Morsekegel


Ein Maschinenkegel ist ein System zur Befestigung von Schneidwerkzeugen oder Werkzeughaltern in der Spindel einer Werkzeugmaschine oder eines Elektrowerkzeugs. Ein konisch geformtes (d. h. mit einem Kegel versehenes) männliches Element passt in die weibliche Aufnahme, die einen passenden Kegel mit gleichem Winkel aufweist. ⓘ
Fast alle Spindeln von Werkzeugmaschinen und viele Spindeln von Elektrowerkzeugen haben einen Kegel als Hauptbefestigungsart für Werkzeuge. Auch bei vielen Bohrmaschinen, Handbohrmaschinen und Drehbänken, die über ein Spannfutter verfügen (z. B. ein Bohrfutter oder eine Spannzange), wird das Spannfutter mit einem Kegel befestigt. Bei Bohrmaschinen, Bohrpressen und Fräsmaschinen ist das männliche Element der Werkzeugschaft oder der Schaft des Werkzeughalters, und die weibliche Aufnahme ist fest mit der Spindel verbunden. Bei Drehmaschinen kann das männliche Teil zum Werkzeug oder zur Spindel gehören; Spindelnasen können männliche Kegel, weibliche Kegel oder beides haben. ⓘ



Der Morsekegel (MK) oder Morsekonus ist die genormte Form eines Werkzeugkegels zum Spannen von Werkzeugen, z. B. großen Bohrern, Reibahlen und Spannfuttern in der Werkzeugaufnahme einer Werkzeugmaschine. Gleichbedeutend ist die internationale Bezeichnung Morse taper (mt). ⓘ
Der Name Morsekegel leitet sich von Steffen Morse ab, der im 19. Jahrhundert lebte und 1864 in den USA eine noch heute existierende Werkzeugfirma gründete (nicht zu verwechseln mit Samuel F. B. Morse, dem Namensgeber des Morsecodes). ⓘ
Die Drehmomentübertragung vom Hohlkegel (Hülse) der angetriebenen Werkzeugspindel auf den darin klemmenden Schaft des Werkzeugs erfolgt reibschlüssig durch Haftreibung, infolge der Selbsthemmung. Zum Trennen hat die Hülse eine Queröffnung (im Bild oben rechts), durch die ein Keil eingetrieben werden kann, um den Kegel herauszudrücken. ⓘ
Erläuterung
Die Bediener von Werkzeugmaschinen müssen in der Lage sein, Werkzeugspitzen schnell und einfach ein- und auszubauen. Eine Drehmaschine hat zum Beispiel eine rotierende Spindel in ihrem Spindelstock, an der man einen Stirnradantrieb anbringen oder in einer Spannzange arbeiten möchte. Ein weiteres Beispiel ist eine Bohrmaschine, an der der Bediener einen Bohrer direkt oder mit Hilfe eines Bohrfutters anbringen kann. ⓘ
Praktisch alle Fräsmaschinen, von den ältesten manuellen Maschinen bis hin zu den modernsten CNC-Maschinen, verwenden Werkzeuge, die auf einer kegelförmigen Oberfläche geführt werden. ⓘ
Der Maschinenkegel ist ein einfaches, kostengünstiges, hochgradig wiederholbares und vielseitiges Werkzeugbefestigungssystem. Er bietet Indexierbarkeit, da die Werkzeuge schnell gewechselt werden können, aber durch den Kegel sowohl konzentrisch als auch axial genau positioniert sind. Außerdem ermöglicht es eine hohe Kraftübertragung über die Schnittstelle, was für das Fräsen erforderlich ist. ⓘ
Maschinenkegel können in selbsthaltende und selbstlösende Klassen eingeteilt werden. Bei selbsthaltenden Kegeln verkeilen sich Außen- und Innenkegel so weit ineinander, dass den Bohrkräften ohne Zugstange standgehalten werden kann und das Werkzeug im Leerlauf in der Spindel bleibt. Es wird mit einem Keil herausgetrieben, wenn ein Werkzeugwechsel erforderlich ist. Morse- und Jacobs-Kegel sind ein Beispiel für die selbsthaltende Variante. Bei selbstlösenden Kegeln bleibt die Patrize nicht in der Matrize stecken, ohne dass eine Zugstange sie dort hält. Bei guter Zugkraft ist es jedoch sehr stabil und unbeweglich. NMTB/CAT, BT und HSK sind Beispiele für die selbstlösende Variante. ⓘ
Bei leichten Belastungen (wie sie z. B. bei einem Reitstock einer Drehmaschine oder einer Bohrmaschine auftreten) werden Werkzeuge mit selbsthaltendem Kegel einfach auf oder in die Spindel geschoben; der Druck der Spindel gegen das Werkstück treibt den kegelförmigen Schaft fest in die kegelförmige Bohrung. Die Reibung über die gesamte Oberfläche der Schnittstelle sorgt für eine hohe Drehmomentübertragung, so dass keine Keilnuten oder Passfedern erforderlich sind. ⓘ
Für den Einsatz bei schweren Lasten (wie z. B. bei einer Frässpindel) gibt es in der Regel eine Passfeder, um eine Drehung zu verhindern, und/oder einen Gewindeabschnitt, in den eine Zugstange eingreift, die entweder in das Gewinde oder in den Kopf eines Zugbolzens eingreift, der in das Gewinde eingeschraubt wird. Die Zugstange wird dann angezogen und zieht den Schaft fest in die Spindel. Die Zugstange ist bei Fräsmaschinen wichtig, da die Querkraftkomponente sonst dazu führen würde, dass das Werkzeug aus dem Kegel taumelt. ⓘ
Alle Maschinenkegel sind empfindlich gegenüber Spänen, Kerben (Dellen) und Schmutz. Sie lassen sich nicht genau positionieren, und die selbsthaltenden Varianten halten nicht zuverlässig, wenn derartige Probleme den Sitz der Patrize in der Matrize mit festem Kontakt über die gesamte konische Fläche beeinträchtigen. Zerspanungsmechaniker werden darin geschult, Kegel sauber zu halten und sie so zu handhaben, dass sie nicht von anderen Werkzeugen eingekerbt werden können. CNC-Werkzeugwechselzyklen beinhalten in der Regel ein Druckluftgebläse, während ein Werkzeughalter gegen den nächsten ausgetauscht wird. Durch den Luftstrom werden Späne weggeblasen, die sonst zwischen Werkzeughalter und Spindel geraten könnten. ⓘ
Verwenden Sie
Werkzeuge mit kegelförmigem Schaft werden in eine passende kegelförmige Aufnahme eingesetzt und eingedrückt oder verdreht. Sie werden dann durch Reibung gehalten. In einigen Fällen muss der Reibschluss verstärkt werden, z. B. durch die Verwendung einer Zugstange, d. h. eines langen Bolzens, der das Werkzeug mit größerer Kraft in der Aufnahme hält, als dies auf andere Weise möglich ist. ⓘ
Vorsicht ist geboten, wenn ein Werkzeug verwendet wird, das ein hohes Drehmoment erfordert, aber nur einen geringen axialen Widerstand bietet, wie z. B. bei der Verwendung einer Bohrmaschine oder einer Drehmaschine, bei der keine Zugstange vorhanden ist, um den Kegel in Eingriff zu bringen. Ein Beispiel wäre die Verwendung eines Bohrers mit großem Durchmesser zur leichten Vergrößerung eines bestehenden Lochs. In diesem Fall kann es zu einer erheblichen Drehbelastung kommen. Im Gegensatz dazu erfordert der Schneidvorgang nur eine sehr geringe Schub- oder Vorschubkraft. Die Schubkraft trägt dazu bei, den Kegel in Position zu halten und sorgt für die notwendige Reibungskopplung. ⓘ
Der Mitnehmerzapfen ist nicht dafür ausgelegt, Verdrehungskräften standzuhalten, die ausreichen, um ein Abrutschen des Kegels zu verursachen, und bricht in dieser Situation häufig ab. Dadurch kann sich das Werkzeug im Innenkegel drehen, was zu dessen Beschädigung führen kann. Es sind Morsekegel-Reibahlen erhältlich, um kleinere Schäden zu beheben. ⓘ
Kegelschäfte "kleben" am besten in einer Buchse, wenn sowohl der Schaft als auch die Buchse sauber sind. Die Schäfte können abgewischt werden, aber die Buchsen, die tief und unzugänglich sind, werden am besten mit einem speziellen Kegelreinigungswerkzeug gereinigt, das eingeführt, gedreht und wieder entfernt wird. ⓘ
Werkzeuge mit kegelförmigem Schaft werden je nach Konstruktion des Schaftes auf unterschiedliche Weise aus dem Schaft entfernt. Bei Bohrmaschinen und ähnlichen Werkzeugen wird das Werkzeug entfernt, indem ein keilförmiger Metallblock, der so genannte "Drift", in eine rechteckige Querbohrung durch den Schaft eingeführt und mit einem Gewinde versehen wird. Da sich der Querschnitt des Dorns vergrößert, wenn er weiter hineingetrieben wird, drückt der Dorn das Werkzeug gegen die vordere Kante des Zapfens heraus. Bei vielen Reitstock-Drehmaschinen wird das Werkzeug entfernt, indem die Pinole vollständig in den Reitstock zurückgezogen wird, wodurch das Werkzeug gegen das Ende der Leitspindel oder einen internen Zapfen stößt, wodurch der Kegel getrennt und das Werkzeug freigegeben wird. Wird das Werkzeug durch eine Zugstange gehalten, wie dies bei einigen Frässpindeln der Fall ist, so wird die Zugstange mit einem Schraubenschlüssel teilweise gelöst und dann mit einem Hammer angeklopft, wodurch der Kegel abgetrennt wird und das Werkzeug weiter gelöst und entfernt werden kann. Einige Frässpindeln haben eine unverlierbare Zugstange, die das Werkzeug auswirft, wenn es aktiv über die lose Stufe hinaus herausgeschraubt wird; in diesen Fällen ist kein Gewindeschneiden erforderlich. Bei einfachen Buchsen mit offenem Zugang zum hinteren Ende wird ein Durchschlag von hinten axial eingeführt und das Werkzeug herausgeschnitten. ⓘ
Typen
Es gibt viele Standardkegel, die sich durch folgende Merkmale unterscheiden:
- dem Durchmesser am kleinen Ende des Kegelstumpfs ("kleiner Durchmesser")
- dem Durchmesser am großen Ende des Kegelstumpfs (dem "großen Durchmesser") und
- der axiale Abstand zwischen den beiden Enden des Kegelstumpfes. ⓘ
Die Normen werden in Familien eingeteilt, die verschiedene Größen umfassen können. Die Verjüngung innerhalb einer Familie kann einheitlich sein, muss es aber nicht. Die Jarno- und NMTB-Kegel sind einheitlich, aber die Familien Jacobs und Morse variieren. ⓘ
Es gibt Adapter, die den Einsatz eines Kegelwerkzeugs, z. B. Morse, auf einer Maschine mit einem anderen Kegel, z. B. R8, oder umgekehrt ermöglichen, sowie einfachere Adapter, die aus einer außen und einer innen verjüngten Hülse bestehen, um die Verwendung eines kleinen Morse-Werkzeugs auf einer Maschine mit größerer Bohrung zu ermöglichen. ⓘ
Eine der ersten Verwendungen von Kegeln war die Montage von Bohrern direkt an Werkzeugmaschinen, z. B. im Reitstock einer Drehmaschine, obwohl später Bohrfutter entwickelt wurden, die Bohrer mit parallelem Schaft aufnahmen. ⓘ
Brown und Sharpe
Brown & Sharpe-Kegel, die von der gleichnamigen Firma standardisiert wurden, sind eine Alternative zu dem häufiger anzutreffenden Morsekegel. Wie die Morsekegel haben sie eine Reihe von Größen, von 1 bis 18, wobei 7, 9 und 11 die gängigsten sind. Die tatsächliche Verjüngung liegt in einem engen Bereich um 0,500 Zoll pro Fuß. ⓘ
Größe | Lg. Durchm. | Sm. Durchm. | Länge | Verjüngung (in/ft) | Kegel (in/in) ⓘ |
---|---|---|---|---|---|
1 | 0.2392 | 0.2000 | 0.94 | 0.5020 | 0.04183 |
2 | 0.2997 | 0.2500 | 1.19 | 0.5020 | 0.04183 |
3 | 0.3753 | 0.3125 | 1.50 | 0.5020 | 0.04183 |
4 | 0.4207 | 0.3500 | 1.69 | 0.5024 | 0.04187 |
5 | 0.5388 | 0.4500 | 2.13 | 0.5016 | 0.04180 |
6 | 0.5996 | 0.5000 | 2.38 | 0.5033 | 0.04194 |
7 | 0.7201 | 0.6000 | 2.88 | 0.5010 | 0.04175 |
8 | 0.8987 | 0.7500 | 3.56 | 0.5010 | 0.04175 |
9 | 1.0775 | 0.9001 | 4.25 | 0.5009 | 0.04174 |
10 | 1.2597 | 1.0447 | 5.00 | 0.5161 | 0.04301 |
11 | 1.4978 | 1.2500 | 5.94 | 0.5010 | 0.04175 |
12 | 1.7968 | 1.5001 | 7.13 | 0.4997 | 0.04164 |
13 | 2.0731 | 1.7501 | 7.75 | 0.5002 | 0.04168 |
14 | 2.3438 | 2.0000 | 8.25 | 0.5000 | 0.04167 |
15 | 2.6146 | 2.2500 | 8.75 | 0.5000 | 0.04167 |
16 | 2.8854 | 2.5000 | 9.25 | 0.5000 | 0.04167 |
17 | 3.1563 | 2.7500 | 9.75 | 0.5000 | 0.04167 |
18 | 3.4271 | 3.0000 | 10.25 | 0.5000 | 0.04167 |
Jacobs
Der Jacobs-Kegel (abgekürzt JT) wird in der Regel zur Befestigung von Bohrmaschinenfuttern auf einem Dorn verwendet. Die Kegelwinkel sind nicht einheitlich und variieren von 1,41° pro Seite für Nr. 0 (und die obskure #2+1⁄2) bis 2,33° pro Seite für Nr. 2 (und Nr. 2 kurz). ⓘ
Es gibt auch mehrere Größen zwischen Nr. 2 und Nr. 3: Nr. 2 kurz, Nr. 6 und Nr. 33. ⓘ
Kegel | Kleines Ende | Großes Ende | Länge ⓘ |
---|---|---|---|
Nr. 0 | 0,22844 Zoll (5,8024 mm) | 0,2500 Zoll (6,3500 mm) | 0,43750 Zoll (11,113 mm) |
Nr. 1 | 0,33341 Zoll (8,4686 mm) | 0,3840 Zoll (9,7536 mm) | 0,65625 Zoll (16,669 mm) |
Nr. 2 | 0,48764 Zoll (12,386 mm) | 0,5590 Zoll (14,199 mm) | 0,87500 Zoll (22,225 mm) |
Nr. 2 Kurz | 0,48764 Zoll (12,386 mm) | 0,5488 Zoll (13,940 mm) | 0,75000 Zoll (19,050 mm) |
#2+1⁄2 | 0,625 Zoll (15,875 mm) | 0,677 Zoll (17,196 mm) | 1,055 Zoll (26,797 mm) |
Nr. 3 | 0,74610 Zoll (18,951 mm) | 0,8110 Zoll (20,599 mm) | 1,21875 Zoll (30,956 mm) |
Nr. 4 | 26,345 mm (1,0372 in) | 28,550 mm (1.1240 in) | 1,6563 Zoll (42,070 mm) |
Nr. 5 | 1,3161 Zoll (33,429 mm) | 35,890 mm (1.4130 in) | 1,8750 Zoll (47,625 mm) |
Nr. 6 | 0,6241 Zoll (15,852 mm) | 0,6760 Zoll (17,170 mm) | 1,0000 Zoll (25,400 mm) |
Nr. 33 | 0,5605 Zoll (14,237 mm) | 0,6240 Zoll (15,850 mm) | 1,0000 Zoll (25,400 mm) |
Jarno
Jarno-Kegel verwenden ein stark vereinfachtes Schema. Der Verjüngungsgrad beträgt 1:20 am Durchmesser, d. h. 0,600" am Durchmesser pro Fuß, 0,050" am Durchmesser pro Zoll. Die Kegel reichen von Nummer 2 bis Nummer 20. Der Durchmesser des großen Endes in Zoll ist immer die Kegelgröße geteilt durch 8, das kleine Ende ist immer die Kegelgröße geteilt durch 10 und die Länge ist die Kegelgröße geteilt durch 2. Ein Jarno No. 7 misst zum Beispiel 0,875" (7/8) am großen Ende. Das kleine Ende misst 0,700" (7/10) und die Länge beträgt 3,5" (7/2). ⓘ
Das System wurde von Oscar J. Beale von Brown & Sharpe erfunden. ⓘ
Kegel | Großes Ende | Kleines Ende | Länge | Kegel/ ft |
Kegel/ in |
Winkel von Mitte/° |
---|---|---|---|---|---|---|
Nr. 2 | 0.2500 | 0.2000 | 1.00 | .6000 | .0500 | 1.4321 |
Nr. 3 | 0.3750 | 0.3000 | 1.50 | .6000 | .0500 | 1.4321 |
Nr. 4 | 0.5000 | 0.4000 | 2.00 | .6000 | .0500 | 1.4321 |
Nr. 5 | 0.6250 | 0.5000 | 2.50 | .6000 | .0500 | 1.4321 |
Nr. 6 | 0.7500 | 0.6000 | 3.00 | .6000 | .0500 | 1.4321 |
Nr. 7 | 0.8750 | 0.7000 | 3.50 | .6000 | .0500 | 1.4321 |
Nr. 8 | 1.0000 | 0.8000 | 4.00 | .6000 | .0500 | 1.4321 |
Nr. 9 | 1.1250 | 0.9000 | 4.50 | .6000 | .0500 | 1.4321 |
Nr. 10 | 1.2500 | 1.0000 | 5.00 | .6000 | .0500 | 1.4321 |
Nr. 11 | 1.3750 | 1.1000 | 5.50 | .6000 | .0500 | 1.4321 |
Nr. 12 | 1.5000 | 1.2000 | 6.00 | .6000 | .0500 | 1.4321 |
Nr. 13 | 1.6250 | 1.3000 | 6.50 | .6000 | .0500 | 1.4321 |
Nr. 14 | 1.7500 | 1.4000 | 7.00 | .6000 | .0500 | 1.4321 |
Nr. 15 | 1.8750 | 1.5000 | 7.50 | .6000 | .0500 | 1.4321 |
Nr. 16 | 2.0000 | 1.6000 | 8.00 | .6000 | .0500 | 1.4321 |
Nr. 17 | 2.1250 | 1.7000 | 8.50 | .6000 | .0500 | 1.4321 |
Nr. 18 | 2.2500 | 1.8000 | 9.00 | .6000 | .0500 | 1.4321 |
Nr. 19 | 2.3750 | 1.9000 | 9.50 | .6000 | .0500 | 1.4321 |
Nr. 20 | 2.5000 | 2.0000 | 10.00 | .6000 | .0500 | 1.4321 |
Morsekegel

Der Morsekegel wurde von Stephen A. Morse in New Bedford, Massachusetts, Mitte der 1860er Jahre entwickelt. Seitdem hat er sich weiterentwickelt und umfasst nun kleinere und größere Größen. Er wurde von zahlreichen Organisationen als Standard übernommen, darunter die Internationale Organisation für Normung (ISO) als ISO 296 und das Deutsche Institut für Normung (DIN) als DIN 228-1. Es handelt sich um eine der am weitesten verbreiteten Arten und ist besonders häufig auf dem Schaft von Spiralbohrern mit Kegelschaft und Maschinenreibahlen, in den Spindeln von industriellen Bohrmaschinen und in den Reitstöcken von Drehbänken zu finden. Der Kegelwinkel des Morsekegels variiert je nach Größe, beträgt aber in der Regel 1,49 Grad (einschließlich etwa 3 Grad). ⓘ
Einige modulare orthopädische Hüftgelenksimplantate verwenden einen Morsekonus, um die Komponenten miteinander zu verbinden. Auch einige Zahnimplantate verwenden einen Morsekonus, um die Komponenten zu verbinden. ⓘ
Größen
Morsekegel gibt es in acht Größen, die mit ganzen Zahlen zwischen 0 und 7 bezeichnet werden, sowie in einer halben Größe (4 1/2 - sehr selten anzutreffen und in der Tabelle nicht aufgeführt). Oft wird die Bezeichnung mit MT abgekürzt, gefolgt von einer Ziffer, z. B. wird ein Morsekegel mit der Nummer 4 als MT4 bezeichnet. Der MT2-Kegel ist die Größe, die am häufigsten in Bohrmaschinen bis zu einer Kapazität von 1⁄2" zu finden ist. Kurze Ausführungen mit demselben Kegelwinkel, aber etwas mehr als der Hälfte der üblichen Länge, sind gelegentlich bei den ganzzahligen Größen von 1 bis 5 anzutreffen. Für diese gibt es Normen, die u. a. bei Drehbänken verwendet werden, um eine größere Spindeldurchgangsbohrung zu erhalten. ⓘ
Endtypen
Morsekegel sind selbsthaltende Kegel, die drei Arten von Enden haben können:
- Zapfen (Abbildung) zur Erleichterung des formschlüssigen Antriebs, um ein Abrutschen zu verhindern
- mit Gewinde, um mit einer Zugstange festgehalten zu werden
- flach (ohne Mitnehmerzapfen oder Gewindeteil) ⓘ
Selbsthaltende Kegel sind darauf angewiesen, dass die Axiallast gegenüber der Radiallast überwiegt, um hohe Drehmomente zu übertragen. Probleme können bei der Verwendung großer Bohrer im Verhältnis zum Schaft auftreten, wenn die Vorbohrung zu groß ist. Die Ausführung mit Gewinde ist für jede Art von Seitenführung, insbesondere beim Fräsen, unerlässlich. Die einzige Ausnahme ist, dass solche ungünstigen Situationen simuliert werden können, um einen verklemmten Schaft zu entfernen. Das Zulassen von Rattern hilft, den Griff zu lösen. Der spitze (schmale) Kegelwinkel kann bei starker axialer Belastung oder über längere Zeiträume zu einer solchen Verklemmung führen. ⓘ
Gelegentlich sieht man Schaftfräser mit einem Morsekegel-Schaft mit Zapfen: Zur Sicherheit müssen diese mit einer C-Manschette oder ähnlichem verwendet werden, die in den Hals zwischen Fräser und Schaft passt und gegen das große Ende des Kegels gezogen wird. ⓘ
Der Kegel selbst hat eine Länge von etwa 5/8" pro Fuß, aber die genauen Verhältnisse und Abmessungen für die verschiedenen Größen von Kegeln mit Zapfen sind unten angegeben. ⓘ
Abmessungen
Morsekegel-Nummer | Kegel | A | B (max) | C (max.) | D (max.) | E (max.) | F | G | H | J | K |
---|---|---|---|---|---|---|---|---|---|---|---|
0 | 1:19.212 | 9.045 | 56.5 | 59.5 | 10.5 | 6 | 4 | 1 | 3 | 3.9 | 1° 29' 27" |
1 | 1:20.047 | 12.065 | 62 | 65.5 | 13 | 8.7 | 5 | 1.2 | 3.5 | 5.2 | 1° 25' 43" |
2 | 1:20.020 | 17.780 | 75 | 80 | 16 | 13.5 | 6 | 1.6 | 5 | 6.3 | 1° 25' 50" |
3 | 1:19.922 | 23.825 | 94 | 99 | 20 | 18.5 | 7 | 2 | 5 | 7.9 | 1° 26' 16" |
4 | 1:19.254 | 31.267 | 117.5 | 124 | 24 | 24.5 | 8 | 2.5 | 6.5 | 11.9 | 1° 29' 15" |
5 | 1:19.002 | 44.399 | 149.5 | 156 | 29 | 35.7 | 10 | 3 | 6.5 | 15.9 | 1° 30' 26" |
6 | 1:19.180 | 63.348 | 210 | 218 | 40 | 51 | 13 | 4 | 8 | 19 | 1° 29' 36" |
7 | 1:19.231 | 83.058 | 285.75 | 294.1 | 34.9 | – | – | 19.05 | – | 19 | 1° 29' 22" |
B-Kegel
Die Kegel der Serie B sind eine DIN-Norm (DIN 238), die typischerweise für die Montage von Spannfuttern auf deren Achsen verwendet wird, wie die ältere Jacobs-Kegelserie. Jeder Kegel der B-Reihe ist praktisch das kleine oder große Ende eines Morsekegels:
- B10 = kleines Ende von MT1 (D = 10,095 mm)
- B12 = großes Ende von MT1 (D = 12,065 mm)
- B16 = kleines Ende von MT2 (D = 15,733 mm)
- B18 = großes Ende von MT2 (T = 17,780 mm)
- B22 = kleines Ende von MT3 (T = 21,793 mm)
- B24 = großes Ende von MT3 (D = 23,825 mm) ⓘ
Die Zahl nach dem B ist der Durchmesser (D) des großen Kegelendes, auf den nächsten mm genau, und "etwa" 1 mm größer als das große Ende der Muffe (~2 mm im Fall von B22 und B24) ⓘ
NMTB-Kegelfamilie

Die National Machine Tool Builders Association (heute: Association for Manufacturing Technology) hat einen Steilkegel definiert, der häufig auf Fräsmaschinen verwendet wird. Der Kegel wird auch als NMTB, NMT oder NT bezeichnet. Der Kegel beträgt 3,500 Zoll pro Fuß und wird auch als "7 in 24" oder 7/24 bezeichnet; der berechnete Winkel beträgt 16,5943 Grad. Alle NMTB-Werkzeuge haben diesen Kegel, aber die Werkzeuge sind in verschiedenen Größen erhältlich: NMTB-10, 15, 20, 25, 30, 35, 40, 45, 50 und 60. Diese Kegel wurden offenbar auch in der ASA (jetzt ANSI) B5.10-1943 festgelegt. ⓘ
NMTB ist ein "selbstlösender" oder "schneller" Kegel. Im Gegensatz zu den oben genannten selbsthaltenden Kegeln sind diese Kegel nicht für die Übertragung hoher Drehmomente ausgelegt; hohe Drehmomente werden durch Mitnehmerkeile übertragen, die in Nuten am Flansch eingreifen. Der Zweck besteht darin, einen schnellen und einfachen Wechsel zwischen verschiedenen Werkzeugen (entweder automatisch oder von Hand) zu ermöglichen und gleichzeitig sicherzustellen, dass das Werkzeug oder der Werkzeughalter fest und starr mit der Spindel verbunden und genau koaxial zu ihr ist. Das größere Ende in der Nähe des Werkzeugs sorgt für eine höhere Steifigkeit als bei Morse- oder R8-Kegeln, die an vergleichbaren Maschinen angebracht sind. ⓘ
Das Patent 1794361 (angemeldet am 25. März 1927) beschreibt Spindel- und Werkzeugformen für Fräsmaschinen, die einen Steilkegel verwenden. Das Patent wurde der Kearney & Trecker Corporation, Brown & Sharpe und der Cincinnati Milling Machine Company zugewiesen. In dem Patent wurde ein Kegel gesucht, der das Werkzeug frei freigibt, und es wurde festgestellt, dass ein Kegel von 3,5 in 12 diese Eigenschaft hat. Das Patent verwendete auch die Keile und Schlitze sowie ein Ende am Werkzeugschaft, um zu verhindern, dass der Werkzeugschaft aus der Spindel einer Horizontalfräse herausfällt, während der Bediener die Zugstange anschließt. ⓘ
Die Norm ANSI B5.18-1972 legt einige wesentliche Abmessungen für Fräsmaschinenspindeln und Werkzeugschäfte mit den Kegelgrößen 30, 40, 45, 50 und 60 fest. Die Spezifikationen beschreiben die Position des Mitnehmerkeils und des Flansches sowie das Gewinde des Einzugsbolzens, der den Schaft in der Spindel hält. ⓘ
Die Werkzeuge werden als Quick Change, National Machine Tool Builders' Association, 1927, NMTB, American Standard Machine Taper, ANSI B5.18, DIN 2080 / IS 2340, ISO R 290-2583 bezeichnet. Es gibt leichte Abweichungen bei Gewinden und Flanschen (JIS B 6339: MAS 403); und die europäischen Normen (z. B. ISO-Kegel) verwenden metrische Zuggewinde. ⓘ
Die NMTB-Werkzeugschäfte hatten den 7:24-Kegel, aber sie hatten auch ein Ende mit konstantem Durchmesser (Pilot) am Ende des Schaftes, das im Patent von 1927 beschrieben wurde. Spätere Konstruktionsvarianten ließen das Ende weg (wodurch der Schaft kürzer wurde) und brachten eine V-Nut in den Flansch ein, die den automatischen Werkzeugwechsel erleichterte. Moderne Konstruktionen begannen mit kraftbetätigten Zugstangen, die in Zugbolzen (auch als Halteknöpfe bekannt) griffen, die in den Werkzeugschaft geschraubt waren, statt in Schraubzugstangen. Die Kraftdeichsel griff in den Zugbolzen, anstatt in den Werkzeugschaft geschraubt zu werden. ⓘ
Die moderneren Werkzeughalterkonstruktionen wurden als Caterpillar "V-Flansch", CAT, V-Flansch, ANSI B5.50, SK, ISO, International (INT), BT, ISO 7388-1, DIN 69871, NFE 62540 bekannt. Auch hier gibt es leichte Abweichungen bei den Werkzeugen. Obwohl die grundlegenden Kegelabmessungen gleich sind, gibt es Unterschiede bei den Flanschen, Einzugsgewindegrößen und Zugbolzen; die internationalen Versionen verwenden metrische Größen. ⓘ
HSK-Kegel



HSK-Werkzeughalter wurden in den frühen 1990er Jahren entwickelt. HSK steht für :de:Hohlschaftkegel; deutsch für "Hohlschaftkegel". ⓘ
Steilkegel neigen dazu, sich bei hohen Drehzahlen zu lockern, da ihre massiven Schäfte steifer sind als die Spindeln, in die sie passen, so dass sich die Spindel bei hohen Fliehkräften stärker ausdehnt als der Werkzeughalter, wodurch sich die Gesamtlänge ändert: Das heißt, wenn sich die Spindel "ausdehnt", neigt der Werkzeughalter dazu, sich in der z-Achse tiefer in die Spindel zu bewegen, was zur Herstellung von Teilen führen kann, die außerhalb der Toleranzen liegen. Der HSK-Hohlschaft ist absichtlich dünn und flexibel, so dass er sich stärker ausdehnt als die Spindel und sich bei hohen Drehzahlen festzieht. Außerdem hat der HSK-Halter zwei Kontakte: Er greift sowohl am Kegel als auch an der Oberseite des Flansches in die Spindel ein, was eine axiale Bewegung bei thermischem Wachstum und/oder Zentrifugalkraft der Spindel verhindert. ⓘ
Die Flexibilität wird auch für eine genaue axiale Positionierung genutzt. Ein HSK-Werkzeughalter hat sowohl einen kegelförmigen Schaft als auch einen Flansch mit einer Gegenlauffläche. Der Schaft ist kurz (etwa halb so lang wie andere Maschinenkegel), hat einen flachen Kegel (Verhältnis 1:10) und ist etwas zu groß, damit der Flansch vollständig in der Aufnahme sitzen kann. Die dünnen Wände, der kurze Schaft und der flache Kegel sorgen für eine große Öffnung auf der Rückseite des Werkzeugs. Dort passt eine Spreizhülse hinein, die mit einer 30°-Fase in den Schaft eingepasst wird. Beim Zurückziehen der Zugstange dehnt sich die Spannzange aus und zieht den Schaft zurück in die Aufnahme, wobei der Schaft zusammengedrückt wird, bis der Flansch an der Vorderseite der Spindel anliegt. Dies sorgt für eine steife, wiederholbare Verbindung, da die Zentrifugalkraft im Inneren der Spindel genutzt wird. Wenn die Zentrifugalkräfte zunehmen, zwingt die sich ausdehnende Spannzange im HSK die Wände des Werkzeughalterschafts dazu, in Kontakt mit der Spindelwand zu bleiben. ⓘ
Die HSK-Konstruktion wurde als herstellerneutrale Norm entwickelt. Die Arbeitsgruppe, die die HSK-Norm erarbeitete, bestand aus Vertretern der Wissenschaft, des Verbandes Deutscher Werkzeughersteller und einer Gruppe von internationalen Unternehmen und Endanwendern. Das Ergebnis waren die deutschen DIN-Normen 69063 für die Spindel und 69893 für den Schaft. Die HSK-Arbeitsgruppe hat sich nicht auf ein bestimmtes Produktdesign festgelegt, sondern auf eine Reihe von Normen, die HSK-Werkzeughalter für verschiedene Anwendungen definieren. Die Gruppe definierte insgesamt sechs HSK-Schaftformen in 9 Größen. ⓘ
Die Größen werden durch den Durchmesser des Schaftflansches in Millimetern angegeben. Diese Durchmesser stammen aus der Vorzugsnummernreihe R10′, die von 25 bis 160 mm reicht. ⓘ
Heute werden die Schaftformen mit den Buchstaben A bis F und T bezeichnet. Die Hauptunterschiede zwischen den Formen liegen in der Lage der Antriebsnuten, der Greiferaufnahmenuten, der Kühlmittelbohrungen und der Fläche des Flansches. ⓘ
A ist die Grundform. Der B-Schaft ist eine Variante für Anwendungen mit hohen Drehmomenten und hat einen Flansch, der im Verhältnis zum Wellendurchmesser eine Nummer größer ist. (Ein A-40-Schaft passt also in eine B-50-Buchse.) ⓘ
Bei den Formen C und D handelt es sich um vereinfachte Varianten von A und B für den manuellen Einsatz, bei denen Merkmale zur Aufnahme von automatischen Werkzeugwechslern wie eine V-Nut und zugehörige Orientierungsschlitze sowie eine Aussparung für einen RFID-Chip wegfallen. ⓘ
Die Flansch- und Kegelformen E und F ähneln den Formen A und B, sind jedoch für die Hochgeschwindigkeitsbearbeitung (20.000 U/min und mehr) von leichten Werkstoffen konzipiert, indem alle asymmetrischen Merkmale eliminiert werden, um Unwucht und Vibrationen zu minimieren. ⓘ
ASME B5.62 "Hollow Taper Tooling With Flange-Face Contact" und ISO 12164-3:2014 "Dimensions of shanks for stationary tools" (Abmessungen von Schäften für feststehende Werkzeuge) enthalten eine zusätzliche Form T, die mit Form A bidirektional kompatibel ist, aber eine viel engere Toleranz bei den Breiten der für die Winkelausrichtung verwendeten Keile und Nuten aufweist. Dadurch können nicht rotierende Drehmeißel genau gehalten werden. ⓘ
Eine HSK-Verbindung beruht auf einer Kombination von axialen Spannkräften und Kegel-Schaft-Übermaß. Alle diese Kräfte werden durch die Konstruktionsparameter der zu verbindenden Komponenten erzeugt und gesteuert. Sowohl der Schaft als auch die Spindel müssen genau aufeinander abgestimmte Kegel und Flächen haben, die rechtwinklig zur Kegelachse sind. Es gibt verschiedene HSK-Spannmethoden. Alle verwenden einen Mechanismus zur Verstärkung der Klemmwirkung von gleichmäßig beabstandeten Spannzangensegmenten. Beim Einspannen des Werkzeughalters in die Spindel wird durch die Zugkraft ein fester Metall-Metall-Kontakt zwischen dem Schaft und dem Innendurchmesser der Spanneinheit hergestellt. Eine zusätzliche Zugkraft verriegelt die beiden Elemente formschlüssig zu einer Verbindung mit hoher radialer und axialer Steifigkeit. Wenn sich die Spannzangensegmente drehen, gewinnt der Spannmechanismus an Fliehkraft. Die HSK-Konstruktion macht sich die Fliehkraft zunutze, um die Festigkeit der Verbindung zu erhöhen. Die Zentrifugalkraft bewirkt auch, dass sich die dünnen Wände des Schafts schneller radial auslenken als die Wände der Spindel. Dies trägt zu einer sicheren Verbindung bei, indem es einen starken Kontakt zwischen dem Schaft und der Spindel gewährleistet. Die Automobilindustrie und die Luft- und Raumfahrtindustrie sind die größten Anwender von HSK-Werkzeughaltern. Ein weiterer Industriezweig, in dem sie zunehmend eingesetzt werden, ist der Werkzeug- und Formenbau. ⓘ
R8
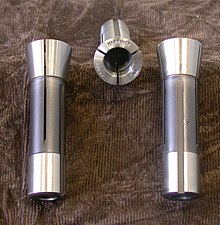
Dieser Kegel wurde von Bridgeport Machines, Inc. für den Einsatz in seinen Fräsmaschinen entwickelt. R8-Kegel sind nicht selbsthaltend und benötigen daher eine Zugstange, die sich durch die Spindel bis zur Oberseite der Maschine erstreckt, um ein Lösen zu verhindern, wenn Seitenkräfte auftreten. Sie sind außerdem verkeilt (siehe Abbildung), um eine Drehung beim Einsetzen und Herausnehmen zu verhindern, obwohl der Kegel das Drehmoment bei der Verwendung überträgt. Das Zugstangengewinde ist normalerweise 7⁄16″-20 tpi (UNF). Der Winkel des Kegels beträgt 16°51′ (16,85°) mit einem Außendurchmesser von 1,25″ und einer Länge von 15⁄16″. (Quelle: Bridgeport Manufacturer) Der Durchmesser des parallelen Aufnahmeteils ist kein "Bruchteil eines Zolls" wie die anderen Abmessungen und beträgt 0,949″ bis 0,9495″. ⓘ
Werkzeuge mit einem R8-Kegel werden direkt in die Spindel der Maschine eingesetzt. R8-Spannzangen werden in der Regel zur Aufnahme von Werkzeugen mit rundem Schaft verwendet, obwohl jede beliebige Form aufgenommen werden kann, wenn in die Spannzange die entsprechende Form geschnitten wurde. Die Spannzangen haben eine Präzisionsbohrung mit axialen Druckschlitzen für die Aufnahme von Schneidwerkzeugen und sind mit einem Gewinde für die Zugstange versehen. Das R8-System wird in der Regel mit Spannzangen mit einem Durchmesser von 1⁄8″ bis 3⁄4″ oder Werkzeughaltern mit demselben oder einem etwas größeren Durchmesser verwendet. Die Spannzangen oder Werkzeughalter werden direkt in die Spindel eingesetzt, und die Zugstange wird von oben in die Oberseite der Spannzange oder des Werkzeughalters eingespannt. Andere Werkzeuge, wie z. B. Bohrfutter, Fräser, Wendeschneidplatten usw. können einen R8-Kegelschaft haben, der in das Werkzeug eingebaut oder diesem hinzugefügt ist. ⓘ
Der R8-Kegel ist häufig bei Bridgeport- und ähnlichen Revolverfräsern aus den USA oder bei (sehr häufigen) Kopien dieser Fräser aus anderen Ländern anzutreffen. Die Beliebtheit ist zum großen Teil auf den Erfolg von Bridgeport und anderen Fräsern zurückzuführen, die in enger Anlehnung an dieses Modell während eines Großteils des 20. Jahrhunderts hergestellt wurden. ⓘ
Genormte Geometrie
Morsekegel in 7 Größen – bezeichnet als MK 0 bis MK 6 – mit maximalen Schaftdurchmessern von etwa 9 bis 63 mm bei nur geringfügig unterschiedlichen Kegelverhältnissen zwischen 1:19,002 und 1:20,047 sind genormt nach DIN 228 Teil 1 und 2. Die Neigungswinkel der Morsekegel betragen etwa 1°26′ bis etwa 1°30′. Die wichtigsten Maße von Schaft und Hülse der Morsekegel 0 bis 6 (alle in mm):
Bauteil | Maß | MK 0 | MK 1 | MK 2 | MK 3 | MK 4 | MK 5 | MK 6 ⓘ |
---|---|---|---|---|---|---|---|---|
Schaft | D1 | 9,212 | 12,240 | 17,981 | 24,052 | 31,544 | 44,732 | 63,726 |
Schaft | d | 6,401 | 9,371 | 14,534 | 19,76 | 25,909 | 37,47 | 53,752 |
Schaft | d2 | 6,115 | 8,972 | 14,06 | 19,133 | 25,156 | 36,549 | 52,422 |
Hülse | D | 9,045 | 12,065 | 17,781 | 23,826 | 31,269 | 44,401 | 63,350 |
Hülse | d5 | 6,7 | 9,7 | 14,9 | 20,2 | 26,5 | 38,2 | 54,8 |
Kegelverhältnis | 1:19,212 | 1:20,047 | 1:20,020 | 1:19,922 | 1:19,254 | 1:19,002 | 1:19,180 |
Die Werkzeugaufnahmen von Bohr- und Drehmaschinen haben häufig die Größen MK 2 bis MK 6. ⓘ
Ergänzend zu dieser Morsekegelreihe normt DIN 228 noch 2 kleinere (4 und 6 mm) und 5 größere Metrische Kegel ME (80 bis 200 mm), durchwegs 1:20 verjüngt. Fa. Morse nennt zusätzlich noch die Zwischengröße MK 4 1/2, sowie MK 7 und 8. Es gibt auch Reduzierhülsen, um kleinere Morsekegel an größere Aufnahmen anzupassen. ⓘ
Morsekegel gibt es in vier Formen:
- Form A (Schaft) und C (Hülse) mit Anzugsgewinde zum Befestigen.
- Form B (Schaft) und D (Hülse) mit Austreiblappen am Schaft und Langloch in der Hülse für den Austreibkeil. ⓘ
Weitere Werkzeugkegel
Außer dem Morsekegel gibt es metrische Kegel (ME), Steilkegel (SK) und Hohlschaftkegel (HSK). ⓘ
Ferner gibt es noch die Bohrfutterkegel in den Größen ⓘ
Größe | d1 | d2 ⓘ |
---|---|---|
B10 | 10,09 | 9,40 |
B12 | 12,06 | 11,10 |
B16 | 15,73 | 14,50 |
B18 | 17,78 | 16,20 |
B22 | 21,79 | 19,80 |
B24 | 23,82 | 21,30 |
Die Bohrfutterkegel stellen jeweils ein Teilstück eines Morsekegels dar. Bei einem Kegeldorn nach DIN 238 liegt an der Antriebseite (im Bild: rechts) ein Morsekegel und an der Abtriebseite ein (kürzerer) Bohrfutterkegel. ⓘ