Verbrennungsmotor

- C - Kurbelwelle
- E - Auslassnockenwelle
- I - Einlassnockenwelle
- P - Kolben
- R - Pleuelstange
- S - Zündkerze
- V - Ventile. rot: Auslass, blau: Einlass.
- W - Kühlwassermantel
- graue Struktur - Motorblock ⓘ

Ein Verbrennungsmotor (ICE oder IC-Motor) ist eine Wärmekraftmaschine, in der die Verbrennung eines Kraftstoffs mit einem Oxidationsmittel (in der Regel Luft) in einer Verbrennungskammer stattfindet, die ein integraler Bestandteil des Kreislaufs der Arbeitsflüssigkeit ist. In einem Verbrennungsmotor übt die Expansion der durch die Verbrennung erzeugten Hochtemperatur- und Hochdruckgase eine direkte Kraft auf eine Komponente des Motors aus. Die Kraft wird in der Regel auf Kolben (Kolbenmotor), Turbinenschaufeln (Gasturbine), einen Rotor (Wankelmotor) oder eine Düse (Strahltriebwerk) ausgeübt. Durch diese Kraft wird das Bauteil über eine bestimmte Strecke bewegt, wobei chemische Energie in kinetische Energie umgewandelt wird, die zum Vortrieb, zur Bewegung oder zum Antrieb des Motors verwendet wird. Dies ersetzte den externen Verbrennungsmotor für Anwendungen, bei denen das Gewicht oder die Größe eines Motors wichtiger waren. ⓘ
Der erste kommerziell erfolgreiche Verbrennungsmotor wurde um 1860 von Étienne Lenoir entwickelt, und der erste moderne Verbrennungsmotor, der so genannte Otto-Motor, wurde 1876 von Nicolaus Otto entwickelt. Der Begriff Verbrennungsmotor bezieht sich in der Regel auf einen Motor, bei dem die Verbrennung intermittierend erfolgt, wie bei den bekannteren Viertakt- und Zweitakt-Kolbenmotoren sowie bei Varianten wie dem Sechstakt-Kolbenmotor und dem Wankelmotor. Eine zweite Klasse von Verbrennungsmotoren arbeitet mit kontinuierlicher Verbrennung: Gasturbinen, Düsentriebwerke und die meisten Raketentriebwerke, die alle Verbrennungsmotoren sind und auf demselben Prinzip beruhen wie oben beschrieben. Schusswaffen sind ebenfalls eine Form von Verbrennungsmotoren, allerdings von so spezieller Art, dass sie üblicherweise als eigene Kategorie behandelt werden, zusammen mit Waffen wie Mörsern und Flugabwehrkanonen. Im Gegensatz dazu wird bei externen Verbrennungsmotoren, wie z. B. Dampf- oder Stirlingmotoren, die Energie an ein Arbeitsmedium abgegeben, das nicht aus Verbrennungsprodukten besteht, mit diesen vermischt oder verunreinigt ist. Zu den Arbeitsmitteln für externe Verbrennungsmotoren gehören Luft, heißes Wasser, unter Druck stehendes Wasser oder sogar flüssiges Natrium, das in einem Kessel erhitzt wird. ⓘ
Es gibt zwar viele stationäre Anwendungen, aber die meisten Verbrennungsmotoren werden in mobilen Anwendungen eingesetzt und sind die primäre Energiequelle für Fahrzeuge wie Autos, Flugzeuge und Boote. ICEs werden in der Regel mit fossilen Brennstoffen wie Erdgas oder Erdölprodukten wie Benzin, Dieselkraftstoff oder Heizöl betrieben. Erneuerbare Kraftstoffe wie Biodiesel werden in Kompressionszündungsmotoren und Bioethanol oder ETBE (Ethyl-tert-Butylether), das aus Bioethanol hergestellt wird, in Fremdzündungsmotoren verwendet. Bereits im Jahr 1900 verwendete der Erfinder des Dieselmotors, Rudolf Diesel, Erdnussöl zum Betrieb seiner Motoren. Erneuerbare Kraftstoffe werden häufig mit fossilen Kraftstoffen gemischt. Wasserstoff, der selten verwendet wird, kann entweder aus fossilen Brennstoffen oder aus erneuerbaren Energien gewonnen werden. ⓘ

1. Ansaugen
2. Verdichten
3. Arbeiten
4. Ausstoßen ⓘ
Geschichte
Verschiedene Wissenschaftler und Ingenieure trugen zur Entwicklung von Verbrennungsmotoren bei. Im Jahr 1791 entwickelte John Barber die Gasturbine. Im Jahr 1794 ließ Thomas Mead einen Gasmotor patentieren. Ebenfalls 1794 ließ Robert Street einen Verbrennungsmotor patentieren, der auch der erste war, der mit flüssigem Kraftstoff betrieben wurde, und baute zu dieser Zeit einen Motor. Im Jahr 1798 baute John Stevens den ersten amerikanischen Verbrennungsmotor. 1807 entwickelten die französischen Ingenieure Nicéphore Niépce (der später die Fotografie erfand) und Claude Niépce den Prototyp eines Verbrennungsmotors mit kontrollierten Staubexplosionen, den Pyréolophore, der von Napoleon Bonaparte zum Patent angemeldet wurde. Dieser Motor trieb ein Boot auf der Saône in Frankreich an. Im selben Jahr erfand der Schweizer Ingenieur François Isaac de Rivaz einen Verbrennungsmotor auf Wasserstoffbasis, der durch elektrische Funken angetrieben wurde. Im Jahr 1808 baute de Rivaz seine Erfindung in ein primitives Fahrzeug ein - das erste Automobil mit Verbrennungsmotor der Welt". 1823 patentierte Samuel Brown den ersten Verbrennungsmotor, der industriell genutzt wurde. ⓘ
Im Jahr 1854 erhielten die italienischen Erfinder Eugenio Barsanti und Felice Matteucci im Vereinigten Königreich die Zertifizierung: "Erlangung von Antriebskraft durch die Explosion von Gasen". Im Jahr 1857 erteilte ihnen das Great Seal Patent Office das Patent Nr. 1655 für die Erfindung eines "Verbesserten Apparats zur Gewinnung von Antriebskraft aus Gasen". Barsanti und Matteucci erhielten zwischen 1857 und 1859 weitere Patente für die gleiche Erfindung in Frankreich, Belgien und Piemont. Im Jahr 1860 stellte der belgische Ingenieur Jean Joseph Etienne Lenoir einen gasbetriebenen Verbrennungsmotor her. 1864 patentierte Nicolaus Otto den ersten atmosphärischen Gasmotor. 1872 erfand der Amerikaner George Brayton den ersten kommerziellen, mit Flüssigkeit betriebenen Verbrennungsmotor. 1876 begann Nicolaus Otto seine Zusammenarbeit mit Gottlieb Daimler und Wilhelm Maybach und patentierte den Viertaktmotor mit komprimierter Ladung. Im Jahr 1879 patentierte Karl Benz einen zuverlässigen Zweitakt-Benzinmotor. Später, im Jahr 1886, begann Benz mit der ersten kommerziellen Produktion von Kraftfahrzeugen mit Verbrennungsmotor, bei denen ein dreirädriger Viertaktmotor und ein Fahrgestell eine Einheit bildeten. 1892 entwickelte Rudolf Diesel den ersten Motor mit Kompressionsladung und Selbstzündung. Im Jahr 1926 startete Robert Goddard die erste Rakete mit Flüssigkeitsantrieb. 1939 wurde die Heinkel He 178 das erste Düsenflugzeug der Welt. ⓘ

Nach gut 150 Jahren weiterer Entwicklungsarbeit an Verbrennungsmotoren zeichnete sich ein Ende der Möglichkeiten ab. Die kohlenstoffbasierten Verbrennungsmotoren gelten im 21. Jahrhundert zunehmend als unerwünscht. Im November 2021 beschlossen rund 2 Dutzend Staaten auf der Weltklimakonferenz von Glasgow eine Erklärung zum Verbot von Verbrennungsmotoren im Bereich der automobilen Nutzung. Deutschland unterzeichnete die Erklärung mit Hinweis auf nicht ausgeschöpftes Potential alternativer Brennstoffe nicht. Das Entwicklungs- und Anwendungspotential von Verbrennungsmotoren für alternative Energien war bis zum Ende der 2010er-Jahre nicht abschließend erforscht. Anfang der 2020er-Jahre zeichneten sich Möglichkeiten für die Zukunftsfähigkeit von Wasserstoffverbrennungsmotoren ab. ⓘ
Etymologie
Früher bezeichnete das Wort Motor (aus dem Altfranzösischen, von lateinisch ingenium, "Fähigkeit") jede Art von Maschine - eine Bedeutung, die sich in Ausdrücken wie Belagerungsmaschine erhalten hat. Ein "Motor" (von lateinisch motor, "Beweger") ist jede Maschine, die mechanische Kraft erzeugt. Traditionell werden Elektromotoren nicht als "Motoren" bezeichnet; Verbrennungsmotoren werden jedoch häufig als "Motoren" bezeichnet. (Ein Elektromotor ist eine mit Strom betriebene Lokomotive.) ⓘ
In der Schifffahrt wird ein Verbrennungsmotor, der in den Rumpf eingebaut ist, als Motor bezeichnet, während die Motoren, die auf dem Heckspiegel sitzen, als Motoren bezeichnet werden. ⓘ
Anwendungen

Hubkolbenmotoren sind die bei weitem häufigste Antriebsquelle für Land- und Wasserfahrzeuge, darunter Autos, Motorräder, Schiffe und in geringerem Maße auch Lokomotiven (einige sind elektrisch, die meisten verwenden jedoch Dieselmotoren). Kreiskolbenmotoren der Wankel-Bauart werden in einigen Automobilen, Flugzeugen und Motorrädern eingesetzt. Diese werden unter dem Begriff Fahrzeuge mit Verbrennungsmotor (ICEV) zusammengefasst. ⓘ
Wo ein hohes Leistungsgewicht erforderlich ist, kommen Verbrennungsmotoren in Form von Verbrennungsturbinen oder manchmal auch Wankelmotoren zum Einsatz. Motorflugzeuge verwenden in der Regel einen Verbrennungsmotor, bei dem es sich um einen Hubkolbenmotor handeln kann. Flugzeuge können stattdessen auch Düsentriebwerke und Hubschrauber Turbowellen verwenden; beides sind Arten von Turbinen. Zusätzlich zum Antrieb können Verkehrsflugzeuge einen separaten Verbrennungsmotor als Hilfstriebwerk einsetzen. Viele unbemannte Flugzeuge sind mit Wankelmotoren ausgestattet. ⓘ
ICEs treiben große Stromgeneratoren an, die elektrische Netze versorgen. Sie werden in Form von Verbrennungsturbinen mit einer typischen elektrischen Leistung von etwa 100 MW eingesetzt. Kombikraftwerke nutzen die hohen Abgastemperaturen, um Wasserdampf zum Betrieb einer Dampfturbine zu kochen und zu überhitzen. Dadurch ist der Wirkungsgrad höher, weil mehr Energie aus dem Brennstoff gewonnen wird, als durch den Verbrennungsmotor allein gewonnen werden könnte. Kombikraftwerke erreichen Wirkungsgrade im Bereich von 50 bis 60 %. In kleinerem Maßstab werden stationäre Motoren wie Gasmotoren oder Dieselgeneratoren als Notstromaggregate oder für die Stromversorgung von Gebieten ohne Stromnetzanschluss eingesetzt. ⓘ
Kleinmotoren (in der Regel 2-Takt-Benzinmotoren) sind eine gängige Stromquelle für Rasenmäher, Fadentrimmer, Kettensägen, Laubbläser, Hochdruckreiniger, Schneemobile, Jetskis, Außenbordmotoren, Mopeds und Motorräder. ⓘ
Klassifizierung
Es gibt mehrere Möglichkeiten, Verbrennungsmotoren zu klassifizieren. ⓘ
Hubkolbenmotoren
Nach Anzahl der Takte:
- Zweitaktmotor
- Schreiberzyklus
- Tagestakt
- Viertaktmotor (Otto-Zyklus)
- Sechs-Takt-Motor ⓘ
Nach Art der Zündung:
- Motor mit Selbstzündung
- Fremdgezündeter Motor (häufig als Ottomotor anzutreffen) ⓘ
Nach mechanischem/thermodynamischem Zyklus (diese Zyklen werden nur selten verwendet, sind aber häufig in Hybridfahrzeugen und anderen Fahrzeugen zu finden, die mit dem Ziel der Kraftstoffeffizienz hergestellt werden):
- Atkinson-Zyklus
- Miller-Zyklus ⓘ
Nach dem Bewegungsablauf
- Hubkolbenmotor (typischerweise Schubkurbel mit Pleuel und Kurbelwelle bei großen Motoren zusätzlich Kreuzkopf und Kolbenstange, exotische Konstruktionen Freikolbenmotor, Knickpleuelmotor, Kurbelschlaufenmotor oder kurbelwellenlose Kurvenscheibenmotoren)
- Rotationskolbenmotor (zum Beispiel der Wankelmotor) ⓘ
Kontinuierliche Verbrennung
- Gasturbinentriebwerk
- Staustrahltriebwerk (Ramjet), ähnlich wie ein Turbotriebwerk, nutzt jedoch die Geschwindigkeit des Fahrzeugs, um die Luft zu komprimieren (Ram), anstatt einen Kompressor zu verwenden.
- Scramjet, eine Variante des Staustrahltriebwerks, bei der die Luft mit Überschall verbrannt wird.
- Raketentriebwerk ⓘ
Hubkolbentriebwerke
Der Wankelmotor ist ein Drehkolbenmotor, der von Felix Wankel erfunden und nach ihm benannt ist. Beim Wankelmotor sind zwei kinematische Formen möglich: Zum einen der Kreiskolbenmotor, bei dem ein bogig-dreieckiger Kolben (Gleichdick) in einem oval-scheibenförmigen Gehäuse auf einer von der Exzenterwelle bestimmten Kreisbahn umläuft. Zum anderen der Drehkolbenmotor, bei dem sowohl der bogig-dreieckige Läufer als auch die oval-scheibenförmige Hüllfigur (Trochoide) auf leicht versetzten Achsen um ihre Schwerpunkte rotieren. ⓘ
Der Stelzer-Motor, benannt nach seinem Erfinder Frank Stelzer, ist ein Zweitakt-Freikolbenmotor mit einem beweglichen Teil, das „Stufenkolben“ genannt wird. Es besteht aus drei starr durch eine Kolbenstange verbundenen Kolben. Der mittlere ist ein doppelt wirkender Scheibenkolben als Spülpumpe für die beiden äußeren Arbeitskolben, die als Kolben schlitzgesteuerter, gleichstromgespülter Zweitakter arbeiten. Wegen der Kolbenstange sind die Brennräume dieser Zweitakter ringförmig. Die äußeren Enden des Stufenkolbens bewegen sich aus dem Motorblock heraus und können Teil einer Arbeitsmaschine sein, zum Beispiel eines Verdichters oder elektrischen Generators. ⓘ
Der Mederer-Motor und der Kreuzschleifenmotor haben einen etwas anderen Bewegungsablauf des Kolbens. ⓘ
Der Kugelmotor: Der erste patentierte Kugelmotor wurde von Frank Berry 1961 in den USA entwickelt. Es folgte ein weiteres Modell, das von dem Diplom-Physiker Wolfhart Willimczik nach 1974 entwickelt wurde und nach dem Zweitakt-Prinzip arbeitet. Herbert Hüttlin entwickelte einen Kugelmotor, der mit gekrümmten Kolben arbeitet, die sich gegeneinander bewegen. Dieser Motor wird im Schrifttum unter dem Oberbegriff Rotationskolbenmaschine genannt. Von Arnold Wagner wird der Hiteng-Kugelmotor entwickelt. Der Hiteng-Kugelmotor arbeitet mit zwei Doppelkolben, die sich in einem kugelförmigen Gehäuse drehen. Der Erfinder bezeichnet diesen Motor als Schwenkkolbenmaschine. ⓘ
In der ersten Hälfte des 20. Jahrhunderts wurde eine Reihe exotischer Konstruktionen entworfen, die jedoch das Prototypstadium nicht überschritten. Durch Fortschritte der Werkstoffforschung sind Lösungen für Probleme alter Konstruktionen möglich. ⓘ
Aufbau
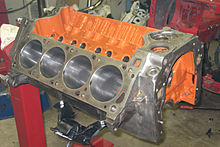

Die Basis eines Hubkolbenmotors ist der Motorblock, der in der Regel aus Gusseisen (wegen seiner guten Verschleißfestigkeit und geringen Kosten) oder aus Aluminium hergestellt wird. In letzterem Fall bestehen die Zylinderlaufbuchsen aus Gusseisen oder Stahl oder aus einer Beschichtung wie Nikasil oder Alusil. Der Motorblock enthält die Zylinder. Bei Motoren mit mehr als einem Zylinder sind diese in der Regel entweder in einer Reihe (Reihenmotor) oder in zwei Reihen (Boxermotor oder V-Motor) angeordnet; bei modernen Motoren werden gelegentlich drei Reihen verwendet (W-Motor), und auch andere Motorkonfigurationen sind möglich und wurden verwendet. Einzylindermotoren (oder Thumper) sind bei Motorrädern und anderen kleinen Motoren in leichten Maschinen üblich. An der Außenseite des Zylinders sind Kanäle für die Kühlflüssigkeit in den Motorblock eingegossen, während bei einigen Hochleistungsmotoren die Kanäle in Form von abnehmbaren und austauschbaren Zylinderbuchsen ausgeführt sind. Wassergekühlte Motoren verfügen über Kanäle im Motorblock, in denen die Kühlflüssigkeit zirkuliert (der Wassermantel). Einige kleine Motoren sind luftgekühlt. Anstelle eines Wassermantels hat der Zylinderblock Rippen, die von ihm abstehen und den Motor durch direkte Wärmeabgabe an die Luft kühlen. Die Zylinderwände werden in der Regel durch Honen bearbeitet, um eine Kreuzschraffur zu erhalten, die mehr Öl zurückhalten kann. Eine zu raue Oberfläche würde den Motor schnell durch übermäßigen Verschleiß am Kolben schädigen. ⓘ
Bei den Kolben handelt es sich um kurze zylindrische Teile, die ein Ende des Zylinders gegen den hohen Druck der Druckluft und der Verbrennungsprodukte abdichten und während des Betriebs des Motors kontinuierlich im Zylinder gleiten. Bei kleineren Motoren bestehen die Kolben aus Aluminium, während sie bei größeren Anwendungen in der Regel aus Gusseisen hergestellt werden. Die obere Wand des Kolbens wird als Kolbenboden bezeichnet und ist normalerweise flach oder konkav. Einige Zweitaktmotoren verwenden Kolben mit einem Umlenkkopf. Die Kolben sind unten offen und bis auf eine integrierte Verstärkungsstruktur (den Kolbensteg) hohl. Wenn ein Motor in Betrieb ist, übt der Gasdruck im Verbrennungsraum eine Kraft auf den Kolbenboden aus, die über den Steg auf einen Kolbenbolzen übertragen wird. Jeder Kolben ist am Umfang mit Ringen versehen, die größtenteils verhindern, dass Gase in das Kurbelgehäuse oder Öl in den Brennraum entweichen. Ein Entlüftungssystem leitet die geringe Menge an Gas, die bei normalem Betrieb an den Kolben vorbei entweicht (die Blow-by-Gase), aus dem Kurbelgehäuse ab, damit sie sich nicht ansammelt und das Öl verunreinigt und Korrosion verursacht. Bei Zweitakt-Ottomotoren ist das Kurbelgehäuse Teil des Luft-Kraftstoff-Weges, und da es kontinuierlich strömt, benötigen Zweitaktmotoren kein separates Kurbelgehäuseentlüftungssystem. ⓘ
Der Zylinderkopf ist mit zahlreichen Bolzen oder Stehbolzen am Motorblock befestigt. Er hat mehrere Funktionen. Der Zylinderkopf dichtet die Zylinder auf der den Kolben gegenüberliegenden Seite ab; er enthält kurze Kanäle (die Kanäle) für Einlass und Auslass und die dazugehörigen Einlassventile, die sich öffnen, um den Zylinder mit Frischluft zu füllen, und Auslassventile, die sich öffnen, um die Verbrennungsgase entweichen zu lassen. Bei Zweitaktmotoren mit Kurbelgehäusespülung sind die Gaskanäle jedoch direkt mit der Zylinderwand verbunden, ohne Tellerventile; stattdessen steuert der Kolben ihr Öffnen und Verschließen. Der Zylinderkopf enthält auch die Zündkerze bei Motoren mit Fremdzündung und die Einspritzdüse bei Motoren mit Direkteinspritzung. Alle Kompressionszündungsmotoren verwenden eine Kraftstoffeinspritzung, in der Regel eine Direkteinspritzung, einige Motoren verwenden jedoch auch eine indirekte Einspritzung. Fremdzündungsmotoren können einen Vergaser oder eine Kraftstoffeinspritzung als Saugrohreinspritzung oder Direkteinspritzung verwenden. Die meisten Fremdzündungsmotoren haben eine einzelne Zündkerze pro Zylinder, einige haben jedoch 2. Eine Kopfdichtung verhindert, dass Gas zwischen dem Zylinderkopf und dem Motorblock entweicht. Das Öffnen und Schließen der Ventile wird durch eine oder mehrere Nockenwellen und Federn gesteuert - oder bei einigen Motoren durch einen desmodromischen Mechanismus, der keine Federn verwendet. Die Nockenwelle kann direkt auf den Ventilschaft drücken oder auf einen Kipphebel wirken, wiederum entweder direkt oder über eine Stößelstange. ⓘ

Das Kurbelgehäuse ist unten mit einer Ölwanne verschlossen, die das bei normalem Betrieb ablaufende Öl auffängt, um es wieder in den Kreislauf zurückzuführen. In dem zwischen dem Zylinderblock und der Ölwanne entstehenden Hohlraum befindet sich eine Kurbelwelle, die die Hin- und Herbewegung der Kolben in eine Drehbewegung umwandelt. Die Kurbelwelle wird durch Hauptlager gegenüber dem Motorblock in Position gehalten und kann sich dadurch drehen. Eine Hälfte jedes Hauptlagers wird durch Schotten im Kurbelgehäuse gebildet, die andere Hälfte ist ein abnehmbarer Deckel. In einigen Fällen wird ein einziger Hauptlagerdeckel anstelle mehrerer kleinerer Kappen verwendet. Eine Pleuelstange ist an einem Ende mit versetzten Abschnitten der Kurbelwelle (den Kurbelzapfen) und am anderen Ende über den Kolbenbolzen mit dem Kolben verbunden und überträgt so die Kraft und die Hin- und Herbewegung der Kolben in die Kreisbewegung der Kurbelwelle. Das Ende der Pleuelstange, das mit dem Kolbenbolzen verbunden ist, wird als kleines Ende bezeichnet, das andere Ende, an dem sie mit der Kurbelwelle verbunden ist, als großes Ende. Das große Ende hat eine abnehmbare Hälfte, damit es um die Kurbelwelle herum montiert werden kann. Es wird durch abnehmbare Bolzen mit der Pleuelstange zusammen gehalten. ⓘ
Der Zylinderkopf hat einen Ansaugkrümmer und einen Auspuffkrümmer, die an den entsprechenden Anschlüssen befestigt sind. Der Ansaugkrümmer ist direkt mit dem Luftfilter verbunden oder mit einem Vergaser, wenn ein solcher vorhanden ist, der wiederum mit dem Luftfilter verbunden ist. Er verteilt die von diesen Geräten kommende Luft auf die einzelnen Zylinder. Der Auspuffkrümmer ist das erste Bauteil der Abgasanlage. Er sammelt die Abgase aus den Zylindern und leitet sie zur nächsten Komponente im Weg. Die Abgasanlage eines Verbrennungsmotors kann auch einen Katalysator und einen Schalldämpfer umfassen. Der letzte Abschnitt auf dem Weg der Abgase ist das Auspuffrohr. ⓘ
4-Takt-Motoren

1 - Ansaugung
2 - Verdichtung
3 - Leistung
4 - Auspuff ⓘ
Der obere Totpunkt (OT) eines Kolbens ist die Position, in der er den Ventilen am nächsten ist; der untere Totpunkt (UT) ist die entgegengesetzte Position, in der er am weitesten von ihnen entfernt ist. Ein Hub ist die Bewegung eines Kolbens vom oberen Totpunkt zum unteren Totpunkt oder umgekehrt und der damit verbundene Vorgang. Während ein Motor in Betrieb ist, dreht sich die Kurbelwelle kontinuierlich mit nahezu konstanter Drehzahl. Bei einem 4-Takt-Verbrennungsmotor durchläuft jeder Kolben pro Kurbelwellenumdrehung 2 Hübe in der folgenden Reihenfolge. Ausgehend von der Beschreibung bei OT sind dies:
- Einlass, Ansaugung oder Ansaugen: Die Einlassventile sind geöffnet, da die Nockenwelle auf den Ventilschaft drückt. Der Kolben bewegt sich nach unten und vergrößert das Volumen des Verbrennungsraums, so dass im Falle eines Verbrennungsmotors Luft oder im Falle eines Fremdzündungsmotors ohne Direkteinspritzung ein Luft-Kraftstoff-Gemisch einströmen kann. Das Luft- oder Kraftstoff-Luft-Gemisch wird in jedem Fall als Ladung bezeichnet.
- Verdichtung: Bei diesem Hub sind beide Ventile geschlossen, und der Kolben bewegt sich nach oben, wodurch sich das Volumen des Verbrennungsraums verringert, das sein Minimum erreicht, wenn sich der Kolben im oberen Totpunkt befindet. Der Kolben verrichtet bei der Verdichtung Arbeit an der Ladung, wodurch sich deren Druck, Temperatur und Dichte erhöhen; eine Annäherung an dieses Verhalten liefert das ideale Gasgesetz. Kurz bevor der Kolben den oberen Totpunkt erreicht, beginnt die Zündung. Bei einem Ottomotor erhält die Zündkerze einen Hochspannungsimpuls, der den namensgebenden Funken erzeugt und die Ladung zündet. Bei einem Fremdzündungsmotor spritzt die Einspritzdüse den Kraftstoff schnell in den Brennraum; der Kraftstoff entzündet sich aufgrund der hohen Temperatur.
- Kraft- oder Arbeitstakt: Der Druck der Verbrennungsgase drückt den Kolben nach unten und erzeugt dabei mehr kinetische Energie als zur Verdichtung der Ladung erforderlich ist. Komplementär zum Verdichtungshub dehnen sich die Verbrennungsgase aus, wodurch ihre Temperatur, ihr Druck und ihre Dichte abnehmen. Wenn sich der Kolben in der Nähe des oberen Totpunkts befindet, öffnet sich das Auslassventil. Die Verbrennungsgase dehnen sich aufgrund des verbleibenden Drucks - der den Gegendruck, den Überdruck an der Auslassöffnung, übersteigt - unumkehrbar aus; dies wird als Abblasen bezeichnet.
- Auspuff: Das Auslassventil bleibt geöffnet, während sich der Kolben nach oben bewegt und die Verbrennungsgase ausstößt. Bei Saugmotoren kann im Normalbetrieb ein kleiner Teil der Verbrennungsgase im Zylinder verbleiben, weil der Kolben den Brennraum nicht vollständig schließt; diese Gase lösen sich in der nächsten Ladung. Am Ende dieses Hubes schließt sich das Auslassventil, das Einlassventil öffnet sich, und die Abfolge wiederholt sich im nächsten Zyklus. Das Einlassventil kann sich öffnen, bevor sich das Auslassventil schließt, um eine bessere Spülung zu ermöglichen. ⓘ
2-Takt-Motoren
Das charakteristische Merkmal dieses Motortyps ist, dass jeder Kolben bei jeder Kurbelwellenumdrehung einen Zyklus durchläuft. Die 4 Vorgänge Ansaugung, Verdichtung, Kraft und Auspuff finden in nur 2 Hüben statt, so dass es nicht möglich ist, jedem dieser Vorgänge einen eigenen Hub zu widmen. Der Zyklus beginnt am oberen Totpunkt und besteht aus:
- Leistung: Während sich der Kolben absenkt, verrichten die Verbrennungsgase wie bei einem 4-Takt-Motor Arbeit an ihm. Es gelten die gleichen thermodynamischen Überlegungen zur Expansion.
- Spülung: Etwa 75° der Kurbelwellendrehung vor dem oberen Totpunkt öffnet sich das Auslassventil oder der Auslasskanal, und es kommt zum Abblasen. Kurz darauf öffnet sich das Einlassventil oder der Überströmkanal. Die einströmende Ladung verdrängt die restlichen Verbrennungsgase in die Auspuffanlage, und ein Teil der Ladung kann auch in die Auspuffanlage gelangen. Der Kolben erreicht den oberen Totpunkt und kehrt die Richtung um. Nachdem der Kolben eine kurze Strecke nach oben in den Zylinder gefahren ist, schließt sich das Auslassventil oder die Auslassöffnung; kurz darauf schließt sich auch das Einlassventil oder die Einlassöffnung.
- Verdichtung: Bei geschlossenem Einlass- und Auslassventil bewegt sich der Kolben weiter nach oben und komprimiert die Ladung, wobei er Arbeit verrichtet. Wie bei einem 4-Takt-Motor beginnt die Zündung kurz bevor der Kolben den oberen Totpunkt erreicht, und es gelten die gleichen Überlegungen zur Thermodynamik der Verdichtung der Ladung. ⓘ
Während ein 4-Takt-Motor den Kolben als Verdrängerpumpe verwendet, um die Spülung in zwei der vier Takte durchzuführen, nutzt ein 2-Takt-Motor den letzten Teil des Arbeitstakts und den ersten Teil des Verdichtungstakts für die kombinierte Ansaug- und Auspuffleistung. Die zur Verdrängung der Lade- und Abgase erforderliche Arbeit wird entweder vom Kurbelgehäuse oder von einem separaten Gebläse geleistet. Für die Spülung, den Ausstoß von verbranntem Gas und die Zufuhr von frischem Gemisch, werden zwei Hauptansätze beschrieben: Schleifenspülung und Uniflow-Spülung. In den 2010er Jahren veröffentlichte SAE News, dass Loop Scavenging" unter allen Umständen besser ist als Uniflow Scavenging. ⓘ
Kurbelgehäuse mit Spülung

Einige Fremdzündungsmotoren sind kurbelgehäusespült und verwenden keine Tellerventile. Stattdessen werden das Kurbelgehäuse und der Teil des Zylinders unterhalb des Kolbens als Pumpe verwendet. Die Ansaugöffnung ist über ein vom Motor angetriebenes Lamellenventil oder ein Drehscheibenventil mit dem Kurbelgehäuse verbunden. Für jeden Zylinder gibt es einen Überströmkanal, der an einem Ende mit dem Kurbelgehäuse und am anderen Ende mit der Zylinderwand verbunden ist. Die Auslassöffnung ist direkt mit der Zylinderwand verbunden. Der Überström- und der Auslasskanal werden durch den Kolben geöffnet und geschlossen. Das Lamellenventil öffnet sich, wenn der Kurbelgehäusedruck etwas unter dem Ansaugdruck liegt, damit es mit neuer Ladung gefüllt werden kann; dies geschieht, wenn sich der Kolben nach oben bewegt. Wenn sich der Kolben nach unten bewegt, steigt der Druck im Kurbelgehäuse und das Lamellenventil schließt sich sofort, so dass die Ladung im Kurbelgehäuse komprimiert wird. Wenn sich der Kolben nach unten bewegt, gibt er auch die Auslassöffnung und die Überströmöffnung frei, und der höhere Druck der Ladung im Kurbelgehäuse führt dazu, dass sie durch die Überströmöffnung in den Zylinder gelangt und die Abgase ausbläst. Die Schmierung erfolgt durch die Zugabe von 2-Takt-Öl zum Kraftstoff in kleinen Verhältnissen. Petroil bezeichnet das Gemisch aus Benzin und dem oben genannten Öl. Diese Art von 2-Takt-Motoren hat einen geringeren Wirkungsgrad als vergleichbare 4-Takt-Motoren und stößt unter den folgenden Bedingungen mehr umweltschädliche Abgase aus:
- Sie verwenden ein Totalverlust-Schmiersystem: Das gesamte Schmieröl wird schließlich zusammen mit dem Kraftstoff verbrannt.
- Es gibt widersprüchliche Anforderungen an die Spülung: Einerseits muss in jedem Zyklus genügend Frischladung zugeführt werden, um fast alle Verbrennungsgase zu verdrängen, andererseits bedeutet eine zu hohe Zufuhr, dass ein Teil der Ladung in die Abgase gelangt.
- Sie müssen die Überströmöffnung(en) als sorgfältig konstruierte und platzierte Düse verwenden, so dass ein Gasstrom erzeugt wird, der den gesamten Zylinder überstreicht, bevor er die Auslassöffnung erreicht, um die Verbrennungsgase zu verdrängen, aber die Menge der ausgestoßenen Ladung zu minimieren. 4-Takt-Motoren haben den Vorteil, dass fast alle Verbrennungsgase zwangsweise ausgestoßen werden, da der Brennraum beim Auspuff auf sein minimales Volumen reduziert wird. Bei 2-Takt-Motoren mit Kurbelgehäusespülung erfolgen Ausstoß und Einlass meist gleichzeitig und bei maximalem Brennraumvolumen. ⓘ
Der Hauptvorteil dieser 2-Takt-Motoren ist ihre mechanische Einfachheit und ihr besseres Leistungsgewicht als das ihrer 4-Takt-Pendants. Trotz der doppelten Anzahl von Arbeitstakten pro Zyklus wird in der Praxis weniger als die doppelte Leistung eines vergleichbaren 4-Takt-Motors erreicht. ⓘ
In den USA wurden 2-Takt-Motoren wegen der Umweltverschmutzung für Straßenfahrzeuge verboten. Motorräder, die nur im Gelände eingesetzt werden, haben oft noch 2-Takt-Motoren, sind aber selten für den Straßenverkehr zugelassen. Allerdings sind viele Tausende von 2-Takt-Motoren für die Rasenpflege im Einsatz. ⓘ
Gebläse mit Spülung

Durch die Verwendung eines separaten Gebläses werden viele der Mängel der Kurbelgehäusespülung vermieden, allerdings auf Kosten einer höheren Komplexität, die zu höheren Kosten und einem höheren Wartungsaufwand führt. Ein solcher Motor hat Einlasskanäle oder -ventile und Auslassventile, mit Ausnahme von Gegenkolbenmotoren, die auch Auslasskanäle verwenden können. Das Gebläse ist in der Regel ein Roots-Gebläse, aber es werden auch andere Typen verwendet. Diese Konstruktion ist bei Fremdzündungsmotoren üblich und wurde gelegentlich auch bei Fremdzündungsmotoren verwendet. ⓘ
Fremdzündungsmotoren, die ein Gebläse verwenden, arbeiten in der Regel mit Uniflow-Spülung. Bei dieser Bauart befinden sich in der Zylinderwand mehrere Einlassöffnungen, die in gleichmäßigen Abständen entlang des Umfangs knapp über der Position angeordnet sind, die der Kolbenboden im oberen Totpunkt erreicht. Es werden ein oder mehrere Auslassventile wie bei 4-Takt-Motoren verwendet. Der letzte Teil des Ansaugkrümmers ist eine Luftleitung, die die Einlassöffnungen versorgt. Die Einlasskanäle sind in einem horizontalen Winkel zur Zylinderwand angeordnet (d. h. sie befinden sich in der Ebene des Kolbenbodens), um der einströmenden Ladung einen Drall zu verleihen und die Verbrennung zu verbessern. Die größten Hubkolben-Verbrennungsmotoren sind niedertourige Verbrennungsmotoren dieses Typs; sie werden für Schiffsantriebe (siehe Schiffsdieselmotor) oder zur Stromerzeugung eingesetzt und erreichen die höchsten thermischen Wirkungsgrade unter den Verbrennungsmotoren aller Art. Einige dieselelektrische Lokomotivmotoren arbeiten nach dem 2-Takt-Verfahren. Die stärksten von ihnen haben eine Bremsleistung von etwa 4,5 MW oder 6.000 PS. Die Lokomotiven der Baureihe EMD SD90MAC sind ein Beispiel für solche Lokomotiven. Die vergleichbare Baureihe GE AC6000CW, deren Antriebsmaschine fast die gleiche Bremsleistung hat, verwendet einen 4-Takt-Motor. ⓘ
Ein Beispiel für einen solchen Motor ist der turbogeladene 2-Takt-Dieselmotor RT-flex96-C von Wärtsilä-Sulzer, der in großen Containerschiffen eingesetzt wird. Er ist der effizienteste und leistungsstärkste Hubkolben-Verbrennungsmotor der Welt mit einem thermischen Wirkungsgrad von über 50 %. Zum Vergleich: Die effizientesten kleinen Viertaktmotoren haben einen thermischen Wirkungsgrad von etwa 43 % (SAE 900648); die Größe ist aufgrund des größeren Verhältnisses von Volumen zu Oberfläche ein Vorteil für den Wirkungsgrad. ⓘ
Unter den externen Links finden Sie ein Video über die Verbrennung im Zylinder eines optisch zugänglichen 2-Takt-Motorradmotors. ⓘ
Historische Konstruktion
Dugald Clerk entwickelte den ersten Zweitaktmotor im Jahr 1879. Er verwendete einen separaten Zylinder, der als Pumpe fungierte, um das Kraftstoffgemisch in den Zylinder zu befördern. ⓘ
Im Jahr 1899 vereinfachte John Day Clerks Konstruktion zu dem heute weit verbreiteten Zweitaktmotor. Day-Motoren haben eine Kurbelgehäusespülung und sind kanalgesteuert. Das Kurbelgehäuse und der Teil des Zylinders unterhalb der Auslassöffnung werden als Pumpe verwendet. Der Betrieb des Day-Cycle-Motors beginnt, wenn die Kurbelwelle gedreht wird, so dass sich der Kolben vom oberen Totpunkt nach oben (zum Zylinderkopf hin) bewegt und ein Unterdruck im Kurbelgehäuse/Zylinderbereich entsteht. Der Vergaser leitet dann das Kraftstoffgemisch über ein Lamellenventil oder ein Drehscheibenventil (das vom Motor angetrieben wird) in das Kurbelgehäuse. Für die Ansaugung gibt es eingegossene Kanäle vom Kurbelgehäuse zur Öffnung im Zylinder und einen weiteren von der Auslassöffnung zum Auspuffrohr. Die Höhe der Öffnung im Verhältnis zur Länge des Zylinders wird als "Öffnungszeit" bezeichnet. ⓘ
Beim ersten Aufwärtshub des Motors wird kein Kraftstoff in den Zylinder eingesaugt, da das Kurbelgehäuse leer ist. Beim Abwärtshub verdichtet der Kolben nun das Kraftstoffgemisch, das den Kolben im Zylinder und die Lager geschmiert hat, da dem Kraftstoffgemisch Öl zugesetzt wurde. Wenn sich der Kolben nach unten bewegt, gibt er zunächst den Auspuff frei, aber beim ersten Hub gibt es keinen verbrannten Kraftstoff zum Auspuff. Wenn sich der Kolben weiter nach unten bewegt, gibt er die Ansaugöffnung frei, die einen Kanal hat, der zum Kurbelgehäuse führt. Da das Kraftstoffgemisch im Kurbelgehäuse unter Druck steht, bewegt sich das Gemisch durch den Kanal und in den Zylinder. ⓘ
Da es im Zylinder kein Hindernis für den Kraftstoff gibt, direkt aus der Auslassöffnung zu strömen, bevor der Kolben weit genug angehoben ist, um die Öffnung zu schließen, verwendeten frühe Motoren einen hoch gewölbten Kolben, um den Kraftstofffluss zu verlangsamen. Später wurde der Kraftstoff mit Hilfe einer Expansionskammer in den Zylinder zurückgesaugt. Wenn sich der Kolben nahe dem oberen Totpunkt befindet, zündet ein Funke den Kraftstoff. Wenn der Kolben mit Kraft nach unten getrieben wird, gibt er zunächst die Auslassöffnung frei, wo der verbrannte Kraftstoff unter hohem Druck ausgestoßen wird, und dann die Einlassöffnung, wo der Prozess abgeschlossen ist und sich immer wieder wiederholt. ⓘ
Spätere Motoren verwendeten eine von der Firma Deutz entwickelte Art der Ansaugung zur Leistungssteigerung. Es wurde das Schnurle Reverse Flow System genannt. DKW lizenzierte diese Konstruktion für alle seine Motorräder. Die DKW RT 125 war eines der ersten Kraftfahrzeuge, das dadurch einen Verbrauch von über 100 mpg erreichte. ⓘ
Zündung
Verbrennungsmotoren erfordern eine Zündung des Gemischs, entweder durch Fremdzündung (SI) oder Selbstzündung (CI). Vor der Erfindung zuverlässiger elektrischer Verfahren wurden Heißrohr- und Flammenverfahren verwendet. Es wurden Versuchsmotoren mit Laserzündung gebaut. ⓘ
Verfahren der Funkenzündung

Der Fremdzündungsmotor war eine Weiterentwicklung der frühen Motoren, die mit der Glührohrzündung arbeiteten. Als Bosch den Magnetzünder entwickelte, wurde dieser zum primären System für die Stromerzeugung zur Erregung einer Zündkerze. Viele kleine Motoren verwenden noch immer Magnetzünder. Kleine Motoren werden mit einem Rücklaufstarter oder einer Handkurbel von Hand angekurbelt. Vor der Entwicklung des Anlassers durch Charles F. Kettering von Delco wurden alle Autos mit Benzinmotor mit einer Handkurbel gestartet. ⓘ
Größere Motoren treiben ihre Anlasser und Zündsysteme in der Regel mit der in einer Blei-Säure-Batterie gespeicherten elektrischen Energie an. Der Ladezustand der Batterie wird durch eine Lichtmaschine oder (früher) einen Generator aufrechterhalten, der die Motorkraft nutzt, um elektrische Energie zu speichern. ⓘ
Die Batterie liefert elektrische Energie zum Starten, wenn der Motor mit einem Anlasser ausgestattet ist, und sie liefert elektrische Energie, wenn der Motor abgestellt ist. Die Batterie liefert auch Strom, wenn die Lichtmaschine in seltenen Fällen nicht mehr als 13,8 Volt aufrechterhalten kann (bei einem üblichen 12-Volt-Bordnetz). Wenn die Spannung der Lichtmaschine unter 13,8 Volt fällt, übernimmt der Blei-Säure-Akku zunehmend die elektrische Last. In praktisch allen Betriebszuständen, einschließlich des normalen Leerlaufs, liefert die Lichtmaschine die primäre elektrische Energie. ⓘ
Bei einigen Systemen wird die Feldleistung (Rotor) der Lichtmaschine bei weit geöffneter Drosselklappe abgeschaltet. Durch die Abschaltung des Feldes wird die mechanische Belastung der Generatorriemenscheibe auf nahezu Null reduziert und die Leistung der Kurbelwelle maximiert. In diesem Fall liefert die Batterie die gesamte primäre elektrische Energie. ⓘ
Benzinmotoren saugen ein Gemisch aus Luft und Benzin an und verdichten es durch die Bewegung des Kolbens vom unteren Totpunkt zum oberen Totpunkt, wenn der Kraftstoff maximal verdichtet ist. Die Verkleinerung der überstrichenen Fläche des Zylinders und die Berücksichtigung des Volumens des Verbrennungsraums werden durch ein Verhältnis beschrieben. Frühe Motoren hatten ein Verdichtungsverhältnis von 6 zu 1. Mit der Erhöhung des Verdichtungsverhältnisses nahm auch der Wirkungsgrad des Motors zu. ⓘ
Mit den frühen Ansaug- und Zündsystemen mussten die Verdichtungsverhältnisse niedrig gehalten werden. Dank Fortschritten in der Kraftstofftechnologie und im Verbrennungsmanagement können Hochleistungsmotoren zuverlässig mit einem Verhältnis von 12:1 betrieben werden. Bei Kraftstoff mit niedriger Oktanzahl trat ein Problem auf, wenn das Verdichtungsverhältnis bei der Zündung des Kraftstoffs aufgrund des damit verbundenen Temperaturanstiegs anstieg. Charles Kettering entwickelte einen Bleizusatz, der höhere Verdichtungsverhältnisse ermöglichte, der aber ab den 1970er Jahren nach und nach für den Einsatz in Kraftfahrzeugen aufgegeben wurde, unter anderem aufgrund von Bedenken wegen Bleivergiftung. ⓘ
Das Kraftstoffgemisch wird bei unterschiedlichen Kolbenbewegungen im Zylinder gezündet. Bei niedrigen Drehzahlen wird der Zündzeitpunkt so gewählt, dass der Kolben den oberen Totpunkt erreicht. Um mehr Leistung zu erzeugen, wird der Zündfunke bei steigender Drehzahl während der Kolbenbewegung früher gezündet. Der Funke wird gezündet, während der Kraftstoff noch komprimiert wird, und zwar mit steigender Drehzahl immer stärker. ⓘ
Die erforderliche Hochspannung, in der Regel 10.000 Volt, wird von einer Induktionsspule oder einem Transformator geliefert. Bei der Induktionsspule handelt es sich um ein Fly-Back-System, bei dem der elektrische Primärstrom durch eine Art synchronisierten Unterbrecher unterbrochen wird. Bei dem Unterbrecher kann es sich entweder um Kontaktpunkte oder einen Leistungstransistor handeln. Das Problem bei dieser Art der Zündung ist, dass mit steigender Drehzahl die Verfügbarkeit von elektrischer Energie abnimmt. Dies ist besonders problematisch, da die zur Zündung eines dichteren Kraftstoffgemischs erforderliche Energiemenge höher ist. Das Ergebnis war häufig eine Fehlzündung bei hohen Drehzahlen. ⓘ
Die Kondensatorentladungszündung wurde entwickelt. Sie erzeugt eine ansteigende Spannung, die an die Zündkerze weitergeleitet wird. CD-Systemspannungen können bis zu 60.000 Volt erreichen. CD-Zündungen verwenden Aufwärtstransformatoren. Der Aufwärtstransformator nutzt die in einer Kapazität gespeicherte Energie, um einen elektrischen Funken zu erzeugen. Bei beiden Systemen liefert ein mechanisches oder elektrisches Steuersystem eine sorgfältig getimte Hochspannung an den richtigen Zylinder. Dieser Funke zündet über die Zündkerze das Luft-Kraftstoff-Gemisch in den Zylindern des Motors. ⓘ
Obwohl Benzinverbrennungsmotoren bei kaltem Wetter viel leichter zu starten sind als Dieselmotoren, können sie unter extremen Bedingungen dennoch Probleme beim Starten haben. Jahrelang bestand die Lösung darin, das Auto in beheizten Bereichen zu parken. In einigen Teilen der Welt wurde das Öl abgelassen und über Nacht erwärmt, um es dann für Kaltstarts wieder in den Motor zu geben. In den frühen 1950er Jahren wurde der Benzinvergaser entwickelt, bei dem beim Kaltstart das Rohbenzin in das Gerät geleitet wurde, wo ein Teil des Kraftstoffs verbrannt wurde und der andere Teil zu heißem Dampf wurde, der direkt in den Ansaugkrümmer geleitet wurde. Diese Anlage war recht beliebt, bis elektrische Motorblockheizungen bei Benzinmotoren, die in kalten Klimazonen verkauft wurden, Standard wurden. ⓘ
Kompressionszündung
Diesel-, PPC- und HCCI-Motoren nutzen für die Zündung ausschließlich die hohe Temperatur und den hohen Druck, die der Motor beim Verdichtungsprozess erzeugt. Der Verdichtungsgrad ist in der Regel doppelt so hoch oder höher als bei einem Benzinmotor. Dieselmotoren saugen nur Luft an und sprühen kurz vor Erreichen der maximalen Verdichtung eine kleine Menge Dieselkraftstoff über eine Einspritzdüse in den Zylinder, so dass der Kraftstoff sofort zündet. HCCI-Motoren saugen sowohl Luft als auch Kraftstoff an, sind aber aufgrund höherer Drücke und Temperaturen weiterhin auf eine selbsttätige Verbrennung angewiesen. Dies ist auch der Grund, warum Diesel- und HCCI-Motoren anfälliger für Kaltstartprobleme sind, obwohl sie bei kaltem Wetter genauso gut laufen, sobald sie einmal gestartet sind. Leichte Dieselmotoren mit indirekter Einspritzung in Personenkraftwagen und leichten Nutzfahrzeugen verwenden Glühkerzen (oder andere Vorheizungen: siehe Cummins ISB#6BT), die den Verbrennungsraum kurz vor dem Anlassen vorwärmen, um Startprobleme bei kaltem Wetter zu vermeiden. Die meisten Dieselmotoren verfügen auch über eine Batterie und ein Ladesystem; dieses System ist jedoch zweitrangig und wird von den Herstellern als Luxus hinzugefügt, um das Anlassen, das Ein- und Ausschalten des Kraftstoffs (was auch über einen Schalter oder eine mechanische Vorrichtung erfolgen kann) und den Betrieb von elektrischen Zusatzkomponenten und Zubehör zu erleichtern. Die meisten neuen Motoren sind mit elektrischen und elektronischen Motorsteuergeräten (ECU) ausgestattet, die auch den Verbrennungsprozess regeln, um die Effizienz zu steigern und die Emissionen zu verringern. ⓘ
Schmierung


Oberflächen, die mit anderen Oberflächen in Berührung kommen und sich relativ zu ihnen bewegen, müssen geschmiert werden, um Verschleiß und Geräusche zu verringern und die Effizienz zu steigern, indem der Kraftaufwand zur Überwindung der Reibung verringert wird, oder um den Mechanismus überhaupt zum Laufen zu bringen. Außerdem kann der verwendete Schmierstoff überschüssige Wärme reduzieren und die Komponenten zusätzlich kühlen. Ein Motor muss zumindest an folgenden Stellen geschmiert werden:
- Zwischen Kolben und Zylindern
- Kleine Lager
- Große Endlager
- Hauptlager
- Ventiltrieb (Die folgenden Elemente dürfen nicht vorhanden sein):
- Stößel
- Kipphebel
- Stößelstangen
- Steuerkette oder Zahnräder. Zahnriemen müssen nicht geschmiert werden. ⓘ
Bei Zweitaktmotoren mit Kurbelgehäusespülung wird das Innere des Kurbelgehäuses und damit die Kurbelwelle, die Pleuelstange und die Unterseite der Kolben durch das Zweitaktöl im Luft-Kraftstoff-Öl-Gemisch besprüht, das dann zusammen mit dem Kraftstoff verbrannt wird. Der Ventiltrieb kann sich in einem mit Schmiermittel gefluteten Raum befinden, so dass keine Ölpumpe erforderlich ist. ⓘ
Bei einem Tauchschmiersystem wird keine Ölpumpe verwendet. Stattdessen taucht die Kurbelwelle in das Öl im Sumpf ein und bespritzt aufgrund ihrer hohen Geschwindigkeit die Kurbelwelle, die Pleuelstangen und die Unterseite der Kolben. Die Pleuelstangenköpfe können mit einer angebrachten Schöpfkelle versehen sein, um diesen Effekt zu verstärken. Der Ventiltrieb kann auch in einem überfluteten Raum abgedichtet oder zur Kurbelwelle hin so offen sein, dass er das Spritzöl aufnimmt und in den Ölsumpf zurückfließen lässt. Die Spritzschmierung ist bei kleinen 4-Takt-Motoren üblich. ⓘ
Bei einem Zwangsschmiersystem (auch Druckschmierung genannt) erfolgt die Schmierung in einem geschlossenen Kreislauf, der das Motoröl zu den vom System bedienten Oberflächen befördert und das Öl dann in einen Behälter zurückführt. Die Nebenaggregate eines Motors werden in der Regel nicht von diesem Kreislauf versorgt; so kann beispielsweise eine Lichtmaschine Kugellager verwenden, die mit ihrem eigenen Schmiermittel abgedichtet sind. Das Reservoir für das Öl ist in der Regel die Ölwanne, und in diesem Fall spricht man von einem Nasssumpfsystem. Wenn ein anderer Ölbehälter vorhanden ist, wird das Öl zwar immer noch im Kurbelgehäuse aufgefangen, aber durch eine spezielle Pumpe kontinuierlich abgelassen; in diesem Fall spricht man von einem Trockensumpfsystem. ⓘ
Am Boden der Ölwanne befindet sich ein Öleinlass, der mit einem Siebfilter abgedeckt ist, der mit einer Ölpumpe und dann mit einem Ölfilter außerhalb des Kurbelgehäuses verbunden ist. Von dort wird es zu den Hauptlagern der Kurbelwelle und dem Ventiltrieb geleitet. Das Kurbelgehäuse enthält mindestens einen Ölkanal (eine Leitung innerhalb der Kurbelgehäusewand), in den das Öl vom Ölfilter eingeleitet wird. Die Hauptlager haben über den gesamten oder halben Umfang eine Nut, in die das Öl aus Kanälen eintritt, die mit dem Ölkanal verbunden sind. Die Kurbelwelle hat Bohrungen, die das Öl aus diesen Nuten aufnehmen und an die Pleuellager weiterleiten. Alle Pleuellager werden auf diese Weise geschmiert. Ein einziges Hauptlager kann Öl für 0, 1 oder 2 Pleuellager liefern. Ein ähnliches System kann zur Schmierung des Kolbens, seines Kolbenbolzens und des kleinen Endes der Pleuelstange verwendet werden; bei diesem System hat das große Ende der Pleuelstange eine Nut um die Kurbelwelle herum und eine mit der Nut verbundene Bohrung, die das Öl von dort zum Boden des Kolbens und von dort in den Zylinder verteilt. ⓘ
Es werden auch andere Systeme zur Schmierung von Zylinder und Kolben verwendet. Die Pleuelstange kann eine Düse haben, die einen Ölstrahl auf den Zylinder und den Boden des Kolbens wirft. Diese Düse bewegt sich relativ zu dem Zylinder, den sie schmiert, ist aber immer auf ihn oder den entsprechenden Kolben gerichtet. ⓘ
Zwangsschmiersysteme haben in der Regel einen höheren Schmierstoffdurchsatz als für eine ausreichende Schmierung erforderlich ist, um die Kühlung zu unterstützen. Konkret hilft das Schmiersystem, die Wärme von den heißen Motorteilen zur Kühlflüssigkeit (bei wassergekühlten Motoren) oder zu den Kühlrippen (bei luftgekühlten Motoren) zu leiten, die sie dann an die Umgebung abgeben. Der Schmierstoff muss so beschaffen sein, dass er chemisch stabil ist und eine geeignete Viskosität innerhalb des Temperaturbereichs aufweist, in dem er im Motor verwendet wird. ⓘ
Zylinderkonfiguration
Zu den gängigen Zylinderkonfigurationen gehören die Reihen- oder Inline-Konfiguration, die kompaktere V-Konfiguration und die breitere, aber glattere Flach- oder Boxer-Konfiguration. Flugzeugmotoren können auch eine radiale Konfiguration annehmen, die eine effektivere Kühlung ermöglicht. Auch ungewöhnlichere Konfigurationen wie die H-, U-, X- und W-Konfiguration wurden bereits verwendet. ⓘ
Bei Motoren mit mehreren Zylindern sind der Ventiltrieb und die Kurbelwelle so angeordnet, dass sich die Kolben in verschiedenen Abschnitten ihres Zyklus befinden. Es ist wünschenswert, dass die Zyklen der Kolben gleichmäßig verteilt sind (dies wird als gleichmäßige Befeuerung bezeichnet), insbesondere bei Motoren mit Zwangsansaugung; dadurch werden Drehmomentpulsationen verringert und Reihenmotoren mit mehr als drei Zylindern sind in ihren Primärkräften statisch ausgeglichen. Einige Motorkonfigurationen erfordern jedoch eine ungerade Befeuerung, um ein besseres Gleichgewicht zu erreichen, als es mit gerader Befeuerung möglich ist. Ein 4-Takt-I2-Motor ist beispielsweise besser ausgewuchtet, wenn der Winkel zwischen den Kurbelzapfen 180° beträgt, da sich die Kolben in entgegengesetzte Richtungen bewegen und sich die Trägheitskräfte teilweise aufheben. Dies führt jedoch zu einem ungeraden Zündmuster, bei dem ein Zylinder 180° der Kurbelwellenumdrehung nach dem anderen zündet und dann 540° lang kein Zylinder. Bei einem gleichmäßigen Zündmuster würden sich die Kolben im Gleichschritt bewegen und die damit verbundenen Kräfte würden sich addieren. ⓘ
Konfigurationen mit mehreren Kurbelwellen benötigen nicht unbedingt einen Zylinderkopf, da sie stattdessen einen Kolben an jedem Ende des Zylinders haben können, eine so genannte Gegenkolbenkonstruktion. Da die Kraftstoffeinlässe und -auslässe an den gegenüberliegenden Enden des Zylinders angeordnet sind, kann eine Gleichstromspülung erreicht werden, die, wie beim Viertaktmotor, über einen großen Drehzahlbereich hinweg effizient ist. Der thermische Wirkungsgrad wird durch das Fehlen von Zylinderköpfen verbessert. Diese Bauweise wurde beim Junkers-Dieselflugmotor Jumo 205 mit zwei Kurbelwellen an beiden Enden einer einzigen Zylinderreihe und vor allem bei den Napier-Deltic-Dieselmotoren verwendet. Hier wurden drei Kurbelwellen verwendet, um drei Bänke mit doppelendigen Zylindern zu versorgen, die in einem gleichseitigen Dreieck angeordnet waren, wobei die Kurbelwellen an den Ecken lagen. Er wurde auch in Lokomotivmotoren mit nur einer Zylinderreihe verwendet und wird immer noch in Schiffsantriebsmotoren und Hilfsgeneratoren für Schiffe eingesetzt. ⓘ
Diesel-Zyklus

Die meisten Lkw- und Pkw-Dieselmotoren verwenden einen Zyklus, der an einen Viertakt-Zyklus erinnert, bei dem jedoch die Temperaturerhöhung durch die Kompression die Zündung bewirkt und kein separates Zündsystem erforderlich ist. Diese Variante wird als Dieselzyklus bezeichnet. Beim Dieselzyklus wird der Dieselkraftstoff direkt in den Zylinder eingespritzt, so dass die Verbrennung bei konstantem Druck erfolgt, wenn sich der Kolben bewegt. ⓘ
Otto-Zyklus
Der Otto-Zyklus ist der gebräuchlichste Zyklus für die meisten Verbrennungsmotoren in Autos, die Benzin als Kraftstoff verwenden. Er besteht aus denselben Hauptschritten wie beim Viertaktmotor: Ansaugung, Verdichtung, Zündung, Expansion und Auspuff. ⓘ
Fünf-Takt-Motor
1879 baute und verkaufte Nicolaus Otto einen Doppel-Expansionsmotor (das Prinzip der Doppel- und Dreifach-Expansion war bereits bei Dampfmaschinen weit verbreitet) mit zwei kleinen Zylindern zu beiden Seiten eines größeren Niederdruckzylinders, in dem eine zweite Expansion des Auspuffgases stattfand; der Besitzer gab den Motor wegen schlechter Leistung zurück. Im Jahr 1906 wurde das Konzept in ein von der EHV (Eisenhuth Horseless Vehicle Company) gebautes Auto eingebaut, und im 21. Jahrhundert entwickelte und testete Ilmor erfolgreich einen 5-Takt-Verbrennungsmotor mit doppelter Expansion, der eine hohe Leistung und einen niedrigen spezifischen Kraftstoffverbrauch aufwies. ⓘ
Sechs-Takt-Motor
Der Sechstaktmotor wurde im Jahr 1883 erfunden. Vier Arten von Sechs-Takt-Motoren verwenden einen normalen Kolben in einem normalen Zylinder (Griffin-Sechs-Takt, Bajulaz-Sechs-Takt, Velozeta-Sechs-Takt und Crower-Sechs-Takt), der alle drei Kurbelwellenumdrehungen zündet. Bei diesen Systemen wird die Abwärme des Viertakt-Otto-Zyklus durch Einblasen von Luft oder Wasser genutzt. ⓘ
Die Beare Head- und "Piston-Charger"-Motoren arbeiten als Gegenkolbenmotoren mit zwei Kolben in einem Zylinder, die alle zwei statt wie bei einem Viertaktmotor alle vier Umdrehungen zünden. ⓘ
Andere Zyklen
Bei den allerersten Verbrennungsmotoren wurde das Gemisch nicht verdichtet. Im ersten Teil des Abwärtshubs des Kolbens wurde ein Kraftstoff-Luft-Gemisch angesaugt, dann schloss sich das Einlassventil, und im restlichen Teil des Abwärtshubs wurde das Kraftstoff-Luft-Gemisch verbrannt. Das Auslassventil öffnete sich für den Aufwärtshub des Kolbens. Diese Versuche, das Prinzip einer Dampfmaschine zu imitieren, waren sehr ineffizient. Es gibt eine Reihe von Variationen dieser Zyklen, vor allem den Atkinson- und den Miller-Zyklus. ⓘ
Bei Split-Cycle-Motoren werden die vier Takte Ansaugung, Verdichtung, Verbrennung und Auspuff auf zwei getrennte, aber gepaarte Zylinder verteilt. Der erste Zylinder wird für die Ansaugung und Verdichtung verwendet. Die komprimierte Luft wird dann durch einen Übergangskanal vom Verdichtungszylinder in den zweiten Zylinder geleitet, wo die Verbrennung und der Ausstoß stattfinden. Ein Spalttaktmotor ist eigentlich ein Luftkompressor auf der einen und eine Verbrennungskammer auf der anderen Seite. ⓘ
Bisherige Split-Cycle-Motoren hatten zwei große Probleme: schlechte Atmung (volumetrischer Wirkungsgrad) und geringer thermischer Wirkungsgrad. Es werden jedoch neue Konstruktionen eingeführt, die diese Probleme beheben sollen. Der Scuderi-Motor behebt das Atmungsproblem, indem er den Abstand zwischen Kolben und Zylinderkopf durch verschiedene Aufladetechniken verringert. Die Scuderi-Konstruktion erfordert die Verwendung von nach außen öffnenden Ventilen, die es dem Kolben ermöglichen, sich sehr nahe am Zylinderkopf zu bewegen, ohne dass die Ventile stören. Scuderi behebt den geringen thermischen Wirkungsgrad durch Zündung nach dem oberen Totpunkt (ATDC). ⓘ
Die Zündung nach dem oberen Totpunkt kann durch die Verwendung von Hochdruckluft im Überströmkanal erreicht werden, um eine Schallströmung und hohe Turbulenzen im Arbeitszylinder zu erzeugen. ⓘ
Der Viertakt-Kurbelwellenmotor mit einem Kurvenzylinder wurde ebenfalls erfunden, um seine Effizienz zu untersuchen. ⓘ
Verbrennungsturbinen
Strahltriebwerk

Strahltriebwerke verwenden mehrere Reihen von Gebläseschaufeln, um die Luft zu verdichten, die dann in eine Brennkammer gelangt, wo sie mit Kraftstoff (in der Regel JP-Kraftstoff) vermischt und dann gezündet wird. Durch die Verbrennung des Treibstoffs erhöht sich die Temperatur der Luft, die dann aus dem Triebwerk ausgestoßen wird und Schub erzeugt. Ein modernes Turbofan-Triebwerk kann mit einem Wirkungsgrad von bis zu 48 % arbeiten. ⓘ
Ein Mantelstromtriebwerk besteht aus sechs Teilen:
- Gebläse
- Verdichter
- Verbrennungsmotor
- Turbine
- Mischer
- Düse ⓘ
Gasturbinen
In einer Gasturbine wird Luft komprimiert und zum Drehen einer Turbine verwendet. Es handelt sich im Wesentlichen um ein Düsentriebwerk, das seine Leistung auf eine Welle lenkt. Eine Turbine besteht aus drei Stufen: 1) Die Luft wird durch einen Verdichter gesaugt, in dem die Temperatur durch die Kompression steigt, 2) im Brenner wird Brennstoff hinzugefügt und 3) die heiße Luft wird durch Turbinenschaufeln ausgestoßen, die eine mit dem Verdichter verbundene Welle drehen. ⓘ
Eine Gasturbine ist eine Rotationsmaschine, die im Prinzip einer Dampfturbine ähnelt und aus drei Hauptkomponenten besteht: einem Verdichter, einer Brennkammer und einer Turbine. Die Temperatur der Luft wird nach der Verdichtung im Verdichter durch die Verbrennung von Brennstoff in der Brennkammer erhöht. Die erhitzte Luft und die Verbrennungsprodukte dehnen sich in einer Turbine aus, wodurch Arbeit erzeugt wird. Etwa 2⁄3 der Arbeit treibt den Kompressor an; der Rest (etwa 1⁄3) steht als nutzbare Arbeitsleistung zur Verfügung. ⓘ
Gasturbinen gehören zu den effizientesten Verbrennungsmotoren. Die 7HA- und 9HA-Turbinen-Kombikraftwerke von General Electric haben einen Wirkungsgrad von über 61 %. ⓘ
Brayton-Zyklus

Eine Gasturbine ist eine Rotationsmaschine, die im Prinzip einer Dampfturbine ähnelt. Sie besteht aus drei Hauptkomponenten: Verdichter, Brennkammer und Turbine. Die Luft wird im Verdichter komprimiert, wobei es zu einem Temperaturanstieg kommt. Die Temperatur der komprimierten Luft wird durch die Verbrennung des eingespritzten Kraftstoffs in der Brennkammer weiter erhöht, wodurch sich die Luft ausdehnt. Diese Energie treibt die Turbine an, die über eine mechanische Kupplung den Verdichter antreibt. Die heißen Gase werden dann zur Erzeugung von Schub abgeleitet. ⓘ
Gasturbinentriebwerke arbeiten mit einem kontinuierlichen Verbrennungssystem, bei dem Verdichtung, Verbrennung und Expansion gleichzeitig an verschiedenen Stellen im Triebwerk stattfinden, wodurch eine kontinuierliche Leistung erzielt wird. Dabei findet die Verbrennung bei konstantem Druck statt und nicht wie beim Otto-Zyklus bei konstantem Volumen. ⓘ
Wankelmotoren

Der Wankelmotor (Kreiskolbenmotor) hat keine Kolbenhübe. Er arbeitet mit der gleichen Phasentrennung wie der Viertaktmotor, wobei die Phasen an verschiedenen Stellen im Motor stattfinden. Thermodynamisch gesehen folgt er dem Otto-Motorenzyklus und kann daher als "Vier-Phasen-Motor" betrachtet werden. Zwar finden pro Rotorumdrehung in der Regel drei Arbeitstakte statt, doch aufgrund des Verhältnisses von 3:1 zwischen dem Rotor und der Exzenterwelle wird nur ein Arbeitstakt pro Wellenumdrehung ausgeführt. Die Antriebswelle (Exzenterwelle) dreht sich bei jedem Arbeitstakt einmal statt zweimal (Kurbelwelle), wie beim Otto-Zyklus, wodurch ein besseres Leistungsgewicht als bei Kolbenmotoren erreicht wird. Dieser Motortyp wurde vor allem im Mazda RX-8, dem früheren RX-7 und anderen Fahrzeugmodellen verwendet. Der Motor wird auch in unbemannten Luftfahrzeugen verwendet, wo die geringe Größe und das geringe Gewicht sowie das hohe Leistungsgewicht von Vorteil sind. ⓘ
Zwangsansaugung
Unter Zwangsansaugung versteht man die Zuführung von Druckluft in den Ansaugtrakt eines Verbrennungsmotors. Ein Motor mit Zwangsansaugung verwendet einen Gaskompressor, um den Druck, die Temperatur und die Dichte der Luft zu erhöhen. Ein Motor ohne Zwangsansaugung wird als Saugmotor bezeichnet. ⓘ
Die Zwangsansaugung wird in der Automobil- und Luftfahrtindustrie eingesetzt, um die Motorleistung und den Wirkungsgrad zu erhöhen. Sie kommt vor allem Flugmotoren zugute, die in großer Höhe betrieben werden müssen. ⓘ
Die Zwangsansaugung wird durch einen Lader erreicht, bei dem der Verdichter direkt von der Motorwelle angetrieben wird, oder beim Turbolader durch eine Turbine, die von den Motorabgasen angetrieben wird. ⓘ
Kraftstoffe und Oxidationsmittel
Alle Verbrennungsmotoren beruhen auf der Verbrennung eines chemischen Kraftstoffs, in der Regel zusammen mit Luftsauerstoff (es ist jedoch auch möglich, Distickstoffoxid einzuspritzen, um das Gleiche zu erreichen und die Leistung zu erhöhen). Der Verbrennungsprozess führt in der Regel zur Erzeugung einer großen Menge thermischer Energie sowie zur Produktion von Dampf, Kohlendioxid und anderen chemischen Stoffen bei sehr hohen Temperaturen; die erreichte Temperatur wird durch die chemische Zusammensetzung des Kraftstoffs und der Oxidationsmittel (siehe Stöchiometrie) sowie durch die Verdichtung und andere Faktoren bestimmt. ⓘ
Kraftstoffe
Die gebräuchlichsten modernen Kraftstoffe bestehen aus Kohlenwasserstoffen und werden meist aus fossilen Brennstoffen (Erdöl) gewonnen. Zu den fossilen Brennstoffen gehören Dieselkraftstoff, Benzin und Petroleumgas sowie seltener Propan. Abgesehen von den Komponenten für die Kraftstoffzufuhr können die meisten Verbrennungsmotoren, die für den Betrieb mit Benzin ausgelegt sind, ohne größere Änderungen mit Erdgas oder Flüssiggas betrieben werden. Große Dieselmotoren können mit einem Luft-Gas-Gemisch und einer Zündanlage für Dieselkraftstoff betrieben werden. Flüssige und gasförmige Biokraftstoffe wie Ethanol und Biodiesel (eine Form von Dieselkraftstoff, die aus Pflanzen hergestellt wird, die Triglyceride wie Sojabohnenöl liefern) können ebenfalls verwendet werden. Mit entsprechenden Modifikationen können Motoren auch mit Wasserstoffgas, Holzgas oder Holzkohlegas sowie mit so genanntem Erzeugergas aus anderen geeigneten Biomassen betrieben werden. Es wurden auch Versuche mit pulverförmigen Festbrennstoffen durchgeführt, wie z. B. mit dem Magnesium-Injektionszyklus. ⓘ
Gegenwärtig werden folgende Brennstoffe verwendet:
- Petroleum:
- Petroleumbenzin (nordamerikanische Bezeichnung: gasoline, britische Bezeichnung: petrol)
- Petroleum-Diesel.
- Autogas (verflüssigtes Petroleumgas).
- Komprimiertes Erdgas.
- Düsenkraftstoff (Flugkraftstoff)
- Restbrennstoff
- Steinkohle:
- Benzin kann aus Kohlenstoff (Kohle) nach dem Fischer-Tropsch-Verfahren hergestellt werden.
- Dieselkraftstoff kann mit Hilfe des Fischer-Tropsch-Verfahrens aus Kohlenstoff hergestellt werden.
- Biokraftstoffe und Pflanzenöle:
- Erdnussöl und andere Pflanzenöle.
- Holzgas, aus einem bordeigenen Holzvergaser, der festes Holz als Brennstoff verwendet
- Biokraftstoffe:
- Biobutanol (ersetzt Benzin).
- Biodiesel (ersetzt Petrodiesel).
- Dimethylether (ersetzt Petroleumdiesel).
- Bioethanol und Biomethanol (Holzalkohol) und andere Biokraftstoffe (siehe Flexible-fuel vehicle).
- Biogas
- Wasserstoff (hauptsächlich für Raketentriebwerke von Raumfahrzeugen) ⓘ
Sogar flüssige Metallpulver und Sprengstoffe wurden bereits verwendet. Motoren, die Gase als Kraftstoff verwenden, werden als Gasmotoren und solche, die flüssige Kohlenwasserstoffe verwenden, als Ölmotoren bezeichnet; umgangssprachlich werden Ottomotoren jedoch oft auch als "Gasmotoren" ("Benzinmotoren" außerhalb Nordamerikas) bezeichnet. ⓘ
Die wichtigsten Einschränkungen für Kraftstoffe sind, dass sie leicht durch das Kraftstoffsystem zur Verbrennungskammer transportiert werden können und dass der Kraftstoff bei der Verbrennung genügend Energie in Form von Wärme freisetzt, um den Motor sinnvoll zu nutzen. ⓘ
Dieselmotoren sind im Allgemeinen schwerer, lauter und bei niedrigeren Drehzahlen leistungsstärker als Benzinmotoren. Außerdem sind sie in den meisten Fällen kraftstoffsparender und werden in schweren Straßenfahrzeugen, einigen Autos (zunehmend wegen ihrer höheren Kraftstoffeffizienz gegenüber Benzinmotoren), Schiffen, Eisenbahnlokomotiven und Leichtflugzeugen eingesetzt. Benzinmotoren werden in den meisten anderen Straßenfahrzeugen verwendet, einschließlich der meisten Autos, Motorräder und Mopeds. In Europa haben hochentwickelte Autos mit Dieselmotor seit den 1990er Jahren etwa 45 % des Marktes erobert. Es gibt auch Motoren, die mit Wasserstoff, Methanol, Ethanol, Flüssiggas (LPG), Biodiesel, Paraffin und Traktorverdampferöl (TVO) betrieben werden. ⓘ
- Motorenbenzin (siehe auch: Ottokraftstoff, Oktanzahl)
- Dieselkraftstoff
- JP-8 (Turbinenkraftstoff, Anwendung in militärischen Dieselmotoren)
- Kerosin (Turbinenkraftstoff, Anwendung in militärischen Dieselmotoren)
- Biodiesel (Pflanzenöl nach Veresterung)
- Pflanzenöl
- Fettsäuremethylester (als Beimischung zum Diesel)
- Autogas (LPG)
- Methan (Erdgas (CNG); Biogas; Holzgas)
- Methanol (MeOH; CH3OH)
- Ethanol (EtOH; C2H5OH; rein oder als Beimischung)
- Hythan (CH4 und H2)
- Teeröl, Schweröl (für größere stationäre Motoren und Schiffsmotoren)
- Kohlenstaub
- Wasserstoff
- Generatorgas
- Gichtgas
- Holzgas
- Nitromethan (meist nur als Kraftstoffzusatz) ⓘ
Wasserstoff
Wasserstoff könnte in Zukunft herkömmliche fossile Kraftstoffe in traditionellen Verbrennungsmotoren ersetzen. Alternativ dazu könnte die Brennstoffzellentechnologie ihr Versprechen einlösen und der Einsatz von Verbrennungsmotoren könnte sogar schrittweise abgeschafft werden. ⓘ
Es gibt zwar mehrere Möglichkeiten, freien Wasserstoff zu erzeugen, aber diese Methoden erfordern die Umwandlung von brennbaren Molekülen in Wasserstoff oder den Verbrauch von elektrischer Energie. Solange dieser Strom nicht aus einer erneuerbaren Quelle stammt und nicht für andere Zwecke benötigt wird, ist Wasserstoff keine Lösung für die Energiekrise. In vielen Situationen liegt der Nachteil von Wasserstoff gegenüber kohlenstoffhaltigen Brennstoffen in seiner Lagerung. Flüssiger Wasserstoff hat eine extrem niedrige Dichte (14-mal geringer als Wasser) und erfordert eine umfangreiche Isolierung, während gasförmiger Wasserstoff schwere Tanks erfordert. Selbst in verflüssigtem Zustand hat Wasserstoff eine höhere spezifische Energie, aber die volumetrische Energiespeicherung ist immer noch etwa fünfmal geringer als bei Benzin. Die Energiedichte von Wasserstoff ist jedoch wesentlich höher als die von Elektrobatterien, was ihn zu einem ernsthaften Anwärter als Energieträger für den Ersatz fossiler Brennstoffe macht. Das "Hydrogen on Demand"-Verfahren (siehe direkte Borhydrid-Brennstoffzelle) erzeugt Wasserstoff nach Bedarf, hat aber andere Probleme, wie den hohen Preis des Rohstoffs Natriumborhydrid. ⓘ
Oxidationsmittel

Da Luft an der Erdoberfläche im Überfluss vorhanden ist, wird als Oxidationsmittel in der Regel Luftsauerstoff verwendet, der den Vorteil hat, dass er nicht im Fahrzeug gespeichert werden muss. Dies erhöht das Verhältnis von Leistung zu Gewicht und Leistung zu Volumen. Andere Materialien werden für spezielle Zwecke verwendet, oft um die Leistung zu erhöhen oder um den Betrieb unter Wasser oder im Weltraum zu ermöglichen.
- Druckluft wurde häufig in Torpedos verwendet.
- Im japanischen Torpedo des Typs 93 wurde komprimierter Sauerstoff sowie etwas komprimierte Luft verwendet. Einige U-Boote führen reinen Sauerstoff mit. Raketen verwenden sehr oft flüssigen Sauerstoff.
- Nitromethan wird einigen Renn- und Modellkraftstoffen zugesetzt, um die Leistung zu erhöhen und die Verbrennung zu steuern.
- Distickstoffoxid wird - zusammen mit zusätzlichem Benzin - in taktischen Flugzeugen und in speziell ausgerüsteten Autos verwendet, um Motoren, die sonst mit Benzin und Luft betrieben werden, kurzzeitig mehr Leistung zu verleihen. Es wird auch in der Rakete von Burt Rutan verwendet.
- Der Wasserstoffperoxidantrieb wurde für deutsche U-Boote des Zweiten Weltkriegs entwickelt. Es wurde möglicherweise in einigen nicht-nuklearen U-Booten verwendet und kam in einigen Raketentriebwerken zum Einsatz (vor allem im Schwarzen Pfeil und im Messerschmitt Me 163 Raketenjäger).
- Andere Chemikalien wie Chlor oder Fluor wurden versuchsweise eingesetzt, haben sich aber nicht als praktisch erwiesen. ⓘ
Kühlung
Eine Kühlung ist erforderlich, um übermäßige Hitze abzuführen - hohe Temperaturen können zu Motorschäden führen, die in der Regel auf Verschleiß (aufgrund von durch hohe Temperaturen verursachten Schmierfehlern), Rissbildung oder Verformung zurückzuführen sind. Die beiden häufigsten Formen der Motorkühlung sind luft- und wassergekühlt. Die meisten modernen Kraftfahrzeugmotoren sind sowohl wasser- als auch luftgekühlt, da das wasser-/flüssigkeitsgekühlte Kühlmittel zu luftgekühlten Kühlrippen und/oder Lüftern geleitet wird, während größere Motoren ausschließlich wassergekühlt sein können, da sie stationär sind und über Wasserleitungen oder Frischwasser eine konstante Wasserversorgung haben, während die meisten Motoren für Elektrowerkzeuge und andere kleine Motoren luftgekühlt sind. Einige Motoren (luft- oder wassergekühlt) haben auch einen Ölkühler. Bei einigen Triebwerken, insbesondere bei der Kühlung von Turbinenschaufeln und Flüssigkeitsraketen, wird der Kraftstoff als Kühlmittel verwendet, da er gleichzeitig vorgewärmt wird, bevor er in die Brennkammer eingespritzt wird. ⓘ
Starten
Verbrennungsmotoren müssen angelassen werden. Bei Hubkolbenmotoren geschieht dies durch die Drehung der Kurbelwelle (Wankelrotorwelle), die die Zyklen von Ansaugung, Verdichtung, Verbrennung und Auspuff in Gang setzt. Die ersten Motoren wurden durch Drehen des Schwungrads gestartet, während das erste Fahrzeug (der Daimler-Reitwagen) mit einer Handkurbel gestartet wurde. Alle Automobile mit Verbrennungsmotor wurden mit Handkurbeln gestartet, bis Charles Kettering den elektrischen Anlasser für Automobile entwickelte. Diese Methode ist heute die am weitesten verbreitete, auch bei Nicht-Automobilen. ⓘ
Da die Dieselmotoren immer größer und ihre Mechanismen immer schwerer wurden, kamen Luftstarter zum Einsatz. Der Grund dafür ist das mangelnde Drehmoment der elektrischen Anlasser. Bei Druckluftanlassern wird Druckluft in die Zylinder eines Motors gepumpt, um ihn in Gang zu setzen. ⓘ
Bei zweirädrigen Fahrzeugen kann der Motor auf eine von vier Arten gestartet werden:
- Durch Treten der Pedale, wie bei einem Fahrrad
- durch Anschieben des Fahrzeugs und anschließendes Einkuppeln, was als "Anfahren und Anfahren" bezeichnet wird
- durch Treten eines einzelnen Pedals nach unten, bekannt als "Kickstarten".
- durch einen elektrischen Anlasser, wie bei Autos ⓘ
Es gibt auch Anlasser, bei denen eine Feder durch eine Kurbelbewegung zusammengedrückt und dann zum Anlassen eines Motors verwendet wird. ⓘ
Bei einigen kleinen Motoren kommt ein Seilzugmechanismus zum Einsatz, der als "Rücklaufstart" bezeichnet wird, da sich das Seil nach dem Herausziehen zum Anlassen des Motors selbst wieder aufrollt. Diese Methode wird häufig bei geschobenen Rasenmähern und anderen Anwendungen verwendet, bei denen nur ein geringes Drehmoment erforderlich ist, um einen Motor zu starten. ⓘ
Turbinenmotoren werden häufig durch einen Elektromotor oder durch Druckluft gestartet. ⓘ
Messungen der Motorleistung
Motortypen unterscheiden sich in vielerlei Hinsicht stark voneinander:
- Energiewirkungsgrad
- Kraftstoff-/Treibstoffverbrauch (bremsspezifischer Kraftstoffverbrauch bei Wellentriebwerken, schubspezifischer Kraftstoffverbrauch bei Strahltriebwerken)
- Verhältnis zwischen Leistung und Gewicht
- Verhältnis zwischen Schub und Gewicht
- Drehmomentkurven (bei Wellentriebwerken), Schubabfall (bei Strahltriebwerken)
- Verdichtungsverhältnis bei Kolbentriebwerken, Gesamtdruckverhältnis bei Strahltriebwerken und Gasturbinen ⓘ
Energiewirkungsgrad
Nach der Zündung und Verbrennung haben die Verbrennungsprodukte - heiße Gase - mehr verfügbare Wärmeenergie als das ursprüngliche komprimierte Kraftstoff-Luft-Gemisch (das eine höhere chemische Energie hatte). Diese verfügbare Energie äußert sich in einer höheren Temperatur und einem höheren Druck, die vom Motor in kinetische Energie umgewandelt werden können. In einem Hubkolbenmotor treiben die unter hohem Druck stehenden Gase in den Zylindern die Kolben des Motors an. ⓘ
Sobald die verfügbare Energie verbraucht ist, werden die verbleibenden heißen Gase abgelassen (häufig durch Öffnen eines Ventils oder Freilegen des Auspuffauslasses), wodurch der Kolben in seine vorherige Position (oberer Totpunkt) zurückkehren kann. Der Kolben kann dann in die nächste Phase seines Zyklus übergehen, die von Motor zu Motor unterschiedlich ist. Jede Wärmeenergie, die nicht in Arbeit umgewandelt wird, gilt normalerweise als Abfallprodukt und wird entweder durch ein Luft- oder Flüssigkeitskühlsystem aus dem Motor entfernt. ⓘ
Verbrennungsmotoren gelten als Wärmekraftmaschinen (da die Freisetzung chemischer Energie bei der Verbrennung dieselbe Wirkung hat wie die Wärmeübertragung in den Motor), und als solche kann ihr theoretischer Wirkungsgrad durch idealisierte thermodynamische Zyklen angenähert werden. Der thermische Wirkungsgrad eines theoretischen Zyklus kann nicht höher sein als der des Carnot-Zyklus, dessen Wirkungsgrad durch die Differenz zwischen der unteren und der oberen Betriebstemperatur des Motors bestimmt wird. Die obere Betriebstemperatur eines Motors wird durch zwei Hauptfaktoren begrenzt: die thermischen Betriebsgrenzen der Werkstoffe und die Selbstentzündungsfestigkeit des Kraftstoffs. Alle Metalle und Legierungen haben eine thermische Betriebsgrenze, und es wird intensiv an keramischen Werkstoffen geforscht, die eine höhere thermische Stabilität und wünschenswerte strukturelle Eigenschaften aufweisen. Eine höhere thermische Stabilität ermöglicht eine größere Temperaturdifferenz zwischen der unteren (Umgebungs-) und der oberen Betriebstemperatur und damit einen höheren thermodynamischen Wirkungsgrad. Außerdem steigt mit zunehmender Zylindertemperatur die Neigung des Kraftstoffs zur Selbstzündung. Dies ist der Fall, wenn sich die Zylindertemperatur dem Flammpunkt der Ladung nähert. An diesem Punkt kann es zu einer Selbstzündung kommen, bevor die Zündkerze zündet, was zu einem übermäßigen Zylinderdruck führt. Die Selbstentzündung kann durch die Verwendung von Kraftstoffen mit hoher Selbstentzündungsfestigkeit (Oktanzahl) gemildert werden, setzt aber dennoch eine Obergrenze für die zulässige Zylinderspitzentemperatur. ⓘ
Bei den thermodynamischen Grenzwerten wird davon ausgegangen, dass der Motor unter idealen Bedingungen betrieben wird: eine Welt ohne Reibung, ideale Gase, perfekte Isolatoren und Betrieb über unendlich lange Zeit. Anwendungen in der realen Welt führen zu Komplexitäten, die die Effizienz verringern. Ein echter Motor läuft beispielsweise bei einer bestimmten Last, dem so genannten Leistungsbereich, am besten. Der Motor eines Autos, das auf der Autobahn unterwegs ist, läuft in der Regel deutlich unter seiner idealen Last, da er für die höheren Lasten ausgelegt ist, die für eine schnelle Beschleunigung erforderlich sind. Darüber hinaus verringern Faktoren wie der Windwiderstand die Gesamteffizienz des Systems. Der Kraftstoffverbrauch eines Motors wird in Meilen pro Gallone oder in Litern pro 100 Kilometer gemessen. Das Volumen des Kohlenwasserstoffs geht von einem Standard-Energiegehalt aus. ⓘ
Selbst mit Hilfe von Turboladern und serienmäßigen Effizienzhilfen haben die meisten Motoren einen durchschnittlichen Wirkungsgrad von etwa 18-20 %. Mit den neuesten Technologien für Formel-1-Motoren konnte der thermische Wirkungsgrad jedoch auf über 50 % gesteigert werden. Es gibt viele Erfindungen, die darauf abzielen, den Wirkungsgrad von Verbrennungsmotoren zu erhöhen. Im Allgemeinen sind praktische Motoren immer mit Kompromissen zwischen verschiedenen Eigenschaften wie Wirkungsgrad, Gewicht, Leistung, Wärme, Ansprechverhalten, Abgasemissionen oder Lärm verbunden. Manchmal spielt auch die Wirtschaftlichkeit eine Rolle, nicht nur bei den Herstellungskosten des Motors selbst, sondern auch bei der Herstellung und Verteilung des Kraftstoffs. Eine Steigerung des Wirkungsgrads des Motors führt zu einem besseren Kraftstoffverbrauch, allerdings nur, wenn die Kraftstoffkosten pro Energiegehalt gleich bleiben. ⓘ
Messungen des Kraftstoffwirkungsgrads und des Wirkungsgrads des Treibstoffs
Bei stationären Motoren und Wellenmotoren, einschließlich Propellermotoren, wird der Kraftstoffverbrauch durch die Berechnung des bremsspezifischen Kraftstoffverbrauchs gemessen, der den Massendurchsatz des verbrauchten Kraftstoffs geteilt durch die erzeugte Leistung angibt. ⓘ
Bei Verbrennungsmotoren in Form von Düsentriebwerken schwankt die Leistungsabgabe drastisch mit der Fluggeschwindigkeit, und es wird ein weniger variables Maß verwendet: der schubspezifische Treibstoffverbrauch (TSFC), d. h. die Masse des Treibstoffs, die zur Erzeugung von Impulsen benötigt wird, die entweder in Pfund-Kraft-Stunden oder in Gramm Treibstoff gemessen werden, die zur Erzeugung eines Impulses von einer Kilonewton-Sekunde erforderlich sind. ⓘ
Für Raketen kann die TSFC verwendet werden, aber üblicherweise werden andere gleichwertige Maße verwendet, wie der spezifische Impuls und die effektive Ausstoßgeschwindigkeit. ⓘ
Luftverschmutzung und Lärm
Teil einer Serie über ⓘ |
Umweltverschmutzung |
---|
![]() |
|
Luftverschmutzung
Verbrennungsmotoren, wie z. B. Hubkolben-Verbrennungsmotoren, erzeugen aufgrund der unvollständigen Verbrennung von kohlenstoffhaltigem Kraftstoff Luftschadstoffemissionen. Die wichtigsten Folgeprodukte dieses Prozesses sind Kohlendioxid CO
2, Wasser und etwas Ruß - auch Feinstaub (PM) genannt. Die Auswirkungen des Einatmens von Feinstaub sind bei Menschen und Tieren untersucht worden und umfassen Asthma, Lungenkrebs, Herz-Kreislauf-Probleme und vorzeitigen Tod. Bei der Verbrennung entstehen jedoch noch weitere Produkte wie Stickoxide und Schwefel sowie einige unverbrannte Kohlenwasserstoffe, die von den Betriebsbedingungen und dem Kraftstoff-Luft-Verhältnis abhängen. ⓘ
Die Kohlendioxidemissionen von Verbrennungsmotoren tragen zum vom Menschen verursachten Klimawandel bei. Eine Steigerung der Kraftstoffeffizienz des Motors kann die Menge der CO
2-Emissionen verringern, da bei der Verbrennung von kohlenstoffhaltigen Kraftstoffen CO
2. Da die Entfernung von CO
2aus den Motorabgasen zu entfernen, ist nicht praktikabel, weshalb das Interesse an Alternativen steigt. Nachhaltige Kraftstoffe wie Biokraftstoffe, synthetische Kraftstoffe und batteriebetriebene Elektromotoren sind Beispiele dafür. ⓘ
Nicht der gesamte Kraftstoff wird durch den Verbrennungsprozess verbraucht. Nach der Verbrennung verbleibt eine kleine Menge Kraftstoff, von der ein Teil zu sauerstoffhaltigen Verbindungen wie Formaldehyd oder Acetaldehyd oder zu Kohlenwasserstoffen reagiert, die ursprünglich nicht im Kraftstoffgemisch enthalten waren. Eine unvollständige Verbrennung ist in der Regel darauf zurückzuführen, dass nicht genügend Sauerstoff vorhanden ist, um das perfekte stöchiometrische Verhältnis zu erreichen. Die Flamme wird durch die relativ kühlen Zylinderwände "gelöscht", wobei nicht umgesetzter Kraftstoff zurückbleibt, der mit dem Abgas ausgestoßen wird. Bei niedrigeren Drehzahlen wird das Quenchen häufig bei Dieselmotoren (Selbstzünder) beobachtet, die mit Erdgas betrieben werden. Das Quenchen verringert den Wirkungsgrad und erhöht das Klopfen, was manchmal zum Abwürgen des Motors führt. Eine unvollständige Verbrennung führt auch zur Bildung von Kohlenmonoxid (CO). Weitere freigesetzte Chemikalien sind Benzol und 1,3-Butadien, die ebenfalls gefährliche Luftschadstoffe darstellen. ⓘ
Eine Erhöhung der Luftmenge im Motor verringert die Emissionen unvollständiger Verbrennungsprodukte, fördert aber auch die Reaktion zwischen Sauerstoff und Stickstoff in der Luft, wodurch Stickoxide (NOx) entstehen. NOx ist sowohl für die Gesundheit von Pflanzen als auch von Tieren gefährlich und führt zur Bildung von Ozon (O3). Ozon wird nicht direkt emittiert, sondern ist ein sekundärer Luftschadstoff, der in der Atmosphäre durch die Reaktion von NOx und flüchtigen organischen Verbindungen in Gegenwart von Sonnenlicht entsteht. Bodennahes Ozon ist schädlich für die menschliche Gesundheit und die Umwelt. Obwohl es sich um dieselbe chemische Substanz handelt, darf das bodennahe Ozon nicht mit dem stratosphärischen Ozon oder der Ozonschicht verwechselt werden, die die Erde vor schädlichen ultravioletten Strahlen schützt. ⓘ
Kohlenstoffhaltige Kraftstoffe enthalten Schwefel und Verunreinigungen, die im Auspuff zu Schwefelmonoxiden (SO) und Schwefeldioxid (SO2) führen, die den sauren Regen begünstigen. ⓘ
In den Vereinigten Staaten werden Stickstoffoxide, Feinstaub, Kohlenmonoxid, Schwefeldioxid und Ozon als Kriterienschadstoffe im Rahmen des Clean Air Act bis zu einem Niveau reguliert, bei dem die menschliche Gesundheit und das Wohlbefinden geschützt sind. Andere Schadstoffe, wie Benzol und 1,3-Butadien, werden als gefährliche Luftschadstoffe reguliert, deren Emissionen je nach technologischen und praktischen Erwägungen so weit wie möglich gesenkt werden müssen. ⓘ
NOx, Kohlenmonoxid und andere Schadstoffe werden häufig durch Abgasrückführung, bei der ein Teil der Abgase in den Ansaugtrakt des Motors zurückgeführt wird, und durch Katalysatoren, die Abgasbestandteile in unschädliche Stoffe umwandeln, kontrolliert. ⓘ
Motoren für nicht straßengebundene Fahrzeuge
Die von vielen Ländern angewandten Emissionsnormen enthalten besondere Anforderungen für Motoren, die nicht für den Straßenverkehr bestimmt sind, d. h. für Geräte und Fahrzeuge, die nicht auf öffentlichen Straßen betrieben werden. Die Normen sind von denen für Straßenfahrzeuge getrennt. ⓘ
Lärmbelästigung
Verbrennungsmotoren tragen erheblich zur Lärmbelästigung bei. Der Pkw- und Lkw-Verkehr auf Autobahnen und Straßen verursacht ebenso Lärm wie der Flugverkehr durch Düsenlärm, insbesondere bei Flugzeugen mit Überschallgeschwindigkeit. Raketenmotoren verursachen den stärksten Lärm. ⓘ
Leerlauf
Verbrennungsmotoren verbrauchen auch im Leerlauf Kraftstoff und stoßen Schadstoffe aus, weshalb es wünschenswert ist, die Leerlaufzeiten auf ein Minimum zu beschränken. Viele Busunternehmen weisen ihre Fahrer an, den Motor abzuschalten, wenn der Bus an einer Haltestelle wartet. ⓘ
In England wurde mit der Road Traffic Vehicle Emissions Fixed Penalty Regulations 2002 (Statutory Instrument 2002 No. 1808) das Konzept des "stationary idling offence" eingeführt. Dies bedeutet, dass ein Fahrer "von einer befugten Person ... gegen Vorlage eines Nachweises seiner Befugnis aufgefordert werden kann, den Motor dieses Fahrzeugs abzustellen", und dass eine "Person, die dem nicht nachkommt ... sich einer Straftat schuldig macht und bei summarischer Verurteilung mit einer Geldstrafe von höchstens Stufe 3 der Standardskala belegt werden kann". Nur wenige lokale Behörden haben die Vorschriften umgesetzt, eine davon ist der Stadtrat von Oxford. ⓘ
In vielen europäischen Ländern wird der Leerlauf standardmäßig durch Stopp-Start-Systeme unterbunden. ⓘ
Bildung von Kohlendioxid
Die Masse des Kohlendioxids, die bei der Verbrennung von einem Liter Dieselkraftstoff (oder Benzin) freigesetzt wird, lässt sich wie folgt schätzen:
In guter Näherung lautet die chemische Formel von Diesel C
nH
2n. Beachten Sie, dass Diesel in Wirklichkeit ein Gemisch aus verschiedenen Molekülen ist. Da Kohlenstoff eine molare Masse von 12 g/mol und Wasserstoff (atomar) eine molare Masse von etwa 1 g/mol hat, beträgt der Gewichtsanteil von Kohlenstoff in Diesel ungefähr 12⁄14. ⓘ
Die Reaktion bei der Verbrennung von Diesel ist gegeben durch:
2C
nH
2n + 3nO
2 ⇌ 2nCO
2 + 2nH
2O ⓘ
Kohlendioxid hat eine molare Masse von 44 g/mol, da es aus 2 Sauerstoffatomen (16 g/mol) und 1 Kohlenstoffatom (12 g/mol) besteht. 12 g Kohlenstoff ergeben also 44 g Kohlendioxid. ⓘ
Diesel hat eine Dichte von 0,838 kg pro Liter. ⓘ
Die Masse des Kohlendioxids, die bei der Verbrennung von 1 Liter Diesel entsteht, lässt sich also wie folgt berechnen: ⓘ
Die mit dieser Schätzung erhaltene Zahl liegt nahe an den in der Literatur gefundenen Werten. ⓘ
Für Benzin mit einer Dichte von 0,75 kg/L und einem Verhältnis von Kohlenstoff- zu Wasserstoffatomen von etwa 6 zu 14 beträgt der geschätzte Wert der Kohlenstoffemission bei der Verbrennung von 1 Liter Benzin: ⓘ
Votum des Europaparlaments zum Ende des Verbrennungsmotos in Kraftfahrzeugen im Jahr 2035
Am 8. Juni 2022 beschloss das EU-Parlament auf Vorschlag der EU-Kommission, dass ab 2035 in der Europäischen Union nur noch emissionsfreie Autos zugelassen werden dürfen. Die Hersteller wurden verpflichtet, ihre Flottenemissionen um 100 Prozent reduzieren. Das Europaparlament nahm den Vorschlag der EU-Kommission mit 339 Ja- zu 249 Neinstimmen bei 24 Enthaltungen an. Bei der Abstimmung stimmten die europäischen Konservativen (inkl. CDU/CSU) und Rechten (inkl. AfD) gegen den Beschluss. Die Fraktion der konservativen Europäischen Volkspartei (EVP) hatte zuvor vergeblich versucht, einen Kompromiss durchzusetzen, nachdem auch Fahrzeuge mit Hybridantrieb oder mit synthetischen Kraftstoffen betriebene Verbrennungsmotoren erlaubt gewesen wären. Die Grüne Fraktion im Europaparlament war mit ihrem Vorschlag eines Verbots von Verbrennungsmotoren schon im Jahr 2030 ebenfalls nicht durchgedrungen. ⓘ
Bezeichnungen
Der Allgemeine Deutsche Sprachverein unternahm in der ersten Hälfte des 20. Jahrhunderts Versuche das zusammengesetzte Fremdwort Explosionsmotor einzudeutschen. Aus „Explosion“ wurde „Zerknall“ (wie heute noch in „Kesselzerknall“) und aus „Motor“ wurde unter anderem „Treiber“. So lautete die Vorgeschlagene deutsche Bezeichnung für einen Verbrennungsmotor „Zerknalltreibling“ die sich heute nur noch als scherzhafte Bezeichnung erhalten hat. ⓘ
Einteilung
In der Geschichte des Motorenbaus sind viele Konzepte erdacht und realisiert worden, die nicht unbedingt in das folgende Raster passen, zum Beispiel Ottomotoren mit Direkteinspritzung oder Vielstoffmotoren. Zugunsten der Übersichtlichkeit werden diese Sonderfälle hier nicht betrachtet. ⓘ
Dazu gehören der Wankelmotor (Ottomotor mit Rotationskolben und Schlitzsteuerung) oder Schiffsdieselmotoren, die oft als Zweitakt-Dieselmotor mit Auslassventilen konzipiert sind. ⓘ
Nach dem Gemischbildungsverfahren


Ottomotoren arbeiten in der Regel mit ungefähr konstantem Verbrennungsluftverhältnis, das heißt pro eine Masseeinheit Kraftstoff werden 13 bis 15 Masseeinheiten Luft hinzugemischt. Zur Verbrennung von 1 kg Benzin werden 14,5 kg Luft benötigt; ein solches Kraftstoff-Luft-Gemisch wird als stöchiometrisch (Luftzahl ) bezeichnet. Ist mehr Luft als nötig im Brennraum, so ist das Gemisch überstöchiometrisch, mager (), ist zu wenig Luft im Brennraum, so ist das Gemisch unterstöchiometrisch, fett (). Um die Abgase in einem Katalysator mit maximaler Wirkung zu entgiften, ist eine Luftzahl von 1 erforderlich. Dieselmotoren arbeiten mit variabler Luftzahl, etwa von 10 bis 1,3. ⓘ
Die Gemischbildung kann sowohl innerhalb, als auch außerhalb des Brennraums stattfinden, wobei der bedeutendste Selbstzündermotor, der Dieselmotor, nur mit Gemischbildung innerhalb des Brennraumes funktioniert. ⓘ
- Äußere Gemischbildung
- Es wird ein zündfähiges Gasgemisch über den Ansaugtrakt in den Zylinder geführt und dort verdichtet. Das ermöglicht hohe Drehzahlen, da es ohne Verzögerung verbrennt, sobald gezündet wird. Durch überhöhte Temperatur (heißer Motor, hohe Verdichtung bei Volllast) kann es zu unkontrollierter Selbstzündung kommen. Dieser Klopfen genannte Effekt begrenzt das Verdichtungsverhältnis. Die Klopffestigkeit eines Kraftstoffs wird mit der Oktanzahl angegeben und kann durch den Zusatz von Antiklopfmitteln verringert werden. Nach der Zündung kann die Verbrennung gewöhnlich nicht mehr beeinflusst werden. Die äußere Gemischbildung kann auf zwei Arten erfolgen:
- Vergaser zerstäuben das Benzin in feine Tröpfchen und bilden so ein Aerosol, das in die Zylinder geführt wird. Bis in die 1990er Jahre waren sie im Automobilbau üblich und werden heute fast nur noch in Kleinmotoren eingesetzt.
- Bei der indirekten Benzineinspritzung, der Saugrohreinspritzung, wird der Kraftstoff mit vergleichsweise geringem Druck im Ansaugtrakt kurz vor dem/den Einlassventil(en) dem Luftstrom beigemengt. Vorteile gegenüber dem Vergaser sind unter anderem die schnellere und präzisere Steuerung der Kraftstoffmenge und die Lageunabhängigkeit (wichtig zum Beispiel bei Flugmotoren).
- Innere Gemischbildung, Direkteinspritzung
- Vom Zylinder wird nur Luft angesaugt und verdichtet. Erst unmittelbar vor der Verbrennung wird mit hohem Druck der Kraftstoff direkt in den Brennraum eingespritzt, weshalb der Wirkungsgrad durch höhere Verdichtung gesteigert werden kann. Nach Einspritzbeginn benötigt der Kraftstoff Zeit zum Verdampfen und Durchmischen mit der Luft. Die Verbrennung beginnt verzögert und begrenzt so die maximale Motordrehzahl. ⓘ
Nach dem Zündverfahren
- Fremdzündung, entweder gesteuert oder ungesteuert als Glühzündung
- Selbstzündung bzw. homogene Kompressionszündung (HCCI) ⓘ
Die Fremdzündung ist Merkmal verschiedener Motoren, unter anderem des Ottomotors. Dabei wird das Entzünden des Kraftstoffluftgemisches durch eine Zündhilfe eingeleitet, in der Regel kurz vor dem oberen Totpunkt. Ottomotoren haben dafür Zündkerzen. Gibt es keine Zündkerze und ist die Fremdzündung unkontrolliert, so spricht man von Glühzündung. Die ersten Motoren von Gottlieb Daimler arbeiteten mit Glühzündung. Ein früher verbreiteter Glühzündermotor ist der Glühkopfmotor, nach seinem Erfinder auch Akroydmotor genannt. In Deutschland ist er insbesondere aus Ackerschleppern der Marke Lanz Bulldog bekannt, in Skandinavien als Motor von Fischerbooten, unter anderem von Bolinders. Bei diesen Motoren muss vor dem Start ein Glühkopf genannter Teil des Zylinderkopfs erhitzt werden, etwa mit einer Lötlampe, ehe die Zündung einsetzen kann. In den Glühkopf wird der Treibstoff während des Verdichtungstaktes eingespritzt. Heute werden Glühzündermotoren (die allerdings nicht nach dem Akroydverfahren arbeiten) vorwiegend im Modellbau verwendet. Beim Ottomotor können in seltenen Fällen Glühzündungen nach dem Abstellen des Motors vorkommen, sie wirken sich aber schädlich auf das Triebwerk aus und sind daher unerwünscht. ⓘ
Die Selbstzündung ist Merkmal verschiedener Motoren, bekanntester Selbstzünder ist der Dieselmotor. Bei einem Selbstzündermotor werden keine Zündhilfen eingesetzt, die Zündung wird stattdessen ausschließlich durch Kompressionswärme eingeleitet. Die Arbeitsweise der Selbstzündermotoren ist von ihrem Funktionsprinzip abhängig: bei einem Dieselmotor wird zuerst reine Luft stark verdichtet und dadurch erhitzt. Kurz vor dem oberen Totpunkt (OT) wird der Dieselkraftstoff eingespritzt, der sich durch die Hitze von selbst entzündet. Da sich der Kraftstoff im Dieselmotor aufgrund der späten Einspritzung entzündet, bevor sich ein homogenes Gemisch bilden kann, spricht man beim Dieselmotor von heterogenem Gemisch. Bei sogenannten HCCI-Motoren wird hingegen ein homogenes Gemisch gebildet, das sich nur durch die Kompressionswärme entzünden soll. Anders als beim Dieselmotor muss daher die Einspritzung des Kraftstoffes früh erfolgen, damit das Gemisch bis zur Zündung gut durchmischt (homogen) ist. Dadurch werden bessere Emissionswerte erreicht. Einige Modellbaumotoren arbeiten ebenfalls mit homogener Kompressionszündung, das Gemisch wird hier mit einem Vergaser gebildet, das Verdichtungsverhältnis kann mit einer Schraube verstellt werden. ⓘ
Nach dem Brennverfahren
Mit Brennverfahren bzw. Verbrennungsverfahren bezeichnet man bei Verbrennungsmotoren den Ablauf, in dem der Treibstoff im Motor verbrennt. ⓘ
- die Schichtladung (Ottomotor)
- das BPI-Brennverfahren (mit Vorkammerzündkerze; Ottomotor)
- das Strahlgeführtes Brennverfahren (Ottomotor) ⓘ
Nach der Füllungsart

- Saugmotor
- Ladermotor ⓘ
Nach dem Kühlverfahren
- Flüssigkeitskühlung
- Verdampfungskühlung
- Luftkühlung
- Ölkühlung
- Kombinationen aus Luft-/Ölkühlung (SAME)
- Stickstoffkühlung ⓘ
Nach dem Grad der Schnellläufigkeit
In früheren Jahren wurde der Grad der Schnellläufigkeit aufgrund der Kolbengeschwindigkeit, später vermehrt durch die Drehzahl bestimmt. Bei Großmotoren (Schiffe, Bahn, Stromerzeuger) unterscheidet man drei Klassen:
- Langsamläufer bis 300/min, die im Zweitaktverfahren arbeiten und für Schweröl tauglich sind
- Mittelschnellläufer zwischen 300 und 1200/min, die überwiegend schweröltaugliche Viertaktmotoren sind
- Schnellläufer ab 1000/min als Viertakter, die für Schweröl nicht mehr geeignet sind. ⓘ
Nach weiteren Definitionen gibt es
- Mittelläufer bis 2000/min für Boots- und Binnenschiffsmotoren, Hilfsaggregate und ähnliches
- Schnellläufer über 2000/min als Otto- und Dieselmotoren für Fahrzeuge ⓘ
- Nach Schrön
Hans Schrön unterscheidet im 1942 erschienenen Werk Die Verbrennungskraftmaschine zwischen drei verschiedenen Typen, den Langsamläufern, den Mittelläufern und den Schnellläufern. Als Unterscheidungsmerkmal zieht Schrön die Kolbengeschwindigkeit heran. Den Umstand, dass noch nicht alle Motoren als Schnellläufer konstruiert sind, sieht er in Punkten, die bei der Konzeption eine wichtigere Rolle als hohe Drehzahlen spielen. Die Langsamläufer und Mittelläufer sollen möglichst eine hohe Lebensdauer und Störungsfreiheit haben, dazu zählen Stationärmotoren und Schiffsmotoren. Bei Schiffsmotoren weist Schrön ebenfalls auf den Vorteil des hohen Wirkungsgrades hin. Weitere Mittelläufer sind unter anderem Triebwagen-, Lastkraftwagen-, Traktoren- und Kampffahrzeugmotoren. Schnellläufer sollen eine niedrige Masse, wenig Volumen und gute Einbaufähigkeiten haben, gegebenenfalls spielt die größtmögliche Leistung noch eine Rolle. Als Anwendungsbereich kommen Schnellboote, Flugzeuge und Leichtfahrzeuge in Betracht. Schnellläufer können sowohl Diesel- als auch Ottomotoren sein. ⓘ
- Dieselmotoren nach Mau ⓘ
Günter Mau unterscheidet den Grad der Schnellläufigkeit bei Dieselmotoren wie folgt:
- Langsamläufer: bis rund 300 min−1
- Mittelschnellläufer: kleiner 1000 min−1
- Schnellläufer: größer gleich 1000 min−1 ⓘ
Partikelemission durch die Verbrennung
Partikel im Abgas von Verbrennungsmotoren (10–1000 nm) sind kleiner als andere, etwa durch Reifenabrieb (15.000 nm) verursachte. Wie jene bestehen sie aber aus Ruß und Kohlenwasserstoffen (zum Beispiel PAK). Ihre für den Menschen vermutete Gesundheitsrelevanz erhalten die Abgasnanopartikel aufgrund ihrer Oberfläche und Größe. Sie können Zellmembranen verletzen (Ruß) oder mit ihnen reagieren (PAK). Durch ihre Größe (als Nanopartikel bezeichnet man alles unter 100 nm) gelingt ihnen die Überwindung der oberen Atemwege und der Lungenwand und damit der Eintritt in den Blutkreislauf (vgl.). Dosis, Einwirkzeit, Projizierbarkeit von Tierversuchen auf den Menschen und Begleitumstände wie das Rauchen von Studienteilnehmern bilden die Zielsetzungen derzeitiger Forschung. Dem vorgreifend begrenzt die Euro 6 Abgasnorm für 2014 erstmals die Partikelmenge (Entwurfswert: 6×1011 Stück pro km) und nicht mehr nur ihre Masse. Die Masse wird durch die entscheidenden Nanopartikel nur zu 20 % beeinflusst, beim Diesel die Gesamtmasse aber durch geschlossene Partikelfilter bereits um 97 % reduziert. Das zeigt, dass die dortige Ansammlung von Filtrat auch relevante Mengen von Nanopartikeln weit unter der eigentlichen Filterporengröße von 1000 nm abfängt. Mit dieser Reduktion minimiert der Filter zudem die Klimawirksamkeit der Partikel. Die dunkle Rußfarbe macht die Partikel zu Wärmeabsorbern. Damit erwärmen sie direkt die rußbelastete Luft und nach Ablagerung auch Schneeflächen in der Arktis, die sie durch Luftströmungen etwa von Europa her erreichen. ⓘ
Benzin- und Dieselmotoren produzieren während Volllast- und Kaltstartphasen vergleichbare Mengen und Größen an Partikeln. In beiden Phasen wird mehr Kraftstoff eingespritzt, als der Sauerstoff im Zylinder verbrennen kann („angefettetes Gemisch“). In Kaltstartphasen geschieht dies zur Katalysatorerwärmung, unter Volllast zur Motorkühlung. Während Benzinmotoren nur im angefetteten Betrieb Partikel durch Sauerstoffmangel erzeugen, entstehen diese beim Diesel selbst im Magerbetrieb und damit während aller Betriebsphasen. Daher liegt die Partikelmenge des Benziners insgesamt dennoch auf dem niedrigen Niveau eines Diesels mit geschlossenem Filtersystem. ⓘ
Ursächlich für den Dieselruß sind seine doppelt so langkettigen Aromate (vgl. Benzin). Sie weisen einen deutlich höheren Siedepunkt auf (von 170 bis 390 °C anstatt 25 bis 210 °C). Gleichzeitig liegt die Verbrennungstemperatur des Diesels aber 500 °C unterhalb der des Benzinmotors. Benzin verdampft daher vollständiger als Diesel. Dessen früher siedende Bestandteile verdampfen zuerst, was den Resttropfen aus Aromaten höherer Siedepunkte zusätzlich auf niederer Temperatur hält (vgl.). Die nicht verdampften Aromate werden während der Selbstzündungsphase temperaturbedingt in ihre Bestandteile gecrackt. Zu diesen zählt der Kohlenstoff, also Ruß. ⓘ
Die Partikelzusammensetzung unterscheidet sich aufgrund der Chemie beider Kraftstoffe. So überwiegen beim Benzinmotor die PAK-Partikel, beim Dieselmotor sind es die Rußpartikel. Sichtbar werden die Partikel erst durch Aneinanderlagerung. Sichtbare Partikel sind nicht mehr lungengängig und werden meist schon im oberen Atemweg ausgefiltert und abgebaut. Anlagerungen finden im Auspuff und besonders im Partikelfilter statt. Die dortige Ansammlung des Filtrats fängt auch Partikel weit unter der eigentlichen Filterporengröße (1 µm) ab. Damit sinkt die Partikelanzahl auf das Niveau eines Benzinmotors. Erkennbar wird die Partikelanlagerung im Auspuff. Fehlt diese, verfügt ein Diesel über ein geschlossenes Filtersystem und ein Benziner über wenige Anteile von Kaltstart- und Volllastphasen. ⓘ
Wichtige Motorenbauer
- Carl Benz
- Georges Bouton
- George Brayton
- Edward N. Cole
- Clessie Cummins
- Gottlieb Daimler
- Joseph Day
- Philippe Lebon d'Humbersin
- Rudolf Diesel
- Ludwig Elsbett
- Hugo Junkers
- Frederick W. Lanchester
- Eugen Langen
- Étienne Lenoir
- Frank Perkins (Ingenieur)
- Siegfried Marcus
- Wilhelm Maybach
- Nicolaus Otto
- Harry Ricardo
- Isaac de Rivaz
- Robert Stirling
- Felix Wankel ⓘ
Ausblick
Beim Einsatz von Kohlenstoffverbindungen als Kraftstoff emittieren Verbrennungsmotoren Kohlenstoffdioxid (CO2). Aufgrund der üblicherweise fossilen Herkunft dieser Kraftstoffe steigt damit die CO2-Konzentration in der Atmosphäre, was zur globalen Erwärmung beiträgt. Viele Länder fördern deshalb den Verkauf von Elektroautos und/oder von Hybridelektrokraftfahrzeugen (siehe auch Elektromobilitätsgesetz und Elektromobilität #Förderwürdigkeit). Eine zunehmende Zahl von Ländern plant, den Verkauf von Neuwagen mit Verbrennungsmotor ab einem bestimmten Stichtag zu verbieten. ⓘ
Im Juni 2022 beschloss das EU-Parlament, dass Neuwagen ab dem Jahr 2035 kein CO2 ausstoßen dürfen. ⓘ
Eine Alternative zu der Umstellung auf Elektromotoren, insbesondere für Bereiche, in denen diese schwierig umzusetzen ist, stellt der klimaneutrale Betrieb von Verbrennungsmotoren mit Kraftstoffen regenerativer Herkunft (z. B. Biokraftstoffe oder E-Fuels) dar. Auch dafür existieren Förderprogramme, beispielsweise in Deutschland. ⓘ