Epoxidharz

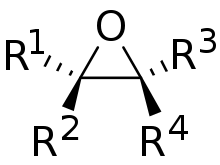
Epoxid ist die Familie der Grundbestandteile oder gehärteten Endprodukte von Epoxidharzen. Epoxidharze, die auch als Polyepoxide bezeichnet werden, sind eine Klasse von reaktiven Präpolymeren und Polymeren, die Epoxidgruppen enthalten. Die funktionelle Gruppe des Epoxids wird auch als Epoxid bezeichnet. Der IUPAC-Name für eine Epoxidgruppe ist Oxiran. ⓘ
Epoxidharze können entweder mit sich selbst durch katalytische Homopolymerisation oder mit einer Vielzahl von Reaktionspartnern wie polyfunktionellen Aminen, Säuren (und Säureanhydriden), Phenolen, Alkoholen und Thiolen (in der Regel als Mercaptane bezeichnet) umgesetzt (vernetzt) werden. Diese Reaktionspartner werden häufig als Härter oder Härtungsmittel bezeichnet, und die Vernetzungsreaktion wird allgemein als Härtung bezeichnet. ⓘ
Durch die Reaktion von Polyepoxiden mit sich selbst oder mit polyfunktionellen Härtern entsteht ein duroplastisches Polymer, das häufig günstige mechanische Eigenschaften und eine hohe thermische und chemische Beständigkeit aufweist. Epoxid hat ein breites Anwendungsspektrum, darunter Metallbeschichtungen, Verbundwerkstoffe, Verwendung in der Elektronik, elektrische Komponenten (z. B. für Chips auf Platinen), LEDs, elektrische Hochspannungsisolatoren, Herstellung von Pinseln, faserverstärkte Kunststoffe und Klebstoffe für strukturelle und andere Zwecke. ⓘ
Zu den Gesundheitsrisiken im Zusammenhang mit der Exposition gegenüber Epoxidharzverbindungen gehören Kontaktdermatitis und allergische Reaktionen sowie Atemprobleme durch das Einatmen von Dämpfen und Schleifstaub, insbesondere wenn diese nicht vollständig ausgehärtet sind. ⓘ

Als Epoxidharz oder abgekürzt EP-Harz bezeichnet man Kunstharze, die Epoxidgruppen tragen. Es handelt sich um Reaktionsharze, die nach Vermischung mit einem Härter zu einem duroplastischen Kunststoff reagieren. Der Härter ist dabei Reaktionspartner und bildet zusammen mit dem Harz einen makromolekularen Polyether mit in der Regel zwei endständigen Epoxidgruppen. Je nach Anwendung können Farb- und weitere Zusatzstoffe eingebunden werden. ⓘ
Nach der Aushärtung besitzen Epoxidharze gute mechanische Eigenschaften sowie eine gute Temperatur- und Chemikalienbeständigkeit und gelten als hochwertige, aber teure Kunststoffe. Sie werden u. a. als Reaktions- und Einbrennlacke, Klebstoffe, für Laminate, als Einbettmittel in der Metallographie und als Formmassen für Komponenten in der Elektrotechnik und Elektronik verwendet. ⓘ
Geschichte
Die Kondensation von Epoxiden und Aminen wurde erstmals von Paul Schlack aus Deutschland im Jahr 1934 gemeldet und patentiert. Die Entdeckung von Epoxidharzen auf Bisphenol-A-Basis wird unter anderem von Pierre Castan im Jahr 1943 behauptet. Castans Arbeit wurde von der Schweizer Ciba AG lizenziert, die später zu einem der drei größten Epoxidharzhersteller weltweit wurde. Das Epoxidharzgeschäft von Ciba wurde in den späten 1990er Jahren als Vantico ausgegliedert, das 2003 verkauft und in den Geschäftsbereich Advanced Materials der amerikanischen Huntsman Corporation überführt wurde. Im Jahr 1946 ließ Sylvan Greenlee, der für die Devoe & Raynolds Company arbeitete, ein Harz patentieren, das aus Bisphenol-A und Epichlorhydrin gewonnen wurde. Devoe & Raynolds, das in den Anfängen der Epoxidharzindustrie tätig war, wurde an Shell Chemical verkauft; die mit dieser Arbeit befasste Abteilung wurde schließlich veräußert und ist heute über eine Reihe weiterer Unternehmenstransaktionen Teil von Hexion Inc. ⓘ
Epoxide wurden zuerst von Paul Schlack in Wolfen (Patentanmeldung 1934, erteilt 1939) und Pierre Castan in der Schweiz (Patent-Anmeldung 1938 in der Schweiz, erteilt 1940, von der Ciba AG produziert) entwickelt. ⓘ
Chemie

Die meisten der kommerziell verwendeten Epoxidmonomere werden durch die Reaktion einer Verbindung mit sauren Hydroxygruppen und Epichlorhydrin hergestellt. Zunächst reagiert eine Hydroxygruppe in einer Kupplungsreaktion mit Epichlorhydrin, anschließend erfolgt eine Dehydrohalogenierung. Epoxidharze, die aus solchen Epoxidmonomeren hergestellt werden, nennt man Epoxidharze auf Glycidylbasis. Die Hydroxygruppe kann von aliphatischen Diolen, Polyolen (Polyetherpolyolen), Phenolverbindungen oder Dicarbonsäuren abgeleitet sein. Bei Phenolen kann es sich um Verbindungen wie Bisphenol A und Novolak handeln. Bei Polyolen kann es sich um Verbindungen wie 1,4-Butandiol handeln. Di- und Polyole führen zu Glycidylethern. Dicarbonsäuren wie Hexahydrophthalsäure werden für Diglycidesterharze verwendet. Anstelle einer Hydroxygruppe kann auch das Stickstoffatom eines Amins oder Amids mit Epichlorhydrin umgesetzt werden. ⓘ

Der andere Weg zur Herstellung von Epoxidharzen ist die Umsetzung von aliphatischen oder cycloaliphatischen Alkenen mit Persäuren: Im Gegensatz zu Epoxidharzen auf Glycidylbasis ist für die Herstellung solcher Epoxidmonomere kein saures Wasserstoffatom, sondern eine aliphatische Doppelbindung erforderlich. ⓘ
Die Epoxidgruppe wird manchmal auch als Oxirangruppe bezeichnet. ⓘ
Bisphenol-basierte
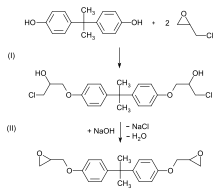
Die gebräuchlichsten Epoxidharze basieren auf der Reaktion von Epichlorhydrin (ECH) mit Bisphenol A, wodurch eine andere chemische Substanz entsteht, die als Bisphenol-A-Diglycidylether (allgemein bekannt als BADGE oder DGEBA) bezeichnet wird. Harze auf der Basis von Bisphenol A sind die am weitesten verbreiteten Harze, aber auch andere Bisphenole werden auf analoge Weise mit Epichlorhydrin umgesetzt, z. B. Bisphenol F. ⓘ
Bei dieser zweistufigen Reaktion wird zunächst Epichlorhydrin zu Bisphenol A gegeben (es entsteht Bis(3-chlor-2-hydroxy-propoxy)bisphenol A), dann wird in einer Kondensationsreaktion mit einer stöchiometrischen Menge Natriumhydroxid ein Bisepoxid gebildet. Das Chloratom wird als Natriumchlorid (NaCl) und das Wasserstoffatom als Wasser freigesetzt. ⓘ
Diglycidylether mit höherem Molekulargewicht (n ≥ 1) werden durch die Reaktion des gebildeten Bisphenol-A-Diglycidylethers mit weiterem Bisphenol A gebildet; dies wird als Präpolymerisation bezeichnet:

Ein Produkt mit wenigen sich wiederholenden Einheiten (n = 1 bis 2) ist eine zähflüssige, klare Flüssigkeit; dies wird als flüssiges Epoxidharz bezeichnet. Ein Produkt mit mehr wiederkehrenden Einheiten (n = 2 bis 30) ist bei Raumtemperatur ein farbloser Feststoff, der dementsprechend als festes Epoxidharz bezeichnet wird. ⓘ
Anstelle von Bisphenol A können auch andere Bisphenole (insbesondere Bisphenol F) oder bromierte Bisphenole (z. B. Tetrabrombisphenol A) für die genannte Epoxidierung und Präpolymerisation verwendet werden. Aus Bisphenol F können Epoxidharze in ähnlicher Weise wie aus Bisphenol A gebildet werden. Diese Harze haben in der Regel eine niedrigere Viskosität und einen höheren durchschnittlichen Epoxidgehalt pro Gramm als Bisphenol-A-Harze, was ihnen (nach dem Aushärten) eine höhere chemische Beständigkeit verleiht. ⓘ
Wichtige Epoxidharze werden durch Kombination von Epichlorhydrin und Bisphenol A zu Bisphenol-A-Diglycidylethern hergestellt. ⓘ

Erhöht man bei der Herstellung das Verhältnis von Bisphenol A zu Epichlorhydrin, so erhält man lineare Polyether mit Glycidyl-Endgruppen mit höherem Molekulargewicht, die je nach dem erreichten Molekulargewicht bei Raumtemperatur halbfest bis hartkristallin sind. Dieser Syntheseweg ist als "Taffy"-Verfahren bekannt. Der übliche Weg zu Epoxidharzen mit höherem Molekulargewicht besteht darin, mit flüssigem Epoxidharz (LER) zu beginnen und eine berechnete Menge Bisphenol A hinzuzufügen. Dann wird ein Katalysator hinzugefügt und die Reaktion auf ca. 160 °C (320 °F) erhitzt. Dieser Vorgang wird als "Weiterentwicklung" bezeichnet. Mit zunehmendem Molekulargewicht des Harzes nimmt der Epoxidgehalt ab, und das Material verhält sich mehr und mehr wie ein Thermoplast. Polykondensate mit sehr hohem Molekulargewicht (ca. 30.000-70.000 g/mol) bilden eine Klasse, die als Phenoxyharze bekannt ist und praktisch keine Epoxidgruppen enthält (da die endständigen Epoxidgruppen im Vergleich zur Gesamtgröße des Moleküls unbedeutend sind). Diese Harze enthalten jedoch im gesamten Gerüst Hydroxylgruppen, die auch andere Vernetzungsreaktionen eingehen können, z. B. mit Aminoplasten, Phenoplasten und Isocyanaten. ⓘ
Epoxidharze sind polymere oder semipolymere Werkstoffe oder ein Oligomer und liegen als solche selten in reiner Form vor, da die variable Kettenlänge aus der Polymerisationsreaktion resultiert, mit der sie hergestellt werden. Für bestimmte Anwendungen können hochreine Qualitäten hergestellt werden, z. B. durch ein Destillationsreinigungsverfahren. Ein Nachteil der hochreinen flüssigen Typen ist ihre Tendenz, aufgrund ihrer sehr regelmäßigen Struktur kristalline Feststoffe zu bilden, die dann zur Verarbeitung geschmolzen werden müssen. ⓘ
Ein wichtiges Kriterium für Epoxidharze ist der Epoxidwert, der mit dem Gehalt an Epoxidgruppen verbunden ist. Dieser wird als "Epoxid-Äquivalentgewicht" ausgedrückt, das das Verhältnis zwischen dem Molekulargewicht des Rorars und der Anzahl der Epoxidgruppen darstellt. Dieser Parameter wird verwendet, um die Masse des Reaktionspartners (Härters) zu berechnen, der beim Aushärten von Epoxidharzen verwendet werden muss. Epoxidharze werden in der Regel mit stöchiometrischen oder nahezu stöchiometrischen Mengen an Härter ausgehärtet, um die besten physikalischen Eigenschaften zu erzielen. ⓘ
Novolaks

Novolaken werden durch Reaktion von Phenol mit Methanal (Formaldehyd) hergestellt. Bei der Reaktion von Epichlorhydrin und Novolaken entstehen Novolaken mit Glycidylresten, wie Epoxyphenol-Novolak (EPN) oder Epoxycresol-Novolak (ECN). Diese hochviskosen bis festen Harze tragen in der Regel 2 bis 6 Epoxidgruppen pro Molekül. Bei der Aushärtung entstehen hoch vernetzte Polymere mit hoher Temperatur- und Chemikalienbeständigkeit, aber geringer mechanischer Flexibilität aufgrund der hohen Funktionalität und damit hohen Vernetzungsdichte dieser Harze. ⓘ
Aliphatische

Es gibt zwei gängige Arten von aliphatischen Epoxidharzen: solche, die durch Epoxidierung von Doppelbindungen gewonnen werden (cycloaliphatische Epoxide und epoxidierte Pflanzenöle) und solche, die durch Reaktion mit Epichlorhydrin entstehen (Glycidylether und -ester). ⓘ
Cycloaliphatische Epoxide enthalten einen oder mehrere aliphatische Ringe in dem Molekül, an dem der Oxiranring enthalten ist (z. B. 3,4-Epoxycyclohexylmethyl-3',4'-Epoxycyclohexancarboxylat). Sie werden durch die Reaktion eines cyclischen Alkens mit einer Persäure hergestellt (siehe oben). Cycloaliphatische Epoxide zeichnen sich durch ihre aliphatische Struktur, einen hohen Oxirangehalt und das Fehlen von Chlor aus, was zu einer niedrigen Viskosität und (nach der Aushärtung) zu einer guten Witterungsbeständigkeit, niedrigen Dielektrizitätskonstanten und einer hohen Tg führt. Allerdings polymerisieren aliphatische Epoxidharze bei Raumtemperatur sehr langsam, so dass in der Regel höhere Temperaturen und geeignete Beschleuniger erforderlich sind. Da aliphatische Epoxidharze eine geringere Elektronendichte als aromatische haben, reagieren cycloaliphatische Epoxidharze weniger leicht mit Nukleophilen als Epoxidharze auf Bisphenol A-Basis (die aromatische Ethergruppen haben). Dies bedeutet, dass herkömmliche nukleophile Härter wie Amine kaum zur Vernetzung geeignet sind. Cycloaliphatische Epoxide werden daher in der Regel thermisch oder UV-initiiert in einer elektrophilen oder kationischen Reaktion homopolymerisiert. Aufgrund der niedrigen Dielektrizitätskonstanten und der Abwesenheit von Chlor werden cycloaliphatische Epoxide häufig zur Verkapselung von elektronischen Systemen wie Mikrochips oder LEDs verwendet. Sie werden auch für strahlenhärtende Farben und Lacke verwendet. Aufgrund ihres hohen Preises ist ihr Einsatz jedoch bisher auf diese Anwendungen beschränkt. ⓘ
Epoxidierte Pflanzenöle entstehen durch Epoxidierung von ungesättigten Fettsäuren durch Reaktion mit Persäuren. In diesem Fall können die Persäuren auch in situ durch Reaktion von Carbonsäuren mit Wasserstoffperoxid gebildet werden. Im Vergleich zu LER (flüssige Epoxidharze) haben sie eine sehr geringe Viskosität. Werden sie jedoch in größeren Anteilen als Reaktivverdünner eingesetzt, führt dies häufig zu einer geringeren chemischen und thermischen Beständigkeit und zu schlechteren mechanischen Eigenschaften der gehärteten Epoxide. Epoxidierte Pflanzenöle wie epoxidierte Soja- und Linsenöle werden in großem Umfang als sekundäre Weichmacher und Kostenstabilisatoren für PVC eingesetzt. ⓘ
Aliphatische Glycidylepoxidharze mit niedriger Molmasse (mono-, bi- oder polyfunktional) werden durch die Reaktion von Epichlorhydrin mit aliphatischen Alkoholen oder Polyolen (es entstehen Glycidylether) oder mit aliphatischen Carbonsäuren (es entstehen Glycidylester) gebildet. Die Reaktion wird in Gegenwart einer Base wie Natriumhydroxid durchgeführt, analog zur Bildung von Bisphenol-A-Diglycidylether. Auch aliphatische Glycidylepoxidharze haben in der Regel eine niedrige Viskosität im Vergleich zu aromatischen Epoxidharzen. Sie werden daher anderen Epoxidharzen als Reaktivverdünner oder als Haftvermittler zugesetzt. Epoxidharze aus (langkettigen) Polyolen werden auch zur Verbesserung der Zugfestigkeit und Schlagzähigkeit zugesetzt. ⓘ
Eine verwandte Klasse sind cycloaliphatische Epoxidharze, die einen oder mehrere cycloaliphatische Ringe im Molekül enthalten (z. B. 3,4-Epoxycyclohexylmethyl-3,4-Epoxycyclohexancarboxylat). Diese Klasse weist ebenfalls eine geringere Viskosität bei Raumtemperatur auf, bietet aber eine deutlich höhere Temperaturbeständigkeit als die aliphatischen Epoxidverdünner. Allerdings ist die Reaktivität im Vergleich zu anderen Epoxidharzklassen eher gering, und normalerweise ist eine Aushärtung bei hohen Temperaturen unter Verwendung geeigneter Beschleuniger erforderlich. Da diese Materialien nicht wie Bisphenol A- und F-Harze aromatisch sind, ist die UV-Stabilität erheblich verbessert. ⓘ
Halogenierte Epoxidharze
Halogenierte Epoxidharze werden für besondere Eigenschaften beigemischt, insbesondere werden bromierte und fluorierte Epoxidharze verwendet. ⓘ
Bromiertes Bisphenol A wird verwendet, wenn flammhemmende Eigenschaften erforderlich sind, wie z. B. bei einigen elektrischen Anwendungen (z. B. Leiterplatten). Das tetrabromierte Bisphenol A (TBBPA, 2,2-Bis(3,5-dibromphenyl)propan) oder sein Diglycidylether, 2,2-Bis[3,5-dibrom-4-(2,3-epoxypropoxy)phenyl]propan, kann der Epoxidformulierung zugesetzt werden. Die Formulierung kann dann auf die gleiche Weise wie reines Bisphenol A umgesetzt werden. Einige (nicht vernetzte) Epoxidharze mit sehr hoher Molmasse werden technischen Thermoplasten zugesetzt, wiederum um flammhemmende Eigenschaften zu erzielen. ⓘ
Fluorierte Epoxidharze wurden für einige Hochleistungsanwendungen untersucht, wie z. B. der fluorierte Diglycidether 5-Heptafluorpropyl-1,3-bis[2-(2,3-epoxypropoxy)hexafluor-2-propyl]benzol. Da es eine niedrige Oberflächenspannung hat, wird es als Netzmittel (Tensid) für den Kontakt mit Glasfasern zugesetzt. Seine Reaktivität gegenüber Härtern ist mit der von Bisphenol A vergleichbar. Nach der Aushärtung ergibt das Epoxidharz einen duroplastischen Kunststoff mit hoher chemischer Beständigkeit und geringer Wasseraufnahme. Die kommerzielle Verwendung von fluorierten Epoxidharzen ist jedoch durch ihre hohen Kosten und ihre niedrige Tg begrenzt. ⓘ
Verdünnungsmittel
Epoxidharz-Verdünnungsmittel werden in der Regel durch Glycidylierung aliphatischer Alkohole oder Polyole und auch aromatischer Alkohole hergestellt. Die resultierenden Materialien können monofunktionell (z. B. Dodecanolglycidylether), difunktionell (1,4-Butandioldiglycidylether) oder höherfunktionell (z. B. Trimethylolpropantriglycidylether) sein. Diese Harze haben in der Regel eine niedrige Viskosität bei Raumtemperatur (10-200 mPa.s) und werden oft als Reaktivverdünner bezeichnet. Sie werden selten allein verwendet, sondern eher zur Modifizierung (Verringerung) der Viskosität anderer Epoxidharze eingesetzt. Dies hat zu dem Begriff "modifiziertes Epoxidharz" geführt, um diejenigen zu bezeichnen, die viskositätssenkende Reaktivverdünner enthalten. Die mechanischen Eigenschaften von Epoxidharzen werden durch die Verwendung von Verdünnungsmitteln im Allgemeinen nicht verbessert. Es sind auch biobasierte Epoxidverdünner erhältlich. ⓘ
Glycidylamin
Glycidylamin-Epoxidharze sind Epoxidharze mit höherer Funktionalität, die durch die Reaktion von aromatischen Aminen mit Epichlorhydrin entstehen. Wichtige Industriequalitäten sind Triglycidyl-p-aminophenol (Funktionalität 3) und N,N,N′,N′-Tetraglycidyl-bis-(4-aminophenyl)-methan (Funktionalität 4). Die Harze weisen bei Raumtemperatur eine niedrige bis mittlere Viskosität auf, wodurch sie leichter zu verarbeiten sind als EPN- oder ECN-Harze. Dies und die hohe Reaktivität sowie die hohe Temperaturbeständigkeit und die mechanischen Eigenschaften des resultierenden gehärteten Netzwerks machen sie zu wichtigen Materialien für Verbundwerkstoffanwendungen in der Luft- und Raumfahrt. ⓘ
Aushärtung
Es gibt mehrere Dutzend Chemikalien, die zum Aushärten von Epoxidharz verwendet werden können, darunter Amine, Imidazole, Anhydride und lichtempfindliche Chemikalien. ⓘ
Im Allgemeinen haben ungehärtete Epoxidharze nur schlechte mechanische, chemische und hitzebeständige Eigenschaften. Gute Eigenschaften werden jedoch durch die Reaktion des linearen Epoxidharzes mit geeigneten Härtungsmitteln erzielt, um dreidimensionale vernetzte duroplastische Strukturen zu bilden. Dieser Prozess wird gemeinhin als Aushärtung oder Gelierung bezeichnet. Die Aushärtung von Epoxidharzen ist eine exotherme Reaktion und erzeugt in einigen Fällen so viel Wärme, dass es zu einem thermischen Abbau kommt, wenn er nicht kontrolliert wird. ⓘ
Die Aushärtung kann durch die Reaktion eines Epoxidharzes mit sich selbst (Homopolymerisation) oder durch die Bildung eines Copolymers mit polyfunktionellen Härtungsmitteln oder Härtern erfolgen. Durch diese Aushärtung werden die Eigenschaften des Stoffes wie Beständigkeit, Haltbarkeit, Vielseitigkeit und Haftung erzielt. Im Prinzip kann jedes Molekül, das einen reaktiven Wasserstoff enthält, mit den Epoxidgruppen des Epoxidharzes reagieren. Zu den gängigen Klassen von Härtern für Epoxidharze gehören Amine, Säuren, Säureanhydride, Phenole, Alkohole und Thiole. Die relative Reaktivität (die niedrigste zuerst) ist ungefähr in der Reihenfolge: Phenol < Anhydrid < aromatisches Amin < cycloaliphatisches Amin < aliphatisches Amin < Thiol. ⓘ
Während einige Epoxidharz/Härter-Kombinationen bei Raumtemperatur aushärten, benötigen viele Wärme, wobei Temperaturen bis zu 150 °C (302 °F) üblich sind, und bis zu 200 °C (392 °F) für einige Spezialsysteme. Eine unzureichende Wärmezufuhr während der Aushärtung führt zu einem Netzwerk mit unvollständiger Polymerisation und damit zu einer verminderten mechanischen, chemischen und Wärmebeständigkeit. Die Aushärtungstemperatur sollte in der Regel die Glasübergangstemperatur (Tg) des vollständig ausgehärteten Netzwerks erreichen, um maximale Eigenschaften zu erzielen. Manchmal wird die Temperatur schrittweise erhöht, um die Aushärtungsgeschwindigkeit zu kontrollieren und einen übermäßigen Wärmestau durch die exotherme Reaktion zu vermeiden. ⓘ
Härter, die bei Raumtemperatur nur eine geringe oder begrenzte Reaktivität aufweisen, aber bei erhöhter Temperatur mit Epoxidharzen reagieren, werden als latente Härter bezeichnet. Bei der Verwendung latenter Härter können Epoxidharz und Härter gemischt und vor der Verwendung einige Zeit gelagert werden, was für viele industrielle Prozesse von Vorteil ist. Sehr latente Härter ermöglichen die Herstellung von Einkomponentenprodukten (1K), bei denen das Harz und der Härter vorgemischt an den Endverbraucher geliefert werden und nur noch Wärme zum Aushärten benötigt wird. Einkomponentige Produkte haben im Allgemeinen eine kürzere Haltbarkeitsdauer als herkömmliche 2-Komponenten-Systeme, und die Produkte müssen unter Umständen gekühlt gelagert und transportiert werden. ⓘ
Die Aushärtungsreaktion von Epoxidharz kann durch Zugabe geringer Mengen von Beschleunigern beschleunigt werden. Tertiäre Amine, Carbonsäuren und Alkohole (insbesondere Phenole) sind wirksame Beschleuniger. Bisphenol A ist ein hochwirksamer und weit verbreiteter Beschleuniger, der jedoch aufgrund gesundheitlicher Bedenken gegen diesen Stoff zunehmend ersetzt wird. ⓘ
Homopolymerisation
Epoxidharz kann in Gegenwart eines anionischen Katalysators (eine Lewis-Base wie tertiäre Amine oder Imidazole) oder eines kationischen Katalysators (eine Lewis-Säure wie ein Bortrifluorid-Komplex) mit sich selbst reagieren, um ein gehärtetes Netzwerk zu bilden. Dieses Verfahren wird als katalytische Homopolymerisation bezeichnet. Das entstehende Netzwerk enthält nur Etherbrücken und weist eine hohe thermische und chemische Beständigkeit auf, ist jedoch spröde und erfordert häufig höhere Temperaturen für den Aushärtungsprozess, so dass es in der Industrie nur Nischenanwendungen gibt. Die Epoxidhomopolymerisation wird häufig eingesetzt, wenn eine UV-Härtung erforderlich ist, da kationische UV-Katalysatoren verwendet werden können (z. B. für UV-Beschichtungen). ⓘ
Amine
Polyfunktionelle primäre Amine bilden eine wichtige Klasse von Epoxidhärtern. Primäre Amine gehen eine Additionsreaktion mit der Epoxidgruppe ein, um eine Hydroxylgruppe und ein sekundäres Amin zu bilden. Das sekundäre Amin kann mit einem Epoxid weiter reagieren, um ein tertiäres Amin und eine zusätzliche Hydroxylgruppe zu bilden. Kinetische Untersuchungen haben gezeigt, dass die Reaktivität des primären Amins etwa doppelt so hoch ist wie die des sekundären Amins. Bei Verwendung eines bifunktionellen oder polyfunktionellen Amins bildet sich ein dreidimensionales vernetztes Netzwerk. Aliphatische, cycloaliphatische und aromatische Amine werden alle als Epoxidhärter eingesetzt. Härter vom Typ Amin verändern sowohl die Verarbeitungseigenschaften (Viskosität, Reaktivität) als auch die endgültigen Eigenschaften (mechanische Eigenschaften, Temperatur- und Wärmebeständigkeit) des gehärteten Copolymer-Netzwerks. Daher wird die Aminstruktur normalerweise entsprechend der Anwendung ausgewählt. Das Gesamtreaktivitätspotenzial der verschiedenen Härter kann grob geordnet werden: aliphatische Amine > cycloaliphatische Amine > aromatische Amine, wobei aliphatische Amine mit sterischen Hindernissen in der Nähe der Aminogruppen ebenso langsam reagieren können wie einige der aromatischen Amine. Die langsamere Reaktivität ermöglicht den Verarbeitern längere Arbeitszeiten. Die Temperaturbeständigkeit nimmt im Allgemeinen in der gleichen Reihenfolge zu, da aromatische Amine viel starrere Strukturen bilden als aliphatische Amine. Aromatische Amine wurden häufig als Epoxidharzhärter verwendet, da sie im Gemisch mit einem Stammharz hervorragende Endeigenschaften aufweisen. In den letzten Jahrzehnten hat die Besorgnis über die möglichen gesundheitsschädlichen Wirkungen vieler aromatischer Amine dazu geführt, dass verstärkt aliphatische oder cycloaliphatische Amin-Alternativen verwendet werden. Amine werden auch gemischt, adduziert und umgesetzt, um die Eigenschaften zu verändern, und diese Aminharze werden häufiger zur Aushärtung von Epoxidharzen verwendet als ein reines Amin wie TETA. Zunehmend werden auch Polyamine auf Wasserbasis verwendet, um unter anderem das Toxizitätsprofil zu verringern. ⓘ

Anhydride
Epoxidharze können mit Anhydriden thermisch gehärtet werden, um Polymere zu schaffen, die ihre Eigenschaften auch bei hohen Temperaturen über längere Zeiträume hinweg beibehalten. Die Reaktion und anschließende Vernetzung erfolgt erst nach Öffnung des Anhydridrings, z. B. durch sekundäre Hydroxylgruppen im Epoxidharz. Die Homopolymerisation kann auch zwischen Epoxid- und Hydroxylgruppen stattfinden. Die hohe Latenzzeit von Anhydridhärtern macht sie geeignet für Verarbeitungssysteme, die vor dem Aushärten den Zusatz von mineralischen Füllstoffen erfordern, z. B. für elektrische Hochspannungsisolatoren. Die Aushärtungsgeschwindigkeit kann durch die Kombination von Anhydriden mit geeigneten Beschleunigern verbessert werden. Für Dianhydride und in geringerem Maße auch für Monoanhydride werden häufig nicht-stöchiometrische, empirische Bestimmungen zur Optimierung der Dosierung verwendet. In einigen Fällen können Mischungen von Dianhydriden und Monoanhydriden die Dosierung und Mischung mit flüssigen Epoxidharzen verbessern. ⓘ
Phenole
Polyphenole wie Bisphenol A oder Novolake können mit Epoxidharzen bei erhöhten Temperaturen (130-180 °C, 266-356 °F) reagieren, normalerweise in Gegenwart eines Katalysators. Das resultierende Material ist etherisch gebunden und weist eine höhere Chemikalien- und Oxidationsbeständigkeit auf, als dies bei der Aushärtung mit Aminen oder Anhydriden der Fall ist. Da viele Novolake Feststoffe sind, wird diese Klasse von Härtern häufig für Pulverlacke verwendet. ⓘ
Thiole
Thiole, die auch als Mercaptane bezeichnet werden, enthalten einen Schwefel, der sehr leicht mit der Epoxidgruppe reagiert, selbst bei Raumtemperatur oder darunter. Das entstehende Netzwerk weist zwar in der Regel keine hohe Temperatur- oder Chemikalienbeständigkeit auf, aber die hohe Reaktivität der Thiolgruppe macht sie für Anwendungen nützlich, bei denen eine Aushärtung durch Erhitzen nicht möglich ist oder eine sehr schnelle Aushärtung erforderlich ist, z. B. bei Klebstoffen für den Hausgebrauch und chemischen Felsankern. Thiole haben einen charakteristischen Geruch, der in vielen Zweikomponenten-Haushaltsklebstoffen nachweisbar ist. ⓘ
Anwendungen
- Vielseitiger Konstruktions-Klebstoff, etwa im Bootsbau, Haushalt und Modellbau
- Speziell eingestellte Epoxidharze finden als Metallkleber Anwendung
- Mörtel auf Kunststoffbasis (Reaktionsharzmörtel)
- zur Produktion von Steinteppichen
- Gießharz zur Herstellung von Bauteilen im Gussverfahren
- Wird in Verbindung mit Glasfaser, Kohlenstofffaser und Aramidfaser beim Bau von modernen Hochleistungs-Segelflugzeugen, aber auch zunehmend bei großen Passagierflugzeugen (Kohlenstoff- bzw. Carbonfaser) als Faserverbundkunststoff eingesetzt
- Glasfaserverstärkter Kunststoff kommt für die Herstellung der Rotorblätter von Windkraftanlagen zum Einsatz
- Herstellung von Mineralgussgestellen für den Maschinenbau
- Industriefußboden; Betonbeschichtung; Betonreparatur
- Ionenaustauschersäulen (Chemie)
- Anstrich; schwerer Korrosionsschutz (Schiffbau, Stahlkonstruktionen)
- Abdichtung von Holzterrarien (Terrarientechnik), da ausgehärtet ungiftig
- Bindemittel für verschiedene Anstrichstoffe (Lacke), durch Kombination von Phenolharzen entstehen Innenschutzlackierungen für Verpackungsmittel aller Art, von Haarspraydosen bis zu Lebensmittelverpackungen (sogenannte Goldlacke)
- Lacke zum Schutz vor Graffiti
- Herstellung von wasserlöslichen Kunstharzen zur kathodischen Tauchlackierung (KTL, Automobilbau)
- Sanierung von Rohren, insbes. Rohrinnensanierung (etwa von Trinkwasserleitungen, Fußbodenheizungen)
- Bemalung von Radwegen
- Vergießen von elektrischen Bauteilen oder anderen Objekten zwecks Isolation und Korrosionsschutz
- Leiterplattenmaterial wie FR-4 als Trägermaterial von elektronischen Schaltungen
- Matrixmaterial für die Herstellung von Faserverbundbauteilen, unter anderem für Luft- und Raumfahrt, für den Motorsport, in der Orthopädietechnik und für den Yachtbau; häufig auch im Handlaminierverfahren
- Plastination; insbesondere spezielle Epoxidharze, wie Epoxy E-12, werden zur Fixierung anatomischer Präparate eingesetzt
- Wird auf Kanten (coping) von Skateboardrampen für bessere Rutschfähigkeit und als Schutz aufgebracht
- Trägermaterial in der Kunst
- Material zur Abformung in der Bildhauerei
- Herstellung von Dünnschliffen ⓘ
Beim Bau von Bootsrümpfen hat Epoxidharz gegenüber manchen Polyesterharzen unter anderem den Vorteil, dass es Osmoseschäden ausschließt, selbst wenn Seewasser durch eine beschädigte Gelcoat-Schicht dringt und mit dem Werkstoff in Berührung kommt. Deshalb wird Epoxidharz auch zur Reparatur von Osmoseschäden an Polyesterharz-Bootsrümpfen verwendet. ⓘ
Epoxidharz ist beim jetzigen Stand der Technik nicht recyclingfähig und die Stoffe zu dessen Herstellung werden überwiegend aus Erdöl gewonnen. Es laufen aber bereits Versuche, Epoxidharz auf Basis nachwachsender Rohstoffe zu gewinnen. Ziel ist es, ein ungiftiges, geruchloses und nicht allergenes Epoxidharz zu entwickeln. ⓘ
Die Anwendungen für Materialien auf Epoxidharzbasis sind umfangreich und sie gelten als sehr vielseitig. Zu den Anwendungen gehören Beschichtungen, Klebstoffe und Verbundwerkstoffe wie Kohlefaser- und Glasfaserverstärkungen (obwohl auch Polyester, Vinylester und andere duroplastische Harze für glasfaserverstärkte Kunststoffe verwendet werden). Aufgrund der chemischen Zusammensetzung von Epoxidharzen und der Vielzahl der im Handel erhältlichen Varianten können härtbare Polymere mit einem sehr breiten Spektrum an Eigenschaften hergestellt werden. Sie wurden in großem Umfang für Beton und zementhaltige Systeme verwendet. Im Allgemeinen sind Epoxide für ihre hervorragende Haftung, Chemikalien- und Wärmebeständigkeit, gute bis sehr gute mechanische Eigenschaften und sehr gute elektrische Isolationseigenschaften bekannt. Viele Eigenschaften von Epoxiden können modifiziert werden (z. B. gibt es silbergefüllte Epoxide mit guter elektrischer Leitfähigkeit, obwohl Epoxide normalerweise elektrisch isolierend sind). Es gibt Varianten mit hoher Wärmeisolierung oder Wärmeleitfähigkeit in Kombination mit hohem elektrischen Widerstand für elektronische Anwendungen. ⓘ
Wie bei anderen Klassen von duroplastischen Polymerwerkstoffen ist es üblich, verschiedene Epoxidharzqualitäten zu mischen und Zusatzstoffe, Weichmacher oder Füllstoffe zu verwenden, um die gewünschten Verarbeitungs- oder Endeigenschaften zu erzielen oder die Kosten zu senken. Die Verwendung von Mischungen, Additiven und Füllstoffen wird oft als Formulierung bezeichnet. ⓘ
Alle Mengen an Mischungen erzeugen ihre eigene Wärme, da die Reaktion exotherm ist. Große Mengen erzeugen mehr Wärme und erhöhen somit die Reaktionsgeschwindigkeit und verkürzen die Verarbeitungszeit (Topfzeit). Daher ist es sinnvoll, kleinere Mengen zu mischen, die schnell verbraucht werden können, um Abfall zu vermeiden und die Sicherheit zu erhöhen. Es gibt verschiedene Methoden, sie zu härten. ⓘ
Anstriche und Beschichtungen
Zweikomponenten-Epoxidbeschichtungen wurden für den harten Einsatz auf Metallsubstraten entwickelt und verbrauchen weniger Energie als wärmegehärtete Pulverbeschichtungen. Diese Systeme bieten eine zähe, schützende Beschichtung mit ausgezeichneter Härte. Einkomponentige Epoxidbeschichtungen werden als Emulsion in Wasser formuliert und können ohne Lösungsmittel gereinigt werden. ⓘ
Epoxidharzlacke werden häufig in der Industrie und im Automobilbau eingesetzt, da sie hitzebeständiger sind als Farben auf Latex- und Alkydbasis. Epoxidfarben neigen dazu, sich durch UV-Einwirkung zu verschlechtern, was als "Auskreiden" bezeichnet wird. ⓘ
Eine Farbveränderung, das so genannte Vergilben, ist ein häufiges Phänomen bei Epoxidharzen und wird häufig bei Kunst- und Konservierungsanwendungen beobachtet. Epoxidharze vergilben mit der Zeit, auch wenn sie nicht der UV-Strahlung ausgesetzt sind. Bedeutende Fortschritte im Verständnis der Vergilbung von Epoxidharzen wurden von Down zunächst 1984 (natürliche Dunkelalterung) und später 1986 (Alterung mit hochintensivem Licht) erzielt. Down untersuchte verschiedene bei Raumtemperatur aushärtende Epoxidharzklebstoffe, die für die Glaskonservierung geeignet sind, und testete ihre Vergilbungsneigung. Ein grundlegendes molekulares Verständnis der Vergilbung von Epoxidharzen wurde erreicht, als Krauklis und Echtermeyer den mechanistischen Ursprung der Vergilbung in einem häufig verwendeten Amin-Epoxidharz entdeckten und 2018 veröffentlichten. Sie fanden heraus, dass der molekulare Grund für die Epoxidvergilbung eine thermo-oxidative Entwicklung von Carbonylgruppen im polymeren Kohlenstoff-Kohlenstoff-Grundgerüst durch einen nukleophilen Radikalangriff ist. ⓘ
Polyester-Epoxide werden als Pulverbeschichtungen für Waschmaschinen, Trockner und andere "weiße Ware" verwendet. Schmelzgebundene Epoxidpulverlacke (FBE) werden in großem Umfang für den Korrosionsschutz von Stahlrohren und Armaturen in der Öl- und Gasindustrie, Trinkwasserleitungen (Stahl) und Betonstahl verwendet. Epoxidbeschichtungen werden auch häufig als Grundierungen verwendet, um die Haftung von Automobil- und Schiffslacken zu verbessern, insbesondere auf Metalloberflächen, bei denen Korrosionsschutz (Rostschutz) wichtig ist. Metalldosen und -behälter werden häufig mit Epoxidharz beschichtet, um das Rosten zu verhindern, insbesondere bei Lebensmitteln wie Tomaten, die säurehaltig sind. Epoxidharze werden auch für dekorative Bodenbeläge wie Terrazzoböden, Splittböden und farbige Aggregatböden verwendet. ⓘ
Epoxidharze wurden auf verschiedene Weise modifiziert. Durch Reaktion mit aus Ölen gewonnenen Fettsäuren entstanden Epoxidester, die auf die gleiche Weise wie Alkydharze gehärtet wurden. Typisch waren L8 (80 % Leinsamen) und D4 (40 % dehydriertes Rizinusöl). Diese wurden häufig mit Styrol zu styrolisierten Epoxidestern umgesetzt, die als Grundierungen verwendet wurden. Aushärtung mit Phenolen zur Herstellung von Fassauskleidungen, Aushärtung von Estern mit Aminharzen und Vorhärtung von Epoxiden mit Aminoharzen zur Herstellung von widerstandsfähigen Decklacken. ⓘ
Eines der besten Beispiele war ein System zur Verwendung lösungsmittelfreier Epoxidharze für die Grundierung von Schiffen während des Baus, bei dem ein Airless-Heißspritzsystem mit Vormischung am Kopf verwendet wurde. Dadurch wurde das Problem der Lösungsmittelretention unter dem Film vermieden, das später zu Haftungsproblemen führte. ⓘ
Klebstoffe

Epoxidharzklebstoffe sind ein wichtiger Teil der Klebstoffklasse, die als "strukturelle Klebstoffe" oder "technische Klebstoffe" bezeichnet wird (dazu gehören Polyurethan, Acryl, Cyanacrylat und andere Chemikalien). Diese Hochleistungsklebstoffe werden beim Bau von Flugzeugen, Autos, Fahrrädern, Booten, Golfschlägern, Skiern, Snowboards und anderen Anwendungen eingesetzt, bei denen hochfeste Verbindungen erforderlich sind. Epoxidklebstoffe können für nahezu jede Anwendung entwickelt werden. Sie können als Klebstoffe für Holz, Metall, Glas, Stein und einige Kunststoffe verwendet werden. Sie können flexibel oder starr, transparent oder undurchsichtig/farbig, schnell oder langsam abbindend hergestellt werden. Epoxidklebstoffe sind hitze- und chemikalienbeständiger als andere übliche Klebstoffe. Im Allgemeinen sind Epoxidklebstoffe, die unter Wärmeeinwirkung ausgehärtet werden, hitze- und chemikalienbeständiger als solche, die bei Raumtemperatur ausgehärtet werden. Die Festigkeit von Epoxidklebstoffen wird bei Temperaturen über 177 °C (350 °F) beeinträchtigt. ⓘ
Einige Epoxidharze werden durch Bestrahlung mit ultraviolettem Licht gehärtet. Solche Epoxidharze werden häufig in der Optik, Faseroptik und Optoelektronik verwendet. ⓘ
Industrieller Werkzeugbau und Verbundwerkstoffe
Epoxidsysteme werden im industriellen Werkzeugbau zur Herstellung von Formen, Urmodellen, Laminaten, Gussteilen, Vorrichtungen und anderen industriellen Produktionshilfen verwendet. Diese "Kunststoffwerkzeuge" ersetzen Metall, Holz und andere herkömmliche Materialien und verbessern im Allgemeinen die Effizienz und senken entweder die Gesamtkosten oder verkürzen die Vorlaufzeit für viele industrielle Prozesse. Epoxidharze werden auch bei der Herstellung von faserverstärkten oder Verbundwerkstoffteilen verwendet. Sie sind teurer als Polyesterharze und Vinylesterharze, ergeben aber in der Regel stärkere und temperaturbeständigere Duroplast-Verbundteile. ⓘ
Verbundwerkstoffe in der Windkraftanlagentechnik
Epoxidharze werden als Bindematrix zusammen mit Glas- oder Kohlefasergeweben verwendet, um Verbundwerkstoffe mit einem sehr guten Verhältnis zwischen Festigkeit und Gewicht herzustellen, wodurch längere und effizientere Rotorblätter produziert werden können. Darüber hinaus werden Epoxidharze bei Offshore- und Onshore-Windenergieanlagen als Schutzbeschichtungen für Stahltürme, Basisstreben und Betonfundamente verwendet. Darüber werden aliphatische Polyurethan-Deckbeschichtungen aufgetragen, um einen vollständigen UV-Schutz zu gewährleisten, die Lebensdauer der Anlagen zu verlängern und die Wartungskosten zu senken. Elektrische Generatoren, die über den Antriebsstrang mit den Rotorblättern verbunden sind, wandeln die mechanische Windenergie in nutzbare elektrische Energie um und sind auf die elektrische Isolierung und die hohe Wärmebeständigkeit von Epoxiden angewiesen. Das Gleiche gilt für Transformatoren, Durchführungen, Abstandshalter und Verbundwerkstoffkabel, die die Windkraftanlagen mit dem Netz verbinden. In Europa machen Komponenten für die Windenergie mit etwa 27 % des Marktes das größte Segment der Epoxidanwendungen aus. ⓘ
Elektrische Systeme und Elektronik


Epoxidharzformulierungen sind in der Elektronikindustrie von großer Bedeutung und werden in Motoren, Generatoren, Transformatoren, Schaltanlagen, Durchführungen, Isolatoren, Leiterplatten (PWB) und Halbleiterkapselungen eingesetzt. Epoxidharze sind ausgezeichnete elektrische Isolatoren und schützen elektrische Bauteile vor Kurzschlüssen, Staub und Feuchtigkeit. In der Elektronikindustrie werden Epoxidharze hauptsächlich für das Umspritzen von integrierten Schaltungen, Transistoren und Hybridschaltungen sowie für die Herstellung von Leiterplatten verwendet. Der volumenstärkste Leiterplattentyp - eine "FR-4-Platte" - ist ein Sandwich aus Schichten von Glasgewebe, die durch ein Epoxidharz zu einem Verbundstoff verbunden sind. Epoxidharze werden verwendet, um Kupferfolien auf Leiterplattensubstrate zu kleben, und sind Bestandteil der Lötmaske vieler Leiterplatten. ⓘ
Flexible Epoxidharze werden für den Verguss von Transformatoren und Drosseln verwendet. Durch die Vakuumimprägnierung von unausgehärtetem Epoxidharz werden Luftporen zwischen Wicklung und Kern sowie zwischen Wicklung und Isolator vermieden. Das ausgehärtete Epoxidharz ist ein elektrischer Isolator und ein viel besserer Wärmeleiter als Luft. Hot Spots bei Transformatoren und Induktoren werden stark reduziert, wodurch die Komponenten stabiler und langlebiger sind als nicht vergossene Produkte. ⓘ
Epoxidharze werden mit der Technologie der Harzdosierung aufgetragen. ⓘ
Erdöl und Petrochemie
Epoxidharze können verwendet werden, um bestimmte Schichten in einem Reservoir zu verstopfen, die übermäßig viel Salzlauge produzieren. Diese Technik wird als "Wasserabdichtungsbehandlung" bezeichnet. ⓘ
Verbraucher- und Schiffsanwendungen
Epoxidharze werden in Baumärkten verkauft, in der Regel als Packung mit getrenntem Harz und Härter, die unmittelbar vor der Verwendung gemischt werden müssen. Sie werden auch in Bootsgeschäften als Reparaturharze für Schiffsanwendungen verkauft. Epoxidharze werden in der Regel nicht für die Außenschicht eines Bootes verwendet, da sie durch UV-Licht beschädigt werden. Sie werden häufig bei der Reparatur und Montage von Booten verwendet und dann mit herkömmlichen oder zweikomponentigen Polyurethanfarben oder Schiffslacken überstrichen, die einen UV-Schutz bieten. ⓘ
Es gibt zwei Hauptanwendungsbereiche in der Schifffahrt. Aufgrund der besseren mechanischen Eigenschaften im Vergleich zu den gebräuchlicheren Polyesterharzen werden Epoxide für die kommerzielle Herstellung von Bauteilen verwendet, bei denen ein hohes Festigkeits-/Gewichtsverhältnis erforderlich ist. Der zweite Bereich ist die Tatsache, dass ihre Festigkeit, ihre spaltfüllenden Eigenschaften und ihre hervorragende Haftung an vielen Materialien, einschließlich Holz, zu einem Boom bei Amateurbauprojekten wie Flugzeugen und Booten geführt haben. ⓘ
Normales Gelcoat, das für die Verwendung mit Polyesterharzen und Vinylesterharzen formuliert ist, haftet nicht auf Epoxidoberflächen, obwohl Epoxid sehr gut auf Polyesterharzoberflächen haftet. "Flocoat", das normalerweise für die Innenbeschichtung von Polyester-Glasfaserjachten verwendet wird, ist auch mit Epoxidharzen kompatibel. ⓘ
Epoxidharze härten in der Regel etwas langsamer aus, während Polyesterharze schnell aushärten, insbesondere wenn viel Katalysator verwendet wird. Die chemischen Reaktionen sind in beiden Fällen exotherm. ⓘ
Obwohl es üblich ist, Polyesterharze und Epoxidharze miteinander in Verbindung zu bringen, sind ihre Eigenschaften so unterschiedlich, dass sie als eigenständige Materialien behandelt werden sollten. Polyesterharze haben in der Regel eine geringe Festigkeit, es sei denn, sie werden mit einem Verstärkungsmaterial wie Glasfasern verwendet, sind relativ spröde, wenn sie nicht verstärkt werden, und haben ein geringes Haftvermögen. Epoxidharze hingegen sind von Natur aus fest, einigermaßen flexibel und haben ein ausgezeichnetes Haftvermögen. Polyesterharze sind jedoch viel billiger. ⓘ
Epoxidharze erfordern in der Regel eine genaue Mischung aus zwei Komponenten, die eine dritte Chemikalie bilden, um die angegebenen Eigenschaften zu erhalten. Je nach den gewünschten Eigenschaften kann das Verhältnis zwischen 1:1 und über 10:1 liegen, aber in der Regel müssen sie genau gemischt werden. Das Endprodukt ist dann ein präziser duroplastischer Kunststoff. Bis zum Vermischen sind die beiden Elemente relativ inert, obwohl die "Härter" chemisch aktiver sind und vor der Atmosphäre und Feuchtigkeit geschützt werden sollten. Die Geschwindigkeit der Reaktion kann durch die Verwendung verschiedener Härter, die die Beschaffenheit des Endprodukts verändern können, oder durch die Steuerung der Temperatur verändert werden. ⓘ
Im Gegensatz dazu werden Polyesterharze in der Regel in einer "geförderten" Form angeboten, so dass die Umwandlung der zuvor gemischten Harze von flüssig zu fest bereits im Gange ist, wenn auch sehr langsam. Die einzige Variable, die dem Benutzer zur Verfügung steht, ist die Veränderung der Geschwindigkeit dieses Prozesses mit Hilfe eines Katalysators, häufig Methyl-Ethyl-Keton-Peroxid (MEKP), das sehr giftig ist. Das Vorhandensein des Katalysators im Endprodukt beeinträchtigt die gewünschten Eigenschaften, so dass geringe Mengen an Katalysator vorzuziehen sind, solange die Aushärtung in einem akzeptablen Tempo erfolgt. Die Aushärtungsgeschwindigkeit von Polyestern kann daher durch die Menge und Art des Katalysators sowie durch die Temperatur gesteuert werden. ⓘ
Als Klebstoffe haften Epoxidharze auf dreierlei Weise: a) mechanisch, weil die Klebeflächen aufgeraut werden; b) durch Nähe, weil die ausgehärteten Harze physisch so nahe an den Klebeflächen liegen, dass sie nur schwer zu trennen sind; c) ionisch, weil die Epoxidharze auf atomarer Ebene Ionenbindungen mit den Klebeflächen bilden. Letzteres ist im Wesentlichen die stärkste der drei Möglichkeiten. Im Gegensatz dazu können Polyesterharze nur die ersten beiden Bindungen eingehen, was ihren Nutzen als Klebstoffe und bei der Reparatur von Schiffen stark einschränkt. ⓘ
Anwendungen im Bauwesen
Epoxide werden seit einigen Jahrzehnten erforscht und im Bauwesen eingesetzt. Sie erhöhen zwar die Kosten für Mörtel und Beton, wenn sie als Zusatzstoff verwendet werden, verbessern aber die Eigenschaften. Derzeit wird die Verwendung von Epoxidharzen und anderen recycelten Kunststoffen in Mörteln erforscht, um die Eigenschaften zu verbessern und Abfälle zu recyceln. Die Verdichtung von Kunststoffen wie PET und Plastiktüten und ihre anschließende Verwendung als teilweiser Ersatz für Zuschlagstoffe sowie die Depolymerisation von PET zur Verwendung als polymeres Bindemittel zusätzlich zu Epoxid zur Verbesserung von Beton sind Gegenstand aktiver Untersuchungen. ⓘ
Anwendungen in der Luft- und Raumfahrt
In der Luft- und Raumfahrtindustrie wird Epoxidharz als strukturelles Matrixmaterial verwendet, das dann durch Fasern verstärkt wird. Typische Verstärkungsfasern sind Glas, Kohlenstoff, Kevlar und Bor. Epoxidharze werden auch als struktureller Klebstoff verwendet. Materialien wie Holz und andere "Low-Tech"-Materialien werden mit Epoxidharz geklebt. Epoxidharze übertreffen im Allgemeinen die meisten anderen Harztypen in Bezug auf mechanische Eigenschaften und Beständigkeit gegen Umwelteinflüsse. ⓘ
Biologie
Wasserlösliche Epoxidharze wie Durcupan werden häufig zum Einbetten von elektronenmikroskopischen Proben in Kunststoff verwendet, damit sie mit einem Mikrotom geschnitten (in dünne Scheiben geschnitten) und dann abgebildet werden können. ⓘ
Kunst
Mit Pigmenten vermischtes Epoxidharz kann als Malmittel verwendet werden, indem Schichten übereinander gegossen werden, um ein vollständiges Bild zu erhalten. Es wird auch in der Schmuckherstellung, als Doming-Harz für Dekorationen und Etiketten sowie für Decoupage-Anwendungen für Kunst, Arbeitsplatten und Tische verwendet. Es wurde für die Kunst und die Erhaltung historischer Strukturen verwendet und untersucht. ⓘ
Produktion
Der globale Epoxidharzmarkt wurde 2021 auf ca. 9,1 (Mrd. USD) geschätzt und wird bis 2028 voraussichtlich einen Umsatz von ca. 14,7 (Mrd. USD) erzielen, wobei für den Zeitraum von 2022 bis 2028 eine CAGR von fast 6,8% erwartet wird. Der Epoxidharzmarkt wird von der asiatisch-pazifischen Region dominiert, die 55,2 % des gesamten Marktanteils ausmacht. China ist der größte Produzent und Verbraucher weltweit und verbraucht fast 35 % der weltweiten Harzproduktion. Der Weltmarkt besteht aus etwa 50 bis 100 Herstellern von Epoxidharzen und -härtern, die als Basis- oder Standardprodukte angeboten werden. In Europa wurden im Jahr 2017 etwa 323.000 Tonnen Epoxidharz hergestellt und ein Umsatz von rund 1.055 Millionen Euro erzielt. Deutschland ist der größte Markt für Epoxidharze in Europa, gefolgt von Italien, Frankreich, dem Vereinigten Königreich, Spanien, den Niederlanden und Österreich. ⓘ
Daher gibt es eine weitere Gruppe von Unternehmen, die Epoxidharz-Rohstoffe von den großen Herstellern kaufen und dann Epoxidharzsysteme aus diesen Rohstoffen herstellen (mischen, modifizieren oder anderweitig anpassen). Diese Unternehmen werden als "Formulierer" bezeichnet. Der Großteil der verkauften Epoxidsysteme wird von diesen Formulierern hergestellt, und sie machen über 60 % des Dollarwerts des Epoxidmarktes aus. Es gibt Hunderte von Möglichkeiten, wie diese Formulierer Epoxidharze modifizieren können - durch Zugabe von mineralischen Füllstoffen (Talkum, Siliziumdioxid, Aluminiumoxid usw.), durch Zugabe von Flexibilisatoren, Viskositätsreduzierern, Farbstoffen, Verdickungsmitteln, Beschleunigern, Haftvermittlern usw. Diese Änderungen werden vorgenommen, um die Kosten zu senken, die Leistung zu verbessern und die Verarbeitung zu erleichtern. Infolgedessen verkauft ein typischer Formulierer Dutzende oder sogar Tausende von Rezepturen, die jeweils auf die Anforderungen einer bestimmten Anwendung oder eines bestimmten Marktes zugeschnitten sind. ⓘ
Die Rohstoffe für die Herstellung von Epoxidharzen werden heute größtenteils aus Erdöl gewonnen, auch wenn einige pflanzliche Rohstoffe inzwischen kommerziell verfügbar sind (z. B. Glycerin aus Pflanzen, das zur Herstellung von Epichlorhydrin verwendet wird). ⓘ
Gesundheitliche Risiken
Flüssige Epoxidharze in unausgehärtetem Zustand werden meist als augen- und hautreizend sowie als giftig für Wasserorganismen eingestuft. Feste Epoxidharze sind im Allgemeinen sicherer als flüssige Epoxidharze, und viele von ihnen werden als ungefährlich eingestuft. Ein besonderes Risiko im Zusammenhang mit Epoxidharzen ist die Sensibilisierung. Dieses Risiko ist nachweislich bei Epoxidharzen, die Epoxidverdünner mit niedrigem Molekulargewicht enthalten, stärker ausgeprägt. Die Exposition gegenüber Epoxidharzen kann im Laufe der Zeit eine allergische Reaktion hervorrufen. Eine Sensibilisierung tritt in der Regel bei wiederholter Exposition (z. B. durch schlechte Arbeitshygiene oder fehlende Schutzausrüstung) über einen langen Zeitraum auf. Die allergische Reaktion tritt manchmal erst mehrere Tage nach der Exposition auf. Die allergische Reaktion zeigt sich häufig in Form von Dermatitis, insbesondere an den Stellen, an denen die Exposition am höchsten war (in der Regel Hände und Unterarme). Die Verwendung von Epoxidharz ist eine der Hauptursachen für berufsbedingtes Asthma bei Kunststoffverarbeitern. Auch über die sichere Entsorgung muss nachgedacht werden, die jedoch in der Regel eine absichtliche Aushärtung erfordert, damit feste und nicht flüssige Abfälle entstehen. ⓘ
Charakterisierung
Epoxidharz-Produkte werden über unterschiedliche Kennzahlen charakterisiert. Hierzu zählen die Molmasse bzw. die Molmassenverteilung, die Hydroxylzahl sowie das Epoxid-Äquivalentgewicht. Des Weiteren bestimmt die bereits erwähnte Glasübergangstemperatur eine entscheidende Rolle für die Eigenschaften der später erhaltenen Produkte. ⓘ
Verarbeitung
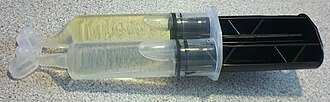
Wie bei allen Reaktionsharzen muss beim Anmischen von Reaktionsharzmassen das stöchiometrische Harz-Härter-Verhältnis genau eingehalten werden – andernfalls verbleiben Teile von Harz oder Härter ohne Reaktionspartner. Diese unreagierten funktionellen Gruppen bleiben zurück und die Vernetzung bleibt unvollständig, was zu einem weichen Produkt und zu klebrigen Oberflächen führt. Einige Epoxidsysteme sind jedoch weniger empfindlich und innerhalb enger Grenzen ausdrücklich für eine Variation des Mischungsverhältnisses geeignet. Dadurch lassen sich Härte, Elastizität und andere Eigenschaften beeinflussen; so wird die Säurebeständigkeit durch einen höheren Anteil Epoxidharz erhöht. Da eine inhomogene Mischung der beiden Komponenten den gleichen negativen Effekt wie ein falsches Mengenverhältnis hat, sind umfangreiche Mischprozeduren beim Anmischen notwendig. Wenn die Farbgebung des resultierenden Kunststoffes ohne Belang ist, können als Durchmischungsindikator die beiden Ausgangsstoffe kontrastreich gefärbt sein. Die Polyaddition ist stark exotherm. Die entstehende Reaktionswärme kann so groß werden, dass es zum Brand kommt; zumindest können jedoch die Eigenschaften des Harzes durch die Überhitzung negativ beeinflusst werden. Für Bauteile mit großen Wanddicken werden daher niedrigreaktive Harze verwendet. ⓘ
Die Verarbeitungsdauer von Reaktionsharzmassen wird Topfzeit genannt. Sie hängt von der Verarbeitungstemperatur, der Einstellung der Reaktionsharzmassen und der Ansatzgröße ab. Übliche Topfzeiten liegen bei einigen Minuten bis hin zu mehreren Stunden. Während der Topfzeit steigt die Viskosität des Harzes in einer nichtlinearen Kurve immer weiter an, bis schließlich keine Verarbeitung mehr möglich ist. Die Angabe der Topfzeit ist in der Regel bei einem Harz/Härter-Ansatz von 100 g bei 20 °C gemacht – größere Verarbeitungsmengen entwickeln eine höhere Temperatur und haben eine wesentlich kürzere Verarbeitungszeit. ⓘ
Eine Erwärmung des angemischten Harzes verringert die Viskosität und verbessert dadurch im Allgemeinen die Verarbeitbarkeit, verkürzt aber auch die Topfzeit. Eine Erhöhung der Verarbeitungstemperatur um 10 °C bewirkt eine Halbierung der Topf- bzw. Aushärtezeit (RGT-Regel). Niedrigreaktive Epoxidharze benötigen lange Härtezeiten und möglichst eine erhöhte Härtungstemperatur (30 °C bis 40 °C). Bei Bedarf können noch Beschleuniger (hochreaktive Härter) zugegeben werden, die die Reaktionszeit verkürzen. Einige Epoxidharze können zur vollständigen Vernetzung und zum Erreichen einer höheren Wärmeformbeständigkeit nach der Aushärtung einer Warmhärtung unterzogen werden. ⓘ
Beim Warmhärten (Temperung) steigt die Glasübergangstemperatur (Tg) der Matrix um ca. 20 °C bis 25 °C über die maximale Warmhärtungstemperatur an – dies ist der sogenannte Temperaturvorlauf. Raumtemperaturanhärtende Systeme härten bei Raumtemperatur teilweise mit einer sehr spröden Matrix – eine Härtung über 40 °C/5 h bis 6 h beseitigt diese und verbessert zusätzlich die mechanischen Eigenschaften. ⓘ
Die Reaktionsharzmassen werden häufig mit niedrigviskosen Zusätzen modifiziert. Durch die niedrigere Viskosität der Reaktionsharzmasse wird eine bessere Penetration in poröse Werkstoffe (Tränkung von Geweben, Beschichtung von Beton) erreicht oder die Verarbeitbarkeit durch Spritzpressen (RTM-Verfahren) verbessert. Andererseits erlauben derartige Reaktionsharzmassen eine höhere Beladung mit Füllstoffen, woraus bei der Härtung ein geringerer Volumenschrumpf resultiert. Ebenfalls können die mechanischen Eigenschaften des gehärteten Harzes verbessert werden, ebenso die Ökonomie. Für diese Zwecke werden bevorzugt Glycidylether verwendet, da diese – im Gegensatz zu nicht reaktiven Verdünnern – kovalent an das Polymer gebunden werden und daher auch nicht migrieren können. ⓘ
Gebräuchlich als Reaktivverdünner sind:
- Monoglycidylether – Glycidylether von einwertigen Phenolen oder Alkoholen
Monoglycidylether neigen dazu, die Polyaddition abzubrechen, da sie nur monofunktionell sind. Daher beeinträchtigen sie die Festigkeit und die Temperaturbeständigkeit, erhöhen aber die Flexibilität. Glycidylether von Phenolen wirken hier weniger nachteilig als Alkylglycidylether, werden aber toxikologisch ungünstiger beurteilt. Bei den Alkylglycidylethern werden langkettige (C12–C14) wegen ihres niedrigen Dampfdrucks bevorzugt eingesetzt; sie lassen sich günstig aus Fettalkoholen herstellen.
- Polyglycidylether
Diese mehrfunktionellen Reaktivverdünner werden eingesetzt, wenn höhere Ansprüche an die mechanischen Eigenschaften gestellt werden. Da sie über mindestens zwei (wie der häufig eingesetzte Hexan-1,6-dioldiglycidylether) Epoxidgruppen verfügen, bewirken sie keinen Abbruch der Polyaddition. ⓘ
Reaktionsharzmassen können mit Zuschlagstoffen (z. B. pyrogenem Siliciumdioxid) versehen werden, um sie thixotrop einzustellen. Dieses verdickte Harz kann als Füllmasse oder Klebstoff verwendet werden. Andere Zuschlagstoffe dienen als Füllmittel (Hohlkugeln aus Glas, Keramik oder Kunststoffen), um die Dichte des Harzes zu verringern, um die Griffigkeit bzw. Abrasionsbeständigkeit der Oberfläche zu verbessern (Quarzsand, keramische Pulver) oder um die maximale Dauer-Betriebstemperatur zu steigern (Metallische Füllstoffe: Aluminium-, Eisen/Stahlpulver). Zuschlagstoffe (wie Aluminiumhydroxid) können das brandhemmende Verhalten von Epoxidharz verbessern. Dies ist besonders beim Einsatz in Verkehrsmitteln wichtig. ⓘ
Das Aushärten kann mittels Zugabe von Photoinitiatoren mit Ultraviolett gestartet werden, wodurch Aushärtezeiten im Sekundenbereich erreicht werden. ⓘ
Eigenschaften
Das ungefüllte ausgehärtete Harz hat eine Dichte von 1020 bis etwa 1200 kg/m3. Der Elastizitätsmodul beträgt 3000 bis 4500 MPa und die Zugfestigkeit etwa 80 MPa. Diese Werte variieren je nach Formulierung und Herstellung. ⓘ
Die Dielektrizitätszahl beträgt im Temperaturbereich −40 bis etwa +60 °C etwa 4 und steigt ebenso wie der dielektrische Verlustfaktor bei beginnender Erweichung (80 bis 100 °C) stark an. Der Verlustfaktor hat bei 40 °C ein Minimum, beträgt dort 50 bis 100 · 10−4 und steigt bei 100 bis 120 °C durch Orientierungspolarisation großer Kettensegmente auf etwa das 10 bis 20-fache an. Bei −40 °C ist ebenfalls ein Maximum (3 bis 10-facher Wert desjenigen bei 40 °C), hier hervorgerufen durch Orientierungspolarisation kurzer Kettensegmente. Es werden Werkstoffe mit CTI-Werten (Kriechstromfestigkeit) von über 600 V angeboten. Durch Bromierung wird das Material schwer entflammbar (UL94 V-1 oder besser). ⓘ
Die Wärmeleitfähigkeit beträgt 0,21 W/(m·K) und kann durch Füllstoffe wesentlich gesteigert werden (isolierende elektrische Vergussmassen etwa 1,26 W/(m·K) bis 6 W/(m·K)). ⓘ
Die chemische Schwindung bei der Polyaddition ist mit 0,5 bis 5 % deutlich geringer als bei den ungesättigten Polyesterharzen. Sie kann mit Füllstoffen noch weiter verringert werden. ⓘ
Das ungefüllte Harz ist transparent gelblich bis wasserklar und ist auch ultraviolettbeständig bzw. vergilbungsfrei erhältlich. Bei Wellenlängen unterhalb 400 nm wird Epoxidharz nahezu intransparent, im Infrarotbereich ist es bis 2000 nm transparent. Der Brechungsindex liegt bei 1,5 bis 1,59 (bei 589,3 nm Natrium-D-Linie). ⓘ
Sicherheit und Gesundheit
Verarbeitung
Epoxidharz-Produkte ⓘ
Sicherheitshinweise ⓘ | ||||||||
---|---|---|---|---|---|---|---|---|
Name |
Bisphenol-A-Epichlorhydrinharze mit durchschnittlicher Molmasse ≤700 g/mol | |||||||
CAS-Nummer | ||||||||
|
Epoxidharz wird üblicherweise in zwei Komponenten geliefert, die vom Anwender gebrauchsfertig zu mischen sind. Die sog. „A-Komponente“ enthält meist das Epoxidharz, die „B-Komponente“ den Härter, der in einem vorbestimmten Mischungsverhältnis dem Harz zuzugeben ist. ⓘ
Üblicherweise sind Epoxidharze mit den GHS-Symbolen GHS07 („Achtung“) und GHS09 („Umweltgefährlich“) und mit entsprechenden H- und P-Sätzen versehen. Die vielfach zum Einsatz kommenden Epoxidharz-Härter auf Amin-Basis müssen üblicherweise ebenfalls mit GHS-Symbolen (häufig GHS05, „Ätzend“) gekennzeichnet und ebenfalls mit H- und P-Sätzen versehen werden. Da die Gefährdungs- und Sicherheitshinweise in Abhängigkeit von eingesetztem Produkt und Härtertyp variieren, ist den Sicherheitsdatenblättern der verwendeten Produkte besondere Aufmerksamkeit zu schenken. ⓘ
Schutzausrüstung bei der Applikation ⓘ
Da der direkte Hautkontakt als weitaus schädlicher anzusehen ist als etwa eine Aufnahme über die Atemwege (z. B. durch ungenügende Belüftung), ist persönliche Schutzausrüstung beim Einsatz vieler Epoxidprodukte vorgeschrieben. Zum Hautschutz eignen sich ausschließlich spezielle Nitril- oder Butyl-, Butyl/Viton- und PE-Laminat-Handschuhe. Ungeeignet sind dünne Einweg-Handschuhe unabhängig vom Material (zum Beispiel Latex, Vinyl oder Nitril). Die allergenen Stoffe durchdringen diese Handschuhe auch ohne Beschädigung innerhalb weniger Minuten, während der Eigenschutz der Haut durch Schwitzen bei fehlender Belüftung geschwächt wird. Hautschutzsalben bieten ebenfalls keinen akzeptablen Schutz. Unter Umständen kann zusätzlich das Tragen eines Schutzanzugs notwendig sein. ⓘ
Einsatzgebiete
Bezüglich der Verwendung von Epoxidharz-Systemen können ggf. je nach Einsatzgebiet und Anwendungsbereich ergänzende – auch gesetzliche – Anforderungen an Sicherheit und Gesundheit bestehen, so z. B. in den Bereichen Kinderspielzeug, Trinkwasser, Lebensmittelbedarfsgegenstände etc. ⓘ
Arbeitsschutz
Inhaltsstoffe von Epoxidharzen haben sensibilisierende Eigenschaften. Bei ungeeigneter Arbeitsweise kann der Verarbeiter sensibilisiert werden, danach kann es zu allergischen Reaktionen in Form von Hautausschlägen kommen, vor allem beim Kontakt mit nicht ausgehärteten Epoxidharzen. Um Möglichkeiten zur Vermeidung von epoxidharzbedingten allergischen Hauterkrankungen zu erarbeiten, wurden verschiedene Arbeitskreise gegründet und Forschungsprojekte initiiert. Die bisherigen Ergebnisse dieser Arbeiten finden sich gesammelt auf der Epoxidharzseite des Instituts für Arbeitsschutz der Deutschen Gesetzlichen Unfallversicherung (IFA). ⓘ