Spritzgießen




Das Spritzgießen (oft auch als Spritzguss oder Spritzgussverfahren bezeichnet) ist ein Urformverfahren, das hauptsächlich in der Kunststoffverarbeitung eingesetzt wird. Dabei wird mit einer Spritzgießmaschine der jeweilige Werkstoff verflüssigt (plastifiziert) und in eine Form, dem Spritzgießwerkzeug, unter Druck eingespritzt. Im Werkzeug geht der Werkstoff durch Abkühlung oder eine Vernetzungsreaktion wieder in den festen Zustand über und wird nach dem Öffnen des Werkzeuges als Fertigteil entnommen. Der Hohlraum, die Kavität, des Werkzeuges bestimmt dabei die Form und die Oberflächenstruktur des fertigen Teiles. Es sind heute Teile im Gewichtsbereich von wenigen zehntel Gramm bis zu einer Größenordnung von 150 kg herstellbar. ⓘ
Mit diesem Verfahren lassen sich direkt verwendbare Formteile in großer Stückzahl kostengünstig herstellen. Die Kosten für das Werkzeug machen einen großen Teil der notwendigen Investitionen aus. Dadurch ist selbst bei einfachen Werkzeugen die Schwelle der Wirtschaftlichkeit erst bei einigen tausend Teilen erreicht. Andererseits können die Werkzeuge für die Herstellung von bis zu einigen Millionen Teilen verwendet werden. ⓘ
Das Spritzgießen, insbesondere erweiterte spezielle Verfahren, erlaubt eine nahezu freie Wahl von Form und Oberflächenstruktur wie z. B. glatte Oberflächen, Narbungen für berührungsfreundliche Bereiche, Muster, Gravuren und Farbeffekte. Zusammen mit der Wirtschaftlichkeit macht dies das Spritzgießen zum meist verbreiteten Verfahren zur Massenherstellung von Kunststoffteilen in praktisch allen Bereichen. ⓘ
Die Formteile, die mit Spritzgießen hergestellt werden, lassen sich wie folgt kategorisieren: A-Teile – Präzisionsteile mit höchsten Anforderungen, B-Teile – technische Teile mit hohen Anforderungen und C-Teile – geometrisch einfache Formteile aus Standardkunststoffen mit geringen Anforderungen. Alle Kategorien besitzen unter anderem folgende wesentliche Qualitätsmerkmale: Formteilmaße und -gewicht, Festigkeit, Verzugserscheinungen und Oberflächenbeschaffenheit. ⓘ

Anwendungen
Im Spritzgussverfahren werden viele Dinge hergestellt, z. B. Drahtspulen, Verpackungen, Flaschenverschlüsse, Automobilteile und -komponenten, Spielzeug, Taschenkämme, einige Musikinstrumente (und Teile davon), einteilige Stühle und kleine Tische, Lagerbehälter, mechanische Teile (einschließlich Zahnräder) und die meisten anderen heute erhältlichen Kunststoffprodukte. Das Spritzgießen ist das gebräuchlichste moderne Verfahren zur Herstellung von Kunststoffteilen; es eignet sich ideal für die Produktion großer Mengen desselben Objekts. ⓘ
Merkmale des Verfahrens

Beim Spritzgießen wird geschmolzenes Kunststoff- oder Gummimaterial mit Hilfe eines Stempels oder eines Schneckenkolbens in einen Formhohlraum gepresst, wo es sich zu einer Form verfestigt, die der Kontur der Form entspricht. Am häufigsten werden sowohl thermoplastische als auch duroplastische Polymere verarbeitet, wobei das Volumen der ersteren wesentlich größer ist. Thermoplaste sind aufgrund ihrer Eigenschaften, die sie für das Spritzgießen besonders geeignet machen, weit verbreitet, z. B. weil sie sich leicht recyceln lassen, vielseitig einsetzbar sind und bei Erwärmung erweichen und fließen. Wenn ein duroplastisches Polymer nicht rechtzeitig aus dem Spritzgießzylinder ausgestoßen wird, kann es zu einer chemischen Vernetzung kommen, die zum Festfressen der Schnecke und der Rückschlagventile führt und möglicherweise die Spritzgießmaschine beschädigt. ⓘ
Beim Spritzgießen wird das Rohmaterial unter hohem Druck in eine Form gespritzt, die das Polymer in die gewünschte Form bringt. Die Formen können aus einem einzigen Hohlraum oder aus mehreren Hohlräumen bestehen. Bei Werkzeugen mit mehreren Kavitäten kann jede Kavität identisch sein und die gleichen Teile formen, oder sie können einzigartig sein und mehrere unterschiedliche Geometrien in einem einzigen Zyklus formen. Die Formen werden in der Regel aus Werkzeugstahl hergestellt, für bestimmte Anwendungen eignen sich jedoch auch rostfreie Stähle und Aluminiumformen. Aluminiumformen eignen sich in der Regel nicht für die Großserienproduktion oder für Teile mit engen Maßtoleranzen, da sie schlechtere mechanische Eigenschaften haben und anfälliger für Verschleiß, Beschädigung und Verformung während der Einspritz- und Schließzyklen sind; Aluminiumformen sind jedoch bei Anwendungen mit geringen Stückzahlen kosteneffizient, da die Kosten und der Zeitaufwand für die Herstellung der Form erheblich reduziert werden. Viele Stahlformen sind für die Verarbeitung von weit über einer Million Teilen während ihrer Lebensdauer ausgelegt und können in der Herstellung Hunderttausende von Dollar kosten. ⓘ
Bei der Formgebung von Thermoplasten wird in der Regel pelletiertes Rohmaterial durch einen Trichter in einen beheizten Zylinder mit einer sich hin- und herbewegenden Schnecke geleitet. Beim Eintritt in den Zylinder erhöht sich die Temperatur, und die Van-der-Waals-Kräfte, die dem relativen Fließen der einzelnen Ketten entgegenstehen, werden aufgrund des größeren Raums zwischen den Molekülen bei höheren thermischen Energiezuständen geschwächt. Durch diesen Vorgang wird die Viskosität verringert, so dass das Polymer mit der Antriebskraft der Spritzeinheit fließen kann. Die Schnecke fördert das Rohmaterial vorwärts, mischt und homogenisiert die thermische und viskose Verteilung des Polymers und verkürzt die erforderliche Heizzeit, indem sie das Material mechanisch schert und dem Polymer ein erhebliches Maß an Reibungswärme zuführt. Das Material fließt durch ein Rückschlagventil nach vorne und sammelt sich an der Vorderseite der Schnecke in einem Volumen, das als Schuss bezeichnet wird. Ein Schuss ist das Materialvolumen, das zum Füllen des Formhohlraums, zum Ausgleich der Schrumpfung und zur Bereitstellung eines Polsters (etwa 10 % des gesamten Schussvolumens, das im Zylinder verbleibt und verhindert, dass die Schnecke den Boden erreicht) verwendet wird, um den Druck von der Schnecke auf den Formhohlraum zu übertragen. Wenn sich genügend Material angesammelt hat, wird das Material mit hohem Druck und hoher Geschwindigkeit in den Formhohlraum gepresst. Das genaue Ausmaß der Schrumpfung hängt von dem verwendeten Kunststoff ab und kann relativ genau vorhergesagt werden. Um Druckspitzen zu vermeiden, wird normalerweise eine Übergabeposition verwendet, die einer zu 95-98 % gefüllten Kavität entspricht, in der die Schnecke von einer konstanten Geschwindigkeit zu einer konstanten Druckregelung übergeht. Die Einspritzzeiten liegen oft deutlich unter 1 Sekunde. Sobald die Schnecke die Übergabeposition erreicht hat, wird der Fülldruck angelegt, der die Formfüllung abschließt und die thermische Schrumpfung ausgleicht, die bei Thermoplasten im Vergleich zu vielen anderen Materialien recht hoch ist. Der Fülldruck wird so lange aufrechterhalten, bis der Anschnitt (Kavitäteneingang) erstarrt. Aufgrund seiner geringen Größe ist der Anschnitt normalerweise die erste Stelle, die in ihrer gesamten Dicke erstarrt. Sobald der Anguss erstarrt ist, kann kein Material mehr in die Kavität eindringen; dementsprechend bewegt sich die Schnecke hin und her und nimmt Material für den nächsten Zyklus auf, während das Material im Werkzeug abkühlt, damit es ausgeworfen werden kann und formstabil ist. Diese Abkühlzeit wird durch den Einsatz von Kühlleitungen, die Wasser oder Öl von einem externen Temperaturregler zirkulieren lassen, drastisch verkürzt. Sobald die erforderliche Temperatur erreicht ist, öffnet sich die Form und eine Reihe von Stiften, Hülsen, Abstreifern usw. wird nach vorne gefahren, um den Artikel zu entformen. Dann wird die Form geschlossen und der Vorgang wiederholt. ⓘ
Beim Zweischuss-Spritzgießen werden zwei verschiedene Materialien in einem Teil verarbeitet. Diese Art des Spritzgießens wird verwendet, um Knöpfen einen weichen Griff zu verleihen, einem Produkt mehrere Farben zu geben oder ein Teil mit mehreren Leistungsmerkmalen herzustellen. ⓘ
Bei Duroplasten werden in der Regel zwei verschiedene chemische Komponenten in den Zylinder eingespritzt. Diese Komponenten setzen sofort irreversible chemische Reaktionen in Gang, die das Material schließlich zu einem einzigen zusammenhängenden Netzwerk von Molekülen vernetzen. Während der chemischen Reaktion verwandeln sich die beiden flüssigen Komponenten dauerhaft in einen viskoelastischen Feststoff. Die Verfestigung im Einspritzzylinder und in der Schnecke kann problematisch sein und finanzielle Auswirkungen haben; daher ist es wichtig, die Aushärtung des Duroplasts im Zylinder zu minimieren. Dies bedeutet in der Regel, dass die Verweilzeit und die Temperatur der chemischen Grundstoffe in der Einspritzeinheit minimiert werden. Die Verweilzeit kann durch eine Minimierung des Fassvolumens und durch eine Maximierung der Zykluszeiten verringert werden. Diese Faktoren haben zur Verwendung einer thermisch isolierten, kalten Einspritzeinheit geführt, die die reagierenden Chemikalien in eine thermisch isolierte, heiße Form einspritzt, was die Geschwindigkeit der chemischen Reaktionen erhöht und zu einer kürzeren Zeitspanne führt, die benötigt wird, um ein verfestigtes duroplastisches Bauteil zu erhalten. Nachdem das Teil erstarrt ist, werden die Ventile geschlossen, um das Einspritzsystem und die chemischen Grundstoffe zu isolieren, und die Form öffnet sich, um die Formteile auszuwerfen. Dann schließt sich die Form und der Prozess wiederholt sich. ⓘ
Vorgeformte oder maschinell bearbeitete Bauteile können bei geöffnetem Werkzeug in den Hohlraum eingelegt werden, damit sich das im nächsten Zyklus eingespritzte Material um sie herum bilden und verfestigen kann. Dieses Verfahren wird als Insert Moulding bezeichnet und ermöglicht es, dass einzelne Teile mehrere Materialien enthalten. Dieses Verfahren wird häufig zur Herstellung von Kunststoffteilen mit hervorstehenden Metallschrauben verwendet, damit sie wiederholt befestigt und gelöst werden können. Diese Technik kann auch für In-Mould-Labelling verwendet werden, und es können auch Foliendeckel auf geformte Kunststoffbehälter aufgebracht werden. ⓘ
Das fertige Teil weist in der Regel eine Trennebene, einen Anguss, Anschnittmarkierungen und Auswerferstiftmarkierungen auf. Keines dieser Merkmale ist in der Regel erwünscht, lässt sich aber aufgrund der Art des Verfahrens nicht vermeiden. Anschnittmarken treten am Anschnitt auf, der die Schmelzezufuhrkanäle (Anguss und Angusskanal) mit dem Formhohlraum des Teils verbindet. Trennebenen- und Auswerferstiftmarkierungen resultieren aus winzigen Ausrichtungsfehlern, Verschleiß, Gasaustritten, Abständen für benachbarte Teile in Relativbewegung und/oder Maßunterschieden der Schmelzflächen, die das eingespritzte Polymer berühren. Maßabweichungen können auf ungleichmäßige, druckbedingte Verformungen während des Einspritzens, auf Bearbeitungstoleranzen und auf ungleichmäßige thermische Ausdehnung und Kontraktion von Formkomponenten zurückzuführen sein, die während der Einspritz-, Pack-, Abkühl- und Ausstoßphasen des Prozesses schnellen Zyklen ausgesetzt sind. Formteile werden oft aus Materialien mit unterschiedlichen Wärmeausdehnungskoeffizienten hergestellt. Diese Faktoren können nicht gleichzeitig berücksichtigt werden, ohne dass die Kosten für Konstruktion, Herstellung, Verarbeitung und Qualitätsüberwachung ins Unermessliche steigen. Der geschickte Formen- und Teilekonstrukteur platziert diese ästhetischen Beeinträchtigungen, wenn möglich, in versteckten Bereichen. ⓘ
Geschichte
Der amerikanische Erfinder John Wesley Hyatt patentierte 1872 zusammen mit seinem Bruder Isaiah die erste Spritzgießmaschine. Diese Maschine war im Vergleich zu den heute gebräuchlichen Maschinen relativ einfach: Sie funktionierte wie eine große Injektionsnadel, die mit Hilfe eines Kolbens Kunststoff durch einen erhitzten Zylinder in eine Form spritzt. Die Industrie entwickelte sich im Laufe der Jahre langsam weiter und stellte Produkte wie Kragenstäbchen, Knöpfe und Haarkämme her. ⓘ
Die deutschen Chemiker Arthur Eichengrün und Theodore Becker erfanden 1903 die ersten löslichen Formen von Celluloseacetat, das viel weniger brennbar war als Cellulosenitrat. Es wurde schließlich in Pulverform zur Verfügung gestellt, aus der es sich leicht im Spritzgussverfahren herstellen ließ. Arthur Eichengrün entwickelte 1919 die erste Spritzgießpresse. Im Jahr 1939 patentierte Arthur Eichengrün das Spritzgießen von weichgemachtem Celluloseacetat. ⓘ
In den 1940er Jahren expandierte die Branche rasch, da der Zweite Weltkrieg eine große Nachfrage nach preiswerten Massenprodukten schuf. 1946 baute der amerikanische Erfinder James Watson Hendry die erste Schneckenspritzgießmaschine, mit der sich die Geschwindigkeit der Einspritzung und die Qualität der hergestellten Artikel viel genauer steuern ließen. Diese Maschine ermöglichte es auch, das Material vor dem Einspritzen zu mischen, so dass gefärbter oder recycelter Kunststoff dem Neumaterial zugefügt und vor dem Einspritzen gründlich gemischt werden konnte. In den 1970er Jahren entwickelte Hendry das erste gasunterstützte Spritzgießverfahren, das die Herstellung komplexer, hohler Artikel ermöglichte, die schnell abkühlten. Dadurch wurden die Designflexibilität sowie die Festigkeit und die Oberflächenbeschaffenheit der hergestellten Teile erheblich verbessert und gleichzeitig Produktionszeit, Kosten, Gewicht und Abfall reduziert. Bis 1979 überholte die Kunststoffproduktion die Stahlproduktion, und bis 1990 wurden Aluminiumformen in großem Umfang im Spritzgussverfahren eingesetzt. Heute machen Schneckenspritzgießmaschinen die große Mehrheit aller Spritzgießmaschinen aus. ⓘ
Die Kunststoffspritzgussindustrie hat sich im Laufe der Jahre von der Herstellung von Kämmen und Knöpfen zu einer breiten Palette von Produkten für viele Branchen entwickelt, darunter die Automobil-, Medizin-, Luft- und Raumfahrt-, Konsumgüter-, Spielzeug-, Sanitär-, Verpackungs- und Bauindustrie. ⓘ
Beispiele für Polymere, die sich am besten für das Verfahren eignen
Die meisten Polymere, manchmal auch als Harze bezeichnet, können verwendet werden, darunter alle Thermoplaste, einige Duroplaste und einige Elastomere. Seit 1995 hat sich die Gesamtzahl der für das Spritzgießen verfügbaren Materialien um 750 pro Jahr erhöht; zu Beginn dieses Trends waren etwa 18.000 Materialien verfügbar. Zu den verfügbaren Werkstoffen gehören auch Legierungen oder Mischungen bereits entwickelter Werkstoffe, so dass die Produktentwickler aus einer großen Auswahl den Werkstoff mit den besten Eigenschaften auswählen können. Wichtige Kriterien für die Auswahl eines Werkstoffs sind die für das endgültige Teil erforderliche Festigkeit und Funktion sowie die Kosten, aber auch jedes Material hat unterschiedliche Parameter für das Gießen, die berücksichtigt werden müssen. Weitere Überlegungen bei der Auswahl eines Spritzgussmaterials betreffen den Biege-Elastizitätsmodul, d. h. das Ausmaß, in dem ein Material ohne Beschädigung gebogen werden kann, sowie die Wärmeformbeständigkeit und die Wasseraufnahme. Gängige Polymere wie Epoxid und Phenol sind Beispiele für duroplastische Kunststoffe, während Nylon, Polyethylen und Polystyrol zu den Thermoplasten gehören. Bis vor relativ kurzer Zeit waren Kunststofffedern nicht möglich, aber dank der Fortschritte bei den Polymereigenschaften sind sie jetzt recht praktisch. Zu den Anwendungen gehören Schnallen zum Verankern und Lösen von Gurtbändern für Outdoor-Ausrüstung. ⓘ
Ausrüstung

Spritzgießmaschinen bestehen aus einem Materialtrichter, einem Spritzkolben oder einem Schneckenkolben und einer Heizeinheit. Sie werden auch als Platten bezeichnet und halten die Formen, in denen die Bauteile geformt werden. Pressen werden nach ihrer Tonnage eingestuft, die die Schließkraft angibt, die die Maschine ausüben kann. Diese Kraft hält die Form während des Einspritzvorgangs geschlossen. Die Tonnage kann von weniger als 5 Tonnen bis zu mehr als 9.000 Tonnen variieren, wobei die höheren Werte nur bei vergleichsweise wenigen Fertigungsvorgängen verwendet werden. Die insgesamt benötigte Schließkraft wird durch die projizierte Fläche des zu formenden Teils bestimmt. Diese projizierte Fläche wird mit einer Schließkraft von 1,8 bis 7,2 Tonnen für jeden Quadratzentimeter der projizierten Fläche multipliziert. Als Faustregel können für die meisten Produkte 4 oder 5 Tonnen/in2 verwendet werden. Wenn das Kunststoffmaterial sehr steif ist, ist ein höherer Einspritzdruck erforderlich, um die Form zu füllen, und somit eine höhere Schließkraft, um die Form geschlossen zu halten. Die erforderliche Kraft kann auch durch das verwendete Material und die Größe des Teils bestimmt werden. Größere Teile erfordern eine höhere Schließkraft. ⓘ
Gussform
Form oder Matrize sind die gebräuchlichen Begriffe für das Werkzeug, das zur Herstellung von Kunststoffteilen beim Gießen verwendet wird. ⓘ
Da Formen in der Herstellung teuer waren, wurden sie in der Regel nur in der Massenproduktion eingesetzt, wo Tausende von Teilen hergestellt wurden. Typische Formen werden aus gehärtetem Stahl, vorgehärtetem Stahl, Aluminium und/oder Beryllium-Kupfer-Legierungen hergestellt. Die Wahl des Materials, aus dem eine Form gebaut wird, ist in erster Linie eine Frage der Wirtschaftlichkeit; im Allgemeinen sind Stahlformen teurer in der Herstellung, aber ihre längere Lebensdauer gleicht die höheren Anfangskosten über eine größere Anzahl von Teilen aus, die hergestellt werden, bevor sie verschleißen. Vorgehärtete Stahlformen sind weniger verschleißfest und werden für geringere Stückzahlen oder größere Bauteile verwendet; ihre typische Stahlhärte beträgt 38-45 auf der Rockwell-C-Skala. Gehärtete Stahlformen werden nach der Bearbeitung wärmebehandelt; sie sind in Bezug auf Verschleißfestigkeit und Lebensdauer bei weitem überlegen. Die typische Härte liegt zwischen 50 und 60 Rockwell-C (HRC). Aluminiumformen sind wesentlich preiswerter und können, wenn sie mit modernen computergesteuerten Anlagen entworfen und bearbeitet werden, für das Formen von zehn- oder sogar hunderttausenden von Teilen wirtschaftlich sein. Berylliumkupfer wird in Bereichen der Form verwendet, die eine schnelle Wärmeabfuhr erfordern, oder in Bereichen, in denen die meiste Scherwärme erzeugt wird. Die Formen können entweder durch CNC-Bearbeitung oder durch Funkenerosion hergestellt werden. ⓘ
- Spritzgießwerkzeug mit Seitenzügen
Der Einsatz wird aus der Form entfernt. ⓘ
Konstruktion der Form

Die Form besteht aus zwei Hauptkomponenten, der Spritzgussform (A-Platte) und der Auswerferform (B-Platte). Diese Komponenten werden auch als Gießer und Formenbauer bezeichnet. Das Kunststoffharz gelangt durch einen Anguss oder Anschnitt in der Spritzgussform in die Form; die Angussbuchse soll dicht gegen die Düse des Einspritzzylinders der Formmaschine abdichten und das Fließen des geschmolzenen Kunststoffs aus dem Zylinder in die Form, auch als Hohlraum bezeichnet, ermöglichen. Die Angussbuchse leitet den geschmolzenen Kunststoff durch Kanäle, die in die Stirnseiten der A- und B-Platten eingearbeitet sind, zu den Kavitätsbildern. An diesen Kanälen kann der Kunststoff entlanglaufen, weshalb sie auch als Angusskanäle bezeichnet werden. Der geschmolzene Kunststoff fließt durch den Angusskanal und tritt in einen oder mehrere spezielle Anschnitte und in die Kavitätsgeometrie ein, um das gewünschte Teil zu formen. ⓘ
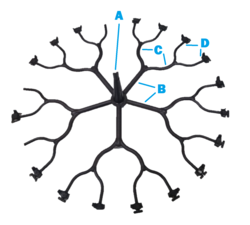
Die zum Füllen des Angusses, des Angusskanals und der Kavitäten eines Werkzeugs benötigte Harzmenge ist ein "Schuss". In der Form eingeschlossene Luft kann durch Entlüftungsöffnungen entweichen, die in die Trennebene der Form eingeschliffen sind, oder um Auswerferstifte und Schieber, die etwas kleiner sind als die Löcher, in denen sie gehalten werden. Wenn die eingeschlossene Luft nicht entweichen kann, wird sie durch den Druck des einströmenden Materials komprimiert und in die Ecken des Hohlraums gepresst, wo sie die Füllung verhindert und auch andere Fehler verursachen kann. Die Luft kann sogar so stark komprimiert werden, dass sie sich entzündet und das umgebende Kunststoffmaterial verbrennt. ⓘ
Damit das Formteil aus der Form entnommen werden kann, dürfen die Formteile in der Richtung, in der sich die Form öffnet, nicht überhängen, es sei denn, Teile der Form sind so konstruiert, dass sie sich beim Öffnen der Form mit Hilfe von Bauteilen, den so genannten Liftern, zwischen solchen Überhängen bewegen. ⓘ
Die Seiten des Teils, die parallel zur Ziehrichtung verlaufen (die Achse der Kernposition (Loch) oder des Einsatzes verläuft parallel zur Auf- und Abwärtsbewegung der Form beim Öffnen und Schließen), werden in der Regel leicht angewinkelt, was als Verzug bezeichnet wird, um die Entnahme des Teils aus der Form zu erleichtern. Ein unzureichender Verzug kann zu Verformungen oder Beschädigungen führen. Der für die Entformung erforderliche Verzug hängt in erster Linie von der Tiefe der Kavität ab; je tiefer die Kavität, desto mehr Verzug ist erforderlich. Auch die Schrumpfung muss bei der Bestimmung des erforderlichen Verzugs berücksichtigt werden. Wenn die Haut zu dünn ist, neigt das Formteil dazu, auf die Kerne zu schrumpfen, die sich beim Abkühlen bilden, und an diesen Kernen zu haften, oder das Teil kann sich verziehen, verdrehen, Blasen werfen oder reißen, wenn die Kavität weggezogen wird. ⓘ
Eine Form ist in der Regel so konstruiert, dass das Formteil beim Öffnen der Form zuverlässig auf der Auswerferseite (B) verbleibt und der Anguss zusammen mit den Teilen aus der Seite (A) herausgezogen wird. Das Teil fällt dann beim Auswerfen aus der (B)-Seite frei herunter. Tunnelangüsse, auch Unterwasser- oder Formangüsse genannt, befinden sich unterhalb der Trennebene oder der Formoberfläche. An der Trennebene wird eine Öffnung in die Oberfläche der Form gefräst. Das Formteil wird (von der Form) beim Auswerfen aus der Form vom Angusssystem abgeschnitten. Auswerferstifte, auch Ausstoßstifte genannt, sind kreisförmige Stifte, die in einer der beiden Formhälften (in der Regel in der Auswerferhälfte) platziert werden und das fertige Formteil oder das Angusssystem aus der Form drücken.Das Ausstoßen des Artikels mit Hilfe von Stiften, Hülsen, Abstreifern usw. kann zu unerwünschten Abdrücken oder Verformungen führen, weshalb bei der Konstruktion der Form Vorsicht geboten ist. ⓘ
Die Standardmethode zur Kühlung besteht darin, ein Kühlmittel (in der Regel Wasser) durch eine Reihe von Löchern zu leiten, die durch die Formplatten gebohrt wurden und durch Schläuche miteinander verbunden sind, um einen kontinuierlichen Weg zu bilden. Das Kühlmittel nimmt die Wärme aus der Form auf (die wiederum die Wärme aus dem heißen Kunststoff aufgenommen hat) und hält die Form auf einer angemessenen Temperatur, damit der Kunststoff möglichst schnell erstarrt. ⓘ
Um die Wartung und Entlüftung zu erleichtern, werden Hohlräume und Kerne in Teile, so genannte Einsätze, und Unterbaugruppen, auch Einsätze, Blöcke oder Chase-Blöcke genannt, unterteilt. Durch den Austausch von austauschbaren Einsätzen können mit einer Form mehrere Varianten desselben Teils hergestellt werden. ⓘ
Komplexere Teile werden mit komplexeren Formen geformt. Diese können Abschnitte, so genannte Schieber, aufweisen, die sich in einen Hohlraum senkrecht zur Ziehrichtung bewegen, um überhängende Teilemerkmale zu bilden. Beim Öffnen der Form werden die Schieber mit Hilfe von feststehenden "Winkelstiften" an der feststehenden Formhälfte vom Kunststoffteil weggezogen. Diese Stifte dringen in einen Schlitz in den Schiebern ein und bewirken, dass sich die Schieber nach hinten bewegen, wenn sich die bewegliche Formhälfte öffnet. Das Teil wird dann ausgeworfen und die Form schließt sich. Der Schließvorgang der Form bewirkt, dass sich die Schieber entlang der Winkelstifte vorwärts bewegen. ⓘ
Eine Form kann mehrere Kopien der gleichen Teile in einem einzigen "Schuss" herstellen. Die Anzahl der "Abdrücke" in der Form dieses Teils wird oft fälschlicherweise als Kavitation bezeichnet. Ein Werkzeug mit einem Abdruck wird oft als Form mit einem Abdruck (Kavität) bezeichnet. Ein Werkzeug mit zwei oder mehr Kavitäten für die gleichen Teile wird in der Regel als Werkzeug mit mehreren Abdrücken (Kavitäten) bezeichnet. Einige Werkzeuge für extrem hohe Produktionsmengen (z. B. für Flaschenverschlüsse) können über 128 Kavitäten haben. ⓘ
In einigen Fällen werden mit Mehrfachwerkzeugen eine Reihe verschiedener Teile in ein und demselben Werkzeug geformt. Einige Werkzeugmacher bezeichnen diese Formen als Familienformen, da alle Teile miteinander verbunden sind, z. B. bei Kunststoffmodellbausätzen. ⓘ
Bei einigen Formen können zuvor geformte Teile wieder eingelegt werden, damit sich eine neue Kunststoffschicht um das erste Teil herum bilden kann. Dies wird oft als Überspritzen bezeichnet. Dieses System kann die Produktion von einteiligen Reifen und Rädern ermöglichen. ⓘ
Multi-Shot-Spritzguss
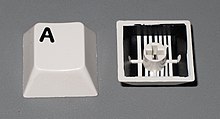
Two-Shot- oder Multi-Shot-Formen sind so konzipiert, dass sie in einem einzigen Zyklus "überspritzt" werden können, und müssen auf speziellen Spritzgießmaschinen mit zwei oder mehr Spritzeinheiten verarbeitet werden. Bei diesem Verfahren handelt es sich eigentlich um einen zweimaligen Spritzgießvorgang, der daher eine viel geringere Fehlerspanne aufweist. Im ersten Schritt wird das Material in der Grundfarbe zu einer Grundform geformt, die Platz für den zweiten Schuss bietet. Dann wird das zweite Material, eine andere Farbe, in diese Zwischenräume gespritzt. Mit diesem Verfahren hergestellte Drucktasten und Tasten haben beispielsweise Markierungen, die sich nicht abnutzen und auch bei starker Beanspruchung lesbar bleiben. ⓘ
Lagerung von Gussformen
Aufgrund ihrer hohen Durchschnittskosten unternehmen die Hersteller große Anstrengungen, um ihre Formen zu schützen. Die perfekte Temperatur und Luftfeuchtigkeit wird aufrechterhalten, um eine möglichst lange Lebensdauer der Gussformen zu gewährleisten. Kundenspezifische Formen, wie z. B. für den Gummispritzguss, werden in temperatur- und feuchtigkeitskontrollierten Umgebungen gelagert, um Verformungen zu vermeiden. ⓘ
Werkstoffe
Häufig wird Werkzeugstahl verwendet. Weichstahl, Aluminium, Nickel oder Epoxid eignen sich nur für Prototypen oder sehr kleine Produktionsserien. Mit modernen Hartaluminiumlegierungen (7075 und 2024) lassen sich bei ordnungsgemäßer Werkzeugkonstruktion problemlos Formen herstellen, die bei entsprechender Wartung eine Lebensdauer von 100.000 oder mehr Teilen erreichen. ⓘ

Bearbeitung
Für die Herstellung von Gussformen gibt es zwei Hauptmethoden: Standardbearbeitung und EDM. Die Standardbearbeitung in ihrer konventionellen Form ist seit jeher die Methode für den Bau von Spritzgussformen. Mit der technologischen Entwicklung wurde die CNC-Bearbeitung zum vorherrschenden Mittel, um komplexere Formen mit genaueren Formdetails in kürzerer Zeit als mit den traditionellen Methoden herzustellen. ⓘ
Das Elektroerosionsverfahren (EDM) oder Funkenerosionsverfahren ist im Formenbau inzwischen weit verbreitet. Das Verfahren ermöglicht nicht nur die Herstellung von schwer zu bearbeitenden Formen, sondern auch die Formgebung von vorgehärteten Gussformen, so dass keine Wärmebehandlung erforderlich ist. Änderungen an einer gehärteten Form durch herkömmliches Bohren und Fräsen erfordern normalerweise ein Glühen, um die Form zu erweichen, gefolgt von einer Wärmebehandlung, um sie wieder zu härten. Die Funkenerosion ist ein einfaches Verfahren, bei dem eine geformte Elektrode, in der Regel aus Kupfer oder Graphit, über einen Zeitraum von mehreren Stunden sehr langsam auf die Oberfläche der Form gesenkt wird, die in Paraffinöl (Kerosin) getaucht ist. Eine zwischen Werkzeug und Form angelegte Spannung bewirkt eine Funkenerosion der Formoberfläche in der umgekehrten Form der Elektrode. ⓘ
Kosten
Die Anzahl der in eine Form eingebauten Kavitäten steht in direktem Zusammenhang mit den Formkosten. Weniger Kavitäten erfordern einen weitaus geringeren Werkzeugaufwand, so dass eine Begrenzung der Kavitätenzahl die anfänglichen Herstellungskosten für den Bau einer Spritzgussform senkt. ⓘ
So wie die Anzahl der Kavitäten eine wichtige Rolle bei den Gusskosten spielt, so spielt auch die Komplexität der Konstruktion des Teils eine Rolle. Die Komplexität kann sich in vielen Faktoren niederschlagen, z. B. in der Oberflächenbearbeitung, den Toleranzanforderungen, den Innen- oder Außengewinden, den feinen Details oder der Anzahl der Hinterschneidungen, die eingebaut werden können. ⓘ
Weitere Details, wie z. B. Hinterschneidungen, oder jedes Merkmal, das zusätzliche Werkzeuge erfordert, erhöhen die Werkzeugkosten. Auch die Oberflächenbeschaffenheit des Kerns und der Kavität der Gussformen beeinflusst die Kosten. ⓘ
Das Gummispritzgussverfahren liefert eine hohe Ausbeute an langlebigen Produkten und ist damit die effizienteste und kostengünstigste Methode des Spritzgießens. Konstante Vulkanisierungsprozesse mit präziser Temperaturkontrolle reduzieren den Materialabfall erheblich. ⓘ
Einspritzverfahren

Normalerweise werden die Kunststoffe in Form von Pellets oder Granulat geformt und von den Rohstoffherstellern in Papiersäcken verschickt. Beim Spritzgießen wird vorgetrocknetes Kunststoffgranulat durch einen Presskolben aus einem Trichter in einen beheizten Zylinder befördert. Während das Granulat von einem Schneckenkolben langsam vorwärts bewegt wird, wird der Kunststoff in eine beheizte Kammer gepresst, wo er geschmolzen wird. Während sich der Kolben vorwärts bewegt, wird der geschmolzene Kunststoff durch eine Düse gepresst, die an der Form anliegt, so dass er durch ein Anschnitt- und Angusssystem in den Formhohlraum gelangt. Die Form bleibt kalt, so dass der Kunststoff fast sofort nach dem Füllen der Form erstarrt. ⓘ
Zyklus des Spritzgießens
Die Abfolge der Ereignisse beim Spritzgießen eines Kunststoffteils wird als Spritzgießzyklus bezeichnet. Der Zyklus beginnt mit dem Schließen der Form, gefolgt vom Einspritzen des Polymers in den Formhohlraum. Sobald der Hohlraum gefüllt ist, wird ein Nachdruck aufrechterhalten, um die Materialschrumpfung auszugleichen. Im nächsten Schritt dreht sich die Schnecke und führt den nächsten Schuss der vorderen Schnecke zu. Dadurch wird die Schnecke zurückgezogen, während der nächste Schuss vorbereitet wird. Sobald das Teil ausreichend abgekühlt ist, öffnet sich die Form und das Teil wird ausgestoßen. ⓘ
Wissenschaftliches versus traditionelles Spritzgießen
Traditionell wurde der Einspritzteil des Gießverfahrens mit einem konstanten Druck durchgeführt, um die Kavität zu füllen und zu verdichten. Diese Methode ermöglichte jedoch eine große Variation der Abmessungen von Zyklus zu Zyklus. Heute wird häufiger das wissenschaftliche oder entkoppelte Spritzgießen verwendet, eine Methode, die von RJG Inc. entwickelt wurde. Bei diesem Verfahren wird das Einspritzen des Kunststoffs in mehreren Stufen "entkoppelt", um eine bessere Kontrolle der Teileabmessungen und eine größere Zyklus-zu-Zyklus-Konsistenz (in der Branche üblicherweise Schuss-zu-Schuss genannt) zu ermöglichen. Zunächst wird die Kavität mit Hilfe der Geschwindigkeitsregelung zu etwa 98 % gefüllt. Obwohl der Druck ausreichen sollte, um die gewünschte Geschwindigkeit zu erreichen, sind Druckbegrenzungen in dieser Phase unerwünscht. Sobald die Kavität zu 98 % gefüllt ist, schaltet die Maschine von der Geschwindigkeitssteuerung auf die Drucksteuerung um, bei der die Kavität bei konstantem Druck "ausgepackt" wird, wobei eine ausreichende Geschwindigkeit zum Erreichen der gewünschten Drücke erforderlich ist. Auf diese Weise können die Werker die Abmessungen der Teile bis auf Tausendstel Zoll oder besser kontrollieren. ⓘ
Verschiedene Arten von Spritzgießverfahren
Obwohl die meisten Spritzgießverfahren durch die oben beschriebene konventionelle Verfahrensweise abgedeckt sind, gibt es einige wichtige Varianten des Spritzgießens, darunter, aber nicht ausschließlich
- Druckguss
- Metall-Spritzgießen
- Dünnwandspritzgießen
- Spritzgießen von flüssigem Silikonkautschuk
- Reaktionsspritzgießen
- Mikro-Spritzgießen
- Gasunterstütztes Spritzgießen
- Würfelformtechnik ⓘ
Eine umfassendere Liste von Spritzgießverfahren finden Sie hier: [1] ⓘ
Prozess-Fehlerbehebung
Wie bei allen industriellen Verfahren können auch beim Spritzgießen fehlerhafte Teile entstehen, selbst bei Spielzeug. Im Bereich des Spritzgießens erfolgt die Fehlersuche häufig durch die Untersuchung fehlerhafter Teile auf bestimmte Mängel und die Behebung dieser Mängel durch die Konstruktion der Form oder die Merkmale des Verfahrens selbst. Versuche werden oft vor der eigentlichen Produktion durchgeführt, um Fehler vorherzusagen und die geeigneten Spezifikationen für den Spritzgussprozess zu bestimmen. ⓘ
Wenn eine neue oder unbekannte Form zum ersten Mal gefüllt wird und die Schussgröße für diese Form nicht bekannt ist, kann ein Techniker/Werkzeugeinrichter einen Probelauf vor einem vollen Produktionslauf durchführen. Er beginnt mit einem geringen Schussgewicht und füllt die Form schrittweise, bis sie zu 95 bis 99 % gefüllt ist. Sobald dies erreicht ist, wird ein geringer Nachdruck ausgeübt und die Nachdruckzeit erhöht, bis der Anschnitt abgekühlt ist (Erstarrungszeit). Die Zeit für das Einfrieren des Angusses kann durch Erhöhung der Nachdruckzeit und anschließendes Wiegen des Teils bestimmt werden. Wenn sich das Gewicht des Teils nicht ändert, ist der Anschnitt eingefroren und es wird kein weiteres Material in das Teil gespritzt. Die Erstarrungszeit des Anschnitts ist wichtig, da sie die Zykluszeit sowie die Qualität und Konsistenz des Produkts bestimmt, was wiederum ein wichtiger Faktor für die Wirtschaftlichkeit des Produktionsprozesses ist. Der Nachdruck wird erhöht, bis die Teile frei von Einfallstellen sind und das Teilegewicht erreicht ist. ⓘ
Fehler in der Formgebung
Das Spritzgießen ist eine komplexe Technologie mit möglichen Produktionsproblemen. Sie können entweder durch Defekte in den Formen oder häufiger durch den Gießprozess selbst verursacht werden. ⓘ
Fehler in der Formgebung | Alternative Bezeichnung | Beschreibungen | Ursachen ⓘ |
---|---|---|---|
Blasenbildung | Blasenbildung | Erhöhte oder geschichtete Zone auf der Oberfläche des Teils | Das Werkzeug oder das Material ist zu heiß, oft verursacht durch mangelnde Kühlung um das Werkzeug herum oder eine defekte Heizung. |
Brandflecken | Luftverbrennungen/Gasverbrennungen/Diesel-/Gasmarken/Blasenmarken | Schwarze oder braune verbrannte Stellen auf dem Teil, die sich am weitesten vom Anschnitt entfernt befinden oder wo Luft eingeschlossen ist | Das Werkzeug hat keine Entlüftung, die Einspritzgeschwindigkeit ist zu hoch. |
Farbschlieren | Örtliche Farbveränderung | Masterbatch wird nicht richtig gemischt, oder das Material ist ausgegangen und kommt nur noch als Naturfarbe durch. Vorher gefärbtes Material "schleift" in der Düse oder im Rückschlagventil. | |
Verunreinigung | Unerwünschtes oder fremdes Material | Andersfarbige Stoffe im Produkt, die das Produkt schwächen | Schlechtes Material, das durch eine schlechte Recycling- oder Mahlgutpolitik eingebracht wurde; kann Bodenfeger, Staub und Schutt enthalten. |
Verunreinigungen | Dünne glimmerähnliche Schichten, die sich in der Wand eines Teils bilden | Verunreinigung des Materials, z. B. PP gemischt mit ABS, sehr gefährlich, wenn das Teil für eine sicherheitskritische Anwendung verwendet wird, da das Material bei einer Delaminierung nur eine sehr geringe Festigkeit aufweist, da sich die Materialien nicht verbinden können. | |
Flash | Überschüssiges Material in einer dünnen Schicht, die über die normale Teilegeometrie hinausgeht | Die Form ist überfüllt oder die Trennebene des Werkzeugs ist beschädigt, zu hohe Einspritzgeschwindigkeit/eingespritztes Material, zu geringe Schließkraft. Kann auch durch Schmutz und Verunreinigungen an den Werkzeugoberflächen verursacht werden. | |
Eingebettete Verunreinigungen | Eingebettete Partikel | In das Teil eingebettete Fremdpartikel (verbranntes Material oder anderes) | Partikel auf der Werkzeugoberfläche, verunreinigtes Material oder Fremdkörper im Zylinder oder zu starke Scherhitze, die das Material vor dem Einspritzen verbrennt. |
Fließspuren | Fließlinien | Wellenförmige Linien oder Muster, die in die falsche Richtung verlaufen | Zu langsame Einspritzgeschwindigkeiten (der Kunststoff hat sich während des Einspritzens zu stark abgekühlt; die Einspritzgeschwindigkeiten sollten so schnell eingestellt werden, wie es für den Prozess und das verwendete Material angemessen ist). |
Anschnitt-Rötung | Halo oder Blush Marks | Kreisförmiges Muster um den Anschnitt, normalerweise nur bei Heißkanalwerkzeugen ein Problem | Die Einspritzgeschwindigkeit ist zu schnell, die Größe des Angusses/des Angusses/des Angusskanals ist zu klein oder die Temperatur der Schmelze/des Werkzeugs ist zu niedrig. |
Strahlen | Jetting ist ein schlangenförmiger Strom, der entsteht, wenn die Polymerschmelze mit hoher Geschwindigkeit durch restriktive Bereiche gedrückt wird. | Schlechte Werkzeugkonstruktion, Anschnittposition oder Angusskanal. Die Einspritzgeschwindigkeit ist zu hoch eingestellt. Schlechtes Design der Anschnitte, was zu einem zu geringen Aufquellen der Form und damit zu Spritzern führt. | |
Gestrickte Linien | Schweißnähte | Kleine Linien auf der Rückseite von Kernstiften oder Fenstern in Teilen, die wie einfache Linien aussehen. | Verursacht durch die Schmelzefront, die um ein überstehendes Objekt in einem Kunststoffteil herumfließt, sowie am Ende der Füllung, wo die Schmelzefront wieder zusammenkommt. Dies kann durch eine Fließstudie in der Entwurfsphase des Werkzeugs minimiert oder beseitigt werden. Ist die Form erst einmal hergestellt und der Anschnitt platziert, kann dieser Fehler nur noch durch Änderung der Schmelze und der Formtemperatur minimiert werden. |
Polymerabbau | Polymerabbau durch Hydrolyse, Oxidation usw. | Überschüssiges Wasser im Granulat, zu hohe Temperaturen im Zylinder, zu hohe Schneckendrehzahlen, die eine hohe Scherhitze verursachen, zu lange Verweildauer des Materials im Zylinder, Verwendung von zu viel Regenerat. | |
Einfallstellen | Einfallstellen | Örtliche Vertiefungen (in dickeren Zonen) | Haltezeit/Druck zu niedrig, Kühlzeit zu kurz, bei angusslosen Heißkanälen kann dies auch durch eine zu hoch eingestellte Anschnitttemperatur verursacht werden. Überschüssiges Material oder zu dicke Wände. |
Kurzer Schuss | Kurze Füllung oder kurze Form | Unvollständiges Teil | Materialmangel, zu niedrige Einspritzgeschwindigkeit oder Druck, zu kaltes Werkzeug, fehlende Entgasungsöffnungen. |
Spreizmarken | Spritzmarken oder Silberschlieren | Erscheint in der Regel als silberne Schlieren entlang des Fließbildes, kann aber je nach Art und Farbe des Materials auch als kleine Blasen erscheinen, die durch eingeschlossene Feuchtigkeit verursacht werden. | Feuchtigkeit im Material, normalerweise wenn hygroskopische Harze unsachgemäß getrocknet werden. Gaseinschlüsse in "Rippen"-Bereichen aufgrund einer zu hohen Einspritzgeschwindigkeit in diesen Bereichen. Das Material ist zu heiß, oder es wird zu stark geschert. |
Fadenziehen | Fadenbildung oder langer Anschnitt | Fadenartige Überreste vom vorherigen Schuss werden in den neuen Schuss übertragen. | Die Düsentemperatur ist zu hoch. Anschnitt ist nicht abgefroren, keine Dekompression der Schnecke, kein Angussbruch, schlechte Platzierung der Heizbänder im Werkzeug. |
Hohlräume | Leerer Raum im Teil (üblicherweise wird eine Lufttasche verwendet) | Mangelnder Nachdruck (Nachdruck wird verwendet, um das Teil während der Nachdruckzeit zu verdichten). Zu schnelles Füllen, so dass sich die Kanten des Teils nicht absetzen können. Auch kann die Form nicht richtig ausgerichtet sein (wenn die beiden Hälften nicht richtig zentriert sind und die Wände des Teils nicht die gleiche Dicke haben). Die hier gegebenen Informationen entsprechen dem allgemeinen Verständnis, Berichtigung: Fehlender Packungsdruck (nicht Nachdruck) (der Packungsdruck wird zum Auspacken verwendet, obwohl das Teil während der Nachdruckzeit steht). Ein zu schnelles Füllen verursacht diesen Zustand nicht, da ein Hohlraum eine Senkung ist, die nicht stattfinden konnte. Mit anderen Worten, während das Teil schrumpft, trennt sich das Harz von sich selbst, da nicht genügend Harz in der Kavität vorhanden ist. Der Hohlraum kann an jeder beliebigen Stelle entstehen, oder das Teil ist nicht durch die Dicke, sondern durch den Harzfluss und die Wärmeleitfähigkeit begrenzt, aber es ist wahrscheinlicher, dass er an dickeren Stellen wie Rippen oder Vorsprüngen entsteht. Weitere Ursachen für Hohlräume sind nicht aufgeschmolzene Stellen im Schmelzbad. | |
Schweißnaht | Stricklinie / Schweißlinie / Transferlinie | Verfärbte Linie, wo sich zwei Fließfronten treffen | Zu niedrig eingestellte Werkzeug- oder Materialtemperaturen (das Material ist kalt, wenn sie aufeinandertreffen, und verbindet sich daher nicht). Die Zeit für den Übergang zwischen Einspritzung und Transfer (zum Verpacken und Halten) ist zu früh. |
Verzug | Verdrehen | Verformtes Teil | Zu kurze Kühlzeit, zu heißes Material, fehlende Kühlung um das Werkzeug herum, falsche Wassertemperaturen (die Teile wölben sich nach innen zur heißen Seite des Werkzeugs hin) Ungleichmäßige Schrumpfung zwischen den Bereichen des Teils. |
Risse | Rissbildung | Unsachgemäße Verschmelzung zweier Flüssigkeitsströme, ein Zustand vor der Schweißnaht. | Spalt zwischen den Teilen aufgrund falscher Anschnittposition bei Teilen mit komplexem Design, einschließlich eines Überschusses an Löchern (Mehrpunktanschnitte sind vorzusehen), Prozessoptimierung, ordnungsgemäße Entlüftung. |
Methoden wie industrielles CT-Scannen können bei der Suche nach diesen Defekten sowohl von außen als auch von innen helfen. ⓘ
Toleranzen
Die Toleranzen hängen von den Abmessungen des Teils ab. Ein Beispiel für eine Standardtoleranz für eine 1-Zoll-Abmessung eines LDPE-Teils mit 0,125 Zoll Wandstärke ist +/- 0,008 Zoll (0,2 mm). ⓘ
Leistungsanforderungen
Die für dieses Spritzgießverfahren erforderliche Leistung hängt von vielen Faktoren ab und variiert je nach verwendetem Material. Im Manufacturing Processes Reference Guide heißt es, dass der Energiebedarf von "dem spezifischen Gewicht, dem Schmelzpunkt, der Wärmeleitfähigkeit, der Teilegröße und der Formgebungsgeschwindigkeit eines Materials" abhängt. Nachfolgend finden Sie eine Tabelle von Seite 243 desselben Handbuchs, die die für den Leistungsbedarf der am häufigsten verwendeten Materialien relevanten Merkmale am besten veranschaulicht. ⓘ
Werkstoff | Spezifisches Gewicht | Schmelzpunkt (°F) | Schmelzpunkt (°C) ⓘ |
---|---|---|---|
Epoxidharz | 1,12 bis 1,24 | 248 | 120 |
Phenolharz | 1,34 bis 1,95 | 248 | 120 |
Nylon | 1,01 bis 1,15 | 381 bis 509 | 194 bis 265 |
Polyethylen | 0,91 bis 0,965 | 230 bis 243 | 110 bis 117 |
Polystyrol | 1,04 bis 1,07 | 338 | 170 |
Robotergestützte Formgebung
Automatisierung bedeutet, dass die geringere Größe der Teile es einem mobilen Prüfsystem ermöglicht, mehrere Teile schneller zu prüfen. Neben der Montage von Inspektionssystemen auf automatischen Vorrichtungen können mehrachsige Roboter Teile aus der Form entnehmen und für weitere Prozesse positionieren. ⓘ
Konkrete Fälle sind die Entnahme von Teilen aus der Form unmittelbar nach der Herstellung der Teile sowie die Anwendung von Bildverarbeitungssystemen. Ein Roboter greift das Teil, nachdem die Auswerferstifte ausgefahren wurden, um das Teil aus der Form zu befreien. Anschließend werden die Teile entweder in eine Haltevorrichtung oder direkt in ein Prüfsystem befördert. Die Wahl hängt von der Art des Produkts sowie von der allgemeinen Auslegung der Fertigungsanlagen ab. Auf Robotern montierte Bildverarbeitungssysteme haben die Qualitätskontrolle von Spritzgussteilen erheblich verbessert. Ein mobiler Roboter kann die Platzierungsgenauigkeit des Metallteils genauer bestimmen und schneller prüfen als ein Mensch. ⓘ
Galerie
Lego-Spritzgießform, Detail der Oberseite ⓘ
Unterteilung der Spritzgießverfahren
Beim Spritzgießen werden fast ausschließlich Kunststoffe verarbeitet. Diese lassen sich in Thermoplaste, Duroplaste und Elastomere unterteilen. Alle drei Materialarten können im Spritzgussverfahren verwendet werden, wobei das Thermoplast-Spritzgießen die größte wirtschaftliche Bedeutung hat. Es ist das am häufigsten verwendete Kunststoffverarbeitungsverfahren überhaupt. ⓘ
Deswegen soll im Folgenden das Verfahren zunächst für Thermoplaste erklärt werden. Das Spritzgießen von Duroplasten und Elastomeren funktioniert prinzipiell gleich und unterscheidet sich in erster Linie nur in den Betriebsparametern (z. B. Temperaturen). ⓘ
Die unten beschriebenen speziellen Verfahren stellen Erweiterungen bzw. Modifikationen des Grundprozesses für bestimmte Anwendungen dar. ⓘ
Thermoplast-Spritzgießen
Grundsätzlicher Aufbau einer Spritzgießmaschine
Die heute übliche Schneckenkolbenspritzgießmaschine besteht aus zwei Einheiten: der Spritzeinheit oder auch Plastifiziereinheit, welche den Kunststoff plastifiziert, aufbereitet und dosiert, und der Schließeinheit, die das Formwerkzeug schließt, zuhält und wieder öffnet. ⓘ
Die Spritzeinheit setzt sich im Wesentlichen aus einem waagerechten Zylinder, dem Plastifizierzylinder und einer darin befindlichen Schnecke zusammen. Die Schnecke rotiert und ist auch axial im Zylinder beweglich. An einem Ende des Plastifizierzylinders befindet sich der Einfülltrichter zum Beschicken mit dem Rohmaterial, am anderen befindet sich die Düse, welche entweder verschließbar oder nicht verschließbar sein kann, sie stellt den Übergang zur Schließeinheit dar. ⓘ
Die Schließeinheit besteht aus dem Formwerkzeug selbst, das in zwei Hälften trennbar ist (Formtrennebene). Die Hälften sind auf zwei Aufspannplatten montiert, von denen die eine, die Düsenseite, starr und der Düse der Spritzeinheit zugewandt ist. Die andere, die Auswerferseite, ist beweglich. Sie kann hydraulisch oder elektromechanisch (Kniehebelmechanismus) von der Düsenseite wegbewegt oder mit Kraft auf sie gepresst werden. Sie enthält den namensgebenden Mechanismus, welcher das Spritzgussteil entformt (auswirft). ⓘ
Spritz- und Schließeinheit müssen entsprechend dem Werkstoff, Bauteil und Prozess temperiert werden (die Spritzgussform ist ggf. temperaturgeführt). Da die beiden Einheiten unterschiedliche Temperaturen aufweisen, können sie, außer bei Heißkanalsystemen, zur thermischen Trennung voneinander wegbewegt werden. ⓘ
Bis 1956 verwendete man Kolbenspritzgießmaschinen. ⓘ
Verfahrensablauf

Plastifizieren und Dosieren
Der thermoplastische Kunststoff rieselt in Form eines Granulats in die Gänge der rotierenden Schnecke ein. Das Granulat wird Richtung Schneckenspitze gefördert und durch die Wärme des Zylinders und die Friktionswärme, die beim Zerteilen und Scheren des Materials entsteht, erwärmt und aufgeschmolzen. Die Schmelze sammelt sich vor der Schneckenspitze, da die Düse zu diesem Zeitpunkt geschlossen ist. Da die Schnecke axial beweglich ist, weicht sie durch den Druck zurück, auch schraubt sie sich ähnlich einem Korkenzieher aus der Masse heraus. Die Rückwärtsbewegung wird durch einen Hydraulikzylinder oder elektrisch gebremst, so dass sich in der Schmelze ein Staudruck aufbaut. Dieser Staudruck in Verbindung mit der Schneckenrotation verdichtet und homogenisiert das Material. ⓘ
Die Schneckenposition wird gemessen und sobald sich eine für das Werkstückvolumen ausreichende Materialmenge angesammelt hat, ist der Dosiervorgang beendet und die Schneckenrotation wird eingestellt. Ebenso wird die Schnecke aktiv oder passiv entlastet, so dass die Schmelze dekomprimiert wird. ⓘ
Einspritzen
In der Einspritzphase wird die Spritzeinheit an die Schließeinheit gefahren, mit der Düse angedrückt und die Schnecke rückseitig unter Druck gesetzt. Dabei wird die Schmelze unter hohem Druck (meist zwischen 500 und 2000 bar) durch die geöffnete Düse und den Anguss bzw. das Angusssystem des Spritzgießwerkzeugs in den formgebenden Hohlraum gedrückt. Die Rückstromsperre verhindert dabei ein Zurückströmen der Schmelze Richtung Einfülltrichter. ⓘ
Während des Einspritzens wird versucht, ein möglichst laminares Fließverhalten der Schmelze zu erreichen. Das heißt, die Schmelze wird im Werkzeug dort, wo sie die gekühlte Werkzeugwand berührt, sofort abgekühlt und bleibt erstarrt „kleben“. Die nachrückende Schmelze wird durch den dadurch verjüngten Schmelzkanal mit noch höherer Geschwindigkeit und noch mehr Scherdeformation gedrückt und vorne an der Schmelzfront zum Rand hin dehndeformiert. Es überlagert sich Wärmeabfuhr über die Werkzeugwand und Wärmezufuhr durch Schererwärmung. Die hohe Einspritzgeschwindigkeit erzeugt in der Schmelze eine Schergeschwindigkeit, welche die Schmelze leichter fließen lässt. Dennoch ist ein stets schnelles Einspritzen nicht anzustreben, denn durch die hohe Schergeschwindigkeit wird auch der Molekülabbau verstärkt. Auch die Oberfläche, das Aussehen und der Orientierungszustand werden durch die Einspritzphase beeinflusst. ⓘ
Nachdrücken und Abkühlen
Da das Werkzeug (mit typischerweise 20 bis 120 °C) kälter als die Kunststoffmasse (mit typischerweise 200 bis 300 °C) ist, kühlt die Schmelze in der Form ab und erstarrt bei Erreichen des Gefrierpunktes. Das Abkühlen geht einher mit einer Volumenschwindung, die sich nachteilig auf Maßhaltigkeit und Oberflächenqualität des Werkstückes auswirkt. Um diese Schwindung teilweise zu kompensieren, wird auch nach Füllung der Form ein reduzierter Druck aufrechterhalten, damit Material nachfließen und die Schwindung ausgleichen kann. Dieses Nachdrücken kann so lange erfolgen, bis der Siegelpunkt erreicht ist, also der Anguss erstarrt ist. ⓘ
Nach Beendigung des Nachdrückens kann die Düse geschlossen werden und in der Spritzeinheit bereits der Plastifizier- und Dosiervorgang für das nächste Formteil beginnen. Das Material in der Form kühlt in der Restkühlzeit weiter ab, bis auch die Seele, der flüssige Kern des Werkstückes, erstarrt ist und eine zum Entformen hinreichende Steifigkeit erreicht ist. ⓘ
Die Spritzeinheit wird dann von der Schließeinheit wegbewegt (abgehoben), da kein Kunststoff mehr aus dem Anguss austreten kann. Dies dient dazu, einen zu starken Wärmeübergang von der wärmeren Düse auf das kältere Werkzeug zu unterbinden und vermeidet so ein zu starkes Abkühlen der Düse (Einfrieren). ⓘ
Entformen
Zum Entformen öffnet sich die Auswerferseite der Schließeinheit und wird das Werkstück durch in die Kavität hineindringende Stifte ausgeworfen. Es fällt dann entweder herunter (Schüttgut) oder wird durch Handlinggeräte aus dem Werkzeug entnommen und geordnet abgelegt oder gleich einer Weiterverarbeitung zugeführt. ⓘ
Der Anguss muss entweder durch separate Bearbeitung entfernt werden oder wird beim Entformen automatisch abgetrennt. Auch angussloses Spritzgießen ist mit Heißkanalsystemen möglich, bei denen das Angusssystem ständig über der Erstarrungstemperatur bleibt und das enthaltene Material somit für den nächsten Schuss verwendet werden kann. ⓘ
Nach dem Entformen schließt sich das Werkzeug wieder und der Zyklus beginnt von neuem. ⓘ
Schritte | 1 s | 2 s | 3 s | 4 s | 5 s | 6 s | 7 s | 8 s | 9 s | 10 s | 11 s | 12 s | 13 s | 14 s | 15 s | 16 s | 17 s | 18 s | 19 s | 20 s | 21 s | 22 s |
---|---|---|---|---|---|---|---|---|---|---|---|---|---|---|---|---|---|---|---|---|---|---|
Werkzeug schließen | ||||||||||||||||||||||
Spritzeinheit vor | ||||||||||||||||||||||
Plastifizieren | ||||||||||||||||||||||
Einspritzen | ||||||||||||||||||||||
Nachdrücken | ||||||||||||||||||||||
Dekomprimieren | ||||||||||||||||||||||
Spritzeinheit zurück | ||||||||||||||||||||||
Restkühlen | ||||||||||||||||||||||
Entformen | ||||||||||||||||||||||
Pause | ||||||||||||||||||||||
Physikalische Kühlzeit |
Verwendete Kunststoffarten und Produkte
Spritzgussteile können mit Massen zwischen einigen Milligramm und ca. 150 kg hergestellt werden. Die verarbeiteten thermoplastischen Kunststoffe werden durch Additive und Füllstoffe für die Spritzgießverarbeitung und die spätere Verwendung modifiziert. Darunter sind auch sehr harte anorganische Füllstoffe wie Glaskugeln oder sehr oft Glasfasern. ⓘ
Im Fahrzeugbau werden Polyolefine, hauptsächlich Polypropylen für Armaturenbretter und Stoßstangen im Spritzguss verwendet. Plexiglas (PMMA) und Polycarbonat (PC) werden für transparente Gegenstände (Kfz-Scheinwerfer, Rückleuchten) verwendet. Polystyrol (PS) und dessen Copolymere (ABS = Acrylnitril-Butadien-Styrol) werden größtenteils für Spielzeug (z. B. Lego) und Haushaltsgeräte benutzt. Polyamid (PA), Polyoxymethylen (POM) und viele weitere technische Kunststoffe werden ebenfalls im Maschinenbau und der Elektrotechnik eingesetzt, allerdings in wesentlich geringeren Mengen für meist hochpreisige Teile. ⓘ
Beim Naturfaser-Spritzguss werden mit Naturfasern gefüllte Thermoplaste verwendet. ⓘ
Duroplast-Spritzgießen
Verfahren
Das Duroplast-Spritzgießen unterscheidet sich vom Thermoplast-Spritzgießen in seinen Betriebsparametern. Duroplaste härten meistens durch Einwirken von Wärme aus. Nach dem Aushärten ist ein erneutes Aufschmelzen nicht mehr möglich, nur ein Recycling. Die noch nicht ausgehärtete Masse muss deshalb mit einer vergleichsweise niedrigen Temperatur (je nach Material ca. 30 bis 110 °C) in die Form eingespritzt und dort durch eine höhere Temperatur (je nach Duroplast zwischen 130 °C und 250 °C) ausgehärtet werden. ⓘ
Die aufbereitete Formmasse fließt u. a. wegen der hohen Füllstoffanteile schlechter als Thermoplastschmelzen. Auf diese Besonderheiten muss der Spritzgießvorgang abgestimmt werden. ⓘ
Die Spritzgießmaschine arbeitet mit einer Förderschnecke, die wenig Scherwärme erzeugt. Die erzielbaren Drücke betragen bis zu 2500 bar. Das Formteil wird heiß entformt. Angussloses Spritzgießen ist mit Kaltkanalsystemen, dem Pendant zum Heißkanalsystem, bei dem der Anguss gekühlt und so eine Vernetzung verhindert wird, möglich. ⓘ
Mit dem Duroplast-Spritzgießen können sehr große Wanddicken der Teile von bis zu 50 mm realisiert werden. ⓘ
Anwendung
Ein typisches Anwendungsgebiet für Duroplaste (BMC) sind Fahrzeugscheinwerfer, genauer deren Reflektoren, bei denen die gute Maßhaltigkeit und Temperaturbeständigkeit von Duroplasten zum Tragen kommt. Bei Wanddicken bis ca. 4 mm allerdings sind die Zykluszeiten der Duroplastverarbeitung meist länger als die bei Thermoplasten, so dass Duroplaste, wenn auf ihre besonderen elektrischen und mechanischen Qualitäten verzichtet werden kann, im Wirtschaftlichkeitsvergleich trotz ihres im Allgemeinen günstigeren Materialpreises meist gegenüber den Thermoplasten verlieren. ⓘ
Elastomer-Spritzgießen
Elastomere – wie Naturkautschuk – vulkanisieren analog zu den Duroplasten durch den Einfluss von Wärme. Das Werkzeug muss also auch hier heißer als die Formmasse beim Einspritzvorgang sein. Eine Ausnahme bilden die thermoplastischen Elastomere. ⓘ
Das Spritzgießen von Elastomeren erfolgt auf Schneckenspritzgießmaschinen. Elastomere können in Form von rieselfähigen Pulvern oder bandförmig von einer speziellen Förderschnecke, die wenig Scherung in die plastifizierte Masse einbringt, eingezogen werden. Der Zylinder wird meist mit einer Flüssigkeit auf ca. 80 °C temperiert (Wassertemperierung), um Überhitzung zu vermeiden, was ein vorzeitiges Ausvulkanisieren des Elastomers zufolge hätte. Des Weiteren stellt auch das gratfreie Spritzgießen von Elastomeren eine besondere Herausforderung dar, da Elastomere im Fließbereich (genauso wie Duroplaste) sehr dünnflüssig sind, so ist auch der Aufwand bei der Werkzeuggestaltung etwas höher als bei Thermoplastwerkzeugen. ⓘ
Von den genannten Besonderheiten abgesehen, verläuft der Spritzgießvorgang prinzipiell auch hier ähnlich wie beim Thermoplast-Spritzgießen ab. Die Schnecke knetet und mischt die Formmasse, die dadurch homogen aufbereitet wird. Dadurch lässt sich z. B. gegenüber dem Pressen, bei dem durch die Wärmezufuhr von außen eine inhomogene Temperaturverteilung entsteht, eine Qualitätsverbesserung der hergestellten Formteile erzielen. Einige mechanische Eigenschaften können bis zu 30 % höher liegen als bei gepressten Elastomeren. ⓘ
Beim Strömen in der Düse und in den Angusskanälen entsteht Reibungswärme. Dies verkürzt die Vulkanisierzeit. Dadurch wird der Spritzgießprozess besonders wirtschaftlich. Die hohe Materialviskosität macht relativ große Angussquerschnitte erforderlich. Auch bei Elastomeren sind Kaltkanalsysteme einsetzbar. ⓘ
Man verwendet beim Elastomerspritzgießen oft Spritzgießmaschinen mit mehreren Schließeinheiten für mehrere Werkzeuge und unterschiedlicher Teile, da die Vulkanisierzeit erheblich größer ist als die Aufbereitungszeit in der Spritzeinheit. ⓘ
Spezielle Verfahren
Das oben beschriebene Grundverfahren lässt sich für spezielle Anwendungszwecke modifizieren bzw. erweitern. ⓘ
So erlaubt das Mehrkomponenten-Spritzgießen die Herstellung von Teilen aus unterschiedlichen Kunststoffen in einem Arbeitsgang. Beim In-Mold-Verfahren werden in das Spritzgießwerkzeug eingelegte Materialien hinterspritzt, z. B. der Hartschaum eines Sporthelmes oder beschriftete Folien (In-Mould-Labeling, IML). Alternativ kann bei der In-Mould Decoration (IMD) auch nur eine bedruckte Folie, die später entfernt wird, eingelegt werden, so dass nur die Farbe auf dem Teil verbleibt. Das Metallfolienhinterspritzen dient der Herstellung von Kunststoffteilen mit Metallfolienüberzug. ⓘ
Wird der Werkstoff in eine nicht ganz geschlossene Form eingespritzt und die Form erst danach vollends geschlossen, so spricht man vom Spritzprägen. Dieses kann zum Quellflussprägen erweitert werden, indem dabei Materialien hinterspritzt werden, analog zum In-Mold-Verfahren. ⓘ
Beim Innendruck-Spritzgießen (auch Fluidinjektionstechnik (FIT) genannt und aufteilbar in Gasinnendruck-Spritzgießen (GID) und Wasserinnendruck-Spritzgießen (WID)) wird zusätzlich ein Gas oder Wasser injiziert, welches nach dem Erstarren oder Aushärten entweicht, so dass ein Hohlraum entsteht. Dagegen dient beim Gashinterdruck-Verfahren (GHD) das zwischen Werkzeugwand und Formteil eingebrachte Gas dem festen Anpressen an die gegenüberliegende Wand, um u. a. eine hohe Oberflächenqualität zu erreichen. Gase können auch mit Treibmitteln verteilt im Kunststoff erzeugt werden, was einen Schaumstoff ergibt (Thermoplast-Schaumgießen (TSG)). ⓘ
Beim Schmelzkern-Spritzgießen wird ein niedrigschmelzendes Metall eingegossen, das nachher im Heizbad ausgeschmolzen wird, um ebenfalls einen Hohlraum zu schaffen. ⓘ
Das Pulverspritzgießen (Powder Injection Molding (PIM)) erlaubt die Herstellung von Metall- und Keramikteilen, indem Metall- und Keramikpulver mit einem Bindemittel spritzgegossen, das Bindemittel danach entfernt und das verbleibende Pulver schließlich gesintert wird. ⓘ
Das Extrusionsspritzgießen (Exjection) stellt eine Kombination aus Spritzgießen und Extrusion dar. Durch dieses Verfahren werden lange funktionalisierte Profile und Leisten auf einer kleinen Spritzgießmaschine hergestellt. Durch die Rotationstechnologie ist eine endlose Produktion mit mehreren Kavitäten, welche permanent Schließen und Öffnen, auch möglich. ⓘ
Beim Spritzstreckblasen wird ein spritzgegossener Rohling, z. B. ein PET-Rohling für Flaschen einem anschließenden Streck- und Blasformprozess unterzogen. ⓘ
Ein Tandem-Werkzeug ähnelt einem klassischen Werkzeug. Es befindet sich jeweils eine Kavität an jeder der zwei Trennebenen. Die Angüsse können je nach Belieben heiß oder kalt ausgeführt sein. Durch die Dopplung ist es möglich, die erste Kavität zu spritzen und, während diese abkühlt, die andere Kavität zu füllen. So ist es möglich, die nicht genutzte Zeit der ersten Erkaltung produktiv zu nutzen. ⓘ
Probleme
Durch die vielfältigen Möglichkeiten bei der Wahl der Bauteilgeometrie, des genauen Spritzverfahrens und des Werkstoffes können beim Spritzprozess bzw. beim fertigen Bauteil verschiedene, meist unerwünschte, Effekte auftreten. Angusshöfe, bei denen die Oberflächenstruktur und -Form vom restlichen Bauteil abweicht, entstehen an der Schnittstelle zwischen Anguss und eigentlichem Bauteil. Gründe hierfür können eine lokale Umorientierung der Moleküle des Werkstoffs, zu hohe Einspritzgeschwindigkeit oder zu geringe Prozesstemperaturen sein. Lufteinschlüsse entstehen bei schlecht gewählter Bauteilgeometrie, zu niedrigen Prozesstemperaturen, zu hoher Einspritzgeschwindigkeit oder mangelhafter Entlüftung. Werden solche Lufteinschlüsse durch den Prozess stark verdichtet, so kann es zu lokal sehr hohen Temperaturen und in deren Folge zu Verkohlungen im Bauteil kommen. Hierbei spricht man auch vom Dieseleffekt. Einfallstellen und generell Verzug, also die Abweichung der Bauteilform von der eigentlich gewünschten, entstehen nach dem Ausformen, beim Abkühlen. Hierfür sind vielfältige Faktoren zu berücksichtigen. Bei der Wahl der Bauteilgeometrie können etwa Massenanhäufungen durch lokal unterschiedliche Wandstärken des Bauteils dazu führen, dass die einzelnen Bereiche beim Abkühlen unterschiedlich stark schrumpfen oder auch unterschiedlich schnell abkühlen. Auch eine nicht optimale Prozesstemperatur oder seltener ein nicht genügend homogener Ausgangsstoff können diese Probleme verursachen. ⓘ
Arbeitsschutz
Bei Kunststoffspritzgießmaschinen handelt es sich um gekapselte Anlagen, an denen in der Regel eine Exposition gegenüber Gefahrstoffen nur bei bestimmten Tätigkeiten, insbesondere bei Umrüst- und Instandhaltungsarbeiten sowie ggf. bei der Probenahme und beim Auftreten von Leckagen möglich ist. Trotzdem können Zersetzungsprodukte bei der Verarbeitung thermoplastischer Kunststoffe in Spritzgießmaschinen in der Luft für Beschäftigte eine Gefahr darstellen. ⓘ
Die Empfehlungen Gefährdungsermittlung der Unfallversicherungsträger (EGU) basieren auf Messungen möglicher Zersetzungsprodukte thermoplastischer Kunststoffe in Spritzgießmaschinen in der Luft an Arbeitsplätzen. Sie stellen ein geeignetes Beurteilungsverfahren für die Exposition bei der Verarbeitung von Kunststoffen in Spritzgießmaschinen dar und bieten praktische Unterstützung bei der Durchführung der Gefährdungsbeurteilung – inklusive Schutzmaßnahmen – gemäß der Gefahrstoffverordnung. Dermale Gefährdungen, z. B. durch heiße Oberflächen und erhitzte Kunststoffe müssen in der Gefährdungsbeurteilung gesondert berücksichtigt werden. ⓘ