieb, Ausgang ⓘ |
---|---|---|---|---|
Selbstkommutierte Motoren | ||||
Gebürsteter DC | Einfache Drehzahlregelung
Niedrige Anschaffungskosten |
Wartung (Bürsten)
Mittlere Lebenserwartung Teurer Kommutator und Bürsten |
Stahlwerke
Maschinen zur Papierherstellung Laufband-Trainingsgeräte Automobilzubehör |
Gleichrichter, Lineartransistor(en) oder DC-Chopper-Regler. |
Bürstenloser Gleichstrommotor (BLDC oder BLDM) | Lange Lebensdauer
Geringe Wartung Hoher Wirkungsgrad |
Höhere Anschaffungskosten
Erfordert EC-Controller mit geschlossenem Regelkreis |
Starre ("harte") Festplattenlaufwerke
CD/DVD-Spieler Elektrische Fahrzeuge RC-Fahrzeuge UAVs |
Synchron; einphasig oder dreiphasig mit PM-Rotor und trapezförmiger Statorwicklung; VFD typischerweise vom Typ VS PWM-Inverter. |
Geschalteter Reluktanzmotor (SRM) | Lange Lebensdauer
Geringe Wartung Hoher Wirkungsgrad Keine Permanentmagnete Niedrige Kosten Einfache Konstruktion |
Mechanische Resonanz
möglich Hohe Eisenverluste Nicht möglich: * Offene oder vektorielle Steuerung * Parallelbetrieb Erfordert EC-Controller |
Haushaltsgeräte
Elektrische Fahrzeuge Textilfabriken Anwendungen in Flugzeugen |
PWM und verschiedene andere Antriebsarten, die in der Regel in spezialisierten / OEM-Anwendungen verwendet werden. |
Universalmotor | Hohes Anlaufmoment, kompakt, hohe Drehzahl. | Wartung (Bürsten)
Kürzere Lebensdauer In der Regel akustische Geräusche Nur kleine Leistungen sind wirtschaftlich |
Handgeführte Elektrowerkzeuge, Mixer, Staubsauger, Isoliergebläse | Variabler Einphasen-Wechselstrom, Halbwellen- oder Vollwellen-Phasenanschnittsteuerung mit Triac(s); Regelung optional. |
AC-Asynchronmotoren | ||||
AC mehrphasig
Kurzschlusskäfig oder gewickelter Läufer Induktionsmotor (SCIM) oder (WRIM) |
Selbstanlaufend
Kostengünstig Robust Zuverlässig Leistungen bis 1+ MW Standardisierte Typen. |
Hoher Anlaufstrom
Geringerer Wirkungsgrad wegen der Notwendigkeit für Magnetisierung. |
Festdrehzahl, traditionell, SCIM das Arbeitspferd der Welt, insbesondere bei Anwendungen mit geringer Leistung aller Art
Variable Drehzahl, traditionell, Pumpen, Ventilatoren, Gebläse und Kompressoren mit niedrigem Drehmoment. Variable Drehzahlen, zunehmend auch für andere Hochleistungsanwendungen mit konstantem Drehmoment und konstanter Leistung oder dynamische Lasten. |
Anwendungen mit fester Drehzahl und geringer Leistung aller Art.
Drehzahlvariable Antriebe, traditionell WRIM-Antriebe oder V/Hz-gesteuerte Umrichter mit fester Drehzahl. Drehzahlvariable, zunehmend vektorgeregelte FU, die DC-, WRIM- und einphasige AC-Asynchronmotorantriebe verdrängen. |
AC SCIM
Spaltphase Kondensator-Start |
Hohe Leistung
hohes Anlaufmoment |
Drehzahl etwas unter der Synchrondrehzahl
Startschalter oder Relais erforderlich |
Geräte
Stationäre Elektrowerkzeuge |
Einphasiger Wechselstrom mit fester oder variabler Drehzahl, wobei die variable Drehzahl in der Regel durch Vollwellen-Phasenanschnittsteuerung mit Triac(s) abgeleitet wird; Regelung optional. |
AC SCIM
phasengeteilt kondensatorbetrieben |
Mäßige Leistung
Hohes Anlaufmoment Kein Startschalter Vergleichsweise lange Lebensdauer |
Drehzahl etwas unter der des Synchronantriebs
Geringfügig teurer |
Industriegebläse
Industrielle Maschinen | |
AC SCIM
phasengeteilt, Hilfsspannung Startwicklung |
Mäßige Leistung
Niedriges Anlaufmoment |
Drehzahl etwas unter der Synchrondrehzahl
Startschalter oder Relais erforderlich |
Geräte
Stationäre Elektrowerkzeuge | |
AC-Induktionsspaltpolmotor
Motor |
Niedrige Kosten
Lange Lebensdauer |
Drehzahl etwas unter der des Synchronmotors
Geringes Anlaufmoment Kleine Leistungen geringer Wirkungsgrad |
Ventilatoren, Geräte, Plattenspieler | |
AC-Synchronmotoren | ||||
Wickelrotor-Synchronmotor (WRSM) | Synchrone Drehzahl
Inhärent effizienter Induktionsmotor, niedriger Leistungsfaktor |
Teurer | Industrielle Motoren | Feste oder variable Drehzahl, dreiphasig; VFD typischerweise sechsstufiger, lastgeführter CS-Umrichtertyp oder VS-PWM-Umrichtertyp. |
Hysteresemotor | Präzise Drehzahlregelung
Geräuscharm Keine Vibrationen Hohes Anlauf Drehmoment |
Sehr niedriger Wirkungsgrad | Uhren, Zeitschaltuhren, Tonerzeugungs- oder Aufzeichnungsgeräte, Festplattenlaufwerke, Capstan-Antriebe | Einphasen-Wechselstrommotor, Zweiphasen-Kondensatorstartmotor, Kondensatorlaufmotor |
Synchroner Reluktanzmotor (SyRM) | Äquivalent zu SCIM
jedoch robuster, effizienter, kühler, kleinerer Platzbedarf Konkurriert mit PM-Synchronmotor ohne Entmagnetisierungsprobleme |
Erfordert eine Steuerung
Nicht allgemein verfügbar Hohe Kosten |
Haushaltsgeräte
Elektrische Fahrzeuge Textilfabriken Anwendungen in Flugzeugen |
VFD können als Standard-DTC-Typ oder als VS-Inverter-PWM-Typ ausgeführt sein. |
Spezialisierte Motoren | ||||
Pancake- oder Axialrotormotoren | Kompakte Bauweise
Einfache Drehzahlregelung |
Mittlere Kosten
Mittlere Lebenserwartung |
Bürogeräte
Lüfter/Pumpen, schnelle Industrie- und Militärservos |
Antriebe können typischerweise bürstenbehaftete oder bürstenlose Gleichstromantriebe sein. |
Schrittmotor | Präzise Positionierung
Hohes Haltedrehmoment |
Einige können kostspielig sein
Erfordern eine Steuerung |
Positionierung in Druckern und Diskettenlaufwerken; industrielle Werkzeugmaschinen | Kein VFD. Die Stepperposition wird durch Impulszählung bestimmt. |
Elektromagnetismus
Kraft und Drehmoment
Ein Elektromotor wandelt elektrische Energie durch die Kraft zwischen zwei entgegengesetzten Magnetfeldern in mechanische Energie um. Mindestens eines der beiden Magnetfelder muss durch einen Elektromagneten erzeugt werden, und zwar durch das Magnetfeld, das durch eine elektrische Ladung in Bewegung entsteht. Die erzeugte Kraft wird genutzt, um eine Masse zu beschleunigen und eine lineare oder rotierende Bewegung zu erzeugen. ⓘ
Nach dem Lorentz-Kraftgesetz ist die Kraft zwischen einem Strom I in einem Leiter der Länge l senkrecht ( x ) zu einem Magnetfeld B:
Anmerkung: X bedeutet nicht die einfache Multiplikation, sondern ist eine kompaktere Darstellung von F=I l B sin(θ), wobei θ der Winkel zwischen dem Leiter und dem Magnetfeld ist. Allgemeiner, ohne Berücksichtigung der Geometrie des Leiters, ergibt sich die Kraft aus der Ladung, die sich senkrecht zu einem Magnetfeld bewegt:
Die allgemeinsten Ansätze zur Berechnung der Kräfte in Motoren verwenden die Tensornotation, die auch als Vektorschreibweise bekannt ist. ⓘ
Leistung
Die mechanische Leistung Pem eines Motors, bei der die Drehzahl die Wellendrehzahl und T das Drehmoment ist, wird wie folgt angegeben, ⓘ
in britischen Einheiten, wobei T in Fuß-Pfund ausgedrückt wird, ⓘ
- (Pferdestärken), und, ⓘ
in SI-Einheiten, wobei die Winkeldrehzahl der Welle in Radiant pro Sekunde und T in Newtonmeter ausgedrückt wird, ⓘ
- (Watt). ⓘ
Bei einem Linearmotor wird die Kraft F in Newton und die Geschwindigkeit v in Metern pro Sekunde ausgedrückt, ⓘ
- (Watt). ⓘ
Bei einem Asynchron- oder Induktionsmotor ist die Beziehung zwischen Motordrehzahl und Luftspaltleistung wie folgt gegeben:
- wobei
- Rr - Rotorwiderstand
- Ir2 - Quadrat des im Rotor induzierten Stroms
- s - Motorschlupf, d. h. die Differenz zwischen der Synchrondrehzahl und der Schlupfdrehzahl, die die für die Strominduktion im Rotor erforderliche Relativbewegung bewirkt. ⓘ
Gegen-EMK
Die Bewegung der Ankerwicklungen eines Gleichstrom- oder Universalmotors durch ein Magnetfeld induziert in ihnen eine Spannung. Diese Spannung wirkt der Versorgungsspannung des Motors entgegen und wird daher als "elektromotorische Gegenkraft (EMK)" bezeichnet. Die Spannung ist proportional zur Drehzahl des Motors. Die Gegen-EMK des Motors plus der Spannungsabfall über den Innenwiderstand der Wicklung und die Bürsten muss der Spannung an den Bürsten entsprechen. Dies ist der grundlegende Mechanismus der Drehzahlregelung in einem Gleichstrommotor. Erhöht sich die mechanische Belastung, wird der Motor langsamer; es entsteht eine niedrigere Gegen-EMK, und es wird mehr Strom aus der Versorgung entnommen. Dieser höhere Strom liefert das zusätzliche Drehmoment, um die Last auszugleichen. ⓘ
Bei AC-Maschinen ist es manchmal sinnvoll, eine Gegen-EMK-Quelle innerhalb der Maschine zu berücksichtigen; dies ist besonders wichtig für die enge Drehzahlregelung von Induktionsmotoren an VFDs. ⓘ
Verluste
Motorverluste sind in erster Linie auf Widerstandsverluste in den Wicklungen, Kernverluste und mechanische Verluste in den Lagern zurückzuführen; außerdem treten aerodynamische Verluste auf, insbesondere wenn Kühlgebläse vorhanden sind. ⓘ
Verluste treten auch bei der Kommutierung auf: mechanische Kommutatoren erzeugen Funken; elektronische Kommutatoren geben ebenfalls Wärme ab. ⓘ
Wirkungsgrad
Technologisch veraltete Elektromotoren führen zu einem erhöhten Energieverbrauch. 1998 wurde eine freiwillige Vereinbarung zwischen dem europäischen Sektorkomitee für elektrische Antriebe CEMEP und der Europäischen Kommission getroffen. In dieser heute veralteten Vereinbarung wurden drei Wirkungsgradklassen definiert:
- EFF3 = Motoren mit niedrigem Wirkungsgrad
- EFF2 = Motoren mit verbessertem Wirkungsgrad
- EFF1 = Motoren mit erhöhtem Wirkungsgrad ⓘ
Im Jahr 2009 wurde eine neue weltweit geltende Normierung für die Effizienzklassen (EN 60034-30:2009) eingeführt. Die folgenden Wirkungsgradklassen für Niederspannungs-Drehstrom-Asynchronmotoren im Leistungsbereich von 0,75 kW bis 375 kW sind heute geltend:
- IE1 = Standard Wirkungsgrad (vergleichbar EFF2, Vertrieb seit Juni 2011 nur noch eingeschränkt gestattet)
- IE2 = Hoher Wirkungsgrad (vergleichbar EFF1)
- IE3 = Premium Wirkungsgrad
- IE4 = Super Premium (> 97 % realisiert)
- IE5 = Ultra Premium ⓘ
Seit 16. Juni 2011 dürfen ungeregelte Motoren (0,75–375 kW) nur noch ab Leistungsklasse IE2 in Verkehr gebracht werden. Der Anteil hocheffizienter Motoren soll stetig ausgebaut werden. Beispiele sind die permanenterregten Synchronmotoren mit höchsten Wirkungsgraden. ⓘ
Ab dem 1. Juli 2021 dürfen ungeregelte Motoren (0,75–375 kW) nur noch ab Leistungsklasse IE3 in Verkehr gebracht werden. ⓘ
Um den Wirkungsgrad eines Motors zu berechnen, wird die mechanische Ausgangsleistung durch die elektrische Eingangsleistung geteilt:
- , ⓘ
wobei der Wirkungsgrad der Energieumwandlung ist, die elektrische Eingangsleistung und die mechanische Ausgangsleistung ist:
wobei ist die Eingangsspannung, Eingangsstrom ist, ist das Ausgangsdrehmoment, und ist die Ausgangs-Winkelgeschwindigkeit. Es ist möglich, den Punkt des maximalen Wirkungsgrads analytisch abzuleiten. Er liegt in der Regel bei weniger als der Hälfte des Stillstandsdrehmoments. ⓘ
Verschiedene nationale Regulierungsbehörden haben Gesetze erlassen, um die Herstellung und Verwendung von Motoren mit höherem Wirkungsgrad zu fördern. Elektromotoren haben einen Wirkungsgrad von mindestens 15 % bei Spaltpolmotoren und bis zu 98 % bei Permanentmagnetmotoren, wobei der Wirkungsgrad auch von der Last abhängt. Der Spitzenwirkungsgrad liegt normalerweise bei 75 % der Nennlast. So ist (als Beispiel) ein 10-PS-Motor am effizientesten, wenn er eine Last antreibt, die 7,5 PS erfordert. Der Wirkungsgrad hängt auch von der Motorgröße ab; größere Motoren sind tendenziell effizienter. Einige Motoren können nicht über einen bestimmten Zeitraum hinweg kontinuierlich betrieben werden (z. B. länger als eine Stunde pro Lauf). ⓘ
Gütefaktor
Eric Laithwaite schlug eine Kennzahl zur Bestimmung der "Güte" eines Elektromotors vor: ⓘ
Wobei:
- der Gütefaktor ist (Faktoren über 1 sind wahrscheinlich effizient)
- sind die Querschnittsflächen des magnetischen und des elektrischen Kreises
- sind die Längen des magnetischen und des elektrischen Kreises
- ist die Permeabilität des Kerns
- ist die Winkelfrequenz, mit der der Motor angetrieben wird ⓘ
Daraus ergibt sich, dass die effizientesten Motoren wahrscheinlich relativ große Magnetpole haben. Die Gleichung bezieht sich jedoch nur direkt auf Nicht-PM-Motoren. ⓘ
Leistungsparameter
Drehmoment
Elektromagnetische Motoren leiten das Drehmoment aus dem Vektorprodukt der interagierenden Felder ab. Die Berechnung des Drehmoments erfordert die Kenntnis der Felder im Luftspalt. Sind diese bekannt, ist das Drehmoment das Integral aller Kraftvektoren multipliziert mit dem Radius des Vektors. Der in der Wicklung fließende Strom erzeugt die Felder. Bei einem Motor, der ein magnetisches Material verwendet, ist das Feld nicht proportional zum Strom. ⓘ
Eine Zahl, die den Strom mit dem Drehmoment in Beziehung setzt, kann bei der Auswahl des Motors helfen. Das maximale Drehmoment eines Motors hängt vom maximalen Strom ab, wobei thermische Überlegungen nicht berücksichtigt werden. ⓘ
Bei optimaler Auslegung innerhalb einer gegebenen Kernsättigungsbeschränkung und für einen gegebenen Wirkstrom (d. h. Drehmomentstrom), Spannung, Polpaarzahl, Erregerfrequenz (d. h. Synchrondrehzahl) und Luftspaltflussdichte weisen alle Kategorien von Elektromotoren/Generatoren praktisch das gleiche maximale kontinuierliche Wellendrehmoment (d. h. Betriebsdrehmoment) innerhalb einer gegebenen Luftspaltfläche mit Wicklungsschlitzen und Rückeisentiefe auf, die die physikalische Größe des elektromagnetischen Kerns bestimmt. Einige Anwendungen erfordern Drehmomentstöße, die über das maximale Drehmoment hinausgehen, z. B. zum Beschleunigen eines Elektrofahrzeugs aus dem Stillstand. Die Kapazität für Drehmomentstöße, die über das Maximum hinausgehen, ist immer durch die Sättigung des Magnetkerns oder den sicheren Betriebstemperaturanstieg und die Spannung begrenzt und unterscheidet sich je nach Motor-/Generatortyp erheblich. ⓘ
Elektrische Maschinen ohne Transformatorschaltkreis-Topologie, wie z. B. WRSMs oder PMSMs, können keine Drehmomentstöße liefern, ohne dass der Magnetkern gesättigt wird. An diesem Punkt kann zusätzlicher Strom das Drehmoment nicht erhöhen. Außerdem kann die Dauermagnetanordnung von PMSMs irreparabel beschädigt werden. ⓘ
Elektrische Maschinen mit einer Transformatorschaltkreistopologie, wie z. B. Induktionsmaschinen, doppelt gespeiste Induktionsmaschinen und doppelt gespeiste Induktions- oder Synchronmaschinen mit gewickeltem Rotor (WRDF), ermöglichen Drehmomentstöße, da die durch EMF induzierten Wirkströme auf beiden Seiten des Transformators einander entgegengesetzt sind und somit nichts zur transformatorisch gekoppelten magnetischen Kernflussdichte beitragen, wodurch eine Kernsättigung vermieden wird. ⓘ
Elektrische Maschinen, die auf Induktions- oder Asynchronprinzipien beruhen, schließen einen Anschluss des Transformatorstromkreises kurz, was zur Folge hat, dass die Blindimpedanz des Transformatorstromkreises mit zunehmendem Schlupf dominant wird, was die Größe des aktiven (d. h. realen) Stroms begrenzt. Drehmomentstöße, die zwei- bis dreimal so hoch sind wie das maximale Auslegungsdrehmoment, sind realisierbar. ⓘ
Die bürstenlose Synchronmaschine mit gewickeltem Rotor und Doppelspeisung (BWRSDF) ist die einzige elektrische Maschine mit einer echten Transformatorschaltkreistopologie mit zwei Anschlüssen (d. h. beide Anschlüsse werden unabhängig voneinander erregt und es gibt keinen kurzgeschlossenen Anschluss). Die Topologie des Transformatorstromkreises mit zwei Anschlüssen ist bekanntermaßen instabil und erfordert eine mehrphasige Schleifringbürstenanordnung, um eine begrenzte Leistung an den Rotorwicklungssatz weiterzuleiten. Wenn eine Präzisionseinrichtung zur Verfügung stünde, die den Drehmomentwinkel und den Schlupf für den Synchronbetrieb während des Betriebs sofort regelt und gleichzeitig den Rotorwicklungssatz mit bürstenlosem Strom versorgt, wäre der Wirkstrom der BWRSDF-Maschine unabhängig von der Blindimpedanz des Transformatorstromkreises, und Drehmomentstöße, die deutlich über dem maximalen Betriebsdrehmoment liegen und weit über die praktischen Möglichkeiten jedes anderen elektrischen Maschinentyps hinausgehen, wären realisierbar. Es wurden Drehmomentstöße berechnet, die mehr als das Achtfache des Betriebsdrehmoments betragen. ⓘ
Kontinuierliche Drehmomentdichte
Die Dauerdrehmomentdichte konventioneller elektrischer Maschinen wird durch die Größe der Luftspaltfläche und die Tiefe des Gegeneisens bestimmt, die durch die Nennleistung des Ankerwicklungssatzes, die Drehzahl der Maschine und die erreichbare Luftspaltflussdichte vor der Kernsättigung bestimmt werden. Trotz der hohen Koerzitivfeldstärke von Neodym- oder Samarium-Kobalt-Permanentmagneten ist die Dauerdrehmomentdichte bei elektrischen Maschinen mit optimal ausgelegten Ankerwicklungssätzen praktisch gleich. Die Dauerdrehmomentdichte bezieht sich auf die Art der Kühlung und die zulässige Betriebsdauer vor Zerstörung durch Überhitzung der Wicklungen oder Beschädigung des Dauermagneten. ⓘ
Andere Quellen geben an, dass verschiedene E-Maschinen-Topologien unterschiedliche Drehmomentdichten aufweisen. Eine Quelle zeigt das Folgende:
Typ der elektrischen Maschine | Spezifische Drehmomentdichte (Nm/kg) ⓘ |
---|---|
SPM - bürstenloser Wechselstrom, 180° Stromführung | 1.0 |
SPM - bürstenloser Wechselstrom, 120° Stromführung | 0.9–1.15 |
IM, Asynchronmaschine | 0.7–1.0 |
IPM, Innenraum-Permanentmagnetmaschine | 0.6–0.8 |
VRM, doppelt ausgeprägte Reluktanzmaschine | 0.7–1.0 |
wobei die spezifische Drehmomentdichte für die bürstenlose Wechselstrommaschine mit Oberflächen-Permanentmagnet (SPM) und 180° Stromrichtung auf 1,0 normiert ist. ⓘ
Die Drehmomentdichte ist bei flüssigkeitsgekühlten Motoren etwa viermal so hoch wie bei luftgekühlten Motoren. ⓘ
Eine Quelle, die Gleichstrom, Induktionsmotoren (IM), PMSM und SRM vergleicht:
Kennlinie | Gleichstrom | IM | PMSM | SRM ⓘ |
---|---|---|---|---|
Drehmomentdichte | 3 | 3.5 | 5 | 4 |
Leistungsdichte | 3 | 4 | 5 | 3.5 |
Eine andere Quelle stellt fest, dass PMSM bis zu 1 MW eine wesentlich höhere Drehmomentdichte haben als Induktionsmaschinen. ⓘ
Kontinuierliche Leistungsdichte
Die Dauerleistungsdichte wird durch das Produkt aus der Dauerdrehmomentdichte und dem Drehzahlbereich mit konstantem Drehmoment bestimmt. Elektromotoren können Dichten von bis zu 20KW/KG erreichen, was 20 Kilowatt Ausgangsleistung pro Kilogramm bedeutet. ⓘ
Akustische Geräusche und Vibrationen
Akustische Geräusche und Vibrationen werden in der Regel in drei Quellen unterteilt:
- mechanische Quellen (z. B. durch Lager)
- aerodynamische Quellen (z. B. durch auf der Welle montierte Ventilatoren)
- magnetische Quellen (z. B. aufgrund von Magnetkräften wie Maxwell- und Magnetostriktionskräften, die auf Stator- und Rotorstrukturen wirken) ⓘ
Die letztgenannte Quelle, die für das "heulende Geräusch" von Elektromotoren verantwortlich sein kann, wird als elektromagnetisch induziertes akustisches Geräusch bezeichnet. ⓘ
Normen
Im Folgenden sind die wichtigsten Konstruktions-, Herstellungs- und Prüfnormen für Elektromotoren aufgeführt:
- American Petroleum Institute: API 541 Form-Wound Squirrel Cage Induction Motors - 375 kW (500 Horsepower) and Larger
- Amerikanisches Erdölinstitut: API 546 Bürstenlose Synchronmaschinen - 500 kVA und größer
- Amerikanisches Erdöl-Institut: API 547 Induktionsmotoren mit formgewickeltem Kurzschlussläufer für allgemeine Zwecke - 250 PS und mehr
- Institut der Elektro- und Elektronikingenieure: IEEE Std 112 Standard Test Procedure for Polyphase Induction Motors and Generators
- Institut für Elektro- und Elektronik-Ingenieure: IEEE Std 115 Guide for Test Procedures for Synchronous Machines
- Institut für Elektro- und Elektronik-Ingenieure: IEEE Std 841 Standard for Petroleum and Chemical Industry - Premium Efficiency Severe Duty Totally Enclosed Fan-Cooled (TEFC) Squirrel Cage Induction Motors - Up to and Including 370 kW (500 Hp)
- Internationale Elektrotechnische Kommission: IEC 60034 Drehende elektrische Maschinen
- Internationale Elektrotechnische Kommission: IEC 60072 Abmessungen und Leistungsreihen für rotierende elektrische Maschinen
- Nationale Vereinigung der Elektrohersteller: MG-1 Motoren und Generatoren
- Unterzeichner-Laboratorien: UL 1004 - Norm für Elektromotoren
- Indische Norm: IS:12615-2018 - Netzbetriebene Dreiphasen-Wechselstrommotoren (IE CODE) "Wirkungsgradklassen und Leistungsspezifikation" (Dritte Revision) ⓘ
Nicht-magnetische Motoren
Ein elektrostatischer Motor basiert auf der Anziehung und Abstoßung von elektrischer Ladung. In der Regel handelt es sich bei elektrostatischen Motoren um das Pendant zu herkömmlichen Motoren auf Spulenbasis. Sie benötigen in der Regel eine Hochspannungsstromversorgung, obwohl kleine Motoren mit niedrigeren Spannungen arbeiten. Herkömmliche Elektromotoren nutzen stattdessen die magnetische Anziehung und Abstoßung und benötigen einen hohen Strom bei niedrigen Spannungen. In den 1750er Jahren wurden die ersten elektrostatischen Motoren von Benjamin Franklin und Andrew Gordon entwickelt. Elektrostatische Motoren werden häufig in mikroelektromechanischen Systemen (MEMS) eingesetzt, deren Antriebsspannungen unter 100 Volt liegen und bei denen sich bewegliche, geladene Platten viel einfacher herstellen lassen als Spulen und Eisenkerne. Die molekulare Maschinerie, die lebende Zellen antreibt, basiert häufig auf linearen und rotierenden elektrostatischen Motoren. ⓘ
Ein piezoelektrischer Motor oder Piezomotor ist ein Elektromotor, der auf der Formveränderung eines piezoelektrischen Materials beruht, wenn ein elektrisches Feld angelegt wird. Piezoelektrische Motoren machen sich den umgekehrten piezoelektrischen Effekt zunutze, bei dem das Material akustische oder Ultraschallschwingungen erzeugt, um eine lineare oder rotierende Bewegung zu erzeugen. Bei einem Mechanismus wird die Dehnung in einer einzigen Ebene genutzt, um eine Reihe von Streckungen und Positionshaltungen vorzunehmen, ähnlich wie bei der Bewegung einer Raupe. ⓘ
Ein elektrisch angetriebenes Antriebssystem für Raumfahrzeuge nutzt die Elektromotortechnologie, um Raumfahrzeuge im Weltraum anzutreiben. Die meisten Systeme beruhen auf der elektrischen Beschleunigung des Treibstoffs auf hohe Geschwindigkeit, während einige Systeme auf dem Prinzip der elektrodynamischen Ankopplung an die Magnetosphäre beruhen. ⓘ
Grundprinzip/Funktionsweise

Die Drehbewegung eines Elektromotors beruht auf den Anziehungs- und Abstoßungskräften, die mehrere Magnetfelder aufeinander ausüben (Lorentzkraft). Im üblichen Elektromotor gibt es einen feststehenden Außenteil sowie einen sich darin drehenden Innenteil. Entweder besitzt einer davon Permanentmagneten und der andere elektrische Spulen, oder beide Komponenten besitzen Spulen. Jede stromdurchflossene Spule erzeugt ein Magnetfeld, dessen Ausrichtung (Nordpol/Südpol) abhängig von der Stromrichtung ist – fließt der Strom in entgegengesetzter Richtung durch die Spule, so wird auch das Magnetfeld umgedreht. Durch fortwährendes Umschalten der Stromrichtung bzw. passendes "Umpolen" der Spulen während des Umlaufs wird eine kontinuierliche Drehung des Innenteils erreicht. ⓘ
Elektromotorarten
Drehfeld- und Wanderfeld-Maschinen
- Drehstrommotor
- Drehstrom-Asynchronmaschine
- Schleifringläufermotor
- Drehstrom-Synchronmaschine
- Kaskadenmaschine
- Schrittmotor
- Bürstenloser Gleichstrommotor
- Drehstrom-Asynchronmaschine
- Linearmotor
- Wechselstrommotor
- Kondensatormotor
- Spaltpolmotor
- Synchronmotor/Einphasenasynchronmotor
- Reluktanzmotor
- Magnetmotor
- Transversalflussmaschine ⓘ
Stromwender- bzw. Kommutator-Maschine
- Gleichstrommotor
- Universalmotor (für Gleich- und Wechselstrom)
- Repulsionsmotor
- permanent erregter Gleichstrommotor
- elektrisch erregter (fremderregter) Gleichstrommotor
- Reihenschlussmotor
- Nebenschlussmaschine
- Verbundmotor ⓘ
Anwendungen

Elektromotoren kommen sowohl ungeregelt als auch geregelt zum Einsatz. In einfachen Fällen kommen ungeregelte Drehstrommotoren mit Stern-Dreieck-Umschaltungen zur Anwendung. Diese sind jedoch nur zur Lösung primitiver Antriebsaufgaben geeignet. In den meisten Fällen in der heutigen Praxis liegen anspruchsvollere Antriebsprobleme vor, sodass die Elektromotoren durch eine Regelung geregelt werden müssen. Handelt es sich dabei um größere Leistungen, die erforderlich sind, so müssen noch leistungselektronische Stellglieder zwischen Regelung und Elektromotor dazwischengeschaltet werden. Kommen Regelung und Elektromotor zusammen und bilden sie gemeinsam eine funktionelle Einheit, so spricht man vom „Elektroantrieb“. Per se ist also ein Elektromotor nicht an eine Regelung gebunden; in vielen praktischen Fällen hat sich jedoch gerade deren Zusammenwirken als zweckmäßig erwiesen. ⓘ
In der Vergangenheit fanden Elektromotoren zunächst praktische Verwendung als Antrieb von Straßenbahnen und etwas später als Universalantrieb zur Ersetzung von Dampfmaschinen in Fabriken und wurden zu diesem Zweck über Riementriebe zum Antreiben mechanischer Webstühle und dergleichen eingesetzt. Mit der Einführung von Fließbändern in der Industrie wurden Elektromotoren dann zum Antriebsmittel ganzer Industriezweige schlechthin. ⓘ
Im Bereich Verkehr und Mobilität kamen Elektromotoren erstmals bei Elektrolokomotiven und Elektrischen Bahnen zum Tragen, später in Elektrokarren und in Gabelstaplern. Mit der Weiterentwicklung von Akkus werden heute Elektroautos mit immer größerer Reichweite gebaut und gelten wegen der hohen Effizienz des Elektroantriebs als Alternative zum Verbrennungsmotor in der Zukunft. Entwicklungen in der Leistungselektronik brachten einen weiteren Anwendungsschub – von da ab konnten die wartungsfreien, preiswerten Asynchronmotoren auch für drehzahlvariable Antriebe eingesetzt werden. ⓘ
Heute werden Elektromotoren in großer Zahl in Maschinen, Automaten, Robotern, Spielzeug, Haushaltsgeräten, Elektronikgeräten (zum Beispiel Videorekorder, Festplatten, CD-Spieler), in Ventilatoren, Rasenmähern, Kranen usw. eingesetzt. Die große Bedeutung des Elektromotors für die heutige moderne Industriegesellschaft spiegelt sich auch im Energieverbrauch wider: Elektromotoren haben einen Anteil von über 50 Prozent am Stromverbrauch in Deutschland. ⓘ
Elektromotoren in mobilen Anwendungen

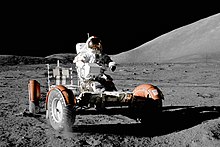

Elektromotoren werden in Kraftfahrzeugen und Bahnen seit langem angewendet. Gründe hierfür sind:
- hoher Wirkungsgrad (insbesondere auch bei Teillastbetrieb, wichtig bei Batteriebetrieb),
- Unterbrechungsfreie Drehmomentabgabe über den vollen Geschwindigkeitsbereich, keine Anfahrsynchronisation oder schaltbare Übersetzung notwendig. Dadurch hoher Fahrkomfort (zum Beispiel auch wichtig bei elektrischen Rollstühlen).
- Geringere Abmessung und geringere Masse als vergleichbarer Verbrennungsmotor; dadurch platzsparender Einbau direkt in der Nähe der Räder möglich.
- Keine Emissionen; daher Einsatz in abgassensiblen Bereichen möglich (Werkhallen, Tunnelgebiete und Wohngebiete etwa)
- Geringere Betriebskosten (sehr lange Motor-Lebensdauer, geringere Wartung).
- Einfacher Aufbau einschließlich einfacherem Kühlsystem.
- Einrichtung einer elektromotorischen Bremse die eine Nutzbremsung mit Energierückgewinnung ermöglicht und keine Wartungsarbeiten wegen Verschleiß benötigt, wie es bei herkömmlichen Bremssystemen der Fall ist. ⓘ
Trotz dieser Vorteile wird der Elektromotor bisher wenig in Pkw und Lkw eingesetzt. Grund ist insbesondere die begrenzte maximale Reichweite bzw. die hohe Masse der Energiespeicher (Akkumulatoren) sowie deren lange Ladezeit. ⓘ
Mit einem Elektromotor und einem Akkumulator werden auch manche Modellflugzeuge (Elektroflug), kleine Schiffe, Torpedos und U-Boote angetrieben. Die Elektromotoren anderer U-Boote werden aus Brennstoffzellen oder aus einem mitgeführten kleinen Kernkraftwerk gespeist. ⓘ
Fahrzeugantriebs-Konzepte mit Elektromotoren, jedoch ohne oder nur teilweiser Energiespeicherung in einem Akkumulator, sind:
- Brennstoffzellen-Antrieb: Ein Projekt ist zum Beispiel HyFLEET:CUTE, die Weiterführung des Projektes CUTE. Probleme bestehen in der Lebensdauer und den Kosten der Brennstoffzellen.
- Hybridantrieb (zum Beispiel Toyota Prius): Ein Ottomotor wird mit einem Elektromotor/Generator kombiniert und mit Akkumulatoren gepuffert (Vorteile im Teillastbereich/Stadtbetrieb, hoher Fahrkomfort, Nutzbremsung (Rekuperation), Pufferung auch mit Doppelschichtkondensatoren).
- Gyroantrieb: Als Energiespeicher dient ein Schwungrad mit einem Generator, der die Fahrmotoren antreibt (wird unter anderem bei Gyrobussen angewendet, geringe Reichweite, Nutzbremsung möglich). ⓘ
Bei elektrischen Bahnen und Oberleitungsbussen wird die Elektroenergie mit Oberleitungen oder Stromschienen zugeführt. Auch hier kann Nutzbremsung stattfinden, wenn das speisende Netz dafür ausgelegt ist oder Akkumulatoren installiert werden. Auch Doppelschichtkondensatoren werden hierbei angewendet. ⓘ
Eine weitere mobile Anwendung ist der dieselelektrische Antrieb; hier erzeugt ein Dieselaggregat elektrischen Strom, der die Fahrmotoren antreibt. Nutzbremsung ist nicht möglich, wenn nicht zusätzlich Akkumulatoren mitgeführt werden. Dieselelektrische Antriebe finden sich in Schiffen, Lokomotiven und U-Booten (hier ergänzt durch einen Akkumulator). ⓘ
Anwendungen in der Industrie
Die vielfältigen Anwendungsgebiete von Elektromotoren in der Industrie lassen sich in zwölf Gebiete aufteilen. Die ersten vier befassen sich mit dem Materialfluss. Die nächsten vier mit kontinuierlichen oder getakteten Produktionsstraßen und die letzten beiden mit Prozessen, die auf die Werkstücke einwirken.
- Förderantriebe: Anforderungen an die Antriebe sind eine hohe Lebensdauer, Robustheit und Zuverlässigkeit, niedriger Wartungsaufwand, hohe Modularität und geringer Energieverbrauch. Die Antriebe werden meist im Dauerbetrieb eingesetzt, Beschleunigungen spielen daher eine untergeordnete Rolle.
- Fahrantriebe werden an Fahrzeugen zum Materialtransport eingesetzt, beispielsweise bei fahrerlosen Transportsystemen, Portalkranen, Regalbediengeräten oder Elektrohängebahnen. Für das genaue Anfahren von Positionen wird eine hohe Präzision der Antriebe gefordert.
- Hubantriebe sollen Güter senkrecht nach oben fördern. Dazu zählen Krane, Hubtische, Lastenaufzüge und Bauaufzüge.
- Positionierantriebe dienen dazu, einzelne Güter von einem Punkt zu einem anderen zu befördern. Dazu zählt das Bestücken von elektronischen Bauteilen, die Zuführung und Entnahme von Werkstücken bei Produktionsmaschinen und Montageautomaten. Die Mehrheit dieser Antriebe ist als linearer Direktantrieb ausgeführt.
- Koordinierte Antriebe für Roboter: Industrieroboter haben häufig bis zu sechs Achsen die gleichzeitig während der Bewegung eine bestimmte Soll-Lage haben sollen. Eine Koordinierung der einzelnen Antriebe ist daher nötig um die gewünschte Bewegung des Roboterarmes zu erzeugen.
- Gleichlaufantriebe werden bei Produktionsprozessen eingesetzt, bei denen ein kontinuierliches Produkt als Endlosmaterial hergestellt wird. Dazu zählen das Transportieren, Walzen, Beschichten, Wickeln und Zwirnen sowie das Bedrucken.
- Wickelantriebe stehen oft am Anfang oder Ende einer kontinuierlichen Fließproduktion. Sie werden beispielsweise in Stahlwerken eingesetzt um Bleche zu Coils aufzuwickeln und im Maschinenbau und der Fahrzeugindustrie, um sie wieder abzuwickeln. Weitere Beispiele sind das Auf- und Abwickeln von Draht, Garn oder Papier. Da das aufgewickelte Material mit der Zeit eine immer größeren Umfang hat, nimmt bei gleichbleibender Drehzahl die Umfangsgeschwindigkeit zu. Um ein Reißen des Produktes zu verhindern, müssen die Antriebe über den Umfang des aufgewickelten Materials geregelt werden.
- Taktantriebe für Querschneider und Fliegende Sägen werden bei der kontinuierlichen Produktion genutzt um das Fließmaterial zu vereinzeln, beispielsweise durch Absägen eines Abschnittes. Besondere Anforderungen ergeben sich daraus, dass das Material sich während des Trennprozesses weiterbewegt.
- Antriebe für elektronische Kurvenscheiben zählen zu Antrieben mit ungleichförmiger Bewegung. Ein Stanzwerkzeug soll sich beispielsweise langsam senken, um eine gute Arbeitsqualität am Werkstück zu erreichen und schnell heben. Weitere Anwendungen sind Kleben, Schweißen, Biegen und Schneiden.
- Antriebe für Umformprozesse: Hierzu zählt das Pressen von Stahlblechen, das Extrudieren von Kunststoffen, das Tiefziehen oder das Gesenkschmieden.
- Haupt- und Werkzeugantriebe bei Werkzeugmaschinen. Sie dienen zum Antrieb von Fräsen, Bohrern und Drehmaschinen. Dies ist der einzige industrielle Anwendungsfall, zu dem reichhaltige ingenieurwissenschaftliche Literatur vorliegt.
- Antriebe für Pumpen und Ventilatoren. ⓘ
Fertigung von Elektromotoren
Die einzelnen Komponenten des Elektromotors werden unabhängig voneinander hergestellt. Die wichtigsten sind das Gehäuse, der Stator, die Welle und der Rotor. Anschließend erfolgt die Endmontage. ⓘ
Fertigung der Gehäuse
Das eigentliche Gehäuse wird auf beiden Seiten von Deckeln abgeschlossen, die beim Elektromotor als Lagerschilde bezeichnet werden, da sie auch zum Lagern der Motorwelle mittels Kugellagern dienen. Die einzelnen Prozessschritte für die Lagerschilde und das Gehäuse stimmen jedoch überein. Beide werden zunächst durch Gießen oder Fließpressen grob in Form gebracht, danach erfolgt die Feinbearbeitung mit Drehen, Bohren und Schleifen und zuletzt die Reinigung. Die Details hängen von der produzierten Stückzahl ab. ⓘ
Gießen mit Formen aus Sand wird nur bei geringen Stückzahlen eingesetzt, beispielsweise bei der Prototypenfertigung. Für mittlere und größere Stückzahlen eignen sich der Druckguss und der Schleuderguss sowie das Strangpressen. Der Druckguss ist mit einem Anteil von 60 % das häufigste Verfahren. Hier besteht die Form aus Stahl und kann etwa 80.000-mal abgegossen werden. Die benötigten Maschinen kosten zwischen 700.000 Euro und einer Million Euro, sodass eine Mindeststückzahl von etwa 15.000 erreicht werden muss, um wirtschaftlich zu sein. Schleudergussanlagen kosten dagegen nur etwa 60.000 bis 100.000 Euro. Am teuersten sind Strangpressanlagen mit 8 Mio. Euro. Sie eignen sich daher nur für sehr große Serien, weisen dann aber die niedrigsten Stückkosten auf. ⓘ
Nach dem Gießen oder Strangpressen werden die Gehäuse entgratet. Die weitere Feinbearbeitung geschieht meist auf Bearbeitungszentren, die auf das Drehen, Bohren, Fräsen und Schleifen spezialisiert sind. Zu den Aufgaben gehört das Ausdrehen der Innenkontur, die Feinbearbeitung von Rändern und das Bohren von Durchgängen oder Gewinden. ⓘ
Die Reinigung der Gehäuse geschieht bei kleinen Serien meist durch Bestrahlen mit Trockeneis (sogenanntes Trockeneisstrahlen) oder mit kleinen Kugeln (Kugelstrahlen). Dadurch werden Gießrückstände, Späne, Stäube und sonstige Schmutzpartikel entfernt. Bei mittelgroßen Serien geschieht die Reinigung mittels Ultraschallbad. Bei Großserien werden Durchlauf-Reinigungsanlagen eingesetzt, die aus einer Aufgabestation bestehen, aus Reinigungs- und Spülzonen, der Trockenzone und der Übergabestation. ⓘ
Fertigung der Blechpakete
Die eigentlichen leistungserzeugenden Komponenten, also der Rotor und der Stator, werden aus Blechpaketen zusammengebaut. Gegenüber der Vollmaterialbauweise haben Blechpakete den Vorteil, dass sie Wirbelströme verhindern und so den Wirkungsgrad erhöhen. Beim Zusammenbau der Bleche zu Paketen ist es wichtig, Kurzschlüsse zu vermeiden. Die einzelnen Bleche sind daher mit einem Isolator beschichtet. Sie werden aus Elektroband hergestellt. Dabei handelt es sich um Bleche aus einem siliziumhaltigen Stahl, der verbesserte magnetische Eigenschaften aufweist. Da seine Produktion recht aufwendig ist, wird es von Elektromotor-Herstellern eingekauft. Die Fertigung der Blechpakete geschieht in mehreren Schritten: Ausschneiden der Bleche, Stapeln, dauerhaftes Fügen (Kleben, Schweißen etc.) und eine Nacharbeit. ⓘ
Für kleinere Serien oder Prototypen wird das Blech mittels Laser- oder Wasserstrahlschneiden getrennt. Bei größeren Serien ist das Stanzen wirtschaftlicher. Anschließend werden die Bleche gestapelt. Beim Stanzen kann dies direkt in der Maschine geschehen, während bei den anderen Verfahren ein weiterer Prozessschritt nötig ist. Zum Fügen der Blechpakete gibt es zahlreiche Möglichkeiten. In der Massenproduktion werden häufig Nasen an einzelnen Blechen nach unten gedrückt, in Aussparungen der darunterliegenden Schichten. Häufig ist dieser Schritt direkt in das Stanzen integriert. Nach dem Stapeln können die einzelnen Lagen auch zusammengeschweißt werden. Dies ist bei deutlich niedrigeren Stückzahlen wirtschaftlich, hat jedoch den Nachteil, dass eine elektrisch leitende Verbindung entsteht, die die Entstehung von Wirbelströmen begünstigt. Da die Schweißnähte an Stellen angebracht werden können, die für das magnetische Feld von geringer Bedeutung sind, sind die Nachteile beim Wirkungsgrad gering. Eine andere Möglichkeit ist die Verwendung von Backlack. Hier werden nach dem Stanzen die einzelnen Bleche mit Backlack beschichtet und gestapelt und anschließend im Ofen gebacken. Dadurch werden einerseits die Schichten zusammengeklebt und andererseits auch isoliert. ⓘ
Als letzter Schritt kann eine Nachbearbeitung geschehen, die den Wirkungsgrad etwas erhöhen. Dazu zählt das Spannungsarmglühen, Außenrunddrehen, Entgraten und eine Nachlackierung. Da die Effizienzsteigerungen gering sind, wird dies vor allem bei Großmotoren praktiziert. ⓘ
Fertigung des Stators
Der Stator ist mit einem Anteil von 35 % an den Gesamtkosten das teuerste Bauteil. Dies liegt an der aufwendigen Produktion und dem teuren Material. Die einzelnen Prozessschritte sind Isolieren der Komponenten, Wickeln der Spulen, Bearbeiten der Wicklung und Imprägnieren. ⓘ
Zwischen dem Blechpaket und den Wicklungen der Spulen wird Isolatorpapier verwendet, um Spannungsüberschläge zu vermeiden. Der für die Spulen benötigte Draht wird mittels Drahtziehen hergestellt, anschließend mit einer isolierenden Lackschicht und danach mit einer Gleitschicht überzogen, die das Wickeln erleichtert. ⓘ
In der Spulenwickeltechnik haben sich zahlreiche Methoden und Verfahren etabliert zur Herstellung der Spulen. Die wichtigsten sind die Linear-, Flyer- und Nadelwickeltechnik. Die Anlagen für die Spulenwicklungen kosten zwischen 150.000 Euro für einfache Maschinen und gehen bis zu 4 Millionen Euro für Anlagen der Großserienproduktion. ⓘ
Nachdem die Spulen in den Stator eingebaut wurden, werden die Enden der Drähte kontaktiert und geprüft. ⓘ
Fertigung der Welle
Der Kostenanteil der Welle liegt mit nur 5 % sehr niedrig. Die Herstellung geschieht in drei Schritten: Grobbearbeitung im weichen Zustand, Härten und die Feinbearbeitung durch Schleifen. ⓘ
Die erste Formgebung geschieht bei großen Stückzahlen meist durch Schmieden, insbesondere mittels Gesenkschmieden. Bei kleineren und mittleren Stückzahlen werden Bearbeitungszentren eingesetzt wie bei der Herstellung der Gehäuse. Zum Härten werden konventionelle Wärmebehandlungsmethoden eingesetzt, darunter das Induktionshärten, das Einsatzhärten und das Nitrierhärten. In allen Fällen wird danach durch Hartdrehen oder Schleifen die endgültige Form präzise erzeugt. ⓘ
Fertigung des Rotors
Bei Motoren mit Permanentmagneten sind die Fertigungsschritte Magnetisieren, Magnetbestückung, Wellenmontage und Auswuchten austauschbar, verschiedene Reihenfolgen aber mit jeweils eigenen Vor- und Nachteilen behaftet. ⓘ
Bei Asynchronmotoren wird stattdessen ein Rotorkäfig verwendet. Meistens wird er mittels Druckguss gefertigt. Beim Prototypenbau wird er auch aus Stäben und Ringen zusammengelötet. Hochwertige Käfige bestehen aus Kupfer, das eine größere Leitfähigkeit aufweist als Aluminium aber auch etwa viermal teurer ist und erst bei 1084 °C schmilzt. Aluminiumlegierungen dagegen schmelzen bereits bei 600 °C. Daher lassen sich Alugussformen etwa 50.000-mal abgießen, Formen für Kupfer dagegen nur 100-mal. Üblicherweise wird die Schmelze direkt in die Rotornuten gegossen. ⓘ
Endmontage
Wegen der Vielfalt der verschiedenen Motorbauarten und möglichen Stückzahlen gibt es bei der Endmontage große Bandbreiten und Varianten von der ausschließlich manuellen Montage bis zur vollautomatischen Montagelinie. ⓘ
Zuerst wird der Stator in das Gehäuse gebaut. Dies kann mit Aufschrumpfen, Einpressen oder Kleben geschehen. Danach wird das Rotorpaket in den Stator eingebracht. ⓘ
Der nächste Schritt ist die Montage der Sensorik. Beim Asynchronmotor ist dies ein Drehzahlmesser und bei Motoren mit Permanentmagnet ein Positionsmesser (Inkrementalgeber). Sie werden ebenfalls aufgeschrumpft, eingepresst oder geklebt. Außerdem werden Temperatursensoren verbaut. ⓘ
Anschließend erfolgt die Kontaktierung der Sensoren und der einzelnen Phasen mit dem Anschlussstecker. ⓘ
Danach werden die Lagerschilde mit Kugellagern bestückt und am Gehäuse angebracht. Im letzten Schritt erfolgt die Endprüfung auf Sicht sowie die Widerstands-, Isolations-, Funktions- und Hochspannungsprüfung sowie einer Prüfung der Leistungselektronik. ⓘ