Dampfmaschine
Geschichte der Technik ⓘ |
---|




Eine Dampfmaschine ist eine Wärmekraftmaschine, die mit Hilfe von Dampf als Arbeitsmedium mechanische Arbeit verrichtet. Die Dampfmaschine nutzt die durch den Dampfdruck erzeugte Kraft, um einen Kolben in einem Zylinder hin und her zu schieben. Diese Schubkraft kann durch eine Pleuelstange und eine Kurbel in eine Rotationskraft umgewandelt werden, die Arbeit verrichtet. Der Begriff "Dampfmaschine" wird im Allgemeinen nur für die soeben beschriebenen Hubkolbenmaschinen verwendet, nicht für die Dampfturbine. Dampfmaschinen sind externe Verbrennungsmotoren, bei denen das Arbeitsmittel von den Verbrennungsprodukten getrennt ist. Der ideale thermodynamische Zyklus, der zur Analyse dieses Prozesses verwendet wird, heißt Rankine-Zyklus. Im allgemeinen Sprachgebrauch kann sich der Begriff Dampfmaschine entweder auf komplette Dampfanlagen (einschließlich Kessel usw.) beziehen, wie z. B. Dampflokomotiven der Eisenbahn und tragbare Maschinen, oder auf die Kolben- oder Turbinenmaschine allein, wie bei der Balkenmaschine und der stationären Dampfmaschine. Wenn Wasser zu Dampf kocht, vergrößert sich sein Volumen um das bis zu 1.700-fache. Diese Ausdehnung treibt Dampfmaschinen an. ⓘ
Obwohl dampfbetriebene Geräte bereits im ersten Jahrhundert n. Chr. mit dem Äolipil bekannt waren und im 16. Jahrhundert einige weitere Anwendungen verzeichnet wurden, ließ Jerónimo de Ayanz y Beaumont 1606 seine Erfindung der ersten dampfbetriebenen Wasserpumpe zur Entwässerung von Bergwerken patentieren. Thomas Savery gilt als Erfinder des ersten kommerziell genutzten dampfbetriebenen Geräts, einer Dampfpumpe, die mit Dampfdruck direkt auf das Wasser wirkt. Der erste kommerziell erfolgreiche Motor, der eine kontinuierliche Kraft auf eine Maschine übertragen konnte, wurde 1712 von Thomas Newcomen entwickelt. James Watt nahm 1764 eine entscheidende Verbesserung vor, indem er den verbrauchten Dampf zur Kondensation in ein separates Gefäß ableitete, wodurch sich die pro verbrauchter Brennstoffeinheit erzielte Arbeitsleistung erheblich verbesserte. Im 19. Jahrhundert trieben stationäre Dampfmaschinen die Fabriken der industriellen Revolution an. Dampfmaschinen ersetzten die Segel von Raddampfern, und Dampflokomotiven wurden bei der Eisenbahn eingesetzt. ⓘ
Hubkolben-Dampfmaschinen waren die vorherrschende Energiequelle bis zum Beginn des 20. Jahrhunderts, als Fortschritte in der Konstruktion von Elektromotoren und Verbrennungsmotoren dazu führten, dass Dampfmaschinen in der kommerziellen Nutzung allmählich ersetzt wurden. Dampfturbinen ersetzten die Kolbenmaschinen bei der Stromerzeugung aufgrund der niedrigeren Kosten, der höheren Betriebsgeschwindigkeit und des höheren Wirkungsgrads. ⓘ
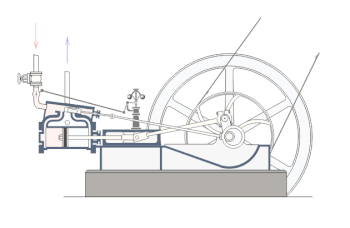
Eine Dampfmaschine ist (im engeren Sinne) eine Kolben-Wärmekraftmaschine. In einem beheizten Dampferzeuger, der als Bestandteil der Maschine gilt, wird Wasser verdampft. Der unter Druck gesetzte Dampf wandelt die in ihm enthaltene Wärmeenergie (auch Druckenergie) durch Verschieben eines in einem Zylinder beweglichen Kolbens in Bewegungsenergie um. Üblicherweise ist der Kolben Teil eines Schubkurbelgetriebes, mit dem die hin- und hergehende Bewegung des Kolbens in Rotation eines Schwungrades, das die Arbeitsmaschine antreibt, umgewandelt wird. Zur Bewegungsumkehr des Kolbens, wird der Druck jeweils auf dessen anderer zylindrischer Seite umgelenkt. ⓘ
Eine andere mit Dampf betriebene Wärmekraftmaschine ist die Dampfturbine, die schon ohne einen die Bewegungsart ändernden Folgemechanismus (Getriebe) die Wärmeenergie des Dampfs in Rotationsenergie umwandelt. ⓘ
Dampfmaschinen sind Wärmekraftmaschinen mit „äußerer Verbrennung“, was sie von Verbrennungsmotoren unterscheidet. ⓘ
Der folgende Artikel behandelt nur Kolbenkraftmaschinen (Dampfmaschinen „im engeren Sinne“). ⓘ

Geschichte
Frühe Experimente
Die erste aufgezeichnete rudimentäre dampfbetriebene "Maschine" war das Äolipil, das von Hero von Alexandria, einem griechischen Mathematiker und Ingenieur im römischen Ägypten im ersten Jahrhundert nach Christus beschrieben wurde. In den folgenden Jahrhunderten waren die wenigen bekannten dampfbetriebenen "Maschinen", wie der Äolipil, im Wesentlichen Versuchsgeräte, mit denen Erfinder die Eigenschaften von Dampf demonstrierten. Eine rudimentäre Dampfturbinenvorrichtung wurde 1551 von Taqi al-Din im osmanischen Ägypten und 1629 von Giovanni Branca in Italien beschrieben. Der spanische Erfinder Jerónimo de Ayanz y Beaumont erhielt 1606 Patente für 50 dampfgetriebene Erfindungen, darunter eine Wasserpumpe zur Entwässerung überschwemmter Minen. Denis Papin, ein Hugenotte, leistete 1679 nützliche Arbeit am Dampfkocher und verwendete 1690 erstmals einen Kolben zum Anheben von Gewichten. ⓘ
Pumpmaschinen
Das erste kommerziell genutzte dampfgetriebene Gerät war eine Wasserpumpe, die 1698 von Thomas Savery entwickelt wurde. Sie nutzte kondensierenden Dampf, um ein Vakuum zu erzeugen, das Wasser von unten anhob, und nutzte dann den Dampfdruck, um es höher zu befördern. Kleine Motoren waren effektiv, doch größere Modelle waren problematisch. Sie hatten eine sehr begrenzte Hubhöhe und waren anfällig für Kesselexplosionen. Die Savery-Maschine wurde in Bergwerken, Pumpstationen und zur Wasserversorgung von Wasserrädern eingesetzt, die Textilmaschinen antrieben. Der Motor von Savery war kostengünstig. Bento de Moura Portugal führte eine Verbesserung der Savery'schen Konstruktion ein, "um sie in die Lage zu versetzen, selbst zu arbeiten", wie John Smeaton in den Philosophical Transactions von 1751 beschrieb. Sie wurde bis zum Ende des 18. Jahrhunderts weiter hergestellt. Wenigstens eine Maschine war 1820 noch in Betrieb. ⓘ
Kolbendampfmaschinen

Die erste kommerziell erfolgreiche Maschine, die kontinuierlich Kraft auf eine Maschine übertragen konnte, war die von Thomas Newcomen um 1712 erfundene atmosphärische Maschine. Sie verbesserte die Dampfpumpe von Savery und verwendete einen von Papin vorgeschlagenen Kolben. Die Newcomen-Maschine war relativ ineffizient und wurde hauptsächlich zum Pumpen von Wasser verwendet. Sie funktionierte, indem sie durch die Kondensation von Dampf unter einem Kolben in einem Zylinder ein Teilvakuum erzeugte. Sie wurde zur Entwässerung von Bergwerken in Tiefen eingesetzt, die mit herkömmlichen Mitteln nicht zu erreichen waren, und zur Bereitstellung von wiederverwendbarem Wasser für den Antrieb von Wasserrädern in Fabriken, die nicht an einem geeigneten "Kopf" lagen. Das Wasser, das über das Rad floss, wurde in ein Reservoir oberhalb des Rades gepumpt. 1780 patentierte James Pickard die Verwendung eines Schwungrads und einer Kurbelwelle, um einen verbesserten Newcomen-Motor in Drehbewegung zu versetzen. ⓘ
Im Jahr 1720 beschrieb Jacob Leupold eine Zweizylinder-Hochdruckdampfmaschine. Die Erfindung wurde in seinem Hauptwerk "Theatri Machinarum Hydraulicarum" veröffentlicht. Die Maschine verwendete zwei schwere Kolben, um eine Wasserpumpe in Bewegung zu setzen. Jeder Kolben wurde durch den Dampfdruck angehoben und durch die Schwerkraft in seine ursprüngliche Position zurückgeführt. Die beiden Kolben teilten sich ein gemeinsames Vier-Wege-Drehventil, das direkt mit einem Dampfkessel verbunden war. ⓘ
Der nächste große Schritt erfolgte, als James Watt (1763-1775) eine verbesserte Version der Newcomen-Maschine mit einem separaten Kondensator entwickelte. Die frühen Maschinen von Boulton und Watt verbrauchten nur halb so viel Kohle wie John Smeatons verbesserte Version der Newcomen-Maschine. Die frühen Motoren von Newcomen und Watt waren "atmosphärisch". Sie wurden durch Luftdruck angetrieben, der einen Kolben in das durch kondensierenden Dampf erzeugte Teilvakuum drückte, anstatt durch den Druck des expandierenden Dampfes. Die Zylinder des Motors mussten groß sein, da die einzige nutzbare Kraft, die auf sie wirkte, der atmosphärische Druck war. ⓘ
Watt entwickelte seine Maschine weiter und modifizierte sie so, dass sie eine für den Antrieb von Maschinen geeignete Drehbewegung erzeugte. Dies ermöglichte die Ansiedlung von Fabriken in der Nähe von Flüssen und beschleunigte das Tempo der industriellen Revolution. ⓘ
Hochdruckmotoren
Die Bedeutung des Begriffs "Hochdruck" in Verbindung mit einem tatsächlichen Wert über dem Umgebungsdruck hängt von der Zeit ab, in der der Begriff verwendet wurde. Van Reimsdijk bezieht sich bei der frühen Verwendung des Begriffs darauf, dass der Dampf einen so hohen Druck hat, dass er in die Atmosphäre abgelassen werden kann, ohne auf ein Vakuum angewiesen zu sein, damit er nützliche Arbeit leisten kann. Ewing 1894, S. 22 stellt fest, dass Watt's Kondensationsmaschinen zu dieser Zeit als Niederdruckmaschinen bekannt waren, verglichen mit den nicht kondensierenden Hochdruckmaschinen der gleichen Zeit. ⓘ
Watts Patent hinderte andere daran, Hochdruck- und Verbundmotoren zu bauen. Kurz nach dem Auslaufen von Watts Patent im Jahr 1800 stellten Richard Trevithick und, getrennt davon, Oliver Evans im Jahr 1801 Maschinen vor, die mit Hochdruckdampf betrieben wurden; Trevithick hatte sein Patent für Hochdruckmaschinen im Jahr 1802 erhalten, und Evans hatte zuvor mehrere funktionierende Modelle gebaut. Diese waren bei gleicher Zylindergröße wesentlich leistungsfähiger als frühere Maschinen und konnten für Transportanwendungen klein genug gebaut werden. In der Folgezeit führten technologische Entwicklungen und Verbesserungen in der Fertigungstechnik (die zum Teil durch die Einführung der Dampfmaschine als Energiequelle bedingt waren) zur Konstruktion effizienterer Motoren, die je nach Einsatzzweck kleiner, schneller oder leistungsstärker sein konnten. ⓘ
Der Cornish-Motor wurde in den 1810er Jahren von Trevithick und anderen entwickelt. Es handelte sich um eine Verbundmaschine, die Hochdruckdampf expansiv nutzte und dann den Niederdruckdampf kondensierte, wodurch sie relativ effizient wurde. Die Cornish-Maschine wies eine unregelmäßige Bewegung und ein unregelmäßiges Drehmoment auf, so dass sie sich hauptsächlich zum Pumpen eignete. Cornish-Motoren wurden bis zum Ende des 19. Jahrhunderts in Bergwerken und für die Wasserversorgung eingesetzt. ⓘ
Horizontale Stationärmaschine
Frühe Erbauer stationärer Dampfmaschinen waren der Ansicht, dass horizontale Zylinder einem übermäßigen Verschleiß unterliegen würden. Ihre Maschinen wurden daher mit senkrecht stehender Kolbenachse gebaut. Im Laufe der Zeit wurde die horizontale Anordnung immer beliebter, da sie kompakte, aber leistungsstarke Maschinen auf kleinerem Raum ermöglichte. ⓘ
Der Höhepunkt der horizontalen Maschine war die 1849 patentierte Corliss-Dampfmaschine, eine Vierventil-Gegenstrommaschine mit getrennten Dampfein- und -auslassventilen und automatischer, variabler Dampfabschaltung. Als Corliss die Rumford-Medaille verliehen wurde, erklärte das Komitee, dass "keine Erfindung seit Watt die Effizienz der Dampfmaschine so sehr verbessert hat". Sie verbrauchte nicht nur 30 % weniger Dampf, sondern ermöglichte auch eine gleichmäßigere Geschwindigkeit durch eine variable Dampfabschaltung, wodurch sie sich gut für die Fertigung, insbesondere für die Baumwollspinnerei, eignete. ⓘ
Straßenfahrzeuge

Die ersten experimentellen dampfgetriebenen Straßenfahrzeuge wurden im späten 18. Jahrhundert gebaut, aber erst nachdem Richard Trevithick um 1800 die Verwendung von Hochdruckdampf entwickelt hatte, wurden mobile Dampfmaschinen zu einem praktischen Vorschlag. In der ersten Hälfte des 19. Jahrhunderts wurden große Fortschritte bei der Konstruktion von Dampffahrzeugen erzielt, und in den 1850er Jahren wurde es möglich, sie auf kommerzieller Basis zu produzieren. Dieser Fortschritt wurde durch die Gesetzgebung gebremst, die den Einsatz dampfgetriebener Fahrzeuge im Straßenverkehr einschränkte oder verbot. Von den 1860er Jahren bis in die 1920er Jahre wurde die Fahrzeugtechnik weiter verbessert. Dampfstraßenfahrzeuge wurden für zahlreiche Anwendungen eingesetzt. Im 20. Jahrhundert führte die rasante Entwicklung der Verbrennungsmotorentechnik zum Niedergang der Dampfmaschine als Antriebsquelle für Fahrzeuge auf kommerzieller Basis, von denen nach dem Zweiten Weltkrieg nur noch relativ wenige im Einsatz waren. Viele dieser Fahrzeuge wurden von Enthusiasten erworben, um sie zu erhalten, und zahlreiche Exemplare sind noch vorhanden. In den 1960er Jahren gab die Luftverschmutzung in Kalifornien Anlass zu einer kurzen Phase des Interesses an der Entwicklung und Erforschung dampfbetriebener Fahrzeuge als mögliches Mittel zur Reduzierung der Luftverschmutzung. Abgesehen von dem Interesse von Dampffreunden, gelegentlichen Nachbauten und experimenteller Technik werden derzeit keine Dampffahrzeuge hergestellt. ⓘ
Schiffsmotoren

Gegen Ende des 19. Jahrhunderts kamen Verbundmaschinen in großem Umfang zum Einsatz. Bei diesen Maschinen wurde der Dampf in immer größere Zylinder geleitet, um das höhere Volumen bei geringerem Druck zu bewältigen und so den Wirkungsgrad zu verbessern. Diese Stufen wurden als Expansionsstufen bezeichnet, wobei Motoren mit doppelter und dreifacher Expansion üblich waren, insbesondere in der Schifffahrt, wo die Effizienz wichtig war, um das Gewicht der transportierten Kohle zu reduzieren. Dampfmaschinen blieben bis zum Beginn des 20. Jahrhunderts die vorherrschende Energiequelle, als Fortschritte in der Konstruktion von Dampfturbinen, Elektromotoren und Verbrennungsmotoren allmählich zu einer Ablösung der Kolbendampfmaschinen führten, wobei die Handelsschifffahrt zunehmend auf Dieselmotoren und Kriegsschiffe auf Dampfturbinen setzten. ⓘ
Dampflokomotiven
Im Laufe des 18. Jahrhunderts wurden verschiedene Versuche unternommen, die Dampfmaschinen für den Straßen- und Eisenbahnverkehr einzusetzen. Im Jahr 1784 baute William Murdoch, ein schottischer Erfinder, ein Modell einer Dampfstraßenlokomotive. Ein frühes Arbeitsmodell einer Dampfeisenbahnlokomotive wurde von dem Dampfschiffpionier John Fitch in den Vereinigten Staaten wahrscheinlich in den 1780er oder 1790er Jahren entworfen und gebaut. Seine Dampflokomotive verfügte über innenliegende Schaufelräder, die von Schienen oder Gleisen geführt wurden. ⓘ

Die erste voll funktionsfähige Eisenbahndampflokomotive wurde von Richard Trevithick im Vereinigten Königreich gebaut, und am 21. Februar 1804 fand die erste Eisenbahnfahrt der Welt statt, als Trevithicks namenlose Dampflokomotive einen Zug auf der Straßenbahnlinie von der Eisenhütte Pen-y-darren in der Nähe von Merthyr Tydfil nach Abercynon in Südwales zog. Die Konstruktion umfasste eine Reihe wichtiger Innovationen, darunter den Einsatz von Hochdruckdampf, der das Gewicht der Maschine reduzierte und ihre Effizienz erhöhte. Trevithick besuchte später im Jahr 1804 die Gegend um Newcastle, und die Zechenbahnen im Nordosten Englands wurden zum führenden Zentrum für die Erprobung und Entwicklung von Dampflokomotiven. ⓘ
Trevithick setzte seine eigenen Experimente mit einem Trio von Lokomotiven fort und beendete sie 1808 mit der Catch Me Who Can. Nur vier Jahre später wurde die erfolgreiche Zweizylinderlokomotive Salamanca von Matthew Murray bei der Middleton Railway mit Zahnstange und Ritzel eingesetzt. Im Jahr 1825 baute George Stephenson die Locomotion für die Stockton and Darlington Railway. Dies war die erste öffentliche Dampfeisenbahn der Welt, und 1829 baute er die Rocket, die an den Rainhill Trials teilnahm und gewann. Die 1830 eröffnete Liverpool and Manchester Railway nutzte ausschließlich die Dampfkraft für Personen- und Güterzüge. ⓘ
Bis ins späte zwanzigste Jahrhundert wurden Dampflokomotiven in Ländern wie China und der ehemaligen DDR (wo die DR-Baureihe 52.80 hergestellt wurde) weiter produziert. ⓘ
Dampfturbinen
Die letzte große Weiterentwicklung der Dampflokomotiven war der Einsatz von Dampfturbinen ab Ende des 19. Jahrhunderts. Jahrhunderts. Dampfturbinen sind in der Regel effizienter als Kolben-Dampfmaschinen (bei Leistungen über mehreren hundert PS), haben weniger bewegliche Teile und liefern die Drehkraft direkt statt über ein Pleuelstangensystem oder ähnliche Mittel. Dampfturbinen haben Anfang des 20. Jahrhunderts die Kolbenmaschinen in Elektrizitätswerken praktisch verdrängt, da ihre Effizienz, die für den Generatorbetrieb geeignete höhere Drehzahl und die gleichmäßige Rotation von Vorteil waren. Heute wird die meiste elektrische Energie durch Dampfturbinen erzeugt. In den Vereinigten Staaten werden 90 % der elektrischen Energie auf diese Weise erzeugt, wobei eine Vielzahl von Wärmequellen genutzt wird. Dampfturbinen wurden während des größten Teils des 20. Jahrhunderts in großem Umfang für den Antrieb großer Schiffe eingesetzt. ⓘ
Gegenwärtige Entwicklung
Obwohl die Kolbendampfmaschine nicht mehr in großem Umfang kommerziell genutzt wird, erforschen oder nutzen verschiedene Unternehmen das Potenzial des Motors als Alternative zu Verbrennungsmotoren. Das schwedische Unternehmen Energiprojekt AB hat Fortschritte bei der Verwendung moderner Materialien zur Nutzung der Dampfkraft erzielt. Der Wirkungsgrad des Dampfmotors von Energiprojekt erreicht bei Hochdruckmotoren etwa 27-30 %. Es handelt sich um einen einstufigen 5-Zylinder-Motor (kein Verbund) mit überhitztem Dampf, der ca. 4 kg Dampf pro kWh verbraucht. ⓘ
Preußen

In Preußen war man bereits 1769 auf die „Feuermaschinen“ aus England aufmerksam geworden. Besonders der Oberkonsistorialrat Johann Esaias Silberschlag, der sich auch als Naturwissenschaftler einen Namen gemacht hatte, erkannte frühzeitig den Nutzen dieser Maschine und fertigte bis 1771 mehrere umfangreiche Gutachten darüber an. 1785 wurde dann die erste, in Preußen nachgebaute Dampfmaschine wattscher Bauart bei Burgörner in Betrieb genommen. Bereits 1778 hatte sich James Watt bereiterklärt, der preußischen Bergverwaltung seine verbesserte Dampfmaschine zur Wasserhaltung unter fachmännischer Anleitung zu überlassen. Seine Firma Boulton & Watt forderte jedoch ein 14-jähriges Liefermonopol, eine Bedingung, auf die man im merkantilistischen Preußen nicht eingehen wollte. Unter dem Vorwand einer Erwerbsabsicht wurden der Oberbergrat Waitz von Eschen und der Assessor Carl Friedrich Bückling (1756–1812) vom preußischen Minister Friedrich Anton von Heynitz nach England geschickt. Waitz sollte sich speziell mit der Funktionsweise der Maschine vertraut machen und Bückling entsprechende Baupläne anfertigen. Lediglich eine englische Dampfmaschine wurde erworben und 1779 auf einer Braunkohlengrube bei Altenweddingen eingesetzt. ⓘ
Nachdem Bückling noch ein zweites Mal nach England geschickt worden war, war er in der Lage, exakte Baupläne für eine eigene Dampfmaschine nach dem Vorbild der wattschen unter Mitwirkung der Preußischen Akademie der Wissenschaften zu entwerfen. Bis 1783 wurde ein verkleinertes, funktionsfähiges Modell gebaut, von da an wurden die Teile in Originalgröße hergestellt und zusammengesetzt. Am 23. August 1785 wurde die erste deutsche Dampfmaschine wattscher Bauart auf dem König-Friedrich-Schacht bei Hettstedt offiziell in Betrieb genommen. Ihre Störanfälligkeit brachte der Maschine anfangs viel Spott ein. Durch die Abwerbung des britischen Dampfmaschinen-Mechanikers William Richards konnten die Probleme in Hettstedt bis 1787 beseitigt werden. Die Maschine wurde zu einem ökonomischen Erfolg. 1794 wurde sie durch eine stärkere ersetzt und nun auf einem Steinkohlenschacht bei Löbejün aufgestellt, wo sie noch bis 1848 arbeitete. Im Mansfeld-Museum in Hettstedt steht seit 1985 ein 1:1-Nachbau dieser Dampfmaschine, der in Bewegung vorgeführt werden kann. Im oberschlesischen Tarnowitz wurde am 19. Januar 1788 eine Dampfmaschine in Betrieb genommen, die zur Entwässerung der Tarnowitzer Bergwerke diente. Von dieser Dampfmaschine wird fälschlicherweise behauptet, sie sei die erste auf dem europäischen Festland gewesen. ⓘ
Die erste Dampfmaschine des Aachener Reviers stand 1793 in Eschweiler und wurde dort ebenfalls für die Wasserhaltung im Bergbau eingesetzt. 1803 baute Franz Dinnendahl in Essen die erste Dampfmaschine im Ruhrgebiet. Bereits zwei Jahre zuvor hatte Dinnendahl den Einsatz der ersten Dampfmaschine zur Wasserhaltung im Ruhrbergbau betreut. Hergestellt in England, wurde diese auf der Zeche Vollmond in Bochum-Langendreer in Betrieb genommen. ⓘ
Andere deutsche Staaten
Etwa zeitgleich wurde im Herzogtum Sachsen-Gotha in einem kleinen Vitriol-Bergwerk bei Mühlberg (Thüringen) vom späteren Ingenieur-Leutnant Carl Christoph Besser, der von 1763 bis 1774 bei dem Bergwerk tätig war, die erste funktionsfähige Dampfmaschine Thüringens aufgebaut und über Wochen in Betrieb gehalten, sie diente zum permanenten Fördern des Grubenwassers und wurde von zwei Heizern bzw. Maschinisten Tag und Nacht am Laufen gehalten. Der vielseits talentierte Besser wurde später vom Herzog Ernst als Ingenieur und Architekt beim Bau der Seeberg-Sternwarte und anderer Projekte in Gotha eingesetzt und verlor so das Interesse am Maschinenbau. ⓘ
Von diesen frühen Anfängen bis zur weiten Verbreitung der Dampfmaschine in der Wirtschaft vergingen jedoch einige Jahrzehnte. 1836 erstellte man die erste deutsche Dampfmaschinenstatistik, und zwar für den Regierungsbezirk Düsseldorf. Durch technische Verbesserungen, der beginnenden Konzentration der sich formierenden Industrie, zunehmend ausgeschöpfter Wasserkraftpotentiale sowie der massiven Verbilligung des Kohletransportes durch die Eisenbahn wurden Dampfmaschinen wirtschaftlich immer rentabler. Nach einer nicht ganz vollständigen Statistik des Jahres 1846 gab es im Zollverein 1518 Dampfmaschinen. 1861 war die Zahl bereits auf 8695 Stück gestiegen. ⓘ
In der Stahlindustrie wurden Dampfmaschinen unter anderem zum Antrieb von Gebläsen, Pumpen und Walzstraßen eingesetzt. Zwei Walzenzugmaschinen mit Leistungen von maximal 10 000 PS, Baujahr 1913, und 15.000 PS, Baujahr 1911, arbeiteten zuverlässig in der Maxhütte (Sulzbach-Rosenberg) bis zu deren Stilllegung im Jahr 2002. Sie gehörten zu den leistungsfähigsten Dampfmaschinen weltweit. ⓘ
Bestandteile und Zubehör von Dampfmaschinen
Eine Dampfanlage besteht aus zwei grundlegenden Komponenten: dem Kessel oder Dampferzeuger und der "Motoreinheit", die selbst als "Dampfmaschine" bezeichnet wird. Bei stationären Dampfmaschinen in festen Gebäuden können sich Kessel und Motor in getrennten Gebäuden in einiger Entfernung voneinander befinden. Bei tragbaren oder mobilen Maschinen, wie z. B. Dampflokomotiven, sind beide zusammen eingebaut. ⓘ
Die weit verbreitete Hubkolbenmaschine bestand in der Regel aus einem gusseisernen Zylinder, einem Kolben, einer Pleuelstange und einem Balken oder einer Kurbel und einem Schwungrad sowie verschiedenen Gestängen. Die Dampfzufuhr und -abfuhr erfolgte abwechselnd über ein oder mehrere Ventile. Die Geschwindigkeit wurde entweder automatisch über einen Regler oder über ein Handventil gesteuert. Der Zylinderguss enthielt die Dampfein- und -auslassöffnungen. ⓘ
Motoren, die mit einem Kondensator ausgestattet sind, gehören zu einem anderen Typ als solche, die in die Atmosphäre ausstoßen. ⓘ
Häufig sind noch weitere Komponenten vorhanden: Pumpen (z. B. ein Injektor), um den Kessel während des Betriebs mit Wasser zu versorgen, Kondensatoren, um das Wasser im Kreislauf zu führen und die latente Verdampfungswärme zurückzugewinnen, und Überhitzer, um die Temperatur des Dampfes über den Sättigungspunkt zu erhöhen, sowie verschiedene Mechanismen zur Erhöhung des Zugs für die Feuerräume. Bei der Verwendung von Kohle kann ein Ketten- oder Schneckenschürmechanismus und der dazugehörige Antriebsmotor vorhanden sein, um den Brennstoff von einem Vorratsbehälter (Bunker) zum Feuerraum zu befördern. ⓘ
Wärmequelle
Die zum Sieden des Wassers und zur Erhöhung der Dampftemperatur benötigte Wärme kann aus verschiedenen Quellen stammen, am häufigsten aus der Verbrennung von brennbaren Stoffen mit einer geeigneten Luftzufuhr in einem geschlossenen Raum (z. B. Brennkammer, Feuerraum, Ofen). Bei Modell- oder Spielzeugdampfmaschinen und in einigen wenigen Fällen in Originalgröße kann die Wärmequelle auch ein elektrisches Heizelement sein. ⓘ
Heizkessel
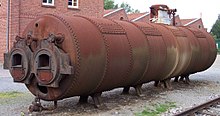
Heizkessel sind Druckbehälter, die das zu kochende Wasser enthalten und so beschaffen sind, dass die Wärme möglichst effektiv auf das Wasser übertragen wird. ⓘ
Die beiden gängigsten Typen sind:
- Wasserrohrkessel
- Das Wasser wird durch Rohre geleitet, die von heißem Gas umgeben sind.
- Feuerrohrkessel
- Das heiße Gas wird durch in Wasser getauchte Rohre geleitet, das gleiche Wasser zirkuliert auch in einem Wassermantel, der die Feuerbüchse umgibt, und bei Lokomotivkesseln mit hoher Leistung auch durch Rohre in der Feuerbüchse selbst (thermische Siphons und Sicherheitsumwälzer). ⓘ
Feuerrohrkessel wurden in der Frühzeit hauptsächlich für die Erzeugung von Hochdruckdampf verwendet (typisch für Dampflokomotiven), wurden aber im späten 19. Jahrhundert für Schiffsantriebe und große stationäre Anwendungen weitgehend von den wirtschaftlicheren Wasserrohrkesseln verdrängt. ⓘ
In vielen Kesseln wird die Temperatur des Dampfes erhöht, nachdem er den Teil des Kessels verlassen hat, in dem er mit dem Wasser in Berührung kommt. Durch die so genannte Überhitzung wird aus "Nassdampf" "überhitzter Dampf". Dadurch wird verhindert, dass der Dampf in den Motorzylindern kondensiert, und der Wirkungsgrad wird erheblich gesteigert. ⓘ
Motoreinheiten
In einer Dampfmaschine nimmt ein Kolben oder eine Dampfturbine oder eine ähnliche Vorrichtung zur Verrichtung mechanischer Arbeit Dampf mit hohem Druck und hoher Temperatur auf und gibt Dampf mit niedrigerem Druck und niedrigerer Temperatur ab, wobei ein möglichst großer Teil der unterschiedlichen Dampfenergie zur Verrichtung mechanischer Arbeit genutzt wird. ⓘ
Diese "Motoreinheiten" werden oft als eigenständige "Dampfmaschinen" bezeichnet. Motoren, die mit Druckluft oder anderen Gasen betrieben werden, unterscheiden sich von Dampfmaschinen nur in Details, die von der Art des Gases abhängen, obwohl Druckluft unverändert in Dampfmaschinen verwendet wurde. ⓘ
Kalte Senke
Wie bei allen Wärmekraftmaschinen muss der größte Teil der Primärenergie als Abwärme mit relativ niedriger Temperatur abgeführt werden. ⓘ
Die einfachste Kältesenke ist die Ableitung des Dampfes in die Umgebung. Dies wird häufig bei Dampflokomotiven eingesetzt, um das Gewicht und die Masse von Kondensatoren zu vermeiden. Ein Teil des freigesetzten Dampfes wird über den Schornstein abgeleitet, um den Zug am Feuer zu erhöhen, was die Motorleistung stark erhöht, aber den Wirkungsgrad verringert. ⓘ
Manchmal wird die Abwärme des Motors selbst genutzt, und in diesen Fällen kann ein sehr hoher Gesamtwirkungsgrad erzielt werden. ⓘ
Dampfmaschinen in stationären Kraftwerken verwenden Oberflächenkondensatoren als Kältesenke. Die Kondensatoren werden mit Wasser aus Ozeanen, Flüssen und Seen gekühlt, oft auch mit Kühltürmen, die Wasser verdampfen, um die Kühlenergie abzuführen. Das dabei entstehende kondensierte Heißwasser (Kondensat) wird dann wieder auf Druck gepumpt und zurück zum Kessel geleitet. Ein Trockenkühlturm ähnelt einem Autokühler und wird dort eingesetzt, wo Wasser sehr teuer ist. Abwärme kann auch durch Verdunstungskühltürme (Nasskühltürme) abgeführt werden, die einen sekundären externen Wasserkreislauf verwenden, der einen Teil der Strömung in die Luft verdampft. ⓘ
Flussschiffe verwendeten ursprünglich einen Strahlkondensator, bei dem kaltes Wasser aus dem Fluss in den Abgasdampf des Motors eingespritzt wird. Kühlwasser und Kondensat vermischen sich. Diese Methode wurde zwar auch auf Seeschiffen angewandt, aber im Allgemeinen war der Kessel schon nach wenigen Tagen Betrieb mit Salzablagerungen überzogen, was die Leistung verringerte und die Gefahr einer Kesselexplosion erhöhte. Ab etwa 1834 wurden auf Schiffen Oberflächenkondensatoren eingesetzt, die die Verschmutzung der Kessel verhinderten und den Wirkungsgrad der Motoren verbesserten. ⓘ
Verdampftes Wasser kann nicht für weitere Zwecke verwendet werden (außer als Regenwasser), während Flusswasser wiederverwendet werden kann. In allen Fällen wird das Kesselspeisewasser der Dampfanlage, das rein gehalten werden muss, vom Kühlwasser oder der Luft getrennt gehalten. ⓘ

Wasserpumpe
Die meisten Dampfkessel verfügen über eine Vorrichtung zur Wasserzufuhr unter Druck, so dass sie kontinuierlich betrieben werden können. Bei Kesseln für Versorgungsunternehmen und in der Industrie werden in der Regel mehrstufige Kreiselpumpen verwendet, es gibt aber auch andere Typen. Eine weitere Möglichkeit, Kesselspeisewasser mit niedrigerem Druck zuzuführen, ist ein Injektor, der einen Dampfstrahl verwendet, der in der Regel vom Kessel kommt. Injektoren wurden in den 1850er Jahren populär, sind aber heute nicht mehr weit verbreitet, außer in Anwendungen wie Dampflokomotiven. Durch die Druckbeaufschlagung des Wassers, das durch den Dampfkessel zirkuliert, kann das Wasser auf eine Temperatur von weit über 100 °C (212 °F), dem Siedepunkt von Wasser bei atmosphärischem Druck, gebracht und damit die Effizienz des Dampfkreislaufs erhöht werden. ⓘ
Überwachung und Kontrolle

Aus Sicherheitsgründen sind fast alle Dampfmaschinen mit Mechanismen zur Überwachung des Kessels ausgestattet, z. B. mit einem Druckmesser und einem Schauglas zur Kontrolle des Wasserstands. ⓘ
Viele stationäre und mobile Maschinen sind außerdem mit einem Regler ausgestattet, der die Drehzahl der Maschine ohne menschliches Zutun regelt. ⓘ
Das nützlichste Instrument zur Analyse der Leistung von Dampfmaschinen ist der Dampfmaschinenanzeiger. Frühe Versionen waren bereits 1851 in Gebrauch, aber der erfolgreichste Indikator wurde von Charles Richard für den Erfinder und Hersteller von Hochgeschwindigkeitsmaschinen Charles Porter entwickelt und 1862 auf der Londoner Ausstellung ausgestellt. Der Dampfmaschinenanzeiger zeichnet den Druck im Zylinder während des gesamten Zyklus auf Papier auf, was zur Erkennung verschiedener Probleme und zur Berechnung der entwickelten Pferdestärken verwendet werden kann. Er wurde routinemäßig von Ingenieuren, Mechanikern und Versicherungsinspektoren verwendet. Der Motoranzeiger kann auch bei Verbrennungsmotoren verwendet werden. Siehe Abbildung des Anzeigediagramms unten (im Abschnitt Arten von Motoreinheiten). ⓘ
Begrenzer

Der Fliehkraftregler wurde 1788 von James Watt für den Einsatz in einer Dampfmaschine übernommen, nachdem Watt's Partner Boulton einen solchen Regler an der Ausrüstung einer Getreidemühle gesehen hatte, die Boulton & Watt bauten. Der Regler konnte eine bestimmte Drehzahl nicht halten, da er bei Laständerungen eine neue konstante Drehzahl annahm. Der Regler war in der Lage, kleinere Schwankungen auszugleichen, wie sie beispielsweise durch die schwankende Wärmebelastung des Kessels verursacht werden. Außerdem neigte er bei jeder Geschwindigkeitsänderung zu Schwingungen. Daher waren Motoren, die nur mit diesem Regler ausgestattet waren, nicht für Arbeiten geeignet, die eine konstante Geschwindigkeit erforderten, wie z. B. das Spinnen von Baumwolle. Der Regler wurde im Laufe der Zeit verbessert, und in Verbindung mit einer variablen Dampfabschaltung war gegen Ende des 19. Jahrhunderts eine gute Geschwindigkeitsregelung als Reaktion auf Laständerungen möglich. ⓘ
Konfiguration der Maschine
Einfache Maschine
Bei einer einfachen Maschine durchläuft die Dampfladung den gesamten Expansionsprozess in einem einzelnen Zylinder, obwohl eine einfache Maschine einen oder mehrere einzelne Zylinder haben kann. Anschließend wird der Dampf direkt in die Atmosphäre oder in einen Kondensator abgeleitet. Wenn sich der Dampf beim Durchströmen einer Hochdruckmaschine ausdehnt, sinkt seine Temperatur, da dem System keine Wärme zugeführt wird; dies wird als adiabatische Expansion bezeichnet und führt dazu, dass der Dampf mit hoher Temperatur in den Zylinder eintritt und mit niedrigerer Temperatur wieder austritt. Dies führt dazu, dass sich der Zylinder bei jedem Hub erwärmt und abkühlt, was eine Quelle der Ineffizienz ist. ⓘ
Der vorherrschende Wirkungsgradverlust bei Dampf-Hubkolbenmotoren ist die Kondensation im Zylinder und die Wiederverdampfung. Der Dampfzylinder und die angrenzenden Metallteile/-anschlüsse arbeiten bei einer Temperatur, die etwa auf halbem Weg zwischen der Sättigungstemperatur beim Dampfeinlass und der dem Auslassdruck entsprechenden Sättigungstemperatur liegt. Wenn Hochdruckdampf in den Arbeitszylinder eingeleitet wird, kondensiert ein Großteil des Hochtemperaturdampfes als Wassertröpfchen auf den Metalloberflächen, wodurch der für die Expansionsarbeit verfügbare Dampf erheblich reduziert wird. Wenn der expandierende Dampf einen niedrigen Druck erreicht (insbesondere während des Auspuffhubs), verdampfen die zuvor im Zylinder/an den Anschlüssen abgelagerten Wassertröpfchen (Wiederverdampfung), und der Dampf verrichtet im Zylinder keine Arbeit mehr. ⓘ
Dem Expansionsverhältnis eines Dampfmaschinenzylinders sind in der Praxis Grenzen gesetzt, da eine Vergrößerung der Zylinderoberfläche das Problem der Kondensation und Wiederverdampfung im Zylinder tendenziell verschärft. Dadurch werden die theoretischen Vorteile, die mit einem hohen Expansionsverhältnis in einem einzelnen Zylinder verbunden sind, zunichte gemacht. ⓘ

Zusammengesetzte Motoren
Eine Methode zur Verringerung des Energieverlusts in einem sehr langen Zylinder wurde 1804 vom britischen Ingenieur Arthur Woolf erfunden, der 1805 seinen Woolf-Hochdruck-Verbundmotor patentieren ließ. Bei der Verbundmaschine entspannt sich der Hochdruckdampf aus dem Kessel in einem Hochdruckzylinder und gelangt dann in einen oder mehrere nachfolgende Niederdruckzylinder. Die vollständige Expansion des Dampfes findet nun in mehreren Zylindern statt, wobei der Gesamttemperaturabfall in jedem Zylinder erheblich reduziert wird. Durch die stufenweise Expansion des Dampfes mit geringerem Temperaturbereich (in jedem Zylinder) wird das oben beschriebene Problem der Kondensation und Wiederverdampfung verringert. Dadurch wird das Ausmaß der Zylindererwärmung und -abkühlung verringert und der Wirkungsgrad des Motors erhöht. Durch die Aufteilung der Expansion auf mehrere Zylinder können die Schwankungen des Drehmoments verringert werden. Um die gleiche Leistung aus einem Zylinder mit niedrigerem Druck zu erzielen, ist ein größeres Zylindervolumen erforderlich, da dieser Dampf ein größeres Volumen einnimmt. Daher werden die Bohrung und in seltenen Fällen der Hub in Niederdruckzylindern vergrößert, was zu größeren Zylindern führt. ⓘ
Doppel-Expansionsmotoren (gewöhnlich als Verbundmotoren bezeichnet) entspannten den Dampf in zwei Stufen. Die Paare können doppelt vorhanden sein, oder die Arbeit des großen Niederdruckzylinders kann aufgeteilt werden, wobei ein Hochdruckzylinder in den einen oder anderen Zylinder ausläuft, so dass sich eine Dreizylinderanordnung ergibt, bei der Zylinder- und Kolbendurchmesser etwa gleich groß sind, wodurch sich die hin- und hergehenden Massen leichter ausbalancieren lassen. ⓘ
Zweizylinder-Verbindungen können wie folgt angeordnet werden:
- Kreuzverbindungen: Die Zylinder liegen nebeneinander.
- Tandem-Verbindungen: Die Zylinder liegen nebeneinander und treiben eine gemeinsame Pleuelstange an.
- Winkelverbindungen: Die Zylinder sind V-förmig angeordnet (in der Regel in einem Winkel von 90°) und treiben eine gemeinsame Kurbel an. ⓘ
Bei Zweizylinder-Verbindungen, die im Eisenbahnbau verwendet werden, sind die Kolben wie bei einem einfachen Zweizylinder um 90° phasenverschoben (geviertelt) mit den Kurbeln verbunden. Bei der Verdoppelung der Doppel-Expansionsgruppe zu einem Vierzylinder-Compound werden die einzelnen Kolben innerhalb der Gruppe normalerweise um 180° ausgewuchtet, wobei die Gruppen um 90° zueinander versetzt sind. In einem Fall (dem ersten Typ des Vauclain-Verbunds) arbeiteten die Kolben in der gleichen Phase und trieben einen gemeinsamen Kreuzkopf und eine Kurbelwelle an, die wiederum wie bei einem Zweizylindermotor um 90° versetzt waren. Bei der Dreizylinder-Motorenkombination wurden die Kurbeln des ND-Motors entweder auf 90° und die des HD-Motors auf 135° zu den beiden anderen Kurbeln eingestellt, oder in einigen Fällen wurden alle drei Kurbeln auf 120° eingestellt. ⓘ
Der Einsatz von Verbundkurbeln war bei Industrie- und Straßenmotoren üblich und bei Schiffsmotoren nach 1880 nahezu universell; bei Eisenbahnlokomotiven war er nicht durchgängig beliebt, da er oft als kompliziert empfunden wurde. Dies ist zum Teil auf das raue Betriebsumfeld der Eisenbahn und den begrenzten Platz, den das Lichtraumprofil bietet, zurückzuführen (insbesondere in Großbritannien, wo Compounding nie üblich war und auch nach 1930 nicht eingesetzt wurde). In vielen anderen Ländern war sie jedoch beliebt, auch wenn sie nie in der Mehrheit war. ⓘ
Mehrfachexpansionsmotoren

Es ist eine logische Erweiterung der (oben beschriebenen) Verbundmaschine, die Expansion in noch mehr Stufen aufzuteilen, um den Wirkungsgrad zu erhöhen. Das Ergebnis ist der Mehrfachexpansionsmotor. Solche Motoren verwenden entweder drei oder vier Expansionsstufen und werden als Dreifach- bzw. Vierfachexpansionsmotoren bezeichnet. Diese Motoren verwenden eine Reihe von Zylindern mit progressiv zunehmendem Durchmesser. Diese Zylinder sind so konstruiert, dass die Arbeit für jede Expansionsstufe zu gleichen Teilen aufgeteilt wird. Wie beim Zweifachexpansionsmotor können bei Platzmangel zwei kleinere Zylinder für die Niederdruckstufe verwendet werden. Bei Mehrfachexpansionsmotoren waren die Zylinder in der Regel in Reihe angeordnet, aber es gab auch verschiedene andere Anordnungen. Im späten 19. Jahrhundert wurde das Yarrow-Schlick-Tweedy-Ausgleichssystem" bei einigen Schiffsmotoren mit Dreifachexpansion verwendet. Bei Y-S-T-Motoren wurden die Niederdruckexpansionsstufen auf zwei Zylinder verteilt, einen an jedem Ende des Motors. Dadurch konnte die Kurbelwelle besser ausgewuchtet werden, was zu einem ruhigeren, schneller reagierenden und vibrationsärmeren Motor führte. Dies machte den Vierzylinder-Dreifach-Expansionsmotor bei großen Passagierschiffen (wie der Olympic-Klasse) beliebt, doch wurde er schließlich durch den praktisch vibrationsfreien Turbinenmotor ersetzt. Es ist jedoch anzumerken, dass die Dreifach-Expansions-Kolbendampfmaschinen für den Antrieb der Liberty-Schiffe des Zweiten Weltkriegs verwendet wurden, die bei weitem größte Anzahl identischer Schiffe, die jemals gebaut wurde. Über 2700 Schiffe wurden in den Vereinigten Staaten nach einem britischen Originalentwurf gebaut. ⓘ
Das Bild in diesem Abschnitt zeigt eine Animation einer Dreifach-Expansionsmaschine. Der Dampf strömt von links nach rechts durch die Maschine. Der Ventilkasten für jeden der Zylinder befindet sich links vom entsprechenden Zylinder. ⓘ
Dampfmaschinen an Land konnten ihren Dampf in die Atmosphäre ablassen, da Speisewasser in der Regel leicht verfügbar war. Vor und während des Ersten Weltkriegs dominierte die Expansionsmaschine in der Schifffahrt, wo eine hohe Schiffsgeschwindigkeit nicht unbedingt erforderlich war. Sie wurde jedoch von der britischen Erfindung der Dampfturbine abgelöst, wenn eine hohe Geschwindigkeit erforderlich war, z. B. bei Kriegsschiffen wie den Dreadnought-Schlachtschiffen und Ozeandampfern. Die HMS Dreadnought von 1905 war das erste große Kriegsschiff, das die bewährte Technologie der Kolbenmaschine durch die damals neuartige Dampfturbine ersetzte. ⓘ
Arten von Motoreinheiten
Hubkolben


Bei den meisten Hubkolbenmotoren kehrt der Dampf bei jedem Hub seine Strömungsrichtung um (Gegenstrom) und tritt am gleichen Ende des Zylinders ein und aus. Der vollständige Motorzyklus umfasst eine Kurbelumdrehung und zwei Kolbenhübe; der Zyklus besteht außerdem aus vier Vorgängen - Einlass, Expansion, Auslass, Verdichtung. Diese Vorgänge werden durch Ventile gesteuert, die häufig in einer Dampfkammer neben dem Zylinder arbeiten; die Ventile verteilen den Dampf durch Öffnen und Schließen von Dampföffnungen, die mit dem/den Zylinderende(n) in Verbindung stehen, und werden durch Ventiltriebe angetrieben, von denen es viele Arten gibt. ⓘ
Die einfachsten Ventiltriebe bewirken Ereignisse fester Länge während des Maschinenzyklus und lassen die Maschine oft nur in eine Richtung rotieren. Viele verfügen jedoch über einen Umkehrmechanismus, mit dem zusätzlich Dampf eingespart werden kann, da Geschwindigkeit und Schwung durch allmähliche "Verkürzung der Abschaltung" bzw. Verkürzung des Einlassvorgangs gewonnen werden; dies wiederum verlängert die Expansionszeit proportional. Da jedoch in der Regel ein und dasselbe Ventil beide Dampfströme steuert, wirkt sich eine kurze Einlassunterbrechung nachteilig auf die Auslass- und Kompressionszeit aus, die idealerweise immer ziemlich konstant gehalten werden sollten; ist die Auslasszeit zu kurz, kann der gesamte Auslassdampf den Zylinder nicht entleeren, was zu einer Drosselung und einer übermäßigen Kompression führt ("kick back"). ⓘ
In den 1840er- und 1850er-Jahren wurde versucht, dieses Problem durch verschiedene patentierte Ventilgetriebe mit einem separaten Expansionsventil mit variabler Abschaltung zu lösen, das auf der Rückseite des Hauptschiebers angebracht war; letzterer hatte in der Regel eine feste oder begrenzte Abschaltung. Die kombinierte Anordnung bot eine gute Annäherung an die idealen Ereignisse, allerdings auf Kosten erhöhter Reibung und Abnutzung, und der Mechanismus war tendenziell kompliziert. Die übliche Kompromisslösung bestand darin, eine Überlappung zu schaffen, indem die Reibflächen des Ventils so verlängert wurden, dass sie die Öffnung auf der Einlassseite überlappten, was zur Folge hatte, dass die Auslassseite nach dem Abschalten auf der Einlassseite länger geöffnet blieb. Dieses Verfahren wird seither für die meisten Zwecke als zufriedenstellend angesehen und ermöglicht die Verwendung der einfacheren Stephenson-, Joy- und Walschaert-Bewegungen. Corliss- und spätere Tellerventilgetriebe verfügten über getrennte Einlass- und Auslassventile, die durch Auslösemechanismen oder Nocken angetrieben wurden, die so profiliert waren, dass sie einen idealen Ablauf gewährleisteten; die meisten dieser Getriebe setzten sich außerhalb des stationären Marktes aufgrund verschiedener anderer Probleme wie Leckagen und empfindlicherer Mechanismen nicht durch. ⓘ
Verdichtung
Bevor die Auslassphase ganz abgeschlossen ist, schließt sich die Auslassseite des Ventils, wodurch ein Teil des Auslassdampfes im Zylinder abgesperrt wird. Dadurch wird die Kompressionsphase eingeleitet, in der sich ein Dampfpolster bildet, gegen das der Kolben arbeitet, während seine Geschwindigkeit rasch abnimmt; außerdem wird der Druck- und Temperaturschock vermieden, der andernfalls durch den plötzlichen Eintritt des Hochdruckdampfes zu Beginn des folgenden Zyklus verursacht würde. ⓘ
Blei
Die oben genannten Effekte werden durch eine Vorspannung noch verstärkt: Wie später bei der Verbrennungskraftmaschine entdeckt, hat es sich seit Ende der 1830er Jahre als vorteilhaft erwiesen, die Einlassphase vorzuverlegen, indem das Ventil mit einer Vorspannung versehen wird, so dass der Einlass etwas vor dem Ende des Auslasshubs erfolgt, um das Freivolumen, das die Öffnungen und die Zylinderböden umfasst (nicht Teil des vom Kolben durchströmten Volumens), zu füllen, bevor der Dampf beginnt, Kraft auf den Kolben auszuüben. ⓘ
Uniflow- (oder Unaflow-) Maschine

Die Tellerventile werden von der rotierenden Nockenwelle im oberen Teil gesteuert. Der unter hohem Druck stehende Dampf tritt ein (rot) und tritt aus (gelb). ⓘ
Mit Gleichstrommotoren wird versucht, die Schwierigkeiten zu beheben, die sich aus dem üblichen Gegenstromkreislauf ergeben, bei dem bei jedem Hub die Öffnungen und die Zylinderwände durch den vorbeiströmenden Abdampf gekühlt werden, während der heißere einströmende Frischdampf einen Teil seiner Energie für die Wiederherstellung der Arbeitstemperatur verschwendet. Mit dem Uniflow soll dieser Mangel behoben und der Wirkungsgrad verbessert werden, indem eine zusätzliche Öffnung geschaffen wird, die am Ende jedes Hubes vom Kolben freigelegt wird, so dass der Dampf nur in eine Richtung strömt. Auf diese Weise erreicht der Uniflow-Motor mit einfacher Ausdehnung einen Wirkungsgrad, der dem klassischer Verbundmotoren entspricht, mit dem zusätzlichen Vorteil einer besseren Teillastleistung und einem mit Turbinen vergleichbaren Wirkungsgrad für kleinere Motoren unter 1000 PS. Der Wärmeausdehnungsgradient, den Uniflow-Motoren entlang der Zylinderwand erzeugen, führt jedoch zu praktischen Schwierigkeiten... ⓘ
Turbinenmotoren
Eine Dampfturbine besteht aus einem oder mehreren Rotoren (rotierenden Scheiben), die auf einer Antriebswelle montiert sind und sich mit einer Reihe von Statoren (statischen Scheiben) abwechseln, die am Turbinengehäuse befestigt sind. Die Rotoren haben am äußeren Rand eine propellerartige Anordnung von Schaufeln. Der Dampf wirkt auf diese Schaufeln und erzeugt eine Drehbewegung. Das Leitrad besteht aus einer ähnlichen, aber feststehenden Reihe von Schaufeln, die dazu dienen, den Dampfstrom auf die nächste Rotorstufe umzuleiten. Die Abgase einer Dampfturbine werden häufig in einen Oberflächenkondensator geleitet, der ein Vakuum erzeugt. Die Stufen einer Dampfturbine sind in der Regel so angeordnet, dass aus einer bestimmten Dampfgeschwindigkeit und einem bestimmten Dampfdruck die maximale potenzielle Arbeit herausgeholt werden kann, was zu einer Reihe unterschiedlich großer Hoch- und Niederdruckstufen führt. Turbinen sind nur dann effizient, wenn sie sich mit relativ hoher Geschwindigkeit drehen. Daher sind sie in der Regel mit einem Untersetzungsgetriebe verbunden, um Anwendungen mit niedrigeren Geschwindigkeiten anzutreiben, wie z. B. Schiffspropeller. In der überwiegenden Mehrheit der großen Stromerzeugungsanlagen sind die Turbinen direkt mit den Generatoren verbunden, ohne Untersetzungsgetriebe. Typische Drehzahlen sind 3600 Umdrehungen pro Minute (RPM) in den Vereinigten Staaten mit 60-Hertz-Strom und 3000 RPM in Europa und anderen Ländern mit 50-Hertz-Stromsystemen. In der Kernenergie laufen die Turbinen in der Regel mit der Hälfte dieser Drehzahlen, d. h. mit 1800 bzw. 1500 Umdrehungen pro Minute. Ein Turbinenrotor kann auch nur in einer Richtung Strom liefern. Daher ist in der Regel eine Umkehrstufe oder ein Getriebe erforderlich, wenn die Leistung in der entgegengesetzten Richtung benötigt wird. ⓘ
Dampfturbinen liefern eine direkte Rotationskraft und benötigen daher keinen Gestängemechanismus zur Umwandlung einer Hin- und Herbewegung in eine Drehbewegung. Dadurch erzeugen sie gleichmäßigere Rotationskräfte an der Abtriebswelle. Dies trägt zu einem geringeren Wartungsbedarf und einem geringeren Verschleiß der von ihnen angetriebenen Maschinen bei als bei einer vergleichbaren Kolbenmaschine. ⓘ
Der Haupteinsatzbereich von Dampfturbinen ist die Stromerzeugung (in den 1990er Jahren wurden etwa 90 % der weltweiten Stromerzeugung mit Dampfturbinen erzeugt). Durch den in letzter Zeit weit verbreiteten Einsatz großer Gasturbineneinheiten und typischer Kombikraftwerke ist dieser Prozentsatz jedoch auf 80 % gesunken. Bei der Stromerzeugung passt die hohe Drehzahl der Turbinen gut zur Drehzahl moderner Stromgeneratoren, die in der Regel direkt mit ihren Antriebsturbinen verbunden sind. In der Schifffahrt dominierten Dampfturbinen mit Untersetzungsgetriebe (obwohl die Turbinia über eine direkte Verbindung zwischen Turbine und Propeller ohne Untersetzungsgetriebe verfügt) den Antrieb großer Schiffe im späten 20. In den letzten Jahrzehnten haben Diesel-Hubkolbenmotoren und Gasturbinen den Dampfantrieb in der Schifffahrt fast vollständig verdrängt. ⓘ
Praktisch alle Kernkraftwerke erzeugen Strom, indem sie Wasser erhitzen, um Dampf zu erzeugen, der eine Turbine antreibt, die mit einem elektrischen Generator verbunden ist. Schiffe und U-Boote mit Nuklearantrieb nutzen entweder direkt eine Dampfturbine für den Hauptantrieb, wobei Generatoren für den Hilfsantrieb sorgen, oder sie verwenden ein turbo-elektrisches Getriebe, bei dem der Dampf einen Turbogeneratorsatz antreibt und der Antrieb durch Elektromotoren erfolgt. Eine begrenzte Anzahl von Dampfturbinen-Eisenbahnlokomotiven wurde hergestellt. Einige nicht kondensierende Lokomotiven mit Direktantrieb wurden mit einigem Erfolg im Güterfernverkehr in Schweden und im Personenschnellverkehr in Großbritannien eingesetzt, wurden aber nicht wiederholt. Anderswo, vor allem in den Vereinigten Staaten, wurden fortschrittlichere Konstruktionen mit elektrischem Antrieb versuchsweise gebaut, aber nicht reproduziert. Es stellte sich heraus, dass Dampfturbinen nicht ideal für den Eisenbahnbetrieb geeignet waren, und diese Lokomotiven konnten den klassischen Dampfantrieb nicht in dem Maße verdrängen, wie es die moderne Diesel- und Elektrotraktion getan hat. ⓘ

Dampfmaschinen mit oszillierendem Zylinder
Eine Dampfmaschine mit oszillierendem Zylinder ist eine Variante der einfachen Expansionsdampfmaschine, die keine Ventile benötigt, um den Dampf in den und aus dem Zylinder zu leiten. Anstelle von Ventilen schwingt der gesamte Zylinder, so dass ein oder mehrere Löcher im Zylinder mit Löchern in einer festen Anschlussfläche oder im Drehzapfen (Trunnion) übereinstimmen. Diese Motoren werden wegen ihrer Einfachheit hauptsächlich in Spielzeugen und Modellen verwendet, aber auch in großen Arbeitsmaschinen, vor allem auf Schiffen, wo ihre Kompaktheit geschätzt wird. ⓘ
Rotierende Dampfmaschinen
Es ist möglich, einen Mechanismus auf der Grundlage eines kolbenlosen Rotationsmotors wie des Wankelmotors anstelle der Zylinder und des Ventiltriebs einer herkömmlichen Dampfmaschine mit hin- und hergehender Bewegung zu verwenden. Von der Zeit James Watts bis heute wurden viele solcher Motoren entworfen, aber nur relativ wenige wurden tatsächlich gebaut und noch weniger gingen in Serie; weitere Einzelheiten finden Sie unter dem Link am Ende des Artikels. Das Hauptproblem ist die Schwierigkeit, die Rotoren abzudichten, um sie angesichts von Verschleiß und Wärmeausdehnung dampfdicht zu machen; die daraus resultierenden Leckagen machten sie sehr ineffizient. Das Fehlen einer expansiven Arbeitsweise oder eines Mittels zur Kontrolle der Abschaltung ist ebenfalls ein ernstes Problem bei vielen dieser Konstruktionen. ⓘ
In den 1840er Jahren war klar, dass das Konzept inhärente Probleme aufwies, und Rotationsmotoren wurden in der Fachpresse mit einigem Spott bedacht. Mit dem Aufkommen der Elektrizität und den offensichtlichen Vorteilen des direkten Antriebs eines Dynamos durch einen schnelllaufenden Motor erwachte das Interesse in den 1880er und 1890er Jahren wieder, und einige wenige Konstruktionen hatten einen begrenzten Erfolg. ⓘ
Von den wenigen Konstruktionen, die in großen Stückzahlen hergestellt wurden, sind die der Hult Brothers Rotary Steam Engine Company aus Stockholm, Schweden, und der Kugelmotor von Beauchamp Tower hervorzuheben. Die Tower-Motoren wurden von der Great Eastern Railway zum Antrieb der Beleuchtungsdynamos ihrer Lokomotiven und von der Admiralität zum Antrieb der Dynamos an Bord der Schiffe der Royal Navy verwendet. In diesen Nischenanwendungen wurden sie schließlich durch Dampfturbinen ersetzt. ⓘ

Raketentyp
Der Aeolipile steht für die Nutzung von Dampf nach dem Prinzip der Raketenreaktion, wenn auch nicht für den direkten Vortrieb. ⓘ
In neuerer Zeit wurde Dampf in begrenztem Umfang für die Raketentechnik genutzt - insbesondere für Raketenautos. Bei der Dampfraketenfahrt wird ein Druckbehälter mit heißem Wasser unter hohem Druck gefüllt und ein Ventil geöffnet, das zu einer geeigneten Düse führt. Durch den Druckabfall kocht ein Teil des Wassers sofort und der Dampf tritt durch eine Düse aus, wodurch eine Antriebskraft erzeugt wird. ⓘ
Die Kutsche von Ferdinand Verbiest wurde 1679 durch ein Aeolipil angetrieben. ⓘ
Sicherheit
Dampfmaschinen verfügen über Kessel und andere Komponenten, die Druckbehälter sind und eine große Menge potenzieller Energie enthalten. Dampfaustritt und Kesselexplosionen (typischerweise BLEVEs) können und haben in der Vergangenheit zu großen Verlusten an Menschenleben geführt. Zwar gibt es in den verschiedenen Ländern unterschiedliche Normen, doch gelten strenge gesetzliche Vorschriften, Prüfungen, Schulungen, Sorgfalt bei der Herstellung, beim Betrieb und bei der Zertifizierung, um die Sicherheit zu gewährleisten. ⓘ
Fehlermöglichkeiten können sein:
- Überdruck im Heizkessel
- zu wenig Wasser im Kessel, was zur Überhitzung und zum Ausfall des Kessels führt
- Ablagerungen und Kalkablagerungen, die insbesondere bei Flussschiffen, die schmutziges Speisewasser verwenden, zu lokalen Hot Spots führen
- Versagen des Druckbehälters des Kessels aufgrund unzureichender Konstruktion oder Wartung.
- Dampfaustritt aus Rohrleitungen/Kessel mit Verbrühungsgefahr ⓘ
Dampfmaschinen verfügen häufig über zwei unabhängige Mechanismen, die sicherstellen, dass der Druck im Kessel nicht zu hoch wird; einer kann vom Benutzer eingestellt werden, der zweite ist in der Regel als ultimative Ausfallsicherung konzipiert. Bei solchen Sicherheitsventilen wurde traditionell ein einfacher Hebel verwendet, um ein Kegelventil im oberen Teil des Kessels zurückzuhalten. Ein Ende des Hebels trug ein Gewicht oder eine Feder, die das Ventil gegen den Dampfdruck festhielt. Frühe Ventile konnten von den Lokführern verstellt werden, was zu vielen Unfällen führte, wenn ein Lokführer das Ventil herunterdrehte, um einen höheren Dampfdruck und mehr Leistung der Maschine zu ermöglichen. Der neuere Typ von Sicherheitsventilen verwendet ein einstellbares, federbelastetes Ventil, das so verriegelt ist, dass das Bedienungspersonal die Einstellung nicht manipulieren kann, es sei denn, eine Dichtung wird widerrechtlich gebrochen. Diese Anordnung ist wesentlich sicherer. ⓘ
Im Scheitel des Feuerraums des Kessels können sich Schmelzsicherungsschrauben aus Blei befinden. Sinkt der Wasserstand, so dass die Temperatur des Feuerraumbodens deutlich ansteigt, schmilzt das Blei, der Dampf entweicht und warnt das Bedienungspersonal, das dann das Feuer manuell unterdrücken kann. Außer bei den kleinsten Kesseln hat der entweichende Dampf kaum Auswirkungen auf die Eindämmung des Feuers. Außerdem ist die Fläche der Stopfen zu klein, um den Dampfdruck erheblich zu senken und den Kessel drucklos zu machen. Wären sie größer, würde das Volumen des entweichenden Dampfes selbst die Mannschaft gefährden. ⓘ
Dampfkreislauf

Der Rankine-Zyklus ist die grundlegende thermodynamische Grundlage der Dampfmaschine. Der Zyklus ist eine Anordnung von Komponenten, wie sie typischerweise für die einfache Stromerzeugung verwendet wird, und nutzt den Phasenwechsel von Wasser (kochendes Wasser erzeugt Dampf, kondensierender Abdampf erzeugt flüssiges Wasser), um ein praktisches Wärme-/Kraftumwandlungssystem zu schaffen. Die Wärme wird einem geschlossenen Kreislauf von außen zugeführt, wobei ein Teil der zugeführten Wärme in Arbeit umgewandelt wird und die Abwärme in einem Kondensator abgeführt wird. Der Rankine-Kreislauf wird in praktisch allen Anwendungen der Dampfenergieerzeugung eingesetzt. In den 1990er Jahren erzeugten Rankine-Dampfkreisläufe etwa 90 % der weltweit genutzten elektrischen Energie, einschließlich praktisch aller Solar-, Biomasse-, Kohle- und Kernkraftwerke. Benannt ist er nach William John Macquorn Rankine, einem schottischen Universalgelehrten. ⓘ
Der Rankine-Zyklus wird manchmal auch als praktischer Carnot-Zyklus bezeichnet, da das TS-Diagramm bei Verwendung einer effizienten Turbine dem Carnot-Zyklus zu ähneln beginnt. Der Hauptunterschied besteht darin, dass die Wärmezufuhr (im Kessel) und die Wärmeabfuhr (im Kondensator) im Rankine-Zyklus isobare (konstanter Druck) und im theoretischen Carnot-Zyklus isotherme (konstante Temperatur) Prozesse sind. In diesem Zyklus wird eine Pumpe verwendet, um das Arbeitsmittel unter Druck zu setzen, das vom Kondensator in flüssiger und nicht in gasförmiger Form aufgenommen wird. Das Pumpen des flüssigen Arbeitsmittels während des Zyklus erfordert nur einen Bruchteil der Energie für den Transport im Vergleich zu der Energie, die benötigt wird, um das gasförmige Arbeitsmittel in einem Kompressor zu verdichten (wie im Carnot-Kreislauf). Der Zyklus einer Kolben-Dampfmaschine unterscheidet sich von dem einer Turbine durch die Kondensation und Wiederverdampfung, die im Zylinder oder in den Dampfeinlasskanälen stattfindet. ⓘ
Das Arbeitsmedium in einem Rankine-Kreislauf kann als geschlossener Kreislauf arbeiten, bei dem das Arbeitsmedium kontinuierlich recycelt wird, oder als "offener Kreislauf", bei dem der Abdampf direkt in die Atmosphäre abgegeben wird und eine separate Wasserquelle den Kessel speist. Normalerweise wird Wasser aufgrund seiner vorteilhaften Eigenschaften (ungiftig und nicht reaktiv, reichlich vorhanden, kostengünstig) und seiner thermodynamischen Eigenschaften als Arbeitsmittel verwendet. Quecksilber ist das Arbeitsmittel in der Quecksilberdampfturbine. Niedrig siedende Kohlenwasserstoffe können in einem binären Kreislauf verwendet werden. ⓘ
Die Dampfmaschine trug viel zur Entwicklung der thermodynamischen Theorie bei; die einzigen Anwendungen der wissenschaftlichen Theorie, die die Dampfmaschine beeinflussten, waren jedoch die ursprünglichen Konzepte zur Nutzung der Kraft des Dampfes und des atmosphärischen Drucks sowie die Kenntnis der Eigenschaften von Wärme und Dampf. Die experimentellen Messungen, die Watt an einer Modelldampfmaschine durchführte, führten zur Entwicklung des separaten Kondensators. Watt entdeckte unabhängig davon die latente Wärme, was von dem ursprünglichen Entdecker Joseph Black bestätigt wurde, der Watt auch bei den experimentellen Verfahren beriet. Watt wusste auch, dass sich der Siedepunkt von Wasser mit dem Druck ändert. Ansonsten waren die Verbesserungen am Motor selbst eher mechanischer Natur. Die thermodynamischen Konzepte des Rankine-Zyklus vermittelten den Ingenieuren das nötige Verständnis für die Berechnung des Wirkungsgrads, was die Entwicklung moderner Hochdruck- und Hochtemperaturkessel und der Dampfturbine förderte. ⓘ
Wirkungsgrad
Der Wirkungsgrad eines Maschinenzyklus lässt sich berechnen, indem man die von der Maschine erzeugte mechanische Arbeit durch die Energie teilt, die der Maschine durch die Verbrennung des Brennstoffs zugeführt wird. ⓘ
Das historische Maß für den Wirkungsgrad einer Dampfmaschine war ihre "Leistung". Das Konzept der Leistung wurde erstmals von Watt eingeführt, um zu zeigen, wie viel effizienter seine Maschinen im Vergleich zu den früheren Newcomen-Konstruktionen waren. Die Leistung ist die Anzahl der Fuß-Pfund Arbeit, die bei der Verbrennung von einem Scheffel (94 Pfund) Kohle geleistet wird. Die besten Exemplare der Newcomen-Konstruktionen hatten eine Leistung von etwa 7 Millionen, aber die meisten lagen eher bei 5 Millionen. Watt's ursprüngliche Niederdruck-Konstruktionen konnten bis zu 25 Millionen Arbeit leisten, lagen aber im Durchschnitt bei 17 Millionen. Dies war eine dreifache Verbesserung gegenüber der durchschnittlichen Newcomen-Konstruktion. Frühe Watt-Motoren, die mit Hochdruckdampf ausgestattet waren, verbesserten diesen Wert auf 65 Millionen. ⓘ
Keine Wärmekraftmaschine kann effizienter sein als der Carnot-Zyklus, bei dem Wärme von einem Reservoir mit hoher Temperatur zu einem Reservoir mit niedriger Temperatur transportiert wird, wobei der Wirkungsgrad von der Temperaturdifferenz abhängt. Der Wirkungsgrad hängt von der Temperaturdifferenz ab. Um den höchsten Wirkungsgrad zu erzielen, sollten Dampfmaschinen mit einer möglichst hohen Dampftemperatur (Heißdampf) betrieben werden und die Abwärme bei einer möglichst niedrigen Temperatur abgeben. ⓘ
Der Wirkungsgrad eines Rankine-Prozesses wird in der Regel durch das Arbeitsmedium begrenzt. Ohne dass der Druck des Arbeitsmediums überkritische Werte erreicht, ist der Temperaturbereich, in dem der Kreislauf arbeiten kann, klein; bei Dampfturbinen liegen die Turbineneintrittstemperaturen in der Regel bei 565 °C (der Kriechgrenze von Edelstahl) und die Kondensatortemperaturen bei etwa 30 °C. Daraus ergibt sich ein theoretischer Carnot-Wirkungsgrad von etwa 63 %, verglichen mit einem tatsächlichen Wirkungsgrad von 42 % in einem modernen Kohlekraftwerk. Diese niedrige Turbineneintrittstemperatur (im Vergleich zu einer Gasturbine) ist der Grund, warum der Rankine-Zyklus häufig als Bottoming-Zyklus in Gas- und Dampfturbinenkraftwerken eingesetzt wird. ⓘ
Ein Hauptvorteil des Rankine-Zyklus besteht darin, dass während der Verdichtungsphase relativ wenig Arbeit für den Antrieb der Pumpe erforderlich ist, da sich das Arbeitsmedium zu diesem Zeitpunkt in seiner flüssigen Phase befindet. Durch die Kondensation der Flüssigkeit verbraucht die von der Pumpe benötigte Arbeit nur 1 bis 3 % der Leistung der Turbine (oder des Hubkolbenmotors) und trägt zu einem wesentlich höheren Wirkungsgrad für einen echten Zyklus bei. Der Vorteil dieses Verfahrens geht aufgrund der niedrigeren Wärmezufuhrtemperatur etwas verloren. Gasturbinen beispielsweise haben Turbineneintrittstemperaturen von nahezu 1500 °C. Dennoch sind die Wirkungsgrade von großen Dampfkreisläufen und großen modernen Gasturbinen mit einfachem Kreislauf recht gut vergleichbar. ⓘ
In der Praxis hat ein Dampfmaschinenkreislauf, der den Dampf an die Atmosphäre abgibt, in der Regel einen Wirkungsgrad (einschließlich Kessel) im Bereich von 1-10 %. Mit einem zusätzlichen Kondensator, Corliss-Ventilen, Mehrfachexpansion und hohem Dampfdruck/-temperatur kann er jedoch erheblich verbessert werden. Historisch gesehen liegt er im Bereich von 10-20 %, und sehr selten etwas höher. ⓘ
Ein modernes, großes Elektrizitätskraftwerk (mit einer elektrischen Leistung von mehreren hundert Megawatt) mit Dampfzwischenüberhitzung, Economizer usw. erreicht einen Wirkungsgrad im mittleren 40 %-Bereich, wobei die effizientesten Anlagen einen thermischen Wirkungsgrad von nahezu 50 % erreichen. ⓘ
Es ist auch möglich, die Abwärme mit Hilfe der Kraft-Wärme-Kopplung zu nutzen, bei der die Abwärme zur Erwärmung einer Arbeitsflüssigkeit mit niedrigerem Siedepunkt oder als Wärmequelle für Fernwärme über gesättigten Niederdruckdampf verwendet wird. ⓘ
Eine Dampflokomotive - eine GNR N2 Class No.1744 in Weybourne nr. Sheringham, Norfolk
Britische pferdegezogene Feuerwehrspritze mit dampfbetriebener Wasserpumpe ⓘ
Wirkungsweise einer Kolbendampfmaschine
Die Kolbendampfmaschine setzt thermodynamische Energie (Dampfdruck) aus Dampferzeugern in mechanische Rotationsenergie um. Dabei bewegt sich ein Kolben in dem zugehörigen Zylinder hin und her, er führt eine oszillierende Bewegung aus. Benötigt wird für die mechanische Nutzenergie jedoch zumeist eine Rotationsbewegung. ⓘ
Die Hinbewegung des Kolbens wird mit Druck des Dampfes als Arbeitstakt ausgeführt. Die Rückbewegung wird bei einseitig beaufschlagtem Kolben (einfachwirkende Dampfmaschine) aus gespeicherter Rotations-Schwungenergie ausgeführt. Bei zweiseitig beaufschlagtem Kolben (doppeltwirkende Dampfmaschine) hingegen wird die Rückbewegung des Kolbens ebenfalls als Arbeitstakt verrichtet, per Dampfdruck-Ansteuerung nunmehr auf die Unterseite des Kolbens. ⓘ
Die Dampfzufuhr in den Zylinder steuert entweder ein Schieber oder sie erfolgt über Ventile. Der Kolben wird mit dem Druck erst nach unten bzw. in Richtung der Kurbelwelle verschoben. Die Linearbewegung des Kolbens wird mittels Kreuzkopf und Pleuel als Koppelglied am Kurbelzapfen der Kurbelwelle in eine Rotationsbewegung umgesetzt. Das Pleuel schiebt anschließend (im einseitigen Betrieb) mit der im Schwungrad und in der Kurbelwelle gespeicherten Rotationsenergie den Kolben wieder aus der unteren Lage linear zurück in seine obere Ausgangsposition. ⓘ
Das Arbeitsverfahren einer Dampfmaschine ist somit in zwei Takte gegliedert und ist daher ein Zweitaktverfahren. ⓘ
Niederdruckdampfmaschine
Bei der Niederdruckdampfmaschine wird der Dampf mit einem leichten Überdruck von einigen 100 mbar aufgegeben. ⓘ
Getrennter Kondensator
Im Gegensatz zur Newcomen-Dampfmaschine wird nicht nur bei der Kondensation, sondern auch bei der Befüllung des Zylinders Arbeit verrichtet. Dies führt zur Steigerung der Leistungsfähigkeit und war Ausgangspunkt für die Weiterentwicklung der Dampfmaschine zu höheren Dampfdrücken. Dabei wurde für die Kondensation durch eingespritztes Kühlwasser ein eigener Behälter vorgesehen, um die Abkühlung des Arbeitszylinders zu vermeiden. Die bekanntesten Vertreter dieser Bauart waren die Dampfmaschinen von James Watt ab etwa 1769 (siehe unten). ⓘ
Doppeltwirkende Maschine
Watt entwickelte die einfachwirkende Dampfmaschine, die den Kolben nur von einer Seite beaufschlagt, zur doppeltwirkenden weiter, bei der der Kolben abwechselnd von beiden Seiten beaufschlagt wird. Dies erbrachte eine Steigerung von Wirkungsgrad und Leistung, da der Leerhub entfiel. Man ging dann dazu über, das Schwungrad über einen Kurbeltrieb direkt anzutreiben, womit eine Senkung der Masse verbunden war, weil das Balancier entfiel. ⓘ
Verbunddampfmaschine
Eine Verbunddampfmaschine oder Mehrfachexpansionsmaschine ist eine Dampfmaschine mit mindestens zwei in Dampfrichtung nacheinander geschalteten Arbeitseinheiten. ⓘ
Gleichstromdampfmaschine
Diese Bauart wurde um 1908 vom Geheimen Regierungsrat und Professor an der Technischen Hochschule J. Stumpf vorgestellt. Bei einer Gleichstromdampfmaschine findet beim Ausstoßen des entspannten Dampfes kein Wechsel der Strömungsrichtung statt. Ein- und Ausströmung sind voneinander getrennt, die Ausströmung erfolgt durch Ausströmschlitze in der Mitte der Zylinder, die Einströmung wie gehabt von den Zylinderenden her. Durch diese Bauweise konnten die Abkühlungsverluste deutlich gesenkt werden, allerdings wird das mit erheblich längeren Zylindern erkauft. Die Einführung dieser Maschinen scheiterte am seinerzeit zu geringen üblichen Dampfdruck von 12 bis 14 bar, erst bei Drücken ab 20 bar hätte sich diese Konstruktion bewährt. ⓘ
Geschichte der Dampfmaschine
Weitere Entwicklungen
Mit diesen Entwicklungen sowie weiteren technischen Verbesserungen wurden Dampfmaschinen ab der zweiten Hälfte des 18. Jahrhunderts – zumindest im Kohlebergbau – nun auch wirtschaftlich. Das erste funktionsfähige Dampfschiff konstruierte 1783 der Franzose Claude François Jouffroy d’Abbans. 1804 baute Richard Trevithick die erste auf Schienen fahrende Dampflokomotive. Wenn auch allmählich weitere Anwendungsgebiete in der Industrie erschlossen wurden, dauerte es bis in die 1860er Jahre, bis Dampfmaschinen in England massenhaft verwendet wurden. Ein Grund war die notwendige Verwendung von Eisen als Werkstoff für die entsprechenden Maschinen. Dies war eine neue Technologie, da vorher viele Maschinenteile noch aus Holz gefertigt wurden. In anderen Staaten wie beispielsweise Frankreich und den USA, wo die Wasserkraft ein starker Konkurrent war, erfolgte der endgültige Durchbruch der Dampfmaschine noch etwas später. ⓘ
Auch der technische Übergang vom Segel- zum Dampfschiff dauerte einige Jahrzehnte. Erst 1889 wurde mit dem von Alexander Carlisle (dem späteren Chefdesigner der Olympic-Klasse) konstruierten, 20 Knoten schnellen White-Star-Liner Teutonic der erste Hochsee-Dampfer ohne Segeleinrichtung in Dienst gestellt. ⓘ
Hochdruck und Heißdampf
Eine Hochdruckdampfmaschine wurde 1784 von Oliver Evans konstruiert. Das erste Exemplar wurde von ihm jedoch erst 1812 gebaut. Ihm zuvor kam Richard Trevithick, der 1801 die erste Hochdruckdampfmaschine in ein Straßenfahrzeug einbaute. Voraussetzung für die Funktionsfähigkeit der Hochdruckdampfmaschinen war der Fortschritt in der Metallherstellung und -bearbeitung zu dieser Zeit, denn in Hochdruckmaschinen müssen die Maschinenteile sehr passgenau sitzen. Außerdem bestand die Gefahr der Explosion des Kessels. ⓘ
Die kontinuierliche Weiterentwicklung der druckbetriebenen Dampfmaschine, die zuerst mit so genanntem Sattdampf arbeitete, führte über die Heißdampf-Maschine mit einfacher Dampfdehnung zur Verbund- oder Compound-Maschine mit Zwei- und Dreifachexpansion und zuletzt zur mehrzylindrigen Heißdampf-Hochdruck-Dampfmaschine, wie sie von Kemna angeboten wurde. Bei einer Sattdampfmaschine befinden sich im Kessel alle Siederohre für die Dampferzeugung im Wasserbett, ein Heißdampfkessel besitzt mit dem Überhitzer ein zweites Röhrensystem, das vom Feuer oder den heißen Rauchgasen bestrichen wird. Dadurch erreicht der Dampf Temperaturen um 350 Grad Celsius. Eine Compound- oder Verbundmaschine besitzt einen Hochdruckzylinder mit kleiner Bohrung und einen oder mehrere in Serie geschaltete Niederdruckzylinder. Der als Heißdampf in den Hochdruckzylinder eingespeiste, nunmehr teilentspannte und kühlere entweichende Dampf hat immer noch genug Arbeitsvermögen, um den mit einer wesentlich größeren Bohrung versehenen Niederdruckzylinder zu betreiben. Dabei wird versucht, die Zylinderbohrungen so abzustimmen, dass das erzeugte Drehmoment beider Zylinder auf die Kurbelwelle etwa gleich ist. Auch muss das Volumen beider Zylinder auf die Drehzahl der Dampfmaschine abgestimmt sein, damit die Entspannung des Dampfes auf beide Zylinder verteilt wird. Kemna baute ab 1908 Dampfmaschinen mit zwei Hochdruckzylindern. Bei ortsfesten und Schiffsmaschinen wurde Dreifachexpansion üblich. ⓘ
Hochdruckmaschinen erreichten im Jahre 1910 beispielsweise einen Steinkohlenverbrauch von 0,5 kg pro PS-Stunde mit „mittlerer Steinkohlenqualität“. Das entspricht einem Wirkungsgrad von über 18 %. ⓘ
Dampfmaschinen heute

Als Fahrzeugantrieb sind Dampfmaschinen weitgehend durch Verbrennungsmotoren abgelöst worden, die ohne Aufwärmzeit starten, einen höheren Wirkungsgrad haben, größere Leistung bei geringerem Gewicht bieten und komfortabler zu bedienen sind. Weiterhin hat die Dampfmaschine durch die flächendeckende Versorgung mit elektrischer Energie ihre Funktion als zentrale Energiequelle eines Industrieunternehmens verloren, die sie lange Zeit innehatte. Im Steinkohlenbergbau wurden und werden noch Dampfmaschinen in Förderanlagen eingesetzt, denn dort kann die Dampfmaschine sowohl als Fördermaschine zum Heben von Kohle als auch als Bremse zum Herablassen von Versatzmaterial dienen. Beim Bremsen wird die Energie zur Erhitzung des Dampfes verwendet. ⓘ
Obwohl die Zeit der Kolbendampfmaschine schon lange vorbei zu sein scheint, ist eine Renaissance nicht ausgeschlossen. Einer ihrer Vorteile gegenüber dem Verbrennungsmotor ist ihr kontinuierlicher Verbrennungsvorgang, der sich emissionsärmer gestalten lässt. Durch den heute üblichen geschlossenen Kreislauf von Dampf und Speisewasser ergibt sich eine emissionsarme Schmierung von Zylinder und Kolben der Maschine. In diesem Sinne ist als modernisierte Dampfmaschine der Dampfmotor entwickelt worden. Die Kolbendampfmaschine arbeitet (wie ein Elektromotor) drehzahlelastisch, somit können Direktantriebe konstruiert werden, wobei im Vergleich zum Verbrennungsmotor Rutschkupplungen entfallen und Getriebe vereinfacht werden. ⓘ
Im Auftrag der Volkswagen AG entwickelte die IAV GmbH in den späten 1990er Jahren eine solche moderne „Dampfmaschine“, die über eine extrem emissionsarme externe Verbrennung einen gewissen Vorrat an hochgespanntem Dampf erzeugt, der dann wie beim Dieselmotor über Düsen je nach Energiebedarf eingespritzt wird. Ende 2000 ging daraus die Firma Enginion hervor, die aus dem ZEE-Prototypen (Zero Emission Engine), der einen Wirkungsgrad von 23,7 % erreichte, die heutige SteamCell weiterentwickelte. Diese Maschine arbeitete im Zweitaktverfahren und kam außerdem ohne übliche Schmiermittel aus, weil die Verschleißteile aus modernen Kohlenstoffkomponenten gefertigt waren. Enginion musste jedoch 2005 Insolvenz anmelden. ⓘ